Introduce about machined parts guide,Qulity,Cost,Supplier,Certification,Market,Tips,FAQ
Machined parts are components that have been molded or shaped using various machining processes such as drilling, cutting, grinding, or turning. Machined parts are crucial in the manufacturing industry, as they are used in a wide range of products and machinery.
When it comes to machined parts, quality is paramount. High-quality machined parts ensure product performance, reliability, and safety. Ensure that machined parts meet specifications, tolerances, and quality standards to avoid product failure or malfunction.
Cost is another important factor to consider when sourcing machined parts. Balance quality with cost-effectiveness to ensure that you are getting the best value for your money. Consider factors such as material, complexity, volume, and lead time when budgeting for machined parts.
Choosing a reliable supplier is key to getting high-quality machined parts. Look for suppliers with experience, expertise, and a track record of delivering quality products on time. Consider factors such as location, capacity, and capabilities when selecting a supplier.
Certification is also important when sourcing machined parts. Look for suppliers who are certified and compliant with industry standards and regulations. Certifications such as ISO 9001 ensure that the supplier follows best practices in manufacturing.
The market for machined parts is competitive, with many suppliers offering a wide range of products and services. Research and compare different suppliers to find the best fit for your specific needs.
Some tips for sourcing machined parts include: clearly defining your requirements, communicating effectively with suppliers, and conducting thorough quality checks before accepting delivery.
Frequently Asked Questions (FAQ) about machined parts include queries about material options, lead times, pricing, and customization options. It’s important to address any doubts or concerns before placing an order.
In conclusion, machined parts are essential components in the manufacturing industry, and ensuring quality, cost-effectiveness, and reliability is key to success. Choose a reputable supplier, communicate effectively, and conduct thorough quality checks to ensure that you are getting the best machined parts for your needs.
Types of machined parts
Machined parts are used in a wide range of industries and applications, and they come in various types based on their design, functionality, and purpose. Some common types of machined parts include:
1. Shafts: Shafts are long, cylindrical rods that transmit torque between rotating components. They are commonly used in automotive engines, industrial machinery, and power transmission systems.
2. Gears: Gears are toothed wheels that mesh together to transmit motion and power. They are used in machinery, such as engines, transmissions, and gearboxes, to control speed, torque, and direction of rotation.
3. Bearings: Bearings are mechanical components that enable smooth and frictionless motion between moving parts. They reduce friction, support loads, and aid in rotational or linear movement. Examples include ball bearings, roller bearings, and thrust bearings.
4. Fasteners: Fasteners are used to join or secure two or more components together. Common types of fasteners include bolts, screws, nuts, and rivets. They are essential for holding assemblies together and ensure structural integrity.
5. Valves: Valves control the flow of fluids or gases by opening, closing, or partially obstructing passage. They are used in various industries, such as oil and gas, water distribution, chemical processing, and HVAC systems.
6. Pistons: Pistons are cylindrical components that move back and forth within a cylinder to generate mechanical power. They are commonly found in internal combustion engines, reciprocating pumps, and compressors.
7. Bushings: Bushings are cylindrical components that act as a bearing surface for rotary or linear motion. They support shafts, rods, or pins, reducing friction and wear. Bushings are used in many applications, including automotive, aerospace, and industrial equipment.
8. Housings: Housings enclose and protect delicate components or assemblies. They provide a protective covering and often have openings for access, ventilation, or cable routing. Examples include motor housings, instrument enclosures, and electrical junction boxes.
9. Connectors: Connectors are used to join electrical cables or wires, providing a secure and reliable electrical connection. They come in various types, such as plugs, sockets, terminals, and connectors for printed circuit boards.
10. Brackets: Brackets are supports or braces used to secure or hold two components or structures together. They provide stability and reinforcement and are often used in construction, automotive, and electronics industries.
These are just a few examples of the many types of machined parts that are essential in a wide array of industries. Each part plays a unique role in ensuring the efficient and reliable functioning of various mechanical systems and assemblies.
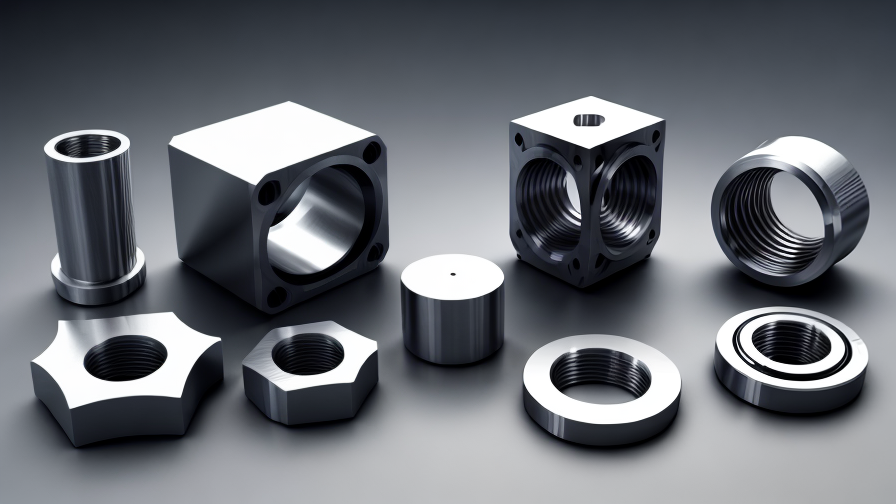
Pros and Cons of Using machined parts
Pros and Cons of Using Machined Parts
Machined parts are crucial components in various industries, including automotive, aerospace, and manufacturing. These parts are manufactured by using various machining techniques, such as milling, turning, drilling, and grinding. While there are several advantages to using machined parts, there are also some drawbacks to consider. Below, we will discuss the pros and cons of using machined parts in different applications.
Pros:
1. Precision: Machined parts can be manufactured to extremely tight tolerances, ensuring high precision and accuracy. This is particularly important in industries where even the smallest deviation can result in significant consequences, such as in aerospace or medical devices.
2. Customization: Machining allows for a high degree of customization, enabling the production of complex or unique parts that may not be easily manufactured using other methods. This flexibility is invaluable when working with prototypes or creating one-off components.
3. Strength and Durability: Machined parts are generally known for their strength and durability. These parts can be made from a wide range of materials, including metals, plastics, or composites, which can be carefully chosen to meet the specific requirements of the application.
4. Batch Production: Machining is well-suited for batch production, where numerous identical parts need to be manufactured. Computer numerical control (CNC) machining processes offer excellent repeatability and consistency, ensuring that each machined part in the batch meets the same quality standards.
Cons:
1. Cost: Machining can be an expensive manufacturing process, especially when compared to other methods like casting or forging. The cost of specialized machinery, skilled labor, and material waste can significantly drive up production expenses, especially for small batch sizes.
2. Time-consuming: Machining can be a time-consuming process, particularly for complex or intricate designs that require multiple machining operations. From programming the machine to performing setup and tool changes, machining can take longer than other production methods.
3. Material Waste: Machining typically generates a considerable amount of material waste. This is particularly true for some machining techniques, like milling, where excess material needs to be removed to achieve the desired shape. The waste material not only affects production costs but also raises environmental concerns.
4. Limited Size: Machining has size limitations, especially when working with large or oversized parts. The size of the machinery and the associated fixtures and tooling may restrict the dimensions of the machined parts, making it necessary to explore alternative manufacturing processes for larger components.
In conclusion, while machined parts offer excellent precision, customization, and durability, they come with some drawbacks. The high cost, time-consuming nature, material waste, and size limitations need to be carefully considered when deciding whether machining is the most suitable manufacturing method for a particular application.
machined parts Reference Specifications (varies for different product)
Machined parts refer to components that are manufactured using machining processes such as cutting, drilling, milling, turning, and grinding. These parts are commonly used in various industries including automotive, aerospace, electronics, and machinery manufacturing. To ensure the correct production of machined parts, reference specifications are utilized to provide detailed information and requirements.
Reference specifications for machined parts vary depending on the specific product and application. These specifications outline the necessary dimensions, tolerances, surface finishes, materials, and other factors that need to be considered during production. They serve as a guide for machinists and manufacturers to produce parts that meet the desired quality and functionality.
Dimensions specified in the reference documents include the overall size, shape, and contours of the machined part. Tolerances, which define the allowable variation in dimensions, are also included to ensure the parts fit and function correctly when assembled. Surface finishes are addressed to meet specific requirements, such as smoothness, roughness, or the application of coatings.
Material specifications are crucial in determining the appropriate material to use for a particular machined part. Factors like strength, hardness, corrosion resistance, and thermal properties are considered to ensure the part functions effectively in its intended environment. These specifications may include industry standards or customer-specific requirements.
Other important details provided in the reference specifications for machined parts can range from specific geometric features and hole patterns to thread sizes, chamfers, and radii. Any special requirements like heat treatments, plating, or special packaging may also be included to meet the desired product functionality and aesthetics.
In conclusion, reference specifications for machined parts are essential for ensuring the correct production of components used in various industries. These specifications provide detailed information on dimensions, tolerances, surface finishes, materials, and other relevant factors to ensure high-quality and functional parts. Machinists and manufacturers rely on these specifications to produce parts that meet the exact requirements of the customers and applications.
Applications of machined parts
Machined parts play a crucial role in various industries and applications. Here are some key uses of machined parts:
1. Automotive Industry: Machined parts are extensively used in the automotive industry for manufacturing engine components, transmission parts, suspension systems, brake systems, and various other critical components. These parts offer high precision, durability, and performance.
2. Aerospace Industry: The aerospace sector heavily relies on machined parts for constructing aircraft components, such as turbine blades, landing gear components, engine brackets, and control systems. Machined parts ensure dimensional accuracy, strength, and reliability, meeting the strict industry standards.
3. Medical Devices: Machined parts are essential for producing medical devices, including implants, surgical instruments, orthopedic tools, and diagnostic equipment. The precise machining techniques enable the creation of complex shapes and designs required for medical applications.
4. Electronics and Technology: Machined parts find extensive usage in electronics and technology sectors, particularly for manufacturing computer components, connectors, mobile phone parts, and optical devices. They offer high precision and tight tolerances required for these applications.
5. Oil and Gas Industry: In the oil and gas industry, machined parts are used in drilling equipment, valves, pumps, and various other components. These parts provide the necessary strength, corrosion resistance, and tolerances required to withstand harsh operating conditions.
6. Manufacturing Machinery: Machined parts are crucial for various manufacturing machinery, including CNC machines, milling machines, lathes, and industrial robots. These parts form the backbone of the machinery, ensuring accurate movements, high speeds, and minimal vibrations.
7. Renewable Energy: Machined parts are widely employed in the renewable energy sector for manufacturing wind turbine components, solar panel frames, hydroelectric power equipment, and wave energy devices. The efficient machining process helps produce large-scale components that endure demanding conditions.
8. Defense Sector: The defense industry relies on machined parts for manufacturing defense equipment, firearm components, military vehicles, and munitions. The parts’ accuracy, reliability, and durability are crucial for military applications.
9. Consumer Goods: Machined parts also find applications in consumer goods, including kitchen appliances, power tools, home electronics, and sporting equipment. These parts provide the necessary strength and precision required for safe and efficient operation.
10. Construction and Infrastructure: In the construction sector, machined parts are utilized for producing heavy machinery, structural components, and specialized tools. These parts enable efficient construction processes and ensure long-lasting infrastructure.
Machined parts’ applications are vast and diverse, impacting various industries and contributing to technological advancements, safety, and overall quality across multiple sectors.
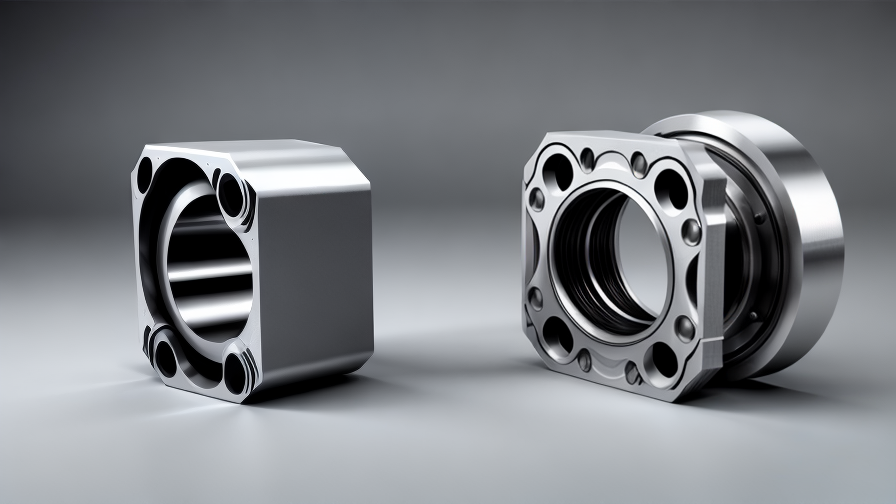
The Work Process and how to use machined parts
The work process of using machined parts involves several steps to ensure proper assembly and functionality.
First, the machined parts are carefully inspected for any defects or imperfections. This ensures that the parts meet the necessary specifications and will function properly within the assembly.
Next, the parts are assembled according to the design specifications. This may involve using specialized tools or equipment to properly align and secure the parts together.
Once the assembly is complete, the machined parts may need to undergo further testing to ensure they are functioning correctly. This can involve running the parts through various tests and inspections to verify their performance.
Finally, the assembled parts can be used in different applications such as automotive, aerospace, or machinery industries. The machined parts are crucial components in the production of various products and play a significant role in ensuring the functionality and efficiency of these products.
To use machined parts effectively, it is essential to follow specific guidelines and procedures provided by the manufacturer. This can include proper handling, storage, and maintenance of the parts to ensure their longevity and performance.
Overall, the work process of using machined parts involves careful inspection, assembly, testing, and application of the parts in various industries. By following these steps and guidelines, machined parts can be effectively utilized in different applications to improve productivity and performance.
Quality Testing Methods for machined parts and how to control the quality
Quality testing methods for machined parts involve a combination of visual inspection, dimensional measurement, and non-destructive testing techniques. These methods aim to ensure that the machined parts meet the required specifications and quality standards. Here are some common testing methods and quality control measures:
1. Visual Inspection: Inspectors visually examine the appearance of machined parts for any defects, such as surface roughness, scratches, burrs, or color variations. This is often the first step in quality testing.
2. Dimensional Measurement: Precision instruments like calipers, micrometers, gauges, and Coordinate Measuring Machines (CMMs) are used to measure critical dimensions of machined parts. These measurements are compared with design specifications to ensure accuracy.
3. Non-Destructive Testing (NDT): Various NDT methods can be employed to evaluate the quality of machined parts without causing damage. Common NDT techniques include liquid penetrant testing, magnetic particle inspection, ultrasonic testing, radiographic testing, and eddy current testing.
4. Statistical Process Control (SPC): Implementing SPC techniques helps identify and control potential quality issues. Data is collected and analyzed to detect variations from the expected quality levels, enabling continuous quality improvement.
5. Design of Experiments (DOE): DOE involves planned testing to investigate the effects of variables on the quality of machined parts. By systematically varying factors, engineers can optimize manufacturing processes and improve quality control methods.
6. Quality Management Systems (QMS): Establishing a QMS, such as ISO 9001, ensures that quality control processes are properly documented, implemented, and maintained. QMS frameworks help standardize procedures, track non-conforming products, and promote accountability.
7. Regular Auditing: Conduct internal and external audits to assess adherence to quality standards, operational processes, and improvement opportunities. Audits assist in identifying potential problems and making necessary adjustments to maintain quality.
To control quality, organizations establish clear quality objectives, train and educate personnel, and promote a culture of quality throughout the manufacturing process. Strict adherence to standardized procedures, well-defined processes, and continuous training and improvement are crucial in ensuring that machined parts meet the desired quality specifications.
machined parts Sample Policy and Post-Purchase Considerations for machined parts from China
Sample Policy:
– All machined parts will undergo strict quality control measures before shipment to ensure they meet the required specifications.
– Any defective or non-conforming parts will be replaced or refunded.
– Shipping and delivery timelines will be clearly communicated to the customer.
– Customers can request for customization or special packaging for an additional fee.
– Bulk orders may be eligible for discounts.
Post-Purchase Considerations:
– Inspect the machined parts upon receipt to ensure they meet the required specifications.
– Test the parts in the intended application to ensure proper functionality.
– Contact the supplier immediately if there are any issues or concerns with the parts.
– Provide feedback to the supplier on the quality and performance of the machined parts.
– Consider establishing a long-term relationship with the supplier for future orders.
Overall, when purchasing machined parts from China, it is important to establish clear policies for quality control, shipping, and customer service. Additionally, customers should thoroughly inspect and test the parts upon receipt and provide feedback to the supplier for continuous improvement. By following these considerations, customers can ensure a successful purchase of machined parts from China.
Sourcing machined parts from China: Opportunities, Risks, and Key Players
China has become a leading destination for sourcing machined parts due to its competitive pricing, advanced manufacturing capabilities, and large pool of skilled labor. Some of the key opportunities for sourcing machined parts from China include cost savings, access to a wide range of suppliers and technologies, and the ability to scale production quickly.
However, there are also risks involved in sourcing from China, such as quality control issues, language barriers, intellectual property concerns, and the potential for supply chain disruptions. It is important for companies to carefully vet suppliers and establish clear communication channels to mitigate these risks.
Some of the key players in the Chinese machined parts market include Foxconn Technology Group, BYD Company Limited, and Huawei Technologies Co., Ltd. These companies have extensive experience in manufacturing high-quality parts for industries such as automotive, aerospace, and consumer electronics.
Overall, sourcing machined parts from China can be a cost-effective and efficient solution for companies looking to expand their supply chains and access new technologies. By carefully evaluating the opportunities and risks involved, companies can make informed decisions about sourcing from China and build successful partnerships with reliable suppliers.
How to find and select reliable machined parts manufacturers in China,use google search manufacturers and suppliers
When searching for reliable machined parts manufacturers in China, utilizing Google search can be an effective method. Here are some steps to follow:
1. Identify specific keywords: Begin by determining the keywords that accurately describe the machined parts you are looking for. For example, “machined parts manufacturer,” “precision machining China,” or “CNC machining services.”
2. Conduct a search: Enter these relevant keywords into Google search and evaluate the results. Pay attention to the top organic search results, as they often indicate more reputable and established companies.
3. Evaluate the website: Visit the websites of the manufacturers that appear in the search results. Look for information such as the company’s background, manufacturing capabilities, product range, quality control measures, and certifications. A professional and informative website is generally a positive sign.
4. Check customer reviews and testimonials: Look for any customer reviews or testimonials on the manufacturer’s website or other online platforms. Feedback from previous customers can provide insights into the company’s reliability and the quality of their products.
5. Verify their experience: Look for information on how long the manufacturer has been in business. A company with many years of experience is likely to have better expertise and manufacturing processes.
6. Contact the manufacturer: Reach out to the selected manufacturers for further inquiries. Communication with the manufacturer can help you assess their responsiveness, willingness to provide information, and clarity in their communication.
7. Request for samples or references: Ask the shortlisted manufacturers for samples of their machined parts or references from their existing customers. This will allow you to evaluate the quality of their products and determine their reputation directly.
8. Compare multiple manufacturers: Consider multiple options before making a final decision. Compare factors such as their product quality, pricing, lead times, communication, and customer support. This will help you select the most reliable and suitable manufacturer for your requirements.
By using Google search and thoroughly evaluating the manufacturers based on their website, customer reviews, experience, and direct communication, you can increase the likelihood of finding a reliable machined parts manufacturer in China.
How to check machined parts manufacturers website reliable,use google chrome SEOquake check if ranking in top 10M
To check if a machined parts manufacturer’s website is reliable, you can use Google Chrome with the SEOquake extension. This tool will allow you to see if the website is ranking in the top 10 search results for relevant keywords. Websites that rank highly in search engine results are usually more reputable and trustworthy.
When using SEOquake, look for the website’s position in the search results for keywords related to machined parts manufacturing. If the website is consistently ranking in the top 10, it is likely a reliable source for information and services.
Additionally, you can check for customer reviews and testimonials on the website or third-party review sites. Positive reviews from satisfied customers indicate a good reputation and reliable services.
It is important to also consider the website’s design, user experience, and the information provided. A professional-looking website with clear, accurate information is more likely to be reliable.
In conclusion, to check if a machined parts manufacturer’s website is reliable, use SEOquake to check its search engine ranking, look for positive customer reviews, and consider the overall design and information provided on the site. Following these steps will help you determine the credibility of the manufacturer’s website.
Top 10 machined parts manufacturers in China with each 160 words introduce products,then use markdown create table compare
1. Foxron Precision Metal Parts Co., Ltd.:
Established in 2005, Foxron specializes in manufacturing precision metal parts such as CNC machined components, sheet metal fabrications, and aluminum extrusions. With advanced technology and state-of-the-art machinery, they provide high-quality products for various industries including automotive, electronics, and medical equipment.
2. Dongguan Fuzhan Electronics Technology Co., Ltd.:
Fuzhan Electronics is a leading manufacturer of machined parts with a focus on precision and high-quality. Their products range from CNC turned parts, connectors, and terminals to metal stamping parts. They offer customized solutions and have built a strong reputation for reliability and efficiency.
3. HNS Machining Parts Co., Ltd.:
HNS is known for producing precision machined parts with tight tolerances for industries like aerospace, automotive, and electronics. They provide services in CNC milling, turning, grinding, and surface treatment. Their products exhibit excellent dimensional accuracy and enhanced durability.
4. Suzhou Good-Ark Electronics Co., Ltd.:
Good-Ark Electronics specializes in the production of precision machined parts, mainly focusing on connectors, metal terminals, and pins. They employ advanced CNC machining technology to ensure the highest accuracy and quality. Their products find applications in electrical and electronic equipment.
5. Shenzhen JunFeng Mould Hardware Machine Co., Ltd.:
JunFeng Mould Hardware Machine is a professional manufacturer of various machined parts. Their product range includes precision CNC machining parts, aluminum extrusion, and sheet metal fabrication. They serve industries such as telecommunications, robotics, and semiconductor equipment.
6. Huizhou Haoxin Precision Machinery Co., Ltd.:
Haoxin Precision Machinery is known for delivering high-quality machined parts using advanced CNC machining and turning processes. They offer customizable solutions in various materials like aluminum, brass, and stainless steel. Their products serve industries such as industrial automation, robotics, and medical equipment.
7. Chengdu Yideli Machinery Co., Ltd.:
Yideli Machinery specializes in the production of precision machined parts, ranging from CNC milling and turning to surface treatment. Their products are widely used in automotive, aerospace, and electronics sectors. They are known for their strict quality control and timely delivery.
8. Qingdao Hualuanji Precision Metal Co., Ltd.:
Hualuanji Precision Metal is a prominent manufacturer specializing in CNC machining, stamping, and laser cutting parts. Their products cover a wide range of industries, including auto parts, communications, and power transmission. They prioritize customer satisfaction and offer quick turnaround times.
9. Ningbo BMW Precision Machining Co., Ltd.:
BMW Precision Machining specializes in manufacturing high-precision machined parts using advanced CNC technology. Their products include precision turning parts, milling components, and die casting parts. They cater to industries like automotive, telecommunications, and energy.
10. Dongguan MQ Precision Hardware Co., Ltd.:
MQ Precision Hardware is a leading manufacturer of precision machined parts, including CNC machining, stamping, and turning parts. They offer a wide range of services to industries such as electronics, medical equipment, and automotive. With strict quality control measures, they ensure precise and durable products.
| Manufacturer | Specialization | Industries Served | Notable Features |
|————–|—————-|————————–|——————————————————|
| Foxron | CNC machining | Automotive, Electronics | Advanced technology, High-quality products |
| Fuzhan | Precision parts| Various | Customized solutions, Reliability |
| HNS | Precision | Aerospace, Automotive | Tight tolerances, CNC milling, turning and grinding |
| Good-Ark | Connectors | Electrical, Electronics | High accuracy, Precision machining |
| JunFeng | Machined parts | Telecommunications, Robotics | CNC machining, Extrusion, Sheet metal fabrication |
| Haoxin | Precision parts | Industrial automation | Customizable solutions, CNC machining and turning |
| Yideli | Machined parts | Automotive, Aerospace | Strict quality control, CNC milling, turning |
| Hualuanji | CNC machining | Auto parts, Communications | Stamping, Laser cutting |
| BMW Precision| High-precision | Automotive, Telecommunications | CNC machining, Die casting, Milling |
| MQ Precision | Precision parts | Electronics, Automotive | Various services offered, Strict quality control |
Background Research for machined parts manufacturers Companies in China, use qcc.com archive.org importyeti.com
Machined parts manufacturers in China are a key component of the country’s manufacturing sector, with a strong reputation for producing high-quality and cost-effective products. Companies in this industry often utilize advanced technology and machinery to produce precision parts for a variety of industries, including automotive, aerospace, and electronics.
By using online platforms such as qcc.com, companies can access valuable information on potential suppliers, including company profiles, product offerings, and customer reviews. This allows businesses to make informed decisions when choosing a manufacturer to partner with.
Archive.org is another useful tool for researching machined parts manufacturers in China, as it provides access to historical data on companies’ websites, allowing businesses to track their growth and development over time. This can help companies identify reliable and established manufacturers with a proven track record of producing quality products.
Importyeti.com is a valuable resource for companies looking to import machined parts from China, as it provides data on import trends and statistics. This information can help businesses identify key players in the industry and make informed decisions when sourcing parts from overseas.
Overall, utilizing these online tools can help companies research and identify reputable machined parts manufacturers in China, ultimately leading to successful partnerships and high-quality products.
Leveraging Trade Shows and Expos for machined parts Sourcing in China
Trade shows and expos are invaluable resources for sourcing machined parts in China. These events provide a platform for buyers to connect with a wide range of suppliers, showcase their products, and stay up-to-date with the latest trends in the industry. By attending these events, buyers can evaluate the quality of products, discuss pricing and production capabilities, and build relationships with potential suppliers.
Some of the key benefits of leveraging trade shows and expos for machined parts sourcing in China include:
1. Access to a wide range of suppliers: Trade shows bring together numerous suppliers under one roof, making it easier for buyers to compare products, services, and prices. This allows buyers to find the best fit for their specific needs and requirements.
2. Networking opportunities: Trade shows provide a platform for buyers to network with industry professionals, peers, and potential suppliers. Building relationships with suppliers can lead to better communication, collaboration, and long-term partnerships.
3. Stay up-to-date with industry trends: Attending trade shows and expos allows buyers to stay informed about the latest developments in the industry, including new technologies, materials, and processes. This knowledge can help buyers make more informed decisions when sourcing machined parts in China.
4. Quality control: By meeting suppliers in person and inspecting their products at trade shows, buyers can ensure the quality of machined parts meets their standards. This hands-on approach can help prevent potential quality issues and ensure a smooth sourcing process.
In conclusion, leveraging trade shows and expos for machined parts sourcing in China offers numerous benefits for buyers looking to find reliable suppliers, stay informed about industry trends, and ensure the quality of products. By taking advantage of these opportunities, buyers can make more informed decisions and build successful partnerships with suppliers in China.
The Role of Agents and Sourcing Companies in Facilitating machined parts Purchases from China
Agents and sourcing companies play a vital role in facilitating machined parts purchases from China. These professionals act as intermediaries between buyers and suppliers, helping to bridge the gap between different languages, cultures, and business practices.
Agents and sourcing companies have a deep understanding of the Chinese market and can provide valuable insights into the best suppliers for specific machined parts. They also have existing relationships with reliable manufacturers, allowing them to negotiate better prices and terms on behalf of the buyers.
Additionally, agents and sourcing companies can help buyers navigate the complexities of international trade, including shipping, customs, and quality control. This can save buyers time and money, as well as reduce the risk of potential pitfalls when purchasing machined parts from China.
Overall, agents and sourcing companies play a crucial role in simplifying the procurement process and ensuring a smooth transaction between buyers and suppliers. Their expertise and industry knowledge can help buyers secure high-quality machined parts at competitive prices, making them an essential partner in sourcing products from China.
Price Cost Research for machined parts manufacturers Companies in China, use temu.com and 1688.com
When it comes to price cost research for machined parts manufacturers in China, two reliable platforms to consider are temu.com and 1688.com. These websites offer a comprehensive range of suppliers and manufacturers, allowing you to connect with potential partners and compare prices.
Temu.com is a leading B2B platform specifically tailored for manufacturing and supply chain management. This website provides access to a plethora of verified and reputable manufacturers, including those specializing in machined parts. Temu.com offers a user-friendly interface where you can easily search for specific products or manufacturers based on your requirements. The platform also enables you to request quotations from multiple suppliers and engage in direct communication to negotiate prices.
1688.com, owned by Alibaba Group, is known as China’s largest wholesale online marketplace. This platform connects buyers with suppliers from various industries, including machined parts manufacturers. Although the website is primarily in Chinese, English translations and browser extensions can be utilized to navigate the platform effectively. 1688.com offers a vast selection of suppliers, allowing you to explore different options and compare prices to find the best deal.
To conduct price cost research, start by searching for specific machined parts on both temu.com and 1688.com. Once you have shortlisted potential suppliers, you can evaluate their pricing strategies by requesting quotations or directly contacting them. It is advisable to clearly specify your requirements to receive accurate pricing information. Additionally, consider factors such as minimum order quantities, manufacturing capabilities, quality certifications, and lead times while comparing prices.
It is important to note that bargaining and negotiations are common in the Chinese manufacturing industry. Therefore, it is recommended to engage in direct communication with suppliers to further discuss pricing, negotiate discounts, and clarify any concerns.
Overall, temu.com and 1688.com are valuable resources for conducting price cost research when looking for machined parts manufacturers in China. Utilizing these platforms, you can efficiently compare prices, evaluate suppliers, and make informed decisions to optimize your sourcing process.
Shipping Cost for machined parts import from China
When importing machined parts from China, one of the major costs to consider is shipping. There are several factors that can impact the shipping cost, including the size and weight of the parts, the shipping method chosen, and the distance between the supplier in China and the importer’s location.
The most common shipping methods for importing machined parts from China include air freight, sea freight, and courier services. Air freight is typically the fastest but also the most expensive option, while sea freight is slower but more cost-effective for larger shipments. Courier services like DHL, FedEx, and UPS may be a good option for smaller and more urgent shipments.
The size and weight of the machined parts will also play a significant role in determining the shipping cost. Larger and heavier parts will require more space and may incur additional fees for handling and transportation. It is important to provide accurate dimensions and weight to the shipping company to receive an accurate quote.
The distance between the supplier in China and the importer’s location will also impact the shipping cost. Longer distances will naturally result in higher shipping costs, so it is important to consider the location of the supplier when calculating the total cost of importing the machined parts.
In conclusion, when importing machined parts from China, it is essential to consider the size and weight of the parts, the shipping method chosen, and the distance between the supplier and importer. By carefully considering these factors and comparing quotes from different shipping companies, it is possible to minimize shipping costs and ensure a smooth import process.
Compare China and Other machined parts Markets: Products Quality and Price,Visible and Hidden Costs
China is known as the world’s largest market for machined parts, accounting for a significant portion of global production. When comparing China to other markets, such as those in North America and Europe, several factors come into play, including product quality, price, and visible and hidden costs.
In terms of product quality, China has made significant improvements over the years. Many Chinese manufacturers now produce high-quality machined parts that meet international standards. However, there can still be variations in quality, especially from smaller or less reputable companies. In comparison, markets in North America and Europe have a longstanding reputation for producing high-quality machined parts. Companies in these markets often adhere to strict quality control measures and have robust certification processes, ensuring consistent product quality.
Price is a crucial consideration when comparing markets. China’s competitive advantage lies in its relatively low labor and production costs. Chinese manufacturers can offer machined parts at lower prices compared to their counterparts in North America and Europe. However, it is important to note that price alone should not be the sole determining factor. Other markets may have higher prices due to factors such as higher labor costs or stricter environmental regulations. In these cases, customers may be paying more for the added value of quality and compliance.
Visible costs, such as production and shipping costs, can be relatively transparent and easily compared across different markets. China has an extensive and efficient supply chain network, allowing for cost-effective production and shipping logistics. This advantage, combined with economies of scale, contributes to China’s competitiveness in visible costs. However, hidden costs, such as intellectual property risks, regulatory compliance, and potential delays, must also be considered. China has faced criticism for intellectual property infringement, which can incur significant costs for businesses. Moreover, navigating China’s complex regulatory landscape can be challenging, and unexpected delays or compliance issues may add additional costs.
Overall, China’s machined parts market has made strides in terms of product quality and competitive pricing. However, customers must carefully consider visible and hidden costs when comparing markets. While China may offer cost advantages, other markets may provide higher product quality and fewer potential risks. Ultimately, the decision will depend on the specific needs and requirements of the customer.
Understanding Pricing and Payment Terms for machined parts: A Comparative Guide to Get the Best Deal
When it comes to machined parts, understanding pricing and payment terms is essential to getting the best deal possible. Here are some key factors to consider when negotiating with suppliers:
1. Price per piece: Be sure to compare quotes from multiple suppliers to ensure you are getting a competitive price per piece. Keep in mind that prices can vary depending on the complexity of the part, materials used, and quantity ordered.
2. Minimum order quantities: Some suppliers may require a minimum order quantity to secure a lower price per piece. Consider your production needs and budget constraints when negotiating minimum order quantities with suppliers.
3. Payment terms: Negotiate payment terms that work best for your business, whether that be net 30, net 60, or another option. Some suppliers may offer discounts for early payment or bulk orders, so be sure to inquire about these options.
4. Tooling costs: If you require custom tooling for your machined parts, be sure to factor in these costs when comparing quotes from different suppliers. Consider negotiating tooling costs into the unit price or amortizing them over the life of the part to reduce upfront expenses.
5. Shipping and handling fees: Don’t forget to factor in shipping and handling fees when comparing quotes from different suppliers. Consider negotiating bulk shipping discounts or arranging for local pickup to reduce these costs.
By understanding pricing and payment terms for machined parts and negotiating effectively with suppliers, you can ensure you are getting the best deal possible for your business. Take the time to research and compare quotes, and don’t be afraid to negotiate terms that work best for your specific needs.
Chinese Regulations and Industry Standards Certifications for machined parts,Import Regulations and Customs for machined parts from China
In China, machined parts need to adhere to various regulations and industry standards in order to ensure quality and safety. Some common certifications required for machined parts include ISO 9001 for quality management systems, ISO 14001 for environmental management systems, and TS 16949 for automotive industry quality management systems. Additionally, specific industry standards may apply depending on the type of machined parts being produced.
When importing machined parts from China, it is important to be aware of the relevant regulations and customs procedures. The import of machined parts is subject to China’s import regulations, which may include tariffs, quotas, and other trade barriers. It is important to work with a reputable customs broker who can help navigate the complex import process and ensure compliance with all applicable regulations.
Customs procedures for imported machined parts typically involve submitting a bill of lading, commercial invoice, packing list, and other relevant documentation to customs authorities. It is also important to properly classify the machined parts according to the Harmonized System (HS) codes to determine the applicable duties and taxes.
Overall, importing machined parts from China requires a thorough understanding of regulations, industry standards, and customs procedures to ensure a smooth and compliant import process. Working with knowledgeable partners and staying informed about regulatory changes can help mitigate risks and ensure successful importation of machined parts from China.
Sustainability and Environmental Considerations in machined parts Manufacturing
Sustainability and environmental considerations are becoming increasingly important in the manufacturing industry, particularly in the production of machined parts. Machined parts manufacturing involves the use of various machines, tools, and materials that can potentially impact the environment. Therefore, implementing sustainable practices in this sector is crucial for minimizing the environmental footprint and ensuring a greener future.
One key aspect of sustainability in machined parts manufacturing is energy efficiency. By optimizing the energy consumption of machines and equipment, manufacturers can reduce their overall carbon footprint. This can be accomplished through the use of energy-efficient machinery, regular maintenance to prevent energy wastage, and the implementation of automation technologies that enable machines to operate more efficiently.
Another significant consideration is the use of raw materials. Machined parts manufacturing often involves the use of metals, plastics, and other materials extracted from the earth. To minimize the environmental impact, it is important to prioritize the use of recycled or renewable materials. This can include using reclaimed scrap materials or employing recyclable alternatives to traditional materials.
To further enhance sustainability, manufacturers should also focus on waste reduction and proper waste management practices. This includes implementing recycling programs for both production waste and end-of-life products, as well as adopting responsible disposal methods for hazardous materials. Minimizing waste not only benefits the environment but can also provide cost savings for the company.
Additionally, manufacturers should assess their supply chain and consider partnering with suppliers who prioritize sustainability. This includes sourcing materials from environmentally conscious suppliers who adhere to sustainable practices throughout their own production processes.
Lastly, machined parts manufacturers can explore opportunities for product design optimization to reduce material usage, weight, and transportation costs. By creating lightweight designs or utilizing alternative materials, manufacturers can contribute to reducing the carbon footprint associated with the production and transportation of machined parts.
In conclusion, sustainability and environmental considerations play a crucial role in machined parts manufacturing. By focusing on energy efficiency, raw material selection, waste reduction, responsible waste management, and supply chain sustainability, manufacturers can positively impact the environment while also driving cost savings and improving their overall competitiveness.
List The Evolution history of “machined parts”
The evolution history of machined parts can be traced back thousands of years to the ancient civilizations. Initially, machined parts were created manually by skilled craftsmen using simple tools like hammers, chisels, and saws. These early machines were mainly used for shaping and cutting wood, stone, and metal.
The Industrial Revolution, which took place from the 18th to the 19th century, brought significant advancements in machining technology. The invention of steam-powered machinery revolutionized the manufacturing industry. The introduction of the steam engine enabled the development of mechanized tools such as lathes, drill presses, and milling machines. This allowed for greater precision, efficiency, and automation in producing machined parts.
In the late 19th century, the advent of the assembly line and mass production techniques further transformed machining. The American engineer Eli Whitney is credited with inventing the concept of interchangeable parts, which revolutionized manufacturing. This development allowed for the mass production of identical parts, leading to the standardization of machined components and the creation of complex machinery.
The early 20th century witnessed the rise of electrical and hydraulic machinery, contributing to further advancements in the machining field. Electrically powered machines provided increased speed and control, while hydraulic systems offered greater force and precision. These technologies opened up new possibilities for industrial automation and the production of more intricate and precise machined parts.
The mid-20th century witnessed the emergence of computer numerical control (CNC), which revolutionized machining. CNC machines utilized computer controls to automate the machining process, eliminating the need for manual intervention. This breakthrough allowed for higher accuracy, repeatability, and the production of complex geometries. Furthermore, advancements in computer-aided design (CAD) and computer-aided manufacturing (CAM) software facilitated the design and programming of intricate machined parts.
Since then, machining technology has continued to evolve rapidly, driven by advancements in materials, cutting tools, and automation. Today, highly advanced CNC machines can produce complex parts with minimal human involvement, utilizing techniques such as multi-axis machining and additive manufacturing. Machined parts play a crucial role in various industries, including automotive, aerospace, electronics, and medical devices, enabling the creation of innovative and sophisticated products.
The Evolution and Market Trends in machined parts Industry
The machined parts industry has experienced significant evolution and market trends in recent years. Technological advancements, changing customer demands, and competitive factors have all played a role in shaping the industry’s trajectory.
One of the notable shifts in the machined parts industry is the adoption of computer numerical control (CNC) machining. This technology has revolutionized the way parts are manufactured by enabling high precision, repeatability, and efficiency. CNC machines can produce complex parts with minimal human intervention, reducing labor costs and improving overall productivity. As a result, many manufacturers have embraced CNC machining, leading to an increased demand for CNC machined parts.
Another trend in the industry is the growing demand for lightweight and durable materials. Automotive, aerospace, and electronics sectors, in particular, have witnessed a drive towards using advanced materials such as aluminum alloys, titanium, and composites. Machined parts made from these materials offer superior strength-to-weight ratios, improved fuel efficiency, and enhanced performance. To meet these market demands, machined parts manufacturers have invested in equipment capable of handling these materials effectively.
Furthermore, there has been a notable increase in the customization and quick turnaround of machined parts. With advances in CAD/CAM software and rapid prototyping technologies, customers are seeking shorter lead times for their specific part requirements. Machined parts manufacturers have responded by streamlining their production processes, utilizing simulation software for quick design iterations, and offering rapid prototyping services. This shift has resulted in improved customer satisfaction and increased market competitiveness.
Moreover, the global market for machined parts has witnessed geographical changes. Traditionally, North America and Europe have been major manufacturing hubs. However, there has been a shift towards emerging markets like China, India, and Southeast Asia due to lower labor costs and growing industrial capabilities. These regions have experienced significant investments in infrastructure and technology, attracting international clients and contributing to the overall growth of the machined parts industry.
In conclusion, the machined parts industry has evolved significantly over the years. The adoption of CNC machining, utilizing advanced materials, customization, and quick turnaround, as well as the shift towards emerging markets, have all contributed to the industry’s growth and market trends. To stay competitive in this evolving landscape, manufacturers must continue to embrace technological advancements, meet customer demands, and explore new market opportunities.
Custom Private Labeling and Branding Opportunities with Chinese machined parts Manufacturers
If you are looking for custom private labeling and branding opportunities with Chinese machined parts manufacturers, you are in luck. Many Chinese manufacturers offer the option to customize their products with your own branding, logo, and packaging. This can be a great way to differentiate your products in the market and build a strong brand identity.
When working with Chinese machined parts manufacturers, it is important to communicate your branding requirements clearly and provide any artwork or designs that you want to be incorporated into the product. Some manufacturers may also offer design services to help you create a unique branding concept for your products.
It is also important to consider the quality and reputation of the manufacturer before entering into a partnership. Look for manufacturers with a track record of producing high-quality products and excellent customer service. You may also want to consider visiting the manufacturer’s facilities in person to ensure that they meet your standards for quality and production capabilities.
Overall, custom private labeling and branding opportunities with Chinese machined parts manufacturers can be a great way to elevate your products and establish a strong brand presence in the market. By working closely with the manufacturer and clearly communicating your branding requirements, you can create unique and customized products that stand out from the competition.
Tips for Procurement and Considerations when Purchasing machined parts
When procuring machined parts, it is important to consider several factors to ensure that you are getting quality parts that meet your specifications. Here are some tips and considerations to keep in mind:
1. Define your requirements: Before purchasing machined parts, clearly define your requirements in terms of dimensions, tolerances, materials, finishes, and quantities. This will help you communicate effectively with suppliers and ensure that you get the parts you need.
2. Quality assurance: Look for suppliers that have a proven track record of delivering high-quality machined parts. Consider asking for samples or references to verify the quality of their work.
3. Cost: While cost is an important factor, it should not be the sole determining factor. Consider the overall value of the parts, taking into account factors such as quality, lead time, and customer service.
4. Lead time: Consider the lead time required to manufacture the parts and factor this into your procurement timeline. Make sure to communicate your delivery deadlines with the supplier to ensure timely delivery.
5. Supplier capabilities: Evaluate the supplier’s capabilities, including their equipment, expertise, and experience with similar projects. A supplier with the right capabilities is more likely to meet your specifications and deliver high-quality parts.
6. Communication: Establish clear communication channels with the supplier to ensure that any issues or changes can be addressed promptly. Regular communication can help prevent misunderstandings and ensure that the project stays on track.
7. Consider material selection: Depending on the application of the machined parts, different materials may be required. Make sure to discuss material options with the supplier to select the most suitable material for your project.
Overall, thorough planning, clear communication, and careful consideration of factors such as quality, cost, lead time, and supplier capabilities are essential for successful procurement of machined parts. By following these tips and considerations, you can ensure that you get the parts you need to complete your project successfully.
FAQs on Sourcing and Manufacturing machined parts in China
Q: Why should I consider sourcing and manufacturing machined parts in China?
A: China has become a popular destination for sourcing and manufacturing machined parts due to its cost-effective production capabilities. Chinese manufacturers often offer lower labor costs, allowing for greater cost savings compared to other countries. Furthermore, China has a strong manufacturing infrastructure, advanced technology, and a large pool of skilled engineers and technicians. This makes it an attractive option for businesses looking to produce machined parts at scale.
Q: What types of machined parts can be sourced and manufactured in China?
A: China has a wide range of capabilities in machining processes, allowing for the production of various types of machined parts. Some common examples include CNC milled parts, CNC turned parts, precision machined components, custom-made parts, and prototypes. These parts can be made from various materials like metals (aluminum, steel, titanium) or plastics, depending on the requirements of the project.
Q: How can I ensure the quality of machined parts sourced from China?
A: To ensure the quality of machined parts sourced from China, it is essential to work with reputable manufacturers who have a proven track record of delivering high-quality products. Conducting thorough research, reading reviews, and requesting samples or prototypes can help assess the manufacturer’s capabilities. Additionally, implementing a comprehensive quality control process and inspecting the parts at each stage of production can help identify any deviations from the specifications and ensure adherence to the required standards.
Q: What is the typical lead time for manufacturing machined parts in China?
A: The lead time for manufacturing machined parts in China varies depending on several factors, including the complexity of the design, quantity required, and the manufacturer’s production capacity. Generally, lead times can range from a few weeks to a few months, with smaller orders typically having shorter lead times. It is crucial to communicate the desired delivery timeline with the manufacturer to ensure realistic expectations and timely production.
Q: What are the common challenges when sourcing and manufacturing machined parts in China?
A: Some common challenges include communication barriers due to language differences, potential intellectual property risks, and the perception of lower quality products from China. To minimize these challenges, working with manufacturers who have English-speaking staff, protecting intellectual property through legal agreements, and carefully evaluating the manufacturer’s quality control processes can be beneficial.
In summary, sourcing and manufacturing machined parts in China can offer cost-effectiveness, a wide range of capabilities, and access to a well-established manufacturing infrastructure. With proper research, quality control measures, and collaboration with reputable manufacturers, businesses can successfully source high-quality machined parts from China.
Why contact sourcifychina.com get free quota from reliable machined parts suppliers?
Sourcifychina.com offers a convenient and trustworthy platform for businesses looking to source reliable machined parts suppliers in China. By contacting Sourcifychina.com, you can easily get a free quota from reputable suppliers who have been vetted for quality and reliability.
This service saves you valuable time and effort by connecting you with trustworthy suppliers who can meet your specific needs. The platform also ensures that you receive competitive pricing and high-quality products, giving you peace of mind when sourcing machined parts from China.
In addition, Sourcifychina.com has a team of experts who can provide guidance and support throughout the sourcing process. They can help you navigate any potential challenges that may arise when working with overseas suppliers, ensuring a smooth and successful sourcing experience.
By utilizing Sourcifychina.com, you can access a wide network of reliable machined parts suppliers in China, all while saving time and effort in the sourcing process. Don’t hesitate to contact Sourcifychina.com to get your free quota and start sourcing high-quality machined parts from trusted suppliers today.