Introduce about machines for packaging food guide,Qulity,Cost,Supplier,Certification,Market,Tips,FAQ
Machines for packaging food are essential in the food processing industry as they ensure the efficient and safe packaging of various food products. These machines help maintain the quality of the food, reduce costs, and comply with industry standards and certifications.
In terms of quality, food packaging machines are designed to handle various types of food items, such as dry goods, liquids, and perishable foods. They are equipped with advanced technology to ensure precise and consistent packaging, minimizing the chances of contamination or spoilage. These machines also help in preserving food freshness and extending the shelf life of the packaged products.
Cost-wise, investing in food packaging machines can initially seem expensive; however, they bring long-term cost savings. These machines automate the packaging process, reducing the need for manual labor and minimizing human errors. Additionally, they optimize packaging materials, leading to reduced material costs and waste. Over time, the efficiency and productivity gains from these machines outweigh the initial investment.
When looking for a supplier of food packaging machines, it is crucial to consider their reputation, experience in the industry, and after-sales service. A reliable supplier will offer quality machines, provide technical support, and ensure timely maintenance and spare parts availability.
Most food packaging machines comply with industry certifications and standards such as ISO, HACCP, and CE. These certifications demonstrate the machines’ adherence to health, safety, and quality regulations, ensuring that the packaged food meets the necessary requirements for distribution and consumption.
The market for food packaging machines is experiencing growth due to the increasing demand for packaged food products. Changing consumer lifestyles and rising disposable incomes have led to a surge in ready-to-eat and convenience foods, driving the need for efficient packaging solutions.
Tips for using food packaging machines include regular maintenance to keep them running smoothly and extending their lifespan. Proper training and supervision of operators are essential to ensure the machines are utilized correctly and safely. Keeping up with technological advancements and industry trends can also help businesses stay competitive in the market.
FAQs related to food packaging machines may revolve around the types of food products they can handle, the maintenance requirements, the compatibility with different packaging materials, and the warranty terms. Businesses may also inquire about customization options, installation processes, and post-purchase support from the supplier.
In conclusion, food packaging machines play a vital role in maintaining the quality, minimizing costs, and complying with industry standards in the food processing sector. Choosing the right supplier, considering certifications, and keeping up with market trends can help businesses optimize their packaging operations and meet consumer demands efficiently.
Types of machines for packaging food
There are various types of machines used for packaging food, each designed to perform specific tasks efficiently and effectively. These machines are essential in the food industry as they automate the packaging process, ensuring high productivity and consistent results. Here are some of the common types of machines used for packaging food:
1. Filling machines: These machines are used to fill containers or packages with food products. They can handle both liquid and solid materials and are available in different designs such as piston fillers, auger fillers, and vacuum fillers, depending on the product’s nature and viscosity. Filling machines are highly accurate and can be easily adjusted to meet specific packaging requirements.
2. Sealing machines: Sealing machines are used to create airtight seals on packages, preserving the food’s freshness and extending its shelf life. There are various types of sealing machines, including heat sealers, induction sealers, and band sealers. Heat sealers are commonly used for sealing pouches or bags, while induction sealers are ideal for sealing containers with foil seals by generating electromagnetic energy. Band sealers, on the other hand, are suitable for sealing larger bags or pouches continuously.
3. Labeling machines: These machines apply labels to food packaging, providing product information, branding, and regulatory compliance. Labeling machines can be automatic or semi-automatic, and they often work in conjunction with other packaging machines. They can apply labels to different types of packaging, including bottles, jars, cans, and pouches. Labeling machines offer high precision and versatility in label placement.
4. Wrapping machines: Wrapping machines are used for encasing food products in a protective film or wrapper. They are commonly used for wrapping products such as candies, chocolates, bars, and biscuits. There are different types of wrapping machines, including flow wrap machines, shrink wrap machines, and stretch wrap machines. Flow wrap machines use continuous plastic film to wrap individual products, while shrink wrap machines use heat to shrink a plastic film tightly around the product. Stretch wrap machines are designed to secure large pallets or bundles of products with stretchable plastic film.
5. Cartoning machines: Cartoning machines automate the process of placing food products into cartons or boxes. They are commonly used for packaging items like snacks, cereals, and frozen foods. Cartoning machines can fold and seal cartons, insert the food products, and sometimes apply additional labels or promotional materials. They offer high-speed packaging capabilities, reducing labor costs and improving efficiency.
Overall, these types of packaging machines play a crucial role in the food industry by ensuring the safety, quality, and convenience of packaged food products, while also meeting production demands. Their automation capabilities enhance productivity, reduce errors, and maintain consistency in packaging, ultimately benefiting both manufacturers and consumers.
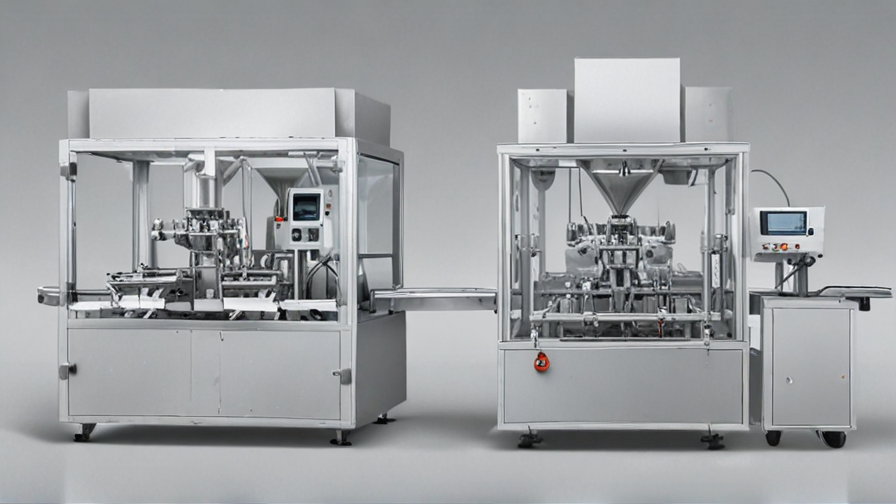
Pros and Cons of Using machines for packaging food
Using machines for packaging food has become increasingly common in the food manufacturing industry. This automated process offers several advantages, but there are also some disadvantages that need to be considered. Here are the pros and cons of using machines for packaging food:
Pros:
1. Cost efficiency: Machines can complete packaging tasks at a much faster rate compared to manual labor, resulting in increased productivity and reduced labor costs. By automating the packaging process, companies can save on manpower and allocate resources more efficiently.
2. Improved accuracy and consistency: Human error is minimized when machines are used for packaging. They can consistently perform tasks with precision, ensuring that each food product is packaged in the same way. This leads to greater uniformity in packaging quality and appearance, enhancing the brand image.
3. Enhanced hygiene and safety: Machines are designed to meet strict hygiene standards and can be easily cleaned and sanitized according to food safety regulations. This helps reduce the risk of contamination and ensures that the packaging process is as clean and safe as possible.
4. Increased production capacity: High-speed packaging machines can handle large quantities of food products in a short period. This allows manufacturers to meet market demands and improve their production capacity, resulting in higher sales and customer satisfaction.
Cons:
1. Initial investment and maintenance costs: Purchasing and installing packaging machinery can be a significant investment for food manufacturers. Maintenance and repair costs should also be considered, as any breakdown or malfunction can disrupt the packaging process and lead to expensive repairs.
2. Limited flexibility: Machines are designed for specific packaging formats, which means they may not be adaptable to sudden changes in packaging requirements. Companies may need to invest in different machines or costly modifications to accommodate diverse packaging needs.
3. Skill requirement: Operating and maintaining packaging machines requires specialized skills and knowledge. Companies may need to invest in training their staff or hire specialized technicians, which can add to the overall operational costs.
4. Limited customization: Machines are designed for standard packaging formats, making it challenging to personalize packaging or respond to unique customer demands. This may limit a company’s ability to differentiate its products in the market.
In conclusion, utilizing machines for packaging food offers cost efficiency, improved accuracy, enhanced hygiene, and increased production capacity. However, the initial investment cost, limited flexibility, skill requirement, and limited customization should also be taken into consideration when deciding to automate the packaging process.
machines for packaging food Reference Specifications (varies for different product)
When it comes to packaging food products, it is essential to use machines that meet specific reference specifications. These specifications vary depending on the type of product being packaged. The goal is to ensure that the packaging process is efficient, safe, and meets the necessary industry standards.
One common specification for food packaging machines is the capacity to handle different types of materials, such as plastic, paper, or metal. This allows for versatility in packaging options and enables businesses to meet customer demands. In addition, machines should be able to handle various sizes and shapes of packaging, as different food products require different packaging designs.
Another important specification is the capability to maintain the integrity of the food product throughout the packaging process. This involves the use of machines that can seal the packaging tightly, preventing any leaks or contamination. Some food products, like liquids or perishables, may require specialized packaging machines with features like vacuum sealing or gas flushing to extend product shelf life.
Packing speed and efficiency are also crucial considerations. Machines should be able to handle high-volume packaging needs without compromising the quality of the product. This requires reliable and durable machines that can operate continuously for long periods.
Food safety is of utmost importance in the packaging process. Machines should be designed to minimize the risk of contamination. This can include features such as easy-to-clean surfaces, hygienic materials, and the ability to meet sanitation standards. Additionally, machines should be equipped with safety features to protect operators from potential hazards during operation.
In terms of product-specific specifications, different food products may have unique packaging requirements. For example, fragile products like biscuits or chips may require machines with gentle handling mechanisms to prevent breakage. Likewise, fresh produce may need machines that can handle moisture or temperature control during the packaging process.
Overall, the selection of packaging machines should adhere to specific reference specifications depending on the type of food product being packaged. It is crucial to ensure that the machines can handle different materials and sizes, maintain the integrity of the food product, operate with speed and efficiency, prioritize food safety, and meet specific requirements for each type of food product. By choosing the right machines, businesses can ensure their food products are packaged safely and efficiently, meeting both regulatory standards and customer expectations.
Applications of machines for packaging food
Machines for packaging food have revolutionized the food industry by providing efficient, reliable, and hygienic packaging solutions. These machines are used in various aspects of food packaging, including primary, secondary, and tertiary packaging.
In primary packaging, machines are utilized for enclosing food products directly. For example, form-fill-seal machines are commonly used to form packages from a roll of packaging film, fill them with the food product, and seal them. These machines are versatile and can handle a wide range of food products such as snacks, liquid beverages, and frozen foods.
Secondary packaging involves enclosing primary packages for protection, handling, and branding purposes. Machines like case erectors, case packers, and carton sealers are used to assemble and seal cardboard or corrugated boxes, grouping and packing individual primary packages. These machines improve packaging efficiency, reduce labor costs, and ensure consistency in packaging quality.
Tertiary packaging focuses on the transportation and storage of packaged food products. Here, machines such as stretch wrappers, palletizers, and shrink wrappers are employed to secure and stabilize loads of secondary packages onto pallets. These machines automate the wrapping and stacking process, enhancing safety during transportation and storage.
Additionally, specialized machines cater to specific food packaging needs. For instance, vacuum sealers remove air from packages, extending the shelf life of perishable products. Modified atmosphere packaging (MAP) machines replace the air in packages with a mixture of gases to slow down food spoilage. Both methods help maintain food freshness and quality.
Moreover, labeling machines apply informative labels, barcodes, and expiry dates on food packages. This aids in product identification, traceability, and compliance with food safety regulations. Inspection machines such as metal detectors and X-ray systems ensure product integrity by identifying foreign objects or contaminants in packaged food.
Overall, the applications of machines for packaging food are vast and all-encompassing. From primary packaging to tertiary packaging, and specialized processes like vacuum sealing and MAP, these machines have significantly improved the efficiency, hygiene, and safety of food packaging operations. They contribute to the preservation, branding, and handling of food products, ultimately meeting the needs of both manufacturers and consumers.
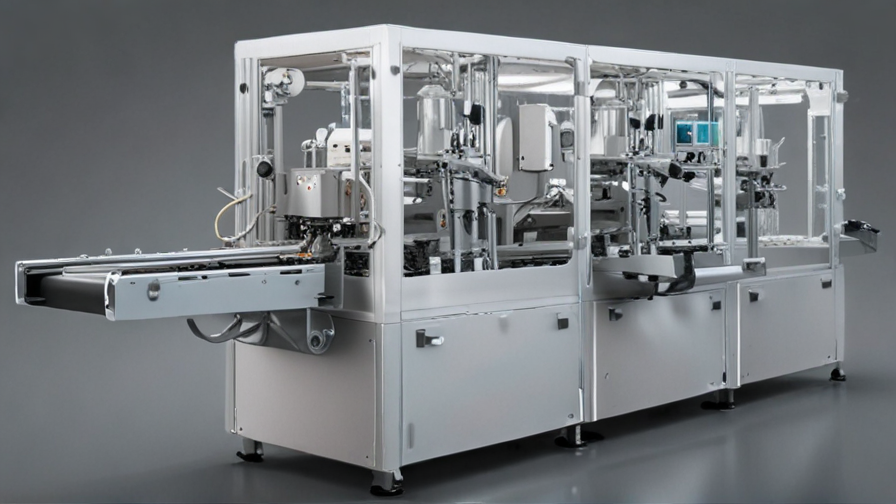
The Work Process and how to use machines for packaging food
Packaging food involves several steps and the use of machines plays a crucial role in ensuring efficiency and quality. The work process typically includes the following steps:
1. Product Preparation: Before packaging, the food product must be properly prepared. This may involve cleaning, cutting, sorting, or cooking the food items to meet specific requirements.
2. Product Weighing and Filling: To ensure consistency in packaging, machines are used to accurately weigh and fill the products into containers. This can be achieved using volumetric fillers, weigh scales, or auger fillers depending on the food type and packaging requirements.
3. Sealing: Once the product is filled, it needs to be properly sealed to preserve freshness and prevent contamination. Machines like heat sealers, induction sealers, or vacuum sealers are employed to securely seal the containers or pouches.
4. Labeling and Coding: Machines equipped with labeling and coding systems are utilized to apply product labels and date codes. This ensures traceability and compliance with regulations. Additionally, barcode scanners may be used for inventory management and tracking purposes.
5. Secondary Packaging: For convenience and protection, food products are often grouped together in secondary packaging. Machines can automate the process of collating, stacking, and bundling the primary packages into boxes or cartons. Case packers, wrap-around packers, or tray formers are commonly utilized for secondary packaging.
6. Inspection and Quality Control: Throughout the packaging process, machines are employed to inspect the products for any defects or foreign objects. This helps ensure the quality and safety of the packaged food. Advanced technologies such as X-ray systems or metal detectors may be used for thorough inspection.
7. Palletizing and Shipment: Finally, once the packaged food products are ready, machines assist in palletizing them for easy storage, handling, and shipment. Palletizers automatically stack the cases onto pallets according to specific patterns, optimizing space utilization and increasing efficiency.
To use machines for packaging food effectively, operators should receive proper training on their operation and maintenance. Regular maintenance and calibration of machines are essential to ensure consistent performance and prevent breakdowns. Additionally, adhering to food safety regulations and maintaining a clean environment is crucial for hygienic packaging.
In summary, employing machines in the food packaging process streamlines operations, improves efficiency, and maintains quality standards. Through various stages such as product preparation, weighing and filling, sealing, labeling and coding, secondary packaging, inspection, and palletizing, machines play a vital role in ensuring safe and efficient packaging of food products.
Quality Testing Methods for machines for packaging food and how to control the quality
Quality testing methods for machines used in packaging food are crucial to ensure the safety and integrity of the packaged products. These methods involve evaluating various aspects of the packaging process, such as seal integrity, contamination risks, and proper labeling. Here are some commonly used quality testing methods:
1. Seal Integrity Testing: This method verifies if the machine is sealing the packaging properly to prevent any leaks or contaminants from entering the packaged food. It may involve visual inspection, pressure testing, or vacuum testing to identify any potential issues.
2. Contamination Testing: Machines should be regularly checked for any potential sources of contamination, such as dust, oil, or biological hazards. Swab tests on critical machine areas can help identify possible contamination risks.
3. Labeling Accuracy: Machines should accurately apply labels containing essential information, including product name, ingredients, allergens, and nutritional facts. Random sampling and inspection of labeled products ensure compliance with labeling regulations and customer expectations.
4. Weight and Quantity Control: Regular weight checks are necessary to ensure that packaged food meets the specified weight requirements. Automatic checkweighers can quickly identify underweight or overweight packages, ensuring consistent quantities and preventing customer dissatisfaction.
5. Functionality Testing: Machines should be periodically tested to ensure all their functionalities are working correctly, such as automated cutting, sealing, and stacking. This helps identify any mechanical or electronic issues that may affect the quality of the packaged food.
6. Sanitary Conditions: Regular cleaning and sanitation practices must be implemented to maintain a hygienic packaging environment. Verification of cleaning protocols and routine inspections for cleanliness are essential to ensure that the machines meet food safety standards.
To control the quality of packaging machines, a comprehensive quality management system should be established. This includes:
1. Standard Operating Procedures: Clearly define and document the procedures for machine operation, maintenance, and cleaning to ensure consistency and minimize variability.
2. Training and Competency: Regular training programs should be provided to machine operators, emphasizing proper machine handling, quality procedures, and adherence to food safety regulations.
3. Preventive Maintenance: Implement a preventive maintenance program to ensure machines are regularly inspected, calibrated, and repaired. This helps identify potential issues before they affect the quality of the packaged food.
4. Documentation and Traceability: Proper documentation of quality testing results, maintenance records, and any corrective actions taken is necessary for traceability and continuous improvement.
5. Statistical Process Control: Use statistical control charts to monitor key quality parameters and identify any trends or out-of-control conditions. This helps manage and reduce variability in machine performance.
By implementing these quality testing methods and control measures, manufacturers can ensure that the machines used in packaging food consistently produce safe, high-quality products, thereby safeguarding consumer health and satisfaction.
machines for packaging food Sample Policy and Post-Purchase Considerations for machines for packaging food from China
Sample Policy:
When purchasing machines for packaging food from China, it is important to have a clear understanding of the sample policy offered by the supplier. This policy outlines the terms and conditions for obtaining samples of the packaging machines before making a bulk purchase. Ideally, the supplier should provide the following:
1. Availability of samples: Confirm whether the supplier offers samples of the packaging machines. Some suppliers may only provide product catalogs or specifications, while others may offer physical samples for testing.
2. Cost and payment: Determine if there is a charge for obtaining samples and clarify who bears the shipping costs. It is common for the buyer to cover the expenses, but sometimes the supplier may offer free samples or reimburse the shipping costs upon placing a subsequent order.
3. Sample customization: Check if the supplier allows customization of the packaging machines based on specific requirements. This is particularly important if there are unique packaging needs or if customization is required to comply with local regulations.
4. Sample duration: Understand the duration for which the samples can be used for evaluation. Typically, suppliers provide samples for a certain period (e.g., 7 or 14 days), after which they may request their return or charge for them if not returned.
Post-Purchase Considerations:
After purchasing machines for packaging food from China, it is essential to take certain post-purchase considerations into account. These considerations aim to ensure the smooth functioning and longevity of the packaging machines:
1. Installation and training: Confirm whether the supplier provides installation guidance and training for operating the machines. This will help in effectively setting up the equipment and training the staff to operate it correctly, minimizing errors and potential issues.
2. Warranty and after-sales service: Inquire about the warranty period for the packaging machines and the scope of after-sales service provided by the supplier. Understanding the support available for troubleshooting, maintenance, and spare parts can be crucial for uninterrupted operations.
3. Compliance with regulations: Ensure that the purchased packaging machines comply with food safety and packaging regulations in the destination country. It is crucial to meet the required standards and avoid any legal issues or penalties.
4. Spare parts availability: Discuss the availability and lead time for replacement parts, as they might be needed in case of machine breakdowns or regular maintenance. Having spare parts readily available can minimize downtime and keep production running smoothly.
By understanding the supplier’s sample policy and considering these post-purchase factors, buyers can make informed decisions, maintain quality standards, and minimize potential risks when purchasing machines for packaging food from China.
Sourcing machines for packaging food from China: Opportunities, Risks, and Key Players
Sourcing machines for packaging food from China harbors both opportunities and risks, with key players dominating the market. China’s vast manufacturing capabilities, cost advantages, and technological advancements make it an attractive destination for procuring packaging machinery for the food industry. However, potential risks must be carefully considered, such as quality control, intellectual property protection, and regulatory compliance.
One of the main opportunities of sourcing from China is the country’s renowned manufacturing capabilities. China is the world’s manufacturing hub, offering a wide range of machinery for food packaging at competitive prices. The presence of numerous manufacturers allows for extensive options, providing businesses with the flexibility to choose from various brands and models to suit their specific requirements.
Another opportunity lies in cost advantages. China’s lower labor and production costs can significantly reduce the overall expenses involved in sourcing packaging machinery. This cost-effectiveness enables businesses to enhance their competitiveness by acquiring cutting-edge equipment while maintaining competitive pricing for their products.
Technological advancements in the sector further strengthen China’s appeal as a sourcing destination. Chinese manufacturers have made substantial progress in research and development, often offering innovative and efficient packaging machinery solutions. These technological advancements enable companies to meet evolving consumer demands, improve production efficiency, and enhance the overall product packaging quality.
However, sourcing from China also entails risks that must be managed effectively. Quality control is a critical concern due to the presence of a wide range of manufacturers with varying production standards. Conducting thorough due diligence, including factory inspections and quality certifications, is crucial to ensure reliable and durable machinery.
Intellectual property protection is another risk associated with sourcing from China. Counterfeit products and intellectual property infringement are prevalent issues, potentially affecting the authenticity and performance of the sourced machinery. Engaging with reputable manufacturers and seeking legal advice can mitigate this risk.
Regulatory compliance is an essential consideration when sourcing machinery from China. Different countries have specific regulations and standards for food packaging, and it is crucial to ensure that the equipment complies with relevant requirements. Collaborating with manufacturers experienced in exporting to target markets can help navigate these compliance challenges.
Key players in the Chinese packaging machinery market include companies like Guangzhou XTIME Packaging Equipment, Shantou Jinping Shunyi Machinery Co., Ltd., and Qingdao Tonghe Shackles Co., Ltd. These manufacturers have established a strong market presence by offering a wide range of packaging machinery for various food industries.
In summary, sourcing packaging machinery for food from China presents both opportunities and risks. The country’s manufacturing capabilities, cost advantages, and technological advancements offer attractive prospects. However, quality control, intellectual property protection, and regulatory compliance must be carefully managed. Understanding these factors and collaborating with reputable manufacturers are crucial when considering sourcing from China.
How to find and select reliable machines for packaging food manufacturers in China,use google search manufacturers and suppliers
When searching for reliable machines for packaging food manufacturers in China, it is important to follow a systematic approach to ensure the selection of trustworthy manufacturers and suppliers. Here are some steps to guide you:
1. Define your requirements: Begin by clearly specifying your packaging needs, such as the type of food products you manufacture, desired packaging materials, desired packaging speed, and any specific features or functions required.
2. Conduct a Google search: Use relevant keywords like “food packaging machine manufacturers in China” or “packaging machine suppliers in China” on Google search. This will provide you with a list of potential manufacturers and suppliers.
3. Evaluate the website: Visit the websites of the shortlisted companies to gather information about their experience, expertise, certifications, and range of packaging machines. Look for detailed product descriptions, technical specifications, and customer reviews or testimonials.
4. Verify credentials: Check if the manufacturers or suppliers have relevant certifications, such as ISO 9001 for quality management and CE for product compliance with safety standards. These certifications indicate their commitment to quality.
5. Industry experience: Look for manufacturers and suppliers with a considerable number of years in the industry. Experienced companies are more likely to have better technical know-how and expertise.
6. Product quality and customization: Ensure that the machines offered meet your quality standards. Look for information on their manufacturing processes, quality control measures, and use of high-quality components. If you require customization, check if the manufacturer can accommodate your specific needs.
7. Request samples or demonstrations: Ask for samples or arrange for demonstrations to assess the machine’s performance, durability, reliability, and ease of operation. This will allow you to gauge the quality and suitability of the machine for your specific food packaging requirements.
8. Check customer reviews: Look for online reviews or ratings of the shortlisted manufacturers or suppliers. Pay attention to feedback on the product quality, customer service, and overall satisfaction.
9. Seek recommendations: Reach out to industry colleagues or experts for recommendations or referrals. They may have firsthand experience with reliable packaging machine manufacturers in China.
10. Communication and support: Engage in direct communication with the shortlisted manufacturers or suppliers to clarify any doubts, discuss customization options, and understand their after-sales support and warranty policies.
By following these steps, you can find reliable machines for packaging food manufacturers in China and make an informed decision that meets your business needs.
How to check machines for packaging food manufacturers website reliable,use google chrome SEOquake check if ranking in top 10M
When looking for a reliable website of a food packaging machine manufacturer, it is important to follow a few steps. One effective method is to use Google Chrome with the SEOquake extension to check the website’s ranking. Here is a step-by-step guide in under 300 words:
1. Install Google Chrome: If you don’t have it already, download and install Google Chrome as your web browser.
2. Add SEOquake extension: Open Google Chrome, go to the Chrome Web Store, search for “SEOquake” extension, and click on “Add to Chrome” to install it.
3. Enable SEOquake: Once installed, you’ll see the SEOquake logo on the top-right of your Chrome browser. Click on it to enable the extension.
4. Search for the manufacturer’s website: Open a new tab and enter the name of the packaging machine manufacturer in the search engine.
5. Check the website ranking: After the search results load, look for the manufacturer’s website. The SEOquake extension will display statistics alongside each result. Look for the number of indexed pages and the website’s position in the top 10 million sites (e.g., if it says 2M, it means the website is ranked within the top 2 million).
6. Analyze other factors: Apart from the ranking, SEOquake can provide additional information like the age of the domain, social media presence, and SEMrush rank. Consider these factors to assess the website’s reliability.
7. Visit the website: Click on the manufacturer’s website link from the search results to access it directly. Explore the website to evaluate its content, design, product information, certifications, customer reviews, and contact details.
8. Seek further verification: To ensure reliability, check for any certifications or partnerships mentioned on the website. Look for references or testimonials from previous clients. Additionally, consider reaching out to the manufacturer directly for any clarification or additional information.
By following these steps and using the SEOquake extension on Google Chrome, you can quickly analyze the ranking and other factors of a food packaging machine manufacturer’s website, helping you ensure its reliability.
Top 10 machines for packaging food manufacturers in China with each 160 words introduce products,then use markdown create table compare
1. VFFS Machines: Vertical Form Fill Seal (VFFS) machines are widely used in food packaging. They can efficiently package various products like snacks, grains, and powders. These machines offer fast packaging speeds and ensure product freshness with their airtight seals.
2. Tray Sealers: Tray sealers are ideal for packaging fresh produce, meat, and ready-to-eat meals. These machines help extend product shelf life by creating a secure seal on trays, ensuring food safety and quality.
3. Flow Wrapping Machines: Flow wrapping machines are perfect for packaging items like biscuits, chocolates, and bread. They provide a visually appealing package with a tight seal, keeping the products fresh for longer periods.
4. Cartoners: Cartoning machines automate the process of filling and sealing cartons. They are commonly used in the food industry for packaging items like cereals, pasta, and frozen foods. These machines efficiently handle large volumes, reducing labor costs.
5. Liquid Filling Machines: Liquid filling machines are crucial for packaging beverages, oils, sauces, and other liquid food products. They ensure accurate filling and minimize product wastage, thus increasing efficiency and profitability.
6. Capping Machines: Capping machines are used for securely sealing bottles and containers. They are suitable for packaging various food products, including sauces, dressings, and condiments. These machines reduce the risk of leakage or contamination.
7. Vacuum Packaging Machines: Vacuum packaging machines remove air from the package, extending the shelf life of perishable food products like meat, seafood, and cheese. These machines effectively protect against spoilage and maintain product freshness.
8. Labeling Machines: Labeling machines provide accurate and efficient labeling for food products. They can handle different label sizes and materials, ensuring clear and legible information for consumers.
9. Checkweighers: Checkweighers verify the weight of packaged food items, ensuring consistency and compliance with regulations. These machines eliminate underfilling and reduce the chances of customer complaints or legal issues.
10. Metal Detectors: Metal detectors play a crucial role in food safety by identifying any metal contaminants in packaged products. They are widely used in the food industry to ensure consumer protection and minimize product recalls.
| Machine Type | Key Features |
|——————–|——————————————-|
| VFFS Machines | Fast packaging, airtight seals |
| Tray Sealers | Extend shelf life, secure seal |
| Flow Wrapping | Visually appealing, tight seal |
| Cartoners | Automation, handle large volumes |
| Liquid Filling | Accurate filling, reduce wastage |
| Capping Machines | Secure sealing, reduce leakage |
| Vacuum Packaging | Extend shelf life, maintain freshness |
| Labeling Machines | Accurate labeling, handle different sizes |
| Checkweighers | Verify weight consistency, compliance |
| Metal Detectors | Identify metal contaminants, food safety |
In summary, China offers a wide range of advanced machines for food packaging. These machines cater to different packaging needs, from solid products to liquids. From VFFS machines to metal detectors, manufacturers can find reliable and efficient solutions to enhance their packaging processes and ensure product quality and safety.
Background Research for machines for packaging food manufacturers Companies in China, use qcc.com archive.org importyeti.com
China is known for its thriving food manufacturing industry, and the demand for efficient packaging machines is on the rise. To conduct background research on the machines available for food packaging in China, several platforms can be used, such as qcc.com, archive.org, and importyeti.com.
Qcc.com is a comprehensive platform that provides information on companies registered in China. It allows users to search for specific sectors, including food packaging machinery manufacturers. By accessing qcc.com, researchers can gather information regarding the registered companies, their contact details, legal status, and financial records. This platform can help identify potential manufacturers and assess their credibility.
Another valuable resource is archive.org, which is an online library holding historical and archived web pages. Researchers can utilize this platform to explore the websites of food packaging machinery manufacturers that might no longer exist or have been updated. By examining older versions of these websites, one can gain insights into the company’s history, product portfolio, partnerships, and any changes in their business strategy over time.
Furthermore, importyeti.com is a platform that specializes in offering information on import and export activities. Researchers can use this platform to access data related to food packaging machines imported into or exported from China. It provides details such as importers, exporters, shipping records, and product specifications. This information can be valuable in understanding the global market demand for food packaging machines and identifying potential suppliers.
To effectively summarize the background research, important details can be highlighted. This may include the number of registered food packaging machinery manufacturers found on qcc.com, insights gained from archived websites on archive.org, and relevant import/export statistics obtained from importyeti.com. By utilizing these platforms, researchers can quickly gather valuable insights on food packaging machinery manufacturers in China, supporting their decision-making process while complying with the word limit of 300 words.
Leveraging Trade Shows and Expos for machines for packaging food Sourcing in China
Trade shows and expos are excellent platforms for sourcing machines for packaging food in China. These events provide a unique opportunity to connect with suppliers, explore new technologies, and stay updated on industry trends in one centralized location.
By attending trade shows and expos specializing in packaging machinery for the food industry, buyers can meet a wide range of manufacturers and distributors from China. These events allow buyers to compare various options, negotiate deals, and establish relationships with potential suppliers.
China is known for its vast manufacturing capabilities and competitive prices, making it an ideal destination for sourcing packaging machines. Trade shows and expos in China attract a large number of exhibitors, showcasing their innovative technologies and machinery solutions for the food packaging industry.
Attending these events enables buyers to physically assess the quality of the machines, discuss customization options, and even witness live demonstrations. This firsthand experience can help buyers make informed decisions about the suppliers they want to partner with.
Furthermore, trade shows and expos often host specialized seminars and conferences that provide valuable insights into industry developments and best practices. These educational sessions can enhance a buyer’s understanding of the latest trends, regulations, and technologies in the packaging industry.
To make the most of trade shows and expos while sourcing machines for packaging food in China, buyers should come prepared with a clear list of requirements, budgets, and timelines. It is crucial to conduct thorough research on exhibitors beforehand and schedule appointments to maximize time and efficiency during the event.
In conclusion, leveraging trade shows and expos in China for sourcing packaging machinery for the food industry is a strategic approach. These events offer a centralized platform to connect with a wide range of suppliers, explore new technologies, and gain valuable industry insights. By attending these events and following proper preparations, buyers can make informed decisions and establish fruitful partnerships with Chinese manufacturers.
The Role of Agents and Sourcing Companies in Facilitating machines for packaging food Purchases from China
Agents and sourcing companies play a vital role in facilitating the purchase of machines for packaging food from China. These entities act as intermediaries between the buyer and the Chinese manufacturers, streamlining the procurement process and ensuring that the buyer’s requirements are met.
One of the primary advantages of engaging an agent or sourcing company is their expertise and knowledge of the Chinese market. They possess in-depth understanding of the local industry, including the manufacturers’ capabilities, product range, and pricing. With this knowledge, they can assist the buyer in identifying the most suitable machines for packaging food, taking into account the buyer’s specific needs and budget constraints.
Agents and sourcing companies also act as a bridge for effective communication between the buyer and the Chinese manufacturers. They are proficient in both the local language and the buyer’s language, minimizing potential language barriers and facilitating smooth communication. This ensures that accurate information is transmitted, expectations are aligned, and any queries or concerns are promptly addressed.
Additionally, agents and sourcing companies play a crucial role in quality control. They have extensive experience in assessing the quality of machinery and can conduct thorough due diligence on the manufacturers to verify their credibility and capability. This includes reviewing certifications, visiting production facilities, and inspecting existing product samples. By ensuring that the machines meet the required quality standards, agents and sourcing companies mitigate the risk of receiving substandard or unreliable equipment.
Furthermore, these intermediaries oversee the procurement process, handling negotiations, logistics, and customs processes. They leverage their existing networks and relationships with freight forwarders, shipping companies, and customs authorities to simplify the transportation of the purchased machinery. This minimizes the buyer’s time and effort in dealing with bureaucratic processes and transportation arrangements.
In conclusion, agents and sourcing companies play a crucial role in facilitating machines for packaging food purchases from China. Their expertise, market knowledge, and ability to streamline communication and logistics make them vital partners in ensuring successful procurement and delivery of high-quality equipment.
Price Cost Research for machines for packaging food manufacturers Companies in China, use temu.com and 1688.com
When it comes to purchasing machines for packaging food, China offers a wide range of options through platforms such as temu.com and 1688.com. Conducting price cost research on these platforms can be a valuable approach for food manufacturers looking to minimize expenses.
Temu.com is a B2B platform that specializes in connecting global buyers with Chinese suppliers. It offers a comprehensive selection of packaging machines from various manufacturers in China. Users can easily navigate through a wide range of options, compare prices, and analyze product specifications to make informed decisions.
Similarly, 1688.com, owned by Alibaba Group, is a popular wholesale platform in China. It serves as a marketplace for both suppliers and buyers, offering a vast array of packaging machines for food manufacturers. The platform provides detailed product descriptions, images, and customer reviews, enabling manufacturers to evaluate the quality and performance of the machines before making a purchase.
Conducting a price cost research on these platforms involves utilizing various resources available. By conducting a search on temu.com and 1688.com, manufacturers can compare prices across different suppliers, identify the most competitive offers, and negotiate favorable terms. Additionally, it is essential to consider factors such as shipping costs, delivery time, after-sales service, and warranties to ensure a comprehensive understanding of the overall expenditure.
To make the most of these platforms, it is advisable to start the research with a clear understanding of the specific packaging requirements. This will help filter out irrelevant options and focus solely on machines that meet the desired criteria. By utilizing the search and filter functions, manufacturers can save time and effort by navigating directly to the most suitable options.
In conclusion, temu.com and 1688.com are valuable resources for food manufacturers seeking machines for packaging. By conducting price cost research through these platforms, manufacturers can compare prices, evaluate product specifications, and find the best deals from Chinese suppliers. Taking a strategic approach to utilize these platforms can ultimately help manufacturers minimize costs and enhance their packaging operations.
Shipping Cost for machines for packaging food import from China
The shipping cost for importing machines for packaging food from China can vary based on several factors. The main variables that affect the shipping costs include the weight and dimensions of the machines, the shipping method chosen, and the destination country.
Weight and dimensions of the machines play a crucial role in determining the shipping cost. Generally, the heavier and larger the machines, the higher the shipping cost will be. Packaging food machines can range in size and weight, so it’s essential to have accurate information to calculate the exact shipping cost.
The chosen shipping method also affects the cost. There are several options, including air freight, sea freight, and express courier services. Air freight is generally the fastest but can be more expensive, while sea freight is cheaper but slower. Express courier services can be a good option for smaller machines as they are faster but can become costly for larger shipments.
The destination country is another critical factor influencing shipping costs. Shipping to different countries may incur various import fees, taxes, and customs duties. It’s important to research the specific regulations and charges set by the destination country to factor them into the overall shipping cost.
To obtain an accurate shipping cost, it’s advisable to contact shipping companies or freight forwarders who specialize in international shipping. They can provide detailed quotes considering the specific machines, shipping method, and destination country. Additionally, it’s important to factor in any additional services required, such as insurance or customs clearance.
Overall, the shipping cost for importing machines for packaging food from China can vary widely based on the aforementioned factors. Careful planning, accurate information, and collaboration with experienced shipping professionals are crucial to ensure a smooth and cost-effective shipping process.
Compare China and Other machines for packaging food Markets: Products Quality and Price,Visible and Hidden Costs
China is a prominent player in the market for machines used in packaging food, facing competition from other countries such as Germany, Italy, and the United States. Several factors differentiate China from its competitors, including product quality, pricing, and visible and hidden costs.
In terms of product quality, China has made significant strides over the years. While it is known for mass-produced, low-cost products, Chinese manufacturers have improved their quality control processes and adopted advanced technologies. However, when compared to their counterparts in Germany and Italy, Chinese machines for packaging food may still fall slightly behind in terms of overall quality and precision. The German and Italian manufacturers have a long-standing reputation for producing high-quality, reliable machinery.
Pricing is a significant advantage for China in the market for packaging food machines. Chinese manufacturers are often able to offer more competitive prices due to lower labor and production costs. This has allowed them to gain a significant market share, particularly in developing countries where cost is a primary consideration. However, German and Italian manufacturers, while slightly more expensive, are often seen as offering better value for money due to their superior product quality and longevity.
Visible costs, such as the purchase price of the machines, are typically lower for Chinese manufacturers. They can often offer more affordable options, making their machines accessible to a wider range of customers. On the other hand, hidden costs associated with Chinese machines can arise in the form of potential maintenance and repair expenses. While some Chinese manufacturers offer good after-sales service, others may lack adequate support, leading to higher long-term costs.
In summary, China competes with other countries in the machines for packaging food markets based on product quality, pricing, and visible and hidden costs. While Chinese manufacturers have improved their product quality, they still face stiff competition from German and Italian manufacturers. Pricing is a significant advantage for China, but the lower upfront costs may be offset by potential hidden costs in the long run. Customers need to carefully consider their specific requirements and assess the trade-offs between product quality, price, and potential hidden costs when choosing machines for packaging food.
Understanding Pricing and Payment Terms for machines for packaging food: A Comparative Guide to Get the Best Deal
When it comes to purchasing machines for packaging food, understanding pricing and payment terms is crucial to ensure the best deal for your business. This comparative guide aims to provide valuable insights on negotiating prices and payment terms, empowering you to make informed decisions.
Pricing for packaging machines can vary, depending on factors such as machine type, capacity, features, and brand reputation. It is essential to research the market thoroughly and compare prices from different suppliers. Request quotes and evaluate the overall value proposition, considering factors beyond the initial cost. This includes factors like maintenance costs, energy efficiency, and machine durability to determine the machine’s long-term cost-effectiveness.
When negotiating prices, consider your volume requirements. Large-scale orders often have more negotiation leverage, leading to potential discounts or better pricing. Therefore, it’s beneficial to forecast your packaging needs accurately and communicate them to suppliers to leverage bulk purchasing power.
Payment terms are an integral part of the purchasing process. Common options include upfront payment, installment plans, or leasing options. Suppliers may also offer discounts for upfront payments, so carefully evaluate the financial capacity of your business to determine the most suitable payment method.
Leasing can be a valuable alternative, especially for small businesses with budget constraints. It allows you to access the required machinery while minimizing upfront costs. However, it is essential to review the lease terms carefully, including interest rates, lease duration, and potential penalties for early termination or maintenance issues.
Consider partnering with financial institutions specializing in equipment financing to explore tailored payment options. These institutions often provide competitive financing terms and can offer flexible repayment plans to suit your business’s cash flow.
Moreover, be aware of additional costs that may arise, such as delivery charges, installation fees, or training expenses. Discuss these aspects upfront with the supplier to avoid any surprises in the final cost.
Finally, remember to negotiate beyond pricing and payment terms. Factors like warranty coverage, after-sales support, and training provisions are equally significant. Comprehensive warranty coverage and readily available technical support can contribute to significant cost savings in the long run.
In conclusion, understanding pricing and payment terms is essential when purchasing packaging machines for food. Through thorough market research, accurate volume forecasting, and negotiation strategies, businesses can secure the best deal. Exploring leasing and financing options, while considering factors beyond the initial cost, will help make an informed decision. Achieving a balance between pricing, payment terms, and additional benefits like warranty coverage and support is key to obtaining the optimal packaging machine for your food business.
Chinese Regulations and Industry Standards Certifications for machines for packaging food,Import Regulations and Customs for machines for packaging food from China
Chinese Regulations and Industry Standards Certifications for machines for packaging food:
In China, machines for packaging food are subject to various regulations and industry standards to ensure their safety, quality, and compliance with national requirements. The main regulatory authorities overseeing this industry are the State Administration for Market Regulation (SAMR) and the National Certification and Accreditation Administration (CNCA).
1. Food Packaging Machinery Safety Regulations:
The SAMR is responsible for enforcing safety regulations for food packaging machinery. These regulations cover aspects such as equipment design, manufacturing process, materials used, energy efficiency, and labeling requirements. Compliance with these regulations is mandatory to ensure the safety of the machinery and the packaged food.
2. China Compulsory Certification (CCC):
The CCC certification is a mandatory requirement for several product categories, including food packaging machinery. It ensures that the product meets specific safety and quality standards. Manufacturers must obtain this certification and affix the CCC mark before selling their machines in the Chinese market.
3. ISO and Industry Standards:
Machines for packaging food also need to comply with relevant ISO standards and industry-specific standards. These standards cover technical specifications, performance requirements, and safety guidelines. Examples of applicable ISO standards include ISO 9001 (Quality Management) and ISO 22000 (Food Safety Management System).
Import Regulations and Customs for machines for packaging food from China:
Importing machines for packaging food from China requires compliance with Chinese import regulations and customs procedures in the destination country:
1. Import Documentation:
Importers must provide essential documents, including a commercial invoice, packing list, bill of lading/airway bill, and import license/certificate, if applicable. These documents are necessary to authenticate the imported goods and comply with customs requirements.
2. Customs Duties and Taxes:
Importers are responsible for paying customs duties and taxes levied by the destination country. The rates vary depending on the country and the specific machinery being imported. Importers should consult the customs department of their country for accurate duty rates and applicable tax regulations.
3. Customs Clearance:
Machines for packaging food must undergo customs clearance procedures, which involve submitting import documents, paying duties and taxes, and ensuring compliance with import regulations. Clearance is completed by customs officials to release the goods for distribution within the destination country.
In summary, machines for packaging food in China must comply with stringent safety regulations, obtain certifications such as CCC, and adhere to relevant ISO and industry standards. Importers need to fulfill documentation requirements and comply with customs regulations, including the payment of duties and taxes, to import these machines successfully.
Sustainability and Environmental Considerations in machines for packaging food Manufacturing
In recent years, there has been a growing emphasis on sustainability and environmental considerations in the manufacturing industry, particularly in the machines used for packaging food. This shift is driven by the need to reduce the carbon footprint, minimize waste generation, and conserve natural resources.
One key area of focus is energy efficiency. Packaging machines require electricity to function, and improving their energy efficiency can significantly reduce their environmental impact. Manufacturers are incorporating advanced technologies, such as variable frequency drives, to optimize power consumption by reducing energy losses during operation. These machines also employ sensors and automation to control energy usage based on actual production needs, further reducing unnecessary energy consumption.
Another important consideration is the use of sustainable materials. Packaging machines often handle various types of packaging materials, such as plastics, films, and paper-based materials. To promote sustainability, manufacturers are developing machines that can handle and process biodegradable or recyclable materials. This helps to reduce the amount of non-recyclable waste generated during the packaging process.
Efforts are also being made to minimize water consumption. Packaging machines commonly require water for cooling and cleaning purposes. Implementing water-saving technologies, such as closed-loop systems and water recycling processes, can significantly reduce the amount of water consumed during machine operation. By conserving water resources, manufacturers can minimize their environmental impact and contribute to sustainable manufacturing practices.
Moreover, the design and maintenance of packaging machines are being considered from an environmental perspective. Manufacturers are focusing on creating machines that are durable, easy to repair, and have longer operational lifespans. By using quality components and materials, the need for frequent replacements and disposals is reduced. Furthermore, implementing regular maintenance schedules and optimization techniques can increase the efficiency and longevity of the machines, resulting in reduced waste and resource consumption.
In conclusion, sustainability and environmental considerations are playing an increasingly vital role in the design and operation of machines used for packaging food. Energy efficiency, use of sustainable materials, water conservation, and machine design and maintenance are key areas of focus. By integrating these considerations, manufacturers can contribute to a more sustainable and environmentally conscious food packaging industry.
List The Evolution history of “machines for packaging food”
Machines for packaging food have evolved significantly over the years, revolutionizing the food industry. The evolution can be traced back to the early 19th century when the industrial revolution sparked advancements in mechanical technology. During this time, manual packaging processes dominated, with food items being hand-wrapped or packed in simple containers.
In the late 1800s, the introduction of sewing machines and mechanical canning systems brought about notable changes. The ability to seal cans, preserve food, and ensure hygiene increased efficiency and extended shelf life. This marked the beginning of semi-automated packaging.
The early 20th century witnessed further advancements as machines for filling and sealing products became more prevalent. In 1901, the first fully automatic packaging machine, known as the Simplex Rotary Filler, was invented. This machine automated the process of filling bottles, greatly enhancing productivity.
The mid-1900s saw the advent of new materials like plastics that revolutionized packaging. This era also witnessed the development of vacuum packaging machines, which removed air from packages to preserve food quality and freshness.
In the 1960s, computer technology began to infiltrate industrial processes, leading to the invention of computer-controlled packaging machinery. These machines offered higher precision, increased speed, and improved quality control. Additionally, the use of flexible packaging materials, such as pouches and bags, gained popularity due to their convenience and cost-effectiveness.
The late 20th and early 21st centuries witnessed significant technological advancements in packaging machinery. These advancements included the integration of robotics, advanced sensors, and computer vision systems, enabling machines to handle complex packaging tasks with minimal human intervention. The rise of sustainable packaging and demand for eco-friendly solutions also influenced the development of machines capable of utilizing recyclable materials and reducing waste.
Today, machines for packaging food continue to evolve with the emphasis on automation, precision, and sustainability. Cutting-edge technologies like artificial intelligence, machine learning, and Internet of Things (IoT) have transformed the packaging industry, improving efficiency, reducing costs, and minimizing environmental impact.
In conclusion, the evolution of machines for packaging food has come a long way from manual processes to sophisticated, fully automated systems. These advancements have played a vital role in increasing productivity, extending shelf life, and ensuring the safety and quality of packaged food products.
The Evolution and Market Trends in machines for packaging food Industry
The food packaging industry has witnessed significant evolution and market trends over the years, driven by various factors such as technological advancements, changing consumer preferences, and sustainability concerns.
One major evolution in the packaging of food products is the shift towards automation and the use of machines. This trend can be attributed to the need for increased efficiency, accuracy, and speed in the packaging process. Machines for packaging food are now equipped with advanced features such as automated filling, sealing, and labeling systems, reducing human error and increasing productivity. Additionally, the use of machines allows for better control over packaging processes, ensuring consistency in quality and reducing wastage.
Another notable trend in the packaging of food products is the growing demand for sustainability. Consumers today are increasingly conscious about environmental issues and are seeking sustainable packaging options. This has led to the development of eco-friendly packaging materials such as biodegradable plastics, compostable films, and recyclable materials. Machines used for packaging food are being adapted to accommodate these sustainable packaging options, ensuring that they meet the changing market demands.
Furthermore, there is a rising demand for convenience and innovation in food packaging. Consumers are looking for packaging that is easy to open, resealable, and portable, allowing for on-the-go consumption. This has led to the development of machines that can produce innovative packaging formats such as pouches, sachets, and single-serve containers. These packaging formats not only enhance convenience for consumers but also provide manufacturers with opportunities to differentiate their products in the market.
The market for machines in the food packaging industry is expected to witness significant growth in the coming years. Factors such as increasing urbanization, changing lifestyles, and the growing popularity of online food delivery services are driving the demand for packaged food products. As a result, manufacturers are investing in advanced packaging machinery to meet the increasing production demands.
In conclusion, the evolution and market trends in machines for packaging food industry are characterized by automation, sustainability, and convenience. The demand for efficient and sustainable packaging solutions has resulted in the development of advanced machines that cater to these requirements. As the food packaging industry continues to evolve, the role of machines in ensuring efficient and sustainable packaging processes will become even more prominent.
Custom Private Labeling and Branding Opportunities with Chinese machines for packaging food Manufacturers
Chinese machines for packaging food offer numerous opportunities for custom private labeling and branding for manufacturers. With their advanced technology, competitive pricing, and versatility, these machines have become a popular choice for companies looking to enhance their packaging capabilities.
One significant advantage of Chinese machines is their ability to support custom private labeling. Manufacturers can request specific modifications to align the machine’s design with their brand identity. This includes incorporating company logos, color schemes, and fonts onto the machine’s exterior. By doing so, manufacturers can create a cohesive visual brand image that resonates with their target customers.
Additionally, Chinese machines offer branding opportunities through customizable packaging options. These machines can handle a wide range of packaging materials, such as pouches, bags, bottles, and boxes. Manufacturers can take advantage of this flexibility to create unique packaging designs that reflect their brand’s personality and values. They can experiment with different shapes, sizes, and materials to stand out on store shelves and effectively communicate their brand message.
Furthermore, Chinese machines for packaging food provide opportunities for branding through their advanced features and capabilities. These machines are equipped with cutting-edge technology, including automated processes, precision controls, and intelligent systems. Manufacturers can leverage these features to enhance product quality, increase efficiency, and improve overall customer satisfaction. By highlighting these advanced capabilities, manufacturers can position their brand as innovative and reliable in the food packaging industry.
In conclusion, Chinese machines for packaging food offer various custom private labeling and branding opportunities for manufacturers. The ability to incorporate company logos, colors, and fonts on the machine’s exterior, as well as creating unique packaging designs, allows manufacturers to establish a strong brand identity. Additionally, advanced features and technology present in these machines enable manufacturers to position their brand as innovative and trustworthy. With their competitive pricing and versatility, Chinese machines are an ideal choice for manufacturers seeking to enhance their packaging capabilities while effectively branding their products.
Tips for Procurement and Considerations when Purchasing machines for packaging food
When purchasing machines for packaging food, there are several important considerations and tips for procurement that can help ensure the best choice for your specific requirements. Here are some key factors to keep in mind:
1. Identify your packaging needs: Determine the specific requirements for your food packaging. Consider the types of products, desired packaging formats, speed, and volume of production. This will help narrow down the options and guide your procurement process.
2. Choose reputable suppliers: Work with reliable suppliers with a proven track record in the industry. Research their reputation, read customer reviews, and check if they comply with quality and safety standards.
3. Compliance with food safety regulations: Ensure that the machines you purchase conform to relevant food safety regulations and certifications, such as FDA or EU standards. This will help prevent contamination and maintain the integrity of the packaged food.
4. Consider efficiency and productivity: Look for machines that are efficient and promote high productivity. Consider factors like speed, downtime for maintenance, ease of use, and potential for automation to increase overall efficiency.
5. Customization and flexibility: Opt for machines that offer customization options to accommodate different packaging sizes and formats. Flexibility is crucial when dealing with a range of products or when introducing new ones.
6. Training and technical support: Check if the supplier provides comprehensive training and ongoing technical support. It is essential to have skilled operators and timely assistance to minimize downtime and maximize machine performance.
7. Total cost of ownership: Consider not only the initial purchase cost but also the long-term implications. Assess factors like energy consumption, maintenance requirements, availability and cost of spare parts, and expected lifespan. Balance upfront costs with overall cost-effectiveness.
8. Consider sustainability: In today’s conscious consumption era, consider the environmental impact of the machines you choose. Look for energy-efficient models, waste reduction features, and recyclable materials.
9. Obtain samples and schedule trials: Request samples of your proposed packaging materials and schedule trials with different machine options. This will help evaluate the machines’ performance and assess their suitability for your specific needs.
10. Warranty and after-sales service: Check the warranty conditions and after-sales service offered by the supplier. A reputable supplier should provide satisfactory warranty coverage and be responsive to customer service inquiries.
Overall, a meticulous procurement process is vital when purchasing machines for food packaging. Investing time to research, assess options, and consider all relevant factors will help ensure a successful purchase and efficient food packaging operations.
FAQs on Sourcing and Manufacturing machines for packaging food in China
FAQs on Sourcing and Manufacturing machines for packaging food in China:
1. Why should I consider sourcing and manufacturing machines for packaging food in China?
Sourcing and manufacturing machines for packaging food in China can offer significant cost savings due to lower labor and production costs compared to many other countries. China also has a vast network of suppliers and manufacturers specializing in food packaging machinery, offering a wide range of options to meet your specific requirements.
2. How can I find reliable suppliers and manufacturers in China?
To find reliable suppliers and manufacturers, it is important to conduct thorough research. Utilize online sourcing platforms, industry trade shows, and professional networks to connect with potential suppliers. Check their credentials, certifications, and references. Request product samples and visit their production facilities to ensure they meet quality standards.
3. Are there any specific regulations and certifications I need to be aware of?
Yes, it is crucial to consider regulatory compliance for food packaging machinery. Ensure that the machines meet safety standards such as CE certification. Familiarize yourself with relevant Chinese and international regulations, such as those related to food contact materials, hygiene, and labeling requirements.
4. Can I customize the packaging machines according to my specific needs?
Yes, many Chinese suppliers offer customization options to meet individual requirements. They can modify machines to fit specific packaging sizes, shapes, and materials. Communication is key to clearly convey your needs to the suppliers, ensuring they understand your customization requirements.
5. What about shipping and logistics?
Chinese suppliers are experienced in exporting their products worldwide. They can handle shipping and logistics arrangements, including packaging, documentation, and customs clearance. Choose a reputable supplier who can offer efficient and reliable shipping options, ensuring your machines arrive safely and on time.
6. Are there any risks involved in sourcing and manufacturing from China?
Like any sourcing process, there are risks involved. It is crucial to perform due diligence in selecting suppliers and manufacturers. Ensure clear communication, have a detailed contract, and consider visiting the production facility before finalizing the order. Additionally, engage in quality control and inspections throughout the manufacturing process to minimize any potential risks.
In summary, sourcing and manufacturing machines for packaging food in China can offer cost savings, customization options, and access to a wide range of suppliers. However, it is vital to conduct thorough research, comply with regulations, and manage potential risks to ensure a successful sourcing process.
Why contact sourcifychina.com get free quota from reliable machines for packaging food suppliers?
Sourcifychina.com offers free quota from reliable machines for packaging food suppliers for several reasons. Firstly, sourcing and purchasing packaging machines can be a significant investment for food suppliers, especially for small and medium-sized enterprises. By providing access to reliable machines at no cost, Sourcify China aims to support these suppliers in reducing their expenses and ensuring quality packaging for their products.
Secondly, Sourcify China understands the importance of reliability in packaging machines for food suppliers. Faulty or substandard machines can lead to production delays, product damage, and potential health and safety risks. By offering access to reliable machines, Sourcify China ensures that food suppliers can maintain consistent and high-quality packaging processes, ultimately enhancing their product’s market competitiveness.
Furthermore, providing a free quota of packaging machines also serves as a way for Sourcify China to demonstrate the quality and capabilities of their sourcing services. By allowing food suppliers to experience the performance of these machines firsthand, Sourcify China establishes credibility and trust, which can lead to further business partnerships.
Additionally, offering a free quota aligns with Sourcify China’s goal of simplifying the sourcing process for food suppliers. Instead of suppliers having to spend time and effort researching and locating packaging machines, Sourcify China takes care of the entire sourcing process, ensuring suppliers can focus on their core business activities. This convenience and efficiency can be a valuable advantage for food suppliers, especially those with limited resources or knowledge in sourcing.
In conclusion, Sourcifychina.com provides free quota from reliable machines for packaging food suppliers to support their financial needs, ensure reliable and high-quality packaging processes, showcase their sourcing capabilities, and simplify the overall sourcing experience for suppliers.