Introduce about machining of plastics guide,Qulity,Cost,Supplier,Certification,Market,Tips,FAQ
Machining of plastics involves the process of shaping, cutting, drilling, and finishing plastic materials to create various components and products. It is essential to understand the key aspects of this process, including quality, cost, suppliers, certifications, market trends, tips, and frequently asked questions (FAQs). Here is a concise introduction to these topics, using no more than 300 words.
Quality plays a vital role in plastic machining, as precision and accuracy are crucial for achieving the desired specifications. Manufacturers must ensure dimensional accuracy, surface finish, and tight tolerances to meet specific requirements. Quality control measures such as inspections, testing, and continuous improvement should be in place to guarantee high-quality machined plastic parts.
Cost is another significant consideration in plastic machining. Factors affecting cost include material selection, complexity of design, quantity, lead time, and finishing requirements. Seeking competitive quotes from multiple suppliers and optimizing the manufacturing process can help reduce costs while maintaining quality standards.
Finding a reliable plastic machining supplier is essential to ensure timely delivery and consistency in product quality. Suppliers should have expertise in machining plastics, offer a wide range of materials, provide excellent customer support, and have a track record of delivering on time.
Certification is an essential aspect when choosing a plastic machining supplier. Certification such as ISO 9001 ensures that the supplier follows strict quality management practices, while certifications like ISO 13485 indicate adherence to medical device manufacturing standards. These certifications are indicative of the supplier’s commitment to quality and continuous improvement.
The market for plastic machining is dynamic and evolving, driven by industries such as automotive, aerospace, electronics, healthcare, and consumer goods. Keeping abreast of market trends such as the increasing demand for lightweight and eco-friendly materials can help manufacturers stay competitive and innovative.
Here are a few tips for successful plastic machining: choose the appropriate plastic material for the application, collaborate closely with the machining supplier, optimize designs for efficient machining, and ensure proper cooling and chip management during the process.
FAQs about plastic machining may include queries about material selection, lead times, cost factors, minimum order quantities, surface finish options, and machining capabilities. A comprehensive FAQ section can provide customers with valuable information and address common concerns.
In summary, machining of plastics requires a focus on quality, careful cost management, selecting reliable suppliers, understanding industry certifications, staying updated on market trends, following machining tips for success, and addressing customer FAQs. By considering these aspects, manufacturers can optimize their plastic machining processes and deliver high-quality products to various industries.
Types of machining of plastics
Machining of plastics refers to the process of shaping or altering plastic materials by removing excess material through various cutting tools. There are several types of machining techniques used for plastics, each with its own advantages and suitable applications.
1. CNC Milling: Computer Numerical Control (CNC) milling is a commonly used machining technique for plastics. It involves using precision milling machines to remove material by rotating cutting tools. CNC milling is highly accurate and can produce intricate shapes with excellent surface finishes. It is suitable for prototypes, small batches, and complex geometries.
2. Turning: Turning is a machining process that utilizes a lathe or turning machine to shape plastic material. The plastic workpiece is rotated against a cutting tool that removes material to create cylindrical shapes, such as shafts or tubes. Turning provides high precision and is suitable for mass production or large-scale components.
3. Drilling: Drilling is the process of creating holes in plastic materials. It can be done using drilling machines or drill presses, which rotate a cutting tool to remove material. Drilling is a versatile machining method and can be used to create holes of various sizes and depths in plastics.
4. Routing: Routing involves using a rotating cutting tool to remove excess material from plastic sheets or blocks. It is commonly used to create complex shapes, profiles, or contours in plastics. Routing can be performed manually or using CNC routers, depending on the desired precision and complexity.
5. Laser Cutting: Laser cutting is a non-contact machining technique that uses a high-powered laser beam to vaporize or melt plastic material, creating clean and precise cuts. It is suitable for cutting intricate shapes, engraving, or creating precise edges in plastics. Laser cutting is often used for prototyping, signage, and small-scale production.
6. Waterjet Cutting: Waterjet cutting utilizes a high-pressure jet of water mixed with abrasive particles to cut through plastic materials. This technique is ideal for cutting thick plastics, as it does not generate heat that could damage the material. Waterjet cutting provides high precision and can cut complex shapes accurately.
In conclusion, machining of plastics encompasses various techniques such as CNC milling, turning, drilling, routing, laser cutting, and waterjet cutting. Each method offers unique advantages and is suitable for different applications based on factors like accuracy, scalability, complexity, and material thickness.
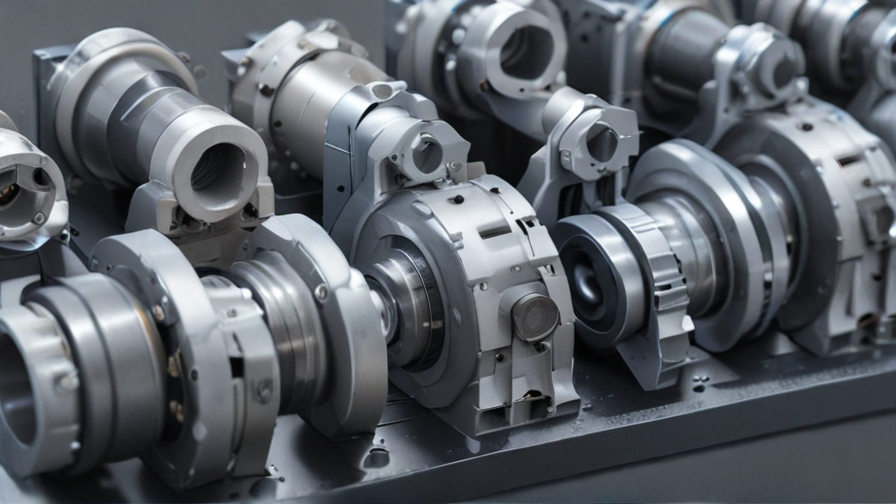
Pros and Cons of Using machining of plastics
Using machining techniques for plastics offers several advantages and disadvantages that need to be considered. Here are the main pros and cons:
Pros:
1. Precision: Machining allows for high precision and tight tolerances, ensuring accurate and consistent results. This is especially advantageous for applications that require intricate designs or complex geometries.
2. Versatility: Machining can be used on a wide range of plastic materials, including both thermoplastics and thermosets. This versatility allows for customization and flexibility in designing various components.
3. Surface Finish: Machining offers the ability to achieve excellent surface finishes on plastics. This is crucial for applications with cosmetic requirements or where a smooth surface is necessary for proper functioning.
4. Cost-effective for small to medium-sized production runs: Machining is a cost-effective option for small to medium-sized production runs, as the initial setup costs are typically lower than for other manufacturing methods such as injection molding. It is especially useful for prototyping and low-volume production.
Cons:
1. Material Waste: Machining involves removing excess material from a block or sheet, leading to significant material waste. This leads to increased costs and is less sustainable compared to other manufacturing methods like injection molding, which can produce near-net shapes.
2. Slower production rates: Machining can have slower production rates compared to other manufacturing methods, such as injection molding or extrusion. This makes it less suitable for high-volume production requirements.
3. Tooling Costs: The cost of tooling for machining can be relatively high, especially for complex geometries or intricate designs. This can be a significant disadvantage for budget-sensitive projects or applications with low profit margins.
4. Limited size constraints: Machining has size limitations due to the size of the machining equipment and the availability of large enough plastic stock materials. This can restrict the size of components that can be produced through machining.
In conclusion, machining plastics offers precision, versatility, and excellent surface finishes, making it suitable for prototyping and low to medium-volume production runs. However, the material waste, slower production rates, tooling costs, and size limitations should be considered as potential drawbacks.
machining of plastics Reference Specifications (varies for different product)
The machining of plastics involves the process of shaping or cutting plastic materials into desired forms or sizes, typically for the production of various products. There are several reference specifications that may vary depending on the specific type of plastic being used and the intended product.
One important aspect of machining plastics is determining the appropriate cutting speed, feed rate, and depth of cut. These parameters need to be optimized to achieve accurate and efficient machining while avoiding damage to the plastic material. The specific values for these parameters will depend on the type of plastic being machined as well as the machinery and tooling being used.
Another consideration in machining plastics is the selection of cutting tools. The type of tool, its geometry, and the material it is made of can significantly impact the machining process and the final product quality. High-speed steel (HSS) and carbide tools are commonly used for machining plastics due to their resistance to wear and ability to maintain sharp cutting edges.
Cooling and lubrication are also important in plastic machining. Although plastics generally do not conduct heat as well as metals, the heat generated during machining can still affect the material and the cutting tool. Therefore, coolants or lubricants may be employed during the machining process to dissipate the heat and prevent overheating or melting of the plastic.
Surface finish is another crucial aspect when machining plastics. Depending on the application, the desired surface finish may vary. Some applications may require a smooth finish, while others may require a textured or patterned surface. The machining process should be adjusted accordingly to achieve the desired surface finish, whether it be through the selection of cutting tools, altering cutting parameters, or implementing post-machining processes.
It is important to note that the reference specifications for plastic machining can vary depending on the unique properties of each plastic material and the specific requirements of the product being produced. It is essential to consult the manufacturer’s guidelines and recommendations for each plastic material to ensure the best machining practices are implemented. Additionally, testing and experimentation may be necessary to optimize the machining process for a specific plastic material or product.
Applications of machining of plastics
Machining of plastics is a key manufacturing process that involves cutting, shaping, and removing material from plastic components. This process offers several applications across various industries, some of which are as follows:
1. Automotive Industry: Machined plastic parts find significant applications in the automotive industry. Examples include gears, bearings, bushings, and fuel system components. Machining allows for precise fabrication of these parts, enabling proper fit, reduced friction, and improved performance of vehicles.
2. Medical Sector: Plastics are widely utilized in the medical field due to their excellent biocompatibility, sterilizability, and corrosion resistance. Machining of plastics is crucial for producing medical device components such as implants, surgical instruments, and laboratory equipment. These machined plastic parts can be customized to meet specific medical requirements, ensuring optimal functionality and patient safety.
3. Electronics and Electrical Industry: Machined plastic parts are extensively used in electronics and electrical applications due to their insulating properties. Plastic housings, connectors, insulators, and switch components are machined to precise tolerances, providing protection and proper functioning of electronic devices. Additionally, machining allows for the production of complex shapes and intricate designs required for electronic components.
4. Aerospace Sector: Machined plastic components are increasingly used in the aerospace industry due to their lightweight properties and resistance to chemicals, corrosion, and high temperatures. Plastics such as PEEK (Polyether Ether Ketone) and ULTEM (Polyetherimide) are machined to produce aircraft interior components, structural parts, and electrical connectors. Precision machining ensures the high performance and durability required in aerospace applications.
5. Packaging Industry: Plastic packaging plays a vital role in preserving and protecting various consumer goods. Machining enables the production of packaging components such as bottles, caps, containers, and trays. These machined parts can incorporate intricate designs, branding, and labeling requirements while maintaining dimensional stability and durability.
6. Fluid Handling and Pump Systems: Machined plastic parts are commonly used in fluid handling applications. Valves, seals, fittings, and pump components are machined to precise specifications, ensuring leak-proof connections, optimal flow control, and resistance to chemicals and abrasion. Machining also allows for the production of parts with tight tolerances to improve overall system performance.
In conclusion, the machining of plastics offers versatile applications across diverse industries, ranging from automotive and medical sectors to electronics, aerospace, packaging, and fluid handling industries. By leveraging the unique properties of plastics and the precision provided by machining processes, manufacturers can produce high-quality plastic components tailored to specific requirements.
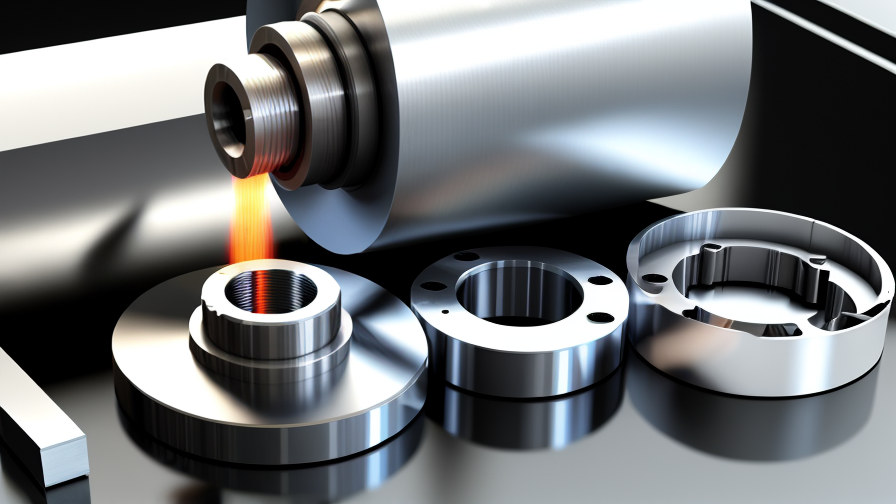
The Work Process and how to use machining of plastics
The work process of machining plastics involves using various techniques to shape and finish plastic materials. It includes cutting, drilling, milling, turning, and other operations to produce the desired shape, dimensions, and surface characteristics. Here is a brief overview of the work process and how to effectively use machining techniques for plastics.
1. Understanding the Plastic Material: Different types of plastics have unique properties, such as hardness, flexibility, and melting point. Before starting the machining process, it is important to know the specific characteristics of the plastic material you are working with. This information will help determine the most suitable machining techniques and tools required.
2. Preparing the Machine: Set up the machining equipment, such as a CNC machine or manual mill, according to the specifications of the plastic material. Ensure the cutting tools are appropriate, such as high-speed steel (HSS) or carbide-based cutters. Adjust the machine parameters, including rotation speed, feed rate, and depth of cut, based on the characteristics of the plastic.
3. Securing the Plastic Workpiece: Use clamps, vises, or other suitable methods to firmly hold the plastic workpiece in place. It is crucial to ensure stability during the machining process, as any movement or vibration may cause inaccuracies or defects.
4. Cutting and Shaping: Start the machining process by removing excess material to achieve the desired shape. Use the appropriate cutting techniques, including milling for flat surfaces, drilling for creating holes, and turning for cylindrical parts. Take small and gradual cuts to prevent excessive heat generation, which can lead to melting, warping, or cracking of the plastic material.
5. Cooling and Chip Control: Plastics tend to generate heat during machining, which can affect the workpiece and cutting tools. Apply an appropriate cooling method, such as using coolants or lubricants, to prevent overheating. Proper chip control is also essential to prevent chip buildup or entanglement with the tool.
6. Finishing and Polishing: Once the rough shape is achieved, use finishing tools, such as sandpaper, polishing compounds, or flame polishing, to smoothen the surface and enhance the aesthetic appeal of the plastic workpiece.
7. Inspection and Quality Control: Thoroughly examine the machined plastic part for dimension accuracy, surface finish, and overall quality. Make necessary adjustments, if required, to meet the desired specifications.
By following these steps, you can effectively utilize machining techniques to shape and finish plastic materials. However, it is crucial to remember that each plastic material may have specific considerations, so it is recommended to consult material datasheets or seek professional advice when machining unfamiliar plastics.
Quality Testing Methods for machining of plastics and how to control the quality
When it comes to machining plastics, there are several quality testing methods that can be employed to ensure the desired outcomes. These methods focus on controlling the quality of the machining processes and the final plastic products. Let’s take a look at some commonly used testing methods and quality control measures within a concise 300-word limit.
1. Measurement and Dimensional Inspection: Accurate measurements are crucial in machining plastics. Various tools like calipers, micrometers, and height gauges are utilized to measure critical dimensions to ensure they meet specifications.
2. Visual Inspection: Visual inspection allows operators to detect surface defects such as scratches, cracks, or irregularities. It is performed throughout the machining process and during the final product inspection.
3. Surface Roughness Analysis: Surface roughness impacts the functionality and aesthetics of plastic components. Techniques like profilometry or laser scanning are used to evaluate the roughness based on specific parameters and ensure it falls within acceptable limits.
4. Mechanical Testing: Mechanical tests, including tensile strength, hardness, and impact resistance tests, are conducted to validate the structural integrity and mechanical properties of machined plastic parts.
5. Chemical Resistance Testing: Plastics must withstand exposure to various chemicals in their applications. Chemical resistance tests assess the response of the plastic material to different chemical substances, ensuring it meets the required standards.
To control the quality of machining processes and plastic products, several key measures can be adopted:
1. Proper Equipment Maintenance: Regular maintenance of machinery and tools helps prevent unexpected issues and ensures accurate and consistent machining performance.
2. Operator Training: Skilled operators who understand the intricacies of plastic machining and quality control methodologies are crucial. Providing adequate training and ongoing education is essential for consistent quality.
3. Standard Operating Procedures (SOPs): Clearly defined SOPs outline best practices to ensure consistent quality output. SOPs should cover all aspects of machining, inspection, and testing processes.
4. Statistical Process Control (SPC): Implementing SPC techniques, such as control charts and quality control checks at regular intervals, allows for real-time monitoring and identification of trends or deviations, enabling timely corrective actions.
5. Documentation and Traceability: Maintaining detailed records of all machining processes, inspections, and test results ensures traceability and facilitates root cause analysis in case of any quality issues.
In summary, achieving and controlling quality in the machining of plastics depends on a combination of various testing methods and quality control measures. By incorporating these methods into the machining processes, manufacturers can ensure the production of high-quality plastic components.
machining of plastics Sample Policy and Post-Purchase Considerations for machining of plastics from China
When considering the machining of plastics from China, it is important to establish a clear sample policy and post-purchase considerations to ensure quality and customer satisfaction. The following guidelines can help streamline the process:
Sample Policy:
1. Request a sample: Before placing a bulk order, ask the supplier to provide a sample of the machined plastic product. This allows you to evaluate the quality, precision, and finishing of their work.
2. Define specifications: Clearly communicate your specifications, such as dimensions, tolerances, surface finish requirements, and any other necessary details, to the supplier. Make sure the sample reflects these specifications accurately.
3. Evaluate compatibility: Assess whether the machined plastic meets the intended application requirements. Consider factors such as chemical resistance, temperature stability, and mechanical durability to ensure the product is suitable for its intended use.
Post-Purchase Considerations:
1. Quality control: Establish quality control measures to assess the produced machined plastics. Conduct inspections and tests to ensure they meet the specified requirements. Define accepted tolerances and reject criteria to maintain consistency and avoid substandard products.
2. Communication: Maintain open lines of communication with the supplier throughout the post-purchase phase. Address any concerns or deviations from the agreed-upon specifications promptly to avoid misunderstandings and ensure timely solutions.
3. Supplier partnership: Develop a relationship with the supplier based on mutual trust and continuous improvement. Provide constructive feedback on the quality of their machined plastics and collaborate to enhance future orders.
4. Cost analysis: Evaluate the overall cost-effectiveness of purchasing machined plastics from China, considering factors such as unit price, shipping costs, and customs regulations. Assess the balance between quality and price to ensure a satisfactory purchase.
In summary, creating a well-defined sample policy and determining post-purchase considerations when sourcing machined plastics from China is crucial. It aids in achieving the desired quality, maintaining effective communication, and forging a successful partnership with the supplier.
Sourcing machining of plastics from China: Opportunities, Risks, and Key Players
Sourcing machining of plastics from China offers several opportunities for businesses looking to optimize cost-efficiency while maintaining product quality. China has a well-developed industrial infrastructure, a large pool of skilled labor, and advanced manufacturing technologies, making it an attractive destination for plastic machining.
One of the major opportunities is cost savings. Labor and manufacturing costs in China are significantly lower compared to many other countries. This allows businesses to save on production expenses, resulting in more competitive pricing for their products. Additionally, China has a wide array of plastic materials available, providing businesses with an extensive range of options to choose from for their specific application requirements.
However, there are also risks associated with sourcing plastic machining from China. Quality control can be a concern, as there is the potential for variations in product standards and inconsistent adherence to specifications. To mitigate this risk, it is important to thoroughly research and select reliable and reputable plastic machining manufacturers, with a proven track record of delivering high-quality products. Communication barriers, cultural differences, and intellectual property protection can also present challenges, so it is crucial to establish effective communication channels and ensure all legal and contractual aspects are well-defined.
Several key players in the plastic machining industry in China include broad-spectrum manufacturers such as XinXin Plastic Mold Co., Ltd., Guangzhou Engineering Plastic Industries Co., Ltd., and Shanghai Dehuan Industry Co., Ltd. These companies have a strong presence in the market and offer a wide range of plastic machining services, including CNC milling, turning, and drilling.
In conclusion, sourcing plastic machining from China provides opportunities for cost savings and access to a wide variety of plastic materials. However, businesses need to carefully consider and manage the associated risks, such as quality control and communication challenges. By selecting reliable manufacturers and establishing effective communication channels, businesses can successfully leverage the benefits of sourcing plastic machining from China.
How to find and select reliable machining of plastics manufacturers in China,use google search manufacturers and suppliers
When searching for reliable machining of plastics manufacturers in China, utilizing Google search can be an effective method. Here are some steps to follow:
1. Begin by entering specific keywords related to your requirements in the search bar. For example, use terms like “machining of plastics manufacturer China” or “CNC plastic machining supplier in China.” This will help narrow down the search results to relevant manufacturers.
2. Browse through the search results and visit the websites of potential manufacturers. Look for information about their expertise, experience, and the range of services they offer. Pay attention to certifications and quality assurance processes mentioned on their websites.
3. Check if they have case studies or testimonials from previous clients, as this can provide insights into their reliability and the quality of their work. Look for companies that have positive feedback and are recognized for their reliable manufacturing services.
4. Evaluate the manufacturers’ capabilities and facilities. Look for advanced equipment and technologies they use in plastic machining processes. It is useful to see if they have invested in modern machinery as it can ensure better precision and efficiency in production.
5. Contact the shortlisted manufacturers directly. Inquire about their expertise, production capabilities, quality control processes, and any certifications they hold. Ask for samples or references of similar projects they have completed in the past.
6. Consider the manufacturer’s response time and attentiveness. Reliable manufacturers should be prompt and professional when answering your queries. Clear communication is essential in establishing a good working relationship.
7. If possible, visit the manufacturer’s facility or arrange a virtual tour to evaluate their production setup, quality control procedures, and overall working environment. This can provide firsthand insights into their operations and reassure you of their reliability.
8. Finally, compare the collected information and select the manufacturer that best meets your requirements in terms of quality, price, lead time, and reliability.
By following these steps and conducting thorough research, it is possible to find and select reliable machining of plastics manufacturers in China.
How to check machining of plastics manufacturers website reliable,use google chrome SEOquake check if ranking in top 10M
To determine the reliability of a machining of plastics manufacturer’s website, you can follow these steps:
1. Use a web browser: Google Chrome is a commonly used web browser, which offers a range of features that can help assess the reliability of a website.
2. Install SEOquake extension: SEOquake is a free browser extension that provides useful insights about websites, including their ranking and other relevant SEO (Search Engine Optimization) data.
3. Verify website ranking: With SEOquake installed, you can check if the manufacturer’s website is ranked within the top 10 million websites globally. A higher ranking indicates better visibility and credibility. For instance, if the website is ranked within the top 1 million, it signifies a relatively popular and reliable website.
4. Consider website design and functionality: Evaluate the website’s design and functionality. A professionally designed, user-friendly website indicates that the manufacturer cares about providing a positive user experience, which can be an indicator of reliability.
5. Check for company information: Look for comprehensive company information, including their contact details, address, and history. Reliable manufacturers usually provide clear and transparent information about their background and operations.
6. Assess customer reviews and testimonials: Seek customer reviews or testimonials on the website or other trusted platforms. Positive reviews and testimonials indicate satisfied customers, which can be a sign of a reliable manufacturer.
7. Check certifications and quality standards: Look for certifications and quality standards prominently displayed on the website. Reliable plastic manufacturers often comply with industry standards, such as ISO certifications, to demonstrate their commitment to quality.
8. Evaluate product information: Assess the provided information about the products they offer. Reliable manufacturers provide detailed technical specifications, materials used, customization options, and any additional services they may offer.
9. Review the FAQ section or customer support: Browse through the Frequently Asked Questions (FAQ) section or contact their customer support if necessary. A responsive and helpful customer support team can indicate a manufacturer’s dedication to customer satisfaction.
By following these steps, using SEOquake to check the website’s ranking, and considering the provided information and user experience, you can make a more reliable assessment of a machining of plastics manufacturer’s website.
Top 10 machining of plastics manufacturers in China with each 160 words introduce products,then use markdown create table compare
1. Dongguan Aomingwei Precision Machinery Co., Ltd. specializes in machining various plastic materials, including ABS, PVC, nylon, and PTFE. Their CNC machining capabilities enable them to produce custom plastic parts with high precision and tight tolerances. The company also offers services such as plastic injection molding and assembly, providing a one-stop solution for customers’ plastic machining needs.
2. Shenzhen Lontek Electronic Technology Co., Ltd. is a leading manufacturer of custom plastic machining products. They have expertise in CNC milling, turning, and drilling of plastics like acrylic, polycarbonate, and POM. Lontek’s state-of-the-art equipment ensures exceptional precision and surface finish. They serve various industries, including electronics, automotive, and consumer goods.
3. Ningbo Special Plastic Manufacturing Co., Ltd. specializes in plastic machining for a wide range of industries. Their capabilities include CNC milling, turning, and routing of plastics such as HDPE, PVC, and PTFE. With advanced machinery and skilled technicians, they produce intricate plastic components with excellent dimensional accuracy and smooth surfaces.
4. Hangzhou Youngpei Precision Machinery Co., Ltd. offers precision plastic machining services using advanced CNC equipment. They can machine various engineering plastics, including PEEK, PA, and PC. The company’s expertise lies in producing complex plastic parts with tight tolerances and high repeatability, catering to industries like aerospace, medical, and automotive.
5. Quanzhou Creator Precision Engineering Co., Ltd. is renowned for its expertise in manufacturing precision plastic components using CNC machining. They specialize in materials like PP, ABS, and PC, delivering top-quality products with exceptional durability and accuracy. Creator Precision Engineering serves industries such as telecommunications, electronics, and industrial equipment.
6. Suzhou Chengli Intelligent Technology Co., Ltd. provides comprehensive plastic machining solutions utilizing advanced CNC equipment and techniques. They excel in machining engineering plastics, including PTFE, POM, and PEI, offering excellent dimensional accuracy and surface finishes for industries like robotics, medical devices, and electronics.
7. Xiamen Mach Cnc Machining Master Co., Ltd. is a trusted manufacturer of plastic machined parts in China. They have expertise in CNC milling, turning, and drilling of plastics such as UHMW-PE, PTFE, and PVC. With a dedicated team and modern equipment, Mach Cnc Machining Master ensures high precision and consistency in their plastic components.
8. Beijing Kingco Technology Development Co., Ltd. specializes in precision plastic machining, including CNC milling and turning. They work with a wide range of plastics, including acrylic, polycarbonate, and nylon, delivering superior quality products with tight tolerances. Kingco Technology Development serves diverse industries, such as optics, electronics, and medical.
9. Shanghai Sourcing International Trade Co., Ltd. offers plastic machining services using state-of-the-art CNC equipment. They have expertise in machining materials like PC, PE, and PET, providing high-precision components for industries such as automotive, electronics, and consumer goods.
10. Guangzhou Dongguang Precision Machinery Co., Ltd. is a leading manufacturer of plastic machined parts in China. They specialize in CNC turning, milling, and drilling of plastics such as ABS, PE, and POM. The company’s commitment to quality ensures precise and durable plastic components for industries like automotive, electronics, and healthcare.
| Manufacturer | Materials Machined | Specializations |
|————————————————|———————-|———————————|
| Dongguan Aomingwei Precision Machinery Co., Ltd.| ABS, PVC, nylon, PTFE| CNC machining, injection molding|
| Shenzhen Lontek Electronic Technology Co., Ltd. | Acrylic, polycarbonate, POM| CNC milling, turning, drilling |
| Ningbo Special Plastic Manufacturing Co., Ltd. | HDPE, PVC, PTFE | CNC milling, turning, routing |
| Hangzhou Youngpei Precision Machinery Co., Ltd. | PEEK, PA, PC | Precision machining, tight tolerances|
| Quanzhou Creator Precision Engineering Co., Ltd.| PP, ABS, PC | Precision machining, durability |
| Suzhou Chengli Intelligent Technology Co., Ltd. | PTFE, POM, PEI | CNC machining, dimensional accuracy|
| Xiamen Mach Cnc Machining Master Co., Ltd. | UHMW-PE, PTFE, PVC | CNC milling, turning, drilling |
| Beijing Kingco Technology Development Co., Ltd. | Acrylic, polycarbonate, nylon | Precision machining, tight tolerances |
| Shanghai Sourcing International Trade Co., Ltd. | PC, PE, PET | CNC machining, high precision |
| Guangzhou Dongguang Precision Machinery Co., Ltd.| ABS, PE, POM | CNC turning, milling, drilling |
(Note: The table above may not be properly displayed in plain text format. Kindly refer to the Markdown conversion to view the table accurately.)
Background Research for machining of plastics manufacturers Companies in China, use qcc.com archive.org importyeti.com
When it comes to machining plastics, China boasts a vast network of manufacturers that specialize in this field. Three websites, namely qcc.com, archive.org, and importyeti.com, provide valuable information about these companies and their background. Here is a concise overview of this industry in China.
QCC.com is a reputable business information platform that offers details about plastic machining manufacturers in China. Users can search for specific companies and access their profiles, which typically include information about their production capabilities, product range, certifications, and contact details. This website serves as a reliable resource for gathering a comprehensive list of manufacturers in the industry.
Archive.org, an online platform that archives website content, can be another useful tool for background research. By accessing archived versions of plastics machining company websites, users can uncover historical information about the development, growth, and changes in these companies over time. This can provide valuable insights into their capabilities, expertise, and experience in the industry.
Importyeti.com is a comprehensive import database that covers various industries and products, including plastic machining. Users can search for specific products or companies and view their import and export activities. This database helps researchers identify manufacturers that have experience in exporting their products, indicating their ability to meet international quality standards and potentially their willingness to engage in international trade.
Overall, these three websites serve as excellent resources for conducting background research on machining of plastics manufacturers in China. QCC.com provides detailed profiles of companies, archive.org offers historical information, and importyeti.com provides insights into their import-export activities. When used collectively, these platforms can help researchers gain a better understanding of the capabilities, expertise, and market presence of plastic machining manufacturers in China.
Leveraging Trade Shows and Expos for machining of plastics Sourcing in China
Trade shows and expos are excellent platforms for sourcing machining services for plastics in China. These events bring together a wide range of industry professionals, including manufacturers, suppliers, and experts, providing an opportunity for effective networking and business collaboration.
Attending trade shows related to plastics machining in China allows companies to explore various suppliers and machinery providers under one roof. With hundreds of exhibitors showcasing their capabilities, attendees can evaluate different options, compare offerings, and make informed decisions. This not only saves time but also provides a comprehensive understanding of the existing market landscape.
Moreover, trade shows provide a unique chance to establish face-to-face connections with potential suppliers. Engaging in direct discussions allows for a clearer understanding of their capabilities, production processes, and quality control measures. Companies can also inquire about the precision and tolerances they can achieve, the types of plastic materials they specialize in, and whether they can handle large volume orders if required.
Additionally, trade shows often feature live demonstrations of machinery and equipment, which offers a firsthand experience of the capabilities and performance of the machines. This allows companies to assess the quality of the machinery, the level of automation, and the efficiency of the machining processes. It is essential to choose suppliers with advanced technology and modern machinery to ensure high-quality and precise machining of plastics.
Furthermore, attending trade shows in China provides an opportunity to gain insights into the latest trends, materials, and innovations in the plastics machining industry. This knowledge can be crucial when selecting suppliers for specific projects or when exploring new applications and possibilities. Trade shows often have conferences and seminars where industry experts share their expertise and discuss emerging technologies, market trends, and best practices, enriching attendees’ knowledge and expertise.
In conclusion, leveraging trade shows and expos for sourcing machining services for plastics in China offers numerous benefits. It enables companies to explore a wide range of suppliers, establish direct connections, assess machinery capabilities, and gain industry insights. By utilizing these platforms effectively, companies can enhance their sourcing strategies, streamline their supply chain, and ensure high-quality, cost-effective plastic machining services.
The Role of Agents and Sourcing Companies in Facilitating machining of plastics Purchases from China
Agents and sourcing companies play a crucial role in facilitating the purchase of machining plastics from China. These intermediaries act as connectors between buyers and manufacturers, streamlining the process and ensuring a successful transaction.
One key function of agents and sourcing companies is to identify reliable and reputable manufacturers in China. They conduct extensive research to find manufacturers with a strong track record and a proven expertise in machining plastics. This ensures that buyers can expect high-quality products and consistent manufacturing standards.
Agents and sourcing companies also assist in negotiations and price discussions. They have in-depth knowledge of the market and are familiar with the prevailing prices for machining plastics in China. By leveraging their expertise, they can help buyers secure competitive pricing and favorable terms.
Furthermore, these intermediaries act as intermediaries in the communication process. They bridge the language and cultural barriers that may exist between buyers and manufacturers, ensuring clear and effective communication. This helps avoid misunderstandings and allows for a smooth collaboration.
Agents and sourcing companies also handle logistical challenges associated with international trade. They coordinate the shipping and transportation of the purchased products, ensuring they are delivered safely and on time. This simplifies the process for buyers, saving them time and resources.
In summary, agents and sourcing companies play a vital role in facilitating the purchase of machining plastics from China. They help buyers find reliable manufacturers, negotiate favorable terms, facilitate communication, and handle logistical challenges. By utilizing their services, buyers can streamline their purchasing process, minimize risks, and ensure successful transactions.
Price Cost Research for machining of plastics manufacturers Companies in China, use temu.com and 1688.com
When it comes to machining of plastics manufacturers in China, two prominent online platforms that can be utilized for price cost research are temu.com and 1688.com. These platforms serve as comprehensive marketplaces, offering a wide range of products and services, including plastic machining services.
temu.com is a leading B2B sourcing platform, connecting buyers with suppliers across various industries, including plastics manufacturing. It provides a user-friendly interface and powerful search filters to find suitable plastic machining manufacturers in China. Users can easily browse through product catalogs, compare prices, and evaluate supplier capabilities.
On the other hand, 1688.com is a popular wholesale platform owned by Alibaba Group. It primarily serves the domestic Chinese market, offering products at factory-direct prices. While the website is in Chinese, it can be translated using browser plugins to facilitate browsing and communication. Buyers can find numerous manufacturers specializing in plastic machining on this platform, providing a cost-effective solution.
When conducting price cost research on these platforms, it is essential to consider specific factors. Firstly, quality standards and certifications are crucial to ensure the manufacturer meets the required quality levels. Secondly, it is advisable to obtain multiple quotes from different suppliers to compare prices and negotiate competitive deals.
To make the most out of temu.com and 1688.com, it is recommended to identify the specific plastic machining requirements in terms of quantity, material type, precision, dimensions, and finishing. Inquiries should be made to multiple manufacturers to gather detailed pricing proposals. It is also important to discuss terms such as payment methods, delivery timeframes, and order volumes to avoid any misunderstandings later.
In conclusion, temu.com and 1688.com are platforms that can be effectively used for price cost research when looking for machining of plastics manufacturers in China. By leveraging these platforms, buyers can find a wide range of suppliers, compare prices, and negotiate the best deals while ensuring quality standards and certifications are met.
Shipping Cost for machining of plastics import from China
When importing machined plastics from China, it is essential to consider the shipping cost to ensure a smooth and cost-effective process. The shipping cost for machining of plastics can vary depending on several factors.
Firstly, the weight and size of the goods will impact the shipping cost. Machined plastics can range in size and weight, so it is crucial to accurately measure these dimensions to estimate shipping fees. Shipping companies use weight or volume weight, whichever is higher, to determine the cost.
Secondly, the mode of transportation chosen will influence the shipping cost. Air freight is the fastest option but tends to be more expensive, while sea freight is more economical but takes longer. The choice depends on factors like urgency, budget, and the volume of the goods.
Additionally, the distance between the manufacturing location in China and the destination country affects the shipping cost. Longer distances generally mean higher shipping fees due to fuel costs and transportation charges.
Customs duties and taxes imposed by the destination country can also impact the overall shipping cost. It is essential to research and understand the specific regulations of the importing country to avoid any unexpected charges.
To optimize costs, it is advisable to use a freight forwarder or shipping agent experienced in handling imports from China. They can help negotiate better shipping rates, navigate customs procedures, and ensure proper documentation, reducing the risk of additional costs or delays.
In conclusion, when importing machined plastics from China, it is crucial to consider the weight and size of the goods, choose the most suitable transportation mode, analyze the distance, and account for customs duties. Seeking assistance from a shipping expert can aid in optimizing the shipping cost and ensuring a seamless import process.
Compare China and Other machining of plastics Markets: Products Quality and Price,Visible and Hidden Costs
China is one of the major players in the machining of plastics market, but how does it compare to other markets in terms of product quality, price, and visible and hidden costs?
Product quality in China’s machining of plastics market can vary. While there are reputable manufacturers that produce high-quality products, there are also lower-end manufacturers that may produce products of inferior quality. It is important for buyers to thoroughly research and select reliable manufacturers to ensure the desired level of product quality.
Price-wise, China generally offers competitive rates in the machining of plastics market. The country benefits from economies of scale, with a vast number of manufacturers operating within its borders. This competition tends to drive prices down, making Chinese products more affordable when compared to other markets.
Visible costs, such as upfront prices, are often competitive in China. Manufacturers in the country have the infrastructure and capabilities to produce large quantities, allowing them to keep prices relatively low. However, it is important to consider hidden costs as well. These costs may include quality control and assurance, transportation, import fees, and potential language or cultural barriers when dealing with Chinese manufacturers.
Other machining of plastics markets may offer similar or even better product quality at higher prices. Manufacturers in these markets may have specialized expertise or access to superior materials, resulting in a higher level of quality. However, buyers should weigh this against potential increased costs and whether the higher quality is essential for their specific needs.
When comparing visible and hidden costs, other markets may provide clearer pricing structures and more transparent communication channels. These markets may also have shorter supply chains, resulting in lower transportation costs and faster delivery times. Buyers should carefully evaluate the potential savings in visible costs against the risks and uncertainties associated with hidden costs in different markets.
In conclusion, China’s machining of plastics market offers competitive prices and a wide range of product quality. However, buyers should be cautious in selecting reliable manufacturers to ensure desired quality levels. Other markets may provide superior product quality but at higher prices. When considering visible and hidden costs, other markets may offer clearer pricing structures and lower transportation costs. Ultimately, buyers must carefully assess their specific requirements and conduct thorough research to choose the most suitable market for their machining of plastics needs.
Understanding Pricing and Payment Terms for machining of plastics: A Comparative Guide to Get the Best Deal
When it comes to the machining of plastics, understanding pricing and payment terms is crucial to ensure you get the best deal. This comparative guide will provide you with valuable insights to make informed decisions within a concise word limit of 300.
Firstly, it is important to note that pricing for machining plastics often varies based on factors such as material type, complexity of the design, tolerances, quantity, and lead time required. Different suppliers may offer different price ranges for their services, so comparing multiple quotes is essential to get the best deal.
Payment terms also play a significant role in your decision-making process. Suppliers usually require a deposit upfront to cover material costs and secure the project. The remaining balance is typically paid upon completion or after delivery. However, some companies may offer alternative payment arrangements, such as installment plans or credit terms for long-term clients. Understanding these options can provide flexibility for budgeting and cash flow management.
To ensure you receive accurate quotes, provide clear specifications and drawings of your desired plastic parts. Sharing comprehensive details will allow suppliers to assess the project complexity accurately and offer more precise pricing. It is also beneficial to inquire about any additional costs like tooling fees, setup charges, or shipping fees to have a comprehensive understanding of the total expenses.
Consider the supplier’s capabilities and experience when evaluating pricing. A company with advanced machinery, skilled technicians, and a solid track record may offer higher prices but can also guarantee quality and accuracy. It is essential to strike a balance between cost-effectiveness and ensuring you receive satisfactory results.
Furthermore, inquire about the supplier’s lead time and production capacity. Some may charge premium prices for expedited delivery, while others may offer discounts for longer lead times, aligning with your project timeline and urgency.
Negotiation is another key component in securing the best deal. Once you have multiple quotes in hand, compare the pricing, payment terms, and additional services offered. Be prepared to negotiate with suppliers to achieve a more favorable agreement, such as discounts for large orders or waiving certain fees if feasible.
In conclusion, understanding pricing and payment terms is vital when seeking the best deal for machining plastics. Compare quotes, consider payment options, provide detailed specifications, understand additional costs, evaluate capabilities, negotiate, and strive for a mutually beneficial agreement. With this comparative guide, you can confidently navigate the pricing landscape and make informed decisions to meet your plastic machining needs.
Chinese Regulations and Industry Standards Certifications for machining of plastics,Import Regulations and Customs for machining of plastics from China
Chinese Regulations and Industry Standards Certifications for machining of plastics ensure the quality and safety of plastic machined products in the country. The main regulatory body overseeing this industry is the China National Certification and Accreditation Administration (CNCA). CNCA administers a range of certifications and standards that manufacturers in China must comply with.
One of the key certifications is the China Compulsory Certification (CCC), which is required for certain products entering the Chinese market, including plastic machined products. This certification ensures that the products meet certain safety and quality requirements.
In addition to CCC, there are several industry standards that manufacturers must adhere to. These standards include the National Standard for Machined Plastic Products (GB/T), which provides guidelines on the dimensions, materials, and technical requirements for plastic machined products.
When importing plastic machined products from China, it is important to comply with import regulations and customs procedures. The General Administration of Customs (GAC) is responsible for regulating imports in China. Importers must provide the necessary documentation such as the bill of lading, commercial invoice, packing list, and any required certifications or licenses.
Importers may also need to comply with specific requirements of their home country, such as obtaining necessary import permits or complying with product safety standards. It is advisable to consult with customs authorities or engage a customs broker to navigate the import process smoothly.
Overall, understanding and complying with Chinese regulations, industry standards certifications, and import regulations and customs procedures are crucial for ensuring the quality, safety, and legality of machining plastic products imported from China.
Sustainability and Environmental Considerations in machining of plastics Manufacturing
The machining of plastics in manufacturing processes poses various challenges and environmental considerations. While plastic materials provide several advantages such as lightweight, durability, and versatility, their production and machining can have adverse effects on the environment if not properly managed.
One significant sustainability concern in plastic machining is the generation of waste. Machining processes often result in significant amounts of plastic waste, including offcuts, shavings, and dust. If not handled appropriately, these waste materials can contribute to pollution and landfills. To address this concern, manufacturers should strive to implement waste management practices such as recycling, reusing, or repurposing plastic waste.
Another environmental consideration is the energy consumption associated with plastic machining. Machining processes, such as milling, turning, or laser cutting, usually require substantial energy inputs. To minimize energy consumption and reduce carbon emissions, companies can adopt energy-efficient machining techniques, invest in modern equipment, and optimize machining parameters to maximize material removal rates and minimize idle times.
In addition, the choice of coolant or cutting fluids in plastic machining should be carefully considered. Traditional cutting fluids often contain harmful chemicals that can negatively impact the environment. Therefore, companies should explore alternatives like water-based or biodegradable cutting fluids to mitigate the environmental impact. Proper maintenance and disposal of cutting fluids are also crucial to prevent contamination of water sources.
Furthermore, the selection of plastic materials itself plays a vital role in sustainability. Some plastics, such as PVC or polystyrene, are derived from non-renewable resources and pose environmental hazards during their production and disposal. Opting for eco-friendly plastics, such as biodegradable or recycled plastics, can significantly reduce the ecological footprint associated with plastic machining.
Lastly, implementing efficient machining practices, such as minimizing scrap or optimizing tool paths, can contribute to sustainability. By reducing material waste or improving production processes’ efficiency, companies can minimize their environmental footprint and simultaneously enhance their profitability.
Overall, sustainability and environmental considerations in plastic machining involve waste management, energy conservation, coolant selection, material choice, and process optimization. By adopting these practices, manufacturers can contribute to a greener future while maintaining their competitiveness in the plastic manufacturing industry.
List The Evolution history of “machining of plastics”
The machining of plastics has witnessed significant evolution throughout history, driven by advancements in technology and growing demand for efficient and precise plastic components. From its humble beginnings to the modern era, here is a concise overview of its evolution:
1. Early techniques (1900s-1940s): In the early 20th century, plastic machining relied on rudimentary processes such as manual cutting, sawing, and abrading. These techniques were limited in terms of precision and efficiency and were mainly used for basic shaping operations.
2. Introduction of routers (1950s-1960s): The arrival of electric routers revolutionized plastic machining. These tools, equipped with rotating cutting bits, expedited the cutting process and allowed for more complex shapes and finishes. However, they still required skilled operators to achieve desired results.
3. Computer Numerical Control (CNC) era (1970s-1980s): The advent of CNC machining brought a major breakthrough in the machining of plastics. Computer-controlled machines enabled precise and repeatable cuts based on pre-programmed instructions. This technology reduced human error, increased productivity, and improved machining accuracy.
4. Milling and lathing advancements (1990s-2000s): In this period, advancements in milling and lathing techniques led to further improvements in plastic machining. High-speed machining became feasible, allowing for faster production and better surface finishes. Additionally, multi-axis CNC machines enabled the simultaneous machining of complex geometries, expanding the possibilities for plastic component design.
5. Digitalization and automation (2010s-present): The recent focus on Industry 4.0 technologies has brought even more advancements to plastic machining. Integration with digital design software allows for seamless transfer of 3D models to CNC machines, reducing setup time and enhancing accuracy. Automation features, such as robotic loading and unloading, further optimize production processes and increase efficiency.
Today, plastic machining has become an indispensable part of various industries, including automotive, aerospace, medical, and consumer goods. Continued research and development aim to refine machining techniques, optimize tooling, and explore novel approaches like additive manufacturing to further advance the field of plastic machining.
The Evolution and Market Trends in machining of plastics Industry
The machining of plastics industry has witnessed significant evolution and market trends in recent years. With the advancements in technology, the industry has experienced a shift towards more automated and precise manufacturing processes.
One of the key developments in the machining of plastics industry is the adoption of computer numerical control (CNC) machines. These machines allow for accurate cutting, milling, drilling, and shaping of plastic materials. CNC machines have enhanced the efficiency and productivity of the industry by reducing human errors and minimizing waste. They can work on complex designs and produce intricate parts with high precision, opening up new possibilities for various applications.
Another important trend in the machining of plastics industry is the increasing demand for lightweight materials. As industries such as automotive and aerospace look for ways to improve fuel efficiency and reduce emissions, lightweight plastic components are becoming more popular. Machining techniques have evolved to meet the requirements of manufacturing lightweight plastic parts that possess high strength-to-weight ratios.
Additionally, the industry has seen a rise in the use of high-performance plastics. These materials offer unique properties such as heat resistance, chemical resistance, and superior mechanical strength. Machining techniques have been adapted to accommodate these high-performance plastics, allowing for the production of components that can withstand extreme conditions.
The market for machining of plastics has also been influenced by the growing awareness and emphasis on sustainability. Manufacturers are increasingly focusing on reducing waste and recycling plastic materials. Machining processes have been optimized to minimize material wastage and promote eco-friendly practices.
Furthermore, the adoption of Industry 4.0 technologies has made its way into the machining of plastics industry. Integration of sensors, data analytics, and automation has enabled real-time monitoring of machining processes, leading to improved quality control and production efficiency.
In conclusion, the machining of plastics industry has undergone significant evolution driven by advancements in technology and changing market demands. The adoption of CNC machines, lightweight materials, high-performance plastics, sustainable practices, and Industry 4.0 technologies has reshaped the industry, making it more efficient, precise, and environmentally friendly.
Custom Private Labeling and Branding Opportunities with Chinese machining of plastics Manufacturers
Chinese machining of plastics manufacturers offer custom private labeling and branding opportunities for businesses looking to create their own unique product lines. With their expertise in plastic machining and manufacturing, these manufacturers can help businesses bring their ideas to life.
The process begins with the business providing their product design or concept to the manufacturer. Using their advanced machinery and tools, the manufacturers can then create prototypes or samples for approval. This allows businesses to visualize and refine their product before proceeding with mass production.
Once the design is finalized, the Chinese manufacturers can proceed with private labeling and branding. This includes adding the business’s logo, product name, and any other desired branding elements onto the product. Manufacturers may employ various techniques such as laser engraving, printing, or embossing to achieve the desired branding outcome.
Additionally, Chinese manufacturers often offer customizable packaging options. This allows businesses to create a cohesive and professional look for their products. Packaging can be tailored to meet specific requirements, such as color schemes, shapes, or sizes, further enhancing the brand’s image.
Working with Chinese machining of plastics manufacturers offers several advantages. Firstly, the cost-effectiveness of manufacturing in China allows businesses to achieve competitive pricing for their products. Secondly, these manufacturers are proficient in working with a wide range of plastic materials, ensuring that businesses can choose the most suitable material for their products.
In conclusion, partnering with Chinese machining of plastics manufacturers presents businesses with attractive custom private labeling and branding opportunities. The ability to create unique product lines, alongside customizable packaging, allows businesses to establish their brand identity and stand out in the market. With their expertise in plastic machining and manufacturing, Chinese manufacturers can ensure high-quality production and cost-effectiveness.
Tips for Procurement and Considerations when Purchasing machining of plastics
When purchasing machining services for plastics, there are several important considerations to keep in mind to ensure a successful procurement process. Here are some tips to help you make informed decisions:
1. Material Selection: Choose the right type of plastic for your specific application. Consider factors such as strength, flexibility, chemical resistance, and heat tolerance.
2. Machining Capabilities: Verify if the supplier has the necessary machinery and expertise to handle the machining process for your desired plastic material. Ensure they have experience working with plastics and can deliver the level of precision required.
3. Quality Control: Inquire about the supplier’s quality control measures. Ensure they have the necessary inspections, testing, and certifications in place to guarantee the desired quality of the machined parts.
4. Cost: Request detailed quotations from multiple suppliers and compare their pricing. However, avoid solely focusing on the cheapest option, as low-cost suppliers may compromise on quality, leading to subpar parts or delays in production.
5. Lead Time: Discuss the expected lead time with the suppliers to ensure it aligns with your project timeline. Consider any potential delays that may arise due to their workload or any unexpected issues.
6. Communication and Documentation: Establish clear lines of communication with the supplier to address any queries, concerns, or modifications during the production process. Request comprehensive documentation, including drawings, specifications, and certificates of compliance.
7. Packaging and Shipping: Inquire about the supplier’s packaging methods to ensure the parts are adequately protected during transit. Discuss shipping options to select the most suitable, cost-effective, and reliable method.
8. Supplier Experience and Reputation: Research the supplier’s reputation in the industry. Look for reviews, testimonials, and case studies that demonstrate their experience and ability to deliver high-quality machined plastic parts.
9. Future Collaboration: Consider building a long-term relationship with the supplier if you anticipate future machining needs. Long-term collaboration can lead to better cost efficiencies, improved communication, and more tailored services.
10. IP Protection: Discuss intellectual property protection measures such as confidentiality agreements to safeguard your designs and proprietary information.
By considering these tips, you can make more informed decisions when procuring machining services for plastics. Prioritizing material selection, quality control, cost, lead time, documentation, and supplier reputation will help ensure a successful and satisfactory purchasing experience.
FAQs on Sourcing and Manufacturing machining of plastics in China
1. Why should I consider sourcing and manufacturing plastic machining in China?
Sourcing and manufacturing plastic machining in China offers various advantages, such as cost-efficiency due to lower labor and production costs. China has a well-developed manufacturing infrastructure, skilled labor, and advanced machinery, which ensures competitive pricing and high-quality products. Additionally, China is a leading global supplier of plastics, offering a wide range of materials and customization options.
2. How can I find a reliable plastic machining supplier in China?
To find a reliable supplier, you can utilize online platforms like Alibaba, Made-in-China, or Global Sources, where you can filter and compare different suppliers based on their certifications, product range, and customer reviews. It’s crucial to thoroughly research and vet potential suppliers, review their experience, capabilities, and request samples or prototypes to evaluate the quality of their work.
3. Can China handle both small and large-scale plastic machining orders?
Yes, China’s manufacturing industry caters to a diverse range of customer needs, from small-scale prototype machining to large-scale production volumes. With their flexible production capabilities, Chinese suppliers can accommodate various order sizes, offering cost-effective options for both small businesses and larger companies.
4. Are there any quality concerns when sourcing plastic machining from China?
While quality standards in China have significantly improved in recent years, it is essential to choose a reputable supplier. Thoroughly review their quality control processes, certifications like ISO 9001 or TS16949, and request quality assurance documentation. Conducting factory visits or hiring third-party quality inspectors can also help ensure compliance with your specific quality requirements.
5. How are intellectual property rights protected when sourcing plastic machining in China?
Protecting intellectual property (IP) rights is a crucial consideration when sourcing from China. While IP infringement cases have been reported, many Chinese manufacturers have recognized the importance of IP protection. When sourcing, it is advisable to sign non-disclosure agreements (NDAs) with suppliers, register your designs and patents, and work solely with trusted suppliers who have a respectable track record and positive customer feedback.
6. How long does the plastic machining process typically take in China?
The lead time for plastic machining in China varies depending on factors like the complexity of the part, order size, and supplier’s production capacity. Generally, it takes around 2-4 weeks to complete plastic machining orders. However, it’s important to communicate your specific project timelines with the supplier and ensure they can meet your delivery requirements.
By considering these FAQs, you can improve your understanding of sourcing and manufacturing plastic machining in China and make informed decisions that optimize cost, quality, and delivery for your specific needs.
Why contact sourcifychina.com get free quota from reliable machining of plastics suppliers?
Sourcifychina.com offers free quota from reliable machining of plastics suppliers for several reasons. Firstly, by offering a free quota, Sourcifychina.com aims to attract potential customers and encourage them to utilize their services. This strategy allows them to showcase the value they can provide as a sourcing platform.
Secondly, Sourcifychina.com seeks to build trust and credibility among customers by partnering with reliable machining of plastics suppliers. By vetting and partnering with trustworthy suppliers, Sourcifychina.com ensures that customers receive high-quality products and services.
Furthermore, the free quota allows customers to assess the capabilities and pricing of different suppliers without any financial commitment. This gives them the opportunity to compare various suppliers and make informed decisions.
The use of plastics in various industries is widespread, and finding reliable machining suppliers can be challenging. Sourcifychina.com recognizes this challenge and aims to simplify the sourcing process by providing a curated list of trusted suppliers.
By offering a free quota, Sourcifychina.com enables customers to easily connect and obtain quotes from these suppliers. This not only saves time and effort but also provides customers with a hassle-free sourcing experience.
Moreover, Sourcifychina.com understands the importance of cost-effectiveness in sourcing. By partnering with reliable suppliers, they can negotiate competitive prices and pass these savings onto their clients. The free quota allows customers to access these cost-effective solutions and leverage the expertise of trusted suppliers, ultimately leading to better business outcomes.
In conclusion, Sourcifychina.com offers a free quota from reliable machining of plastics suppliers to attract customers, build trust, simplify the sourcing process, and provide cost-effective solutions. This approach demonstrates their commitment to customer satisfaction and streamlining the sourcing experience for businesses.