Introduce about machining work guide,Qulity,Cost,Supplier,Certification,Market,Tips,FAQ
Machining work is a process that involves using various tools and machinery to shape, cut, or finish a material into a desired product or component. This guide will provide an overview of different aspects related to machining work, including quality, cost, supplier selection, certification, market trends, tips, frequently asked questions (FAQs), with concise information not exceeding 300 words.
Quality is of utmost importance in machining work as it determines the performance and durability of the final product. Machined parts must adhere to precise specifications and tolerances, ensuring accuracy and functionality. To ensure quality, it is advisable to work with reputable suppliers who have a track record of delivering high-quality machining services.
Cost is another crucial factor to consider in machining work. It is influenced by various factors, including the complexity of the design, material type, machining process, and quantity required. It is essential to obtain quotes from different suppliers to compare costs and make an informed decision, balancing quality and price.
Selecting the right supplier is critical for successful machining work. Consider factors such as experience, expertise, technology, and equipment capabilities. Look for suppliers who can meet your specific requirements, provide timely deliveries, and offer competitive prices. Checking for certifications like ISO 9001 can also ensure the supplier’s commitment to delivering quality products.
Certifications play a significant role in distinguishing reliable suppliers. ISO certifications indicate adherence to international standards and quality assurance practices. Suppliers with certifications demonstrate their commitment to excellence, product consistency, and continuous improvement.
The machining market is highly competitive, with advancements in technology, automation, and precision. As industries such as automotive, aerospace, electronics, and medical continue to grow, the demand for high-quality machined parts is increasing steadily.
Here are a few tips for successful machining work: provide detailed specifications, communicate clearly with the supplier, conduct regular inspections to ensure quality, and establish a long-term partnership for consistent results.
Frequently Asked Questions (FAQs):
1. What materials can be machined?
– Machining can be performed on a wide range of materials, including metals like steel, aluminum, titanium, and various plastics.
2. What machining processes are commonly used?
– Common machining processes include turning, milling, drilling, tapping, grinding, and various types of cutting.
3. Can complex geometries be machined?
– Yes, with advanced CNC (Computer Numeric Control) machines, complex shapes and intricate features can be accurately machined.
In conclusion, understanding the key aspects of machining work such as quality, cost, supplier selection, certifications, market trends, tips, and frequently asked questions can facilitate successful and efficient manufacturing processes.
Types of machining work
Machining is the process of shaping or reshaping materials using various cutting tools and machines. It involves removing unwanted material from a workpiece to create the desired shape, size, and finish. There are several types of machining work, each serving a specific purpose and requiring different techniques and equipment. Some of the most common types of machining work include:
1. Turning: Turning is the process of rotating a workpiece while a single-point cutting tool removes material to create cylindrical shapes. This type of machining is commonly used to produce round parts such as shafts, screws, and nuts.
2. Milling: Milling involves using a rotating multi-point cutting tool to remove material from the workpiece in an up-and-down motion. It is commonly used to create complex shapes, slots, and contours on various materials. There are different types of milling, including face milling, plain milling, and peripheral milling.
3. Drilling: Drilling is the process of creating holes in a workpiece using a rotating cutting tool called a drill bit. It is one of the most common machining operations and is used to create holes of various sizes and depths in different materials.
4. Grinding: Grinding is a machining process that uses an abrasive wheel to remove small amounts of material from the workpiece’s surface. It is commonly used to achieve precise surface finishes, improve part dimensions and accuracy, and sharpen cutting tools.
5. Boring: Boring is the process of enlarging or refining an existing hole in a workpiece using a single-point cutting tool. It is typically used to achieve tight tolerances and improve surface finish.
6. Sawing: Sawing involves using a saw blade to cut through materials. It can be done manually or using power tools like bandsaws or circular saws. Sawing is commonly used to cut stock material into desired lengths or to separate parts.
7. Laser Cutting: Laser cutting uses a focused laser beam to melt, burn, or vaporize material from the workpiece. It is a precise and fast method commonly used for cutting complex shapes and contours on materials like metal, plastic, and wood.
In addition to these, there are various other machining processes such as honing, threading, broaching, and electrochemical machining that serve specific purposes and are used in different industries. Each machining process requires skilled operators and specialized machinery to ensure accurate and high-quality workpieces are produced.
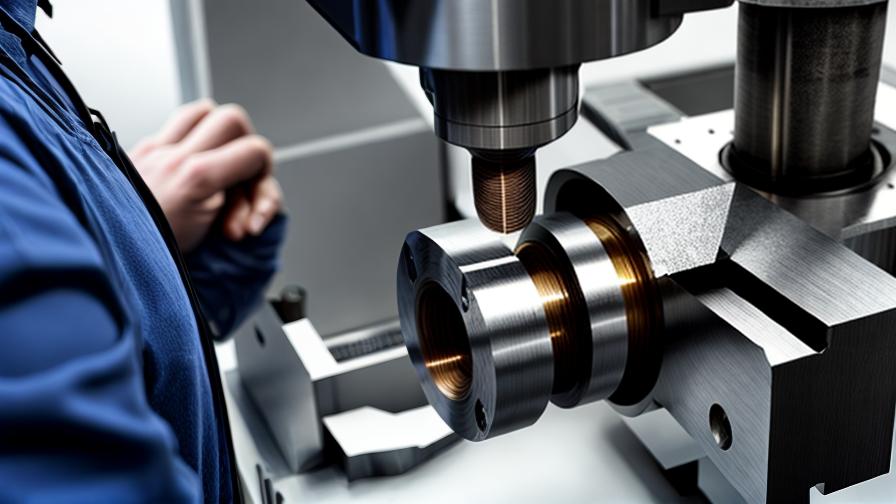
Pros and Cons of Using machining work
Using machining work has its own set of pros and cons, which can be considered before deciding whether or not to employ this method. Here are some of the key points to consider:
Pros:
1. Precision: Machining work allows for high levels of precision and accuracy in the production process. Computer Numerical Control (CNC) machines can carry out complex tasks with minimal errors, resulting in high-quality end products.
2. Versatility: Machining work is suitable for a wide range of materials, including metals, plastics, and composites. This versatility enables manufacturers to produce a diverse array of products.
3. Efficiency: CNC machines are capable of performing repetitive tasks quickly and efficiently, resulting in higher productivity levels. This can be especially beneficial for mass production or projects with tight deadlines.
4. Complex geometries: Machining work can achieve intricate and complex shapes that may be challenging or impossible with other manufacturing techniques. This can be advantageous in industries such as aerospace and automotive where intricate designs are common.
5. Customization: Machining work allows for easy customization of products. CNC machines can be programmed to produce specific designs or modifications quickly, catering to individual customer requirements.
Cons:
1. High initial investment: Acquiring machining equipment can be expensive, especially for smaller businesses. CNC machines and other required tools may require a substantial investment, making it difficult for startups or those on a limited budget to adopt this technology.
2. Skilled labor requirement: Operating machining equipment often requires skilled operators who are properly trained in programming and operating CNC machines. Finding and training skilled personnel can pose a challenge.
3. Time-consuming setup: Setting up the machines for each new task can be time-consuming, as proper programming and calibration are essential. This might not be suitable for projects requiring quick turnarounds or high flexibility.
4. Limited suitability for certain materials: While machining can work with various materials, some heat-sensitive materials or extremely hard substances may be unsuitable for this process. Alternative manufacturing techniques may be more appropriate in such cases.
5. High maintenance and operating costs: Machining equipment maintenance and operation expenses can be significant. Routine maintenance, software updates, and tool replacements can incur ongoing costs that need to be considered.
In conclusion, machining work offers several advantages such as precision, versatility, and efficiency. Nonetheless, it also presents challenges like initial investment, skilled labor requirements, setup time, limited material suitability, and high maintenance costs. Thus, weighing these pros and cons is crucial in determining whether machining work is the most suitable manufacturing method for a given situation.
machining work Reference Specifications (varies for different product)
Machining work commonly refers to the process of shaping or cutting material using various tools and equipment. It involves removing unwanted material from a workpiece to achieve the desired shape, size, and surface finish. Machining work plays a crucial role in manufacturing and is used in various industries such as aerospace, automotive, medical, electronics, and more.
When it comes to machining work, reference specifications are essential. These specifications serve as a guide or set of instructions that help ensure the desired outcome of the machining process. The reference specifications may vary depending on the specific product being machined.
Reference specifications typically include details about the material to be machined, such as its composition, hardness, and other physical properties. They also provide information about the required dimensions, tolerances, and surface finish of the finished product. In addition, reference specifications may specify the type of machining process to be used, such as milling, turning, drilling, grinding, or a combination of these.
Furthermore, the reference specifications may specify the use of certain cutting tools, such as end mills, drills, or inserts, as well as the cutting parameters like speed, feed rate, and depth of cut. These parameters ensure that the machining process is optimized for efficiency and to achieve the desired level of precision.
Another important aspect of reference specifications is the quality requirements. They may include standards or industry-specific specifications that the final product must meet, such as ISO, ASTM, or customer-specific requirements. These quality requirements ensure that the machined product meets the desired functional and aesthetic standards.
It is crucial for machinists and manufacturers to carefully review and adhere to the reference specifications provided for each product. Following the specifications accurately helps prevent errors, minimize scrap and rework, and deliver a high-quality finished product.
In conclusion, machining work involves shaping or cutting material to achieve the desired outcome. Reference specifications serve as a guide for machining processes and include information about the material, dimensions, tolerances, surface finish, cutting tools, parameters, and quality requirements. Adhering to these specifications is essential to ensure the successful completion of machining work and the production of high-quality products.
Applications of machining work
Machining work plays a crucial role in a wide range of industries, including automotive, aerospace, medical, and manufacturing. Some of the key applications of machining work include:
1. Prototyping: Machining is commonly used in the creation of prototypes for new products. By using Computer Numerical Control (CNC) machining processes, manufacturers can quickly and accurately produce prototype parts for testing and evaluation.
2. Production of precision components: Machining is essential for producing high-precision components for various industries. From small intricate parts for medical devices to large components for aerospace applications, machining processes enable the production of precise and complex parts.
3. Repair and maintenance: Machining is often used for repair and maintenance tasks, such as re-machining worn parts or fixing damaged components. By using machining techniques, manufacturers can restore parts to their original condition and extend their lifespan.
4. Custom tooling: Machining work is crucial for the production of custom tooling, such as molds, dies, and fixtures. These tools are essential for manufacturing processes and require high precision and accuracy, which machining can provide.
5. Fabrication of prototypes: Machining is also used in the fabrication of prototypes for new products. By using machining processes, manufacturers can quickly produce custom parts and components for testing and validation before moving to full-scale production.
Overall, machining work is a versatile and essential process that is utilized in a variety of applications across different industries. From prototyping to production, repair, and custom tooling, machining plays a critical role in the manufacturing process.
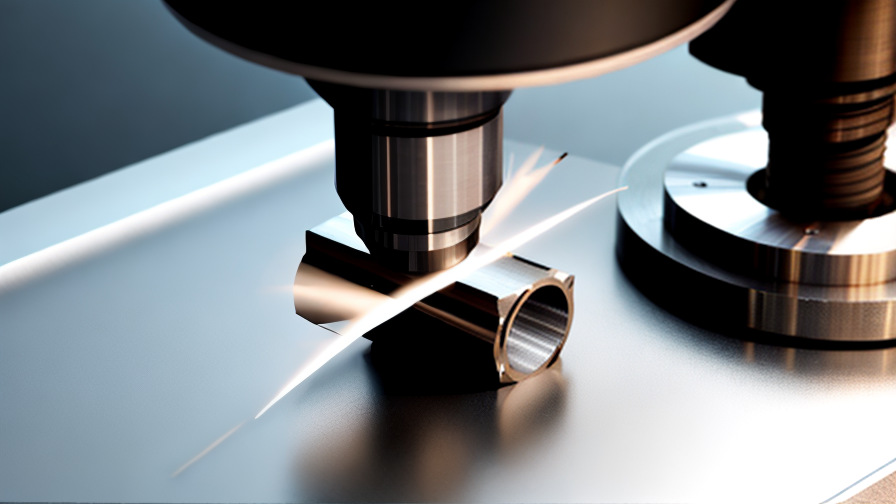
The Work Process and how to use machining work
The work process and how to use machining work is an important aspect in various industries where precise and accurate manufacturing is required. Machining is a manufacturing process that involves the removal of material from a workpiece using a cutting tool, resulting in the desired shape and size. It is commonly used for creating intricate and complex components.
The first step in the work process is to determine the requirements and specifications of the desired component. This includes understanding the material, dimensions, tolerances, and any surface finish requirements. Once these details are established, the machining work can begin.
The next step is to select the appropriate machining tools and equipment. This may include lathes, mills, drills, grinders, or other specialized machines. The choice of tools depends on the complexity of the part, material type, and required level of precision.
After selecting the tools, the workpiece is securely mounted onto the machine. This ensures stability and accuracy during the machining process. The operator then sets the cutting parameters such as the cutting speed, feed rate, and depth of cut. These parameters may vary depending on the material and cutting tool being used.
Once everything is set, the machining work begins. The cutting tool makes contact with the workpiece and removes material in the desired shape and size. The operator closely monitors the process to ensure that the dimensions and tolerances are adhered to. This may involve making adjustments to the cutting parameters or tooling as necessary.
During the machining process, coolant or lubricant may be used to reduce heat and friction, improve surface finish, and extend tool life. The type and application of coolant depend on the material being machined.
Once the machining work is completed, the finished component is inspected for quality and accuracy. This may involve measurements using precision instruments such as calipers, micrometers, or coordinate measuring machines.
In conclusion, machining work is a crucial part of the manufacturing process. It involves understanding the requirements, selecting appropriate tools and equipment, setting cutting parameters, monitoring the operation, and inspecting the finished product. Adhering to these steps ensures the production of high-quality and precise components in various industries.
Quality Testing Methods for machining work and how to control the quality
There are several quality testing methods that can be used for machining work, including visual inspection, dimensional inspection, surface finish measurement, hardness testing, and non-destructive testing techniques such as ultrasonic testing and dye penetrant testing. Visual inspection involves visually examining the machined part for any defects or abnormalities. Dimensional inspection involves measuring the dimensions of the machined part using tools such as calipers, micrometers, and CMM machines. Surface finish measurement involves measuring the surface roughness of the machined part using tools such as profilometers. Hardness testing involves measuring the hardness of the machined part using tools such as hardness testers. Non-destructive testing techniques such as ultrasonic testing and dye penetrant testing can be used to detect defects in the machined part without causing any damage to the part.
To control the quality of machining work, it is important to implement a quality control plan that includes regular inspection and testing of machined parts throughout the manufacturing process. This can involve creating inspection checkpoints at various stages of the machining process, training operators on quality standards and testing methods, using quality control tools and equipment such as gauges and measuring devices, and establishing clear quality control procedures and documentation. By implementing a comprehensive quality control plan and utilizing effective testing methods, manufacturers can ensure that machined parts meet the required quality standards and specifications.
machining work Sample Policy and Post-Purchase Considerations for machining work from China
Sample Policy for Machining Work from China:
1. Quality Assurance:
– The supplier must adhere to strict quality control measures throughout the machining process.
– They should provide samples and prototypes for approval before proceeding with mass production.
– Regular inspections and quality tests should be conducted during production.
2. Communication and Documentation:
– Clear and effective communication channels should be established with the supplier.
– All specifications and requirements for the machining work should be documented in writing.
– Any changes to the project scope must be communicated and documented promptly.
3. Timelines and Delivery:
– The supplier should provide a clearly defined timeline for the completion of the machining work.
– Regular updates on the project’s progress should be provided.
– Delivery dates should be agreed upon and adhered to.
4. Pricing and Payment Terms:
– The supplier should provide a detailed breakdown of all costs associated with the machining work.
– Pricing should be competitive and transparent.
– Payment terms should be clear and mutually agreed upon.
Post-Purchase Considerations for Machining Work from China:
1. Inspection upon Arrival:
– Thoroughly inspect the received machining work upon arrival to ensure it meets the agreed-upon quality standards.
– Address any discrepancies or quality issues with the supplier immediately.
2. Prompt Communication:
– Maintain open lines of communication with the supplier to address any post-purchase concerns promptly.
– Communicate any issues, such as defective pieces or damages, and work towards a resolution.
3. Feedback and Reviews:
– Provide constructive feedback to the supplier regarding the quality, timeliness, and overall experience of the machining work.
– Consider leaving reviews or testimonials to assist other potential buyers.
4. Establish Long-Term Relationships:
– If satisfied with the machining work, consider establishing a long-term relationship with the Chinese supplier for future projects.
– Building strong partnerships can lead to improved pricing, consistent quality, and better communication.
It is crucial to customize the sample policy and post-purchase considerations based on individual requirements and the specific nature of the machining work being outsourced from China.
Sourcing machining work from China: Opportunities, Risks, and Key Players
Sourcing machining work from China has become increasingly popular due to the country’s abundant manufacturing capabilities and competitive prices. However, there are both opportunities and risks associated with this decision, and understanding the key players is crucial for a successful business engagement.
Opportunities:
1. Cost advantage: China’s lower manufacturing costs provide an opportunity for businesses to reduce their production expenses significantly. This cost advantage allows for higher profit margins or more competitive pricing for the end product.
2. Wide range of capabilities: China has a vast network of machining facilities that offer a wide range of capabilities. From CNC machining to precision milling, businesses can find suitable suppliers for their specific machining needs.
3. Scale and capacity: Chinese manufacturers have immense production capacity, making them capable of handling large orders and meeting tight deadlines.
4. Technological advancements: China has made considerable progress in adopting advanced manufacturing technologies. Partnering with the right suppliers can provide access to cutting-edge machinery and innovation.
5. Diverse supply chain: China’s diverse manufacturing ecosystem allows businesses to source various components and materials from a single location, streamlining the supply chain.
Risks:
1. Quality control: Maintaining consistent quality may pose challenges when sourcing from China. Partnerships with reputable suppliers, thorough inspections, and clear quality requirements are essential to mitigate this risk.
2. Intellectual property risks: Protecting intellectual property (IP) can be a concern when sourcing from China. Engaging in due diligence, establishing confidentiality agreements, and seeking legal advice are crucial to safeguard IP rights.
3. Communication and language barriers: Cultural and language differences can impact communication, leading to misunderstandings or delays. Businesses should establish effective communication channels, preferably with bilingual staff involved.
4. Long lead times: Shipping from China can take longer, which can impact production timelines. Adequate planning and utilizing express shipping options can help mitigate this risk.
5. Geopolitical and trade uncertainties: Changing trade policies, geopolitical tensions, or tariffs can introduce uncertainties in the global supply chain. Periodic assessments and contingency plans are essential to adapt to such situations.
Key players:
1. Foxconn Technology Group: Known for electronic manufacturing, Foxconn offers comprehensive machining capabilities across various industries.
2. BYD Company Limited: A leader in electric vehicle manufacturing, BYD also provides machining services for automobile components.
3. Huawei Technologies Co., Ltd.: Besides telecommunications, Huawei manufactures complex precision components, offering a wide range of machining services.
4. Wuxi Techwell Machinery Co., Ltd.: Specializing in metal fabrication and machining, Techwell serves multiple industries, including automotive and construction.
5. Shanghai Electric Group Co., Ltd.: With a focus on power generation and electrical equipment, Shanghai Electric also provides machining services for related components.
In conclusion, sourcing machining work from China offers opportunities such as cost advantages, a diverse supply chain, and advanced manufacturing capabilities. However, businesses must carefully manage risks related to quality control, IP protection, communication barriers, lead times, and geopolitical uncertainties. Partnering with reputable companies like Foxconn, BYD, Huawei, Techwell, or Shanghai Electric can provide a reliable foundation for successful sourcing endeavors.
How to find and select reliable machining work manufacturers in China,use google search manufacturers and suppliers
When searching for reliable machining work manufacturers in China, utilizing Google search for manufacturers and suppliers is an effective approach. To begin your search, follow these steps:
1. Perform a general search: Use relevant keywords such as “machining work manufacturers” or “machining work suppliers” in China on Google. The results will display numerous websites and directories related to manufacturers.
2. Refine your search: Specify your search by including necessary details like the type of machining work you require (CNC machining, precision machining, etc.), material specifications, or any other specific requirements. This step will help you narrow down the search results to find manufacturers that match your criteria.
3. Evaluate the websites: Visit the websites of potential manufacturers to gather information about their capabilities, experience, certifications, production capabilities, and quality control processes. Look for details about the types of machining work they specialize in and their clientele. Established companies with a positive track record are more likely to provide reliable services.
4. Check for certifications and quality control: Verify if the manufacturers have appropriate certifications such as ISO 9001, ISO 13485, or any industry-specific certifications. These certifications indicate their dedication to quality. Additionally, inquire about their quality control measures to ensure consistent and reliable machining work production.
5. Evaluate customer reviews and testimonials: Look for customer reviews, testimonials, or feedback on the manufacturer’s website or through a separate search. Reviews from other buyers can provide valuable insights into the manufacturer’s reliability, communication, response time, delivery, and quality of products.
6. Communicate directly: Reach out to the shortlisted manufacturers through their provided contact information. Ask questions related to your machining work requirements, production capacity, lead times, pricing, and any other concerns you may have. Prompt and clear communication is indicative of their professionalism and reliability.
7. Request samples or prototypes: Consider requesting samples or prototypes of the machining work you require. This will allow you to evaluate the manufacturer’s quality firsthand before making any large commitments.
By following these steps and thoroughly evaluating the potential manufacturers, you can select a reliable machining work manufacturer in China that best suits your needs. Remember to conduct due diligence and scrutinize all available factors before making your final decision.
How to check machining work manufacturers website reliable,use google chrome SEOquake check if ranking in top 10M
To check if a machining work manufacturer’s website is reliable, you can use Google Chrome with the SEOquake extension installed. First, open the manufacturer’s website in Google Chrome and then click on the SEOquake icon in the toolbar. This will display important SEO data about the website, including its rank in the top 10 search results.
If the manufacturer’s website is ranking within the top 10 search results, it is likely to be a reliable and reputable source. This indicates that the website is well-optimized for search engines and is considered authoritative in its field.
In addition to checking the website’s ranking, you can also look for other signs of reliability such as a professional design, clear contact information, positive customer reviews, and an active blog or news section.
By using Google Chrome with SEOquake and following these tips, you can quickly assess the reliability of a machining work manufacturer’s website before making a decision to do business with them.
Top 10 machining work manufacturers in China with each 160 words introduce products,then use markdown create table compare
1. **Foxron Precision Metal Parts Co., Ltd.**
Foxron specializes in CNC machining, precision turning, milling, and sheet metal fabrication. They produce a wide range of products such as aluminum parts, stainless steel components, and custom machined parts.
2. **Dongguan Qy Hardware Products Co., Ltd.**
Qy Hardware offers CNC machining services for a variety of industries including automotive, medical, and electronics. Their products range from precision machined parts to complex assemblies.
3. **Shenzhen Dajin Precision Hardware Co., Ltd.**
Dajin Precision Hardware is known for their high-quality precision machining services including CNC turning, milling, and grinding. They produce custom machined parts for industries like aerospace, defense, and medical.
4. **Ningbo Tengxiang Precision Machinery Co., Ltd.**
Tengxiang Precision Machinery specializes in CNC machining of aluminum, brass, and stainless steel parts. They offer services like drilling, tapping, and surface finishing.
5. **Qingdao Golden-Delta Machinery Co., Ltd.**
Golden-Delta Machinery focuses on CNC milling and turning services for industries such as automotive, aerospace, and electronics. They produce precision machined parts and components.
| Manufacturer | Specialties | Industries Served |
|—————————————–|——————————|——————————-|
| Foxron Precision Metal Parts Co., Ltd. | CNC machining, sheet metal fabrication | Various industries |
| Dongguan Qy Hardware Products Co., Ltd. | Precision machining services | Automotive, medical, electronics |
| Shenzhen Dajin Precision Hardware Co., Ltd. | Precision machining services | Aerospace, defense, medical |
| Ningbo Tengxiang Precision Machinery Co., Ltd. | CNC machining of metal parts | Various industries |
| Qingdao Golden-Delta Machinery Co., Ltd. | CNC milling, turning services | Automotive, aerospace, electronics |
Background Research for machining work manufacturers Companies in China, use qcc.com archive.org importyeti.com
Machining work manufacturers in China offer a wide range of services including CNC machining, precision machining, casting, forging, and fabrication. These companies are known for their high-quality products, competitive pricing, and quick turnaround times. They serve a variety of industries such as automotive, aerospace, electronics, and medical devices.
Qcc.com is a popular online platform that provides information on Chinese companies, including their business scope, production capacity, certifications, and contact details. Users can search for specific machining work manufacturers and access detailed profiles to make informed decisions.
Archive.org is a digital archive that stores historical data from websites, including information about machining work manufacturers in China. Users can access past records to track the company’s performance, changes in products, pricing, and customer reviews over time.
Importyeti.com is a valuable resource for buyers looking to import products from China. It provides data on shipment records, including details of products imported, suppliers, and importers. Users can use this information to identify reliable machining work manufacturers and assess their credibility based on their export history.
By utilizing these platforms, buyers can conduct thorough background research on machining work manufacturers in China, ensuring they select reputable suppliers who can meet their specific requirements and standards.
Leveraging Trade Shows and Expos for machining work Sourcing in China
Trade shows and expos can be highly effective in sourcing machining work in China. These events provide a platform for businesses to showcase their products and services, establish connections, and explore potential partnerships. When leveraged strategically, trade shows and expos can help companies find reliable and high-quality machining suppliers in China.
Attending trade shows and expos allows businesses to interact directly with manufacturers and assess their capabilities. It provides an opportunity to witness demonstrations, examine samples, and discuss specific requirements face-to-face. This direct interaction helps build trust and enables businesses to gain a better understanding of the machining processes and capabilities offered by Chinese suppliers.
Furthermore, trade shows and expos often attract a wide range of suppliers, creating a competitive environment where businesses can compare multiple options to find the best fit for their machining needs. This allows for a comprehensive evaluation of suppliers in terms of quality, cost, delivery time, and after-sales support.
In addition to sourcing potential suppliers, trade shows and expos also provide valuable insights into industry trends, technological advancements, and emerging market opportunities. Attending seminars, workshops, and networking events during these exhibitions can help businesses stay updated on the latest developments in the machining industry, leading to improved decision-making and ultimately, better sourcing outcomes.
To maximize the effectiveness of trade shows and expos, businesses should conduct thorough research beforehand, identify the specific events that focus on machining and manufacturing in China, and target those that align with their sourcing objectives. Prioritize building relationships and collecting relevant information during the shows to make informed decisions when selecting potential suppliers.
In conclusion, trade shows and expos offer a unique opportunity to efficiently and effectively source machining work in China. By leveraging these platforms, businesses can directly interact with suppliers, assess their capabilities, compare options, and gain valuable industry insights. This proactive sourcing approach can lead to successful partnerships and enhanced quality in machining work.
The Role of Agents and Sourcing Companies in Facilitating machining work Purchases from China
Agents and sourcing companies play a crucial role in facilitating machining work purchases from China. They act as intermediaries between foreign buyers and Chinese manufacturers, helping to bridge the gap in language, culture, and business practices. By leveraging their local knowledge and networks, these agents and sourcing companies simplify the entire procurement process and mitigate potential risks.
One of the key roles agents and sourcing companies play is in supplier identification and qualification. They have a deep understanding of the Chinese market and can identify reliable and reputable machining manufacturers that meet the buyer’s specific requirements. This saves time and effort for the buyer who might otherwise struggle to find suitable suppliers on their own.
Once potential suppliers are identified, agents and sourcing companies help in the negotiation and contract process. They facilitate communication between both parties, ensuring that all terms and conditions are clearly understood and agreed upon. Agents also assist in price negotiations, using their knowledge of local market conditions to ensure fair pricing for the buyer.
During production, agents and sourcing companies provide quality control inspections to ensure that the machining work meets the specified standards. They conduct regular inspections at various stages of production and report any issues or deviations to the buyer. This helps to minimize the risk of receiving substandard products and allows for timely corrective actions if needed.
Furthermore, agents and sourcing companies handle logistics and shipping arrangements. They liaise with freight forwarders and customs agents to ensure proper documentation and smooth transportation of the purchased machining work. This allows the buyer to focus on their core activities while leaving the complexities of international logistics to the experts.
Overall, agents and sourcing companies play a vital role in facilitating machining work purchases from China. From supplier identification and qualification to negotiation, quality control, and logistics, they provide essential support throughout the procurement process. Their expertise and local knowledge help buyers navigate the challenges of cross-border procurement, ensuring successful and streamlined transactions.
Price Cost Research for machining work manufacturers Companies in China, use temu.com and 1688.com
When looking for machining work manufacturers in China, two popular websites to use are temu.com and 1688.com. These platforms provide a wide range of options for companies seeking machining services at competitive prices.
On Temu.com, users can easily search for machining work manufacturers based on their specific requirements and browse through a variety of suppliers. The platform allows users to compare prices, read reviews from other customers, and communicate directly with suppliers to negotiate pricing and specifications.
1688.com, on the other hand, is a popular Chinese e-commerce platform that connects buyers with manufacturers and wholesalers. Users can search for machining work manufacturers on the platform and view pricing information, specifications, and reviews from other buyers. 1688.com is known for its competitive pricing and large selection of suppliers, making it a popular choice for companies looking to source machining services in China.
When researching pricing for machining work manufacturers on these platforms, it is important to consider factors such as the complexity of the machining work, materials used, production volume, and shipping costs. By carefully comparing prices and evaluating suppliers based on their capabilities and track record, companies can find the best value for their machining needs in China.
Shipping Cost for machining work import from China
When it comes to shipping machining work from China, there are several factors that can affect the overall shipping cost. These factors include the weight and dimensions of the shipment, the shipping method chosen, the delivery location, and any additional services required.
The weight and dimensions of the shipment play a crucial role in determining the shipping cost. Heavier and bulkier shipments generally incur higher shipping fees due to the increased fuel and handling charges. Therefore, it is important to ensure accurate measurements and weight calculations before shipping.
The chosen shipping method can also impact the cost. There are various options available, ranging from air freight and sea freight to express delivery services. Air freight tends to be faster but more expensive, while sea freight is generally cheaper but requires a longer transit time. Express delivery services often offer a balance between speed and cost, making them a popular choice for many businesses.
The delivery location is another crucial factor. Distance, customs regulations, and local tariffs or taxes all influence the shipping cost. Some remote or rural areas may also incur additional fees or require special arrangements, further impacting the overall cost.
Finally, additional services such as packaging, insurance, and customs clearance can also add to the shipping cost. Proper packaging and insurance help protect the goods during transit but may come at an extra cost. Customs clearance fees may vary depending on the complexity of the documentation and any required inspections.
To obtain accurate shipping quotes for machining work imports from China, it is recommended to consult with freight forwarders or shipping companies. They can provide detailed information tailored to specific requirements, ensuring a smooth and cost-effective shipping process.
Compare China and Other machining work Markets: Products Quality and Price,Visible and Hidden Costs
China is known as a major player in the machining work market, but it’s important to compare its products quality and price with other markets. When considering product quality, China has made significant advancements over the years. Many Chinese manufacturers have improved their precision machining capabilities and can now produce high-quality products. However, it is still generally true that products from developed countries such as Japan, Germany, and the United States tend to have superior quality due to their advanced technology, stringent quality control measures, and skilled workforce.
In terms of price, China has gained a reputation for offering competitive prices in the machining work market. This is primarily due to its low labor costs and large-scale production capabilities. Chinese manufacturers can often produce products at a significantly lower cost compared to other markets. However, it is important to note that the price advantage offered by China may not always be sustainable. As labor costs in China rise, the price advantage may diminish, making other markets more competitive.
When comparing visible and hidden costs, China can sometimes present challenges. While the initial product cost may be low, buyers should consider factors such as shipping and logistics costs, import duties, and intellectual property issues, which can increase the overall cost. Additionally, language barriers, time zone differences, and cultural differences can sometimes create communication challenges and affect the efficiency of collaboration with Chinese manufacturers.
Other machining work markets, particularly those in developed countries, often have higher visible costs due to higher labor and production costs. However, they may offer advantages in terms of closer proximity, easier communication, and a better understanding of the target market. These markets also tend to have more robust intellectual property protection and stricter adherence to international standards, which can provide reassurance regarding product quality.
In summary, China’s machining work market has made strides in terms of product quality and offers competitive prices. However, other markets may still offer superior product quality, while potentially having higher visible costs. Buyers must weigh the advantages and disadvantages of each market and consider visible and hidden costs to make informed decisions.
Understanding Pricing and Payment Terms for machining work: A Comparative Guide to Get the Best Deal
When it comes to getting machining work done, understanding pricing and payment terms is crucial to getting the best deal. Here are some key points to consider when comparing quotes from different machining shops:
1. Pricing structure: Different machining shops may have different pricing structures, such as hourly rates, flat fees, or a combination of both. Make sure to clarify how the pricing is determined so you can accurately compare quotes.
2. Additional fees: Some machining shops may charge additional fees for rush orders, setup costs, or material handling. Be sure to ask about any extra charges to avoid any surprises on your final bill.
3. Payment terms: Payment terms can vary from shop to shop, with some requiring payment upfront or upon completion of the work. Consider your cash flow and budget when negotiating payment terms to ensure a smooth transaction.
4. Volume discounts: If you have a large volume of work to be done, ask about volume discounts. Some machining shops may offer discounted rates for larger orders, so it’s worth inquiring about potential savings.
5. Quality of work: While pricing is important, don’t forget to consider the quality of work that each machining shop provides. Cheaper may not always mean better, so make sure to weigh the cost with the level of craftsmanship and precision offered.
By understanding pricing and payment terms for machining work, you can compare quotes effectively and ultimately secure the best deal for your project. Be sure to communicate openly with machining shops to negotiate terms that work for both parties and ensure a successful partnership.
Chinese Regulations and Industry Standards Certifications for machining work,Import Regulations and Customs for machining work from China
China has developed a comprehensive set of regulations and industry standards certifications for machining work. These regulations and certifications ensure the quality, safety, and compliance of machining work in various industries. The following are some of the key regulations and certifications applicable to machining work in China:
1. GB/T 6414-1999: This is the general specification for machining parts that covers the definitions, materials, dimensions, tolerances, surface quality, and marking requirements.
2. ISO 9001: This certification focuses on quality management systems and ensures that an organization can meet customer and regulatory requirements related to machining work.
3. ISO 14001: This certification emphasizes environmental management systems and ensures that an organization complies with environmental regulations and minimizes its environmental impact during machining processes.
4. GB/T 6418-2006: This standard specifies the technical requirements for the precision machining of mechanical parts, including tolerances, surface roughness, materials, and hardness.
5. GB/T 1804-2000: This standard outlines the tolerances for linear and angular dimensions for machining work, ensuring the precision and accuracy of machined parts.
When importing machining work from China, it is crucial to understand the import regulations and customs procedures involved. The following are some key points to consider:
1. Tariffs and Duties: Importing machining work from China might attract customs duties, which vary depending on the product category. It is essential to consult the local customs authorities or import/export agents to determine the applicable duties.
2. Import Licenses: Some machined parts may require specific import licenses or permits. Importers should ensure compliance with these requirements before proceeding with the importation.
3. Customs Declaration: Importers are required to provide accurate and complete customs declarations, including details of the imported machining work, such as quantity, value, and specifications. Customs authorities may inspect the goods to verify the information provided.
4. Product Compliance: Imported machining work should comply with the applicable safety, quality, and industry standards in the destination country. Importers may need to obtain additional certifications or pass product inspections to ensure compliance.
In conclusion, China has established regulations and industry standards certifications to ensure the quality and compliance of machining work. When importing machining work from China, it is essential to understand the applicable import regulations, customs procedures, and product compliance requirements to facilitate a smooth import process.
Sustainability and Environmental Considerations in machining work Manufacturing
In today’s world, sustainability and environmental considerations are becoming increasingly important in the manufacturing industry, including machining work. The machining process involves cutting, shaping, and finishing materials such as metals, plastics, and composites to create various products and components. However, this process can have a significant environmental impact if not managed properly.
One way to promote sustainability in machining work is to optimize the use of materials. This can be achieved by reducing waste and scrap materials through accurate cutting and machining techniques. Utilizing computer numerical control (CNC) machines can help optimize cutting paths and minimize material waste. Additionally, using recyclable materials and promoting material reuse can further reduce the environmental impact of machining work.
Another important consideration for sustainability in machining work is energy efficiency. Machining processes are typically energy-intensive, with machines consuming a significant amount of power during operation. Implementing energy-efficient practices, such as using energy-efficient equipment and optimizing machining parameters, can help reduce energy consumption and lower carbon emissions.
Furthermore, managing the disposal of hazardous chemicals and waste generated during machining work is critical for environmental sustainability. Implementing proper waste management practices, such as recycling coolant fluids and properly disposing of metal shavings and other waste materials, can minimize environmental pollution and promote a cleaner working environment.
Overall, promoting sustainability in machining work requires a holistic approach that considers the entire manufacturing process, from material selection and waste reduction to energy efficiency and waste management. By implementing sustainable practices in machining work, manufacturers can reduce their environmental footprint, lower operating costs, and contribute to a more sustainable future.
List The Evolution history of “machining work”
The history of machining work can be traced back to ancient times when primitive tools like stones and bones were used to cut and shape materials. The next significant leap in the evolution of machining work occurred during the Bronze Age, around 3000 BCE, when humans began utilizing metal tools made of copper and bronze. These early machining tools, such as chisels, saws, and drills, allowed for more precise shaping and cutting of materials like wood and stone.
The next major advancement came with the discovery of iron around 1200 BCE, leading to the development of iron tools. Iron tools were stronger and more durable, enabling the machining of tougher materials. This period also witnessed the emergence of basic lathe machines, which were operated manually and primarily used for turning operations.
Fast forward to the Industrial Revolution in the 18th century, and machining work experienced a significant transformation. The invention of power-driven machinery, such as steam engines and waterwheels, revolutionized machining capabilities. This facilitated the development of more sophisticated machines like lathes, milling machines, and planers. These machines enabled the mass production of interchangeable parts, contributing to the rise of the modern manufacturing industry.
The 19th century saw the introduction of the first automatic screw machine, invented by Christopher Spencer in 1872. This revolutionary machine allowed for continuous, high-speed production of screw threads, vastly improving efficiency and productivity.
The 20th century brought about further advancements in machining work. The introduction of computer numerical control (CNC) in the 1950s and 1960s marked a turning point in machining technology. CNC machines replaced manually operated machines, allowing for more precise and automated machining processes. This led to increased productivity, reduced human error, and facilitated the production of complex parts with intricate designs.
Today, machining work continues to evolve with the integration of technologies like robotics, additive manufacturing (3D printing), and advanced computer-aided design and computer-aided manufacturing (CAD/CAM) systems. These advancements have further enhanced the accuracy, speed, and versatility of machining processes, opening up new possibilities for industries ranging from aerospace and automotive to healthcare and electronics.
In conclusion, the history of machining work has seen a continuous evolution from primitive tools to the sophisticated machinery and automation we have today. The quest for more efficient, precise, and versatile machining methods continues to shape the future of manufacturing.
The Evolution and Market Trends in machining work Industry
The machining work industry has evolved significantly over the years, with advancements in technology and automation leading to increased efficiency and precision in the manufacturing process. CNC machining has become the industry standard, allowing for complex designs and high-volume production at a faster rate than ever before.
Market trends in the machining work industry show a growing demand for customized and high-precision components across various sectors such as automotive, aerospace, and medical devices. As industries continue to prioritize innovation and efficiency, machining work companies must adapt by investing in the latest technology and software to meet these demands.
Additionally, sustainability and environmental concerns are becoming increasingly important in the machining work industry. Companies are focusing on reducing waste, energy consumption, and harmful emissions to ensure a more sustainable manufacturing process. This has led to the development of eco-friendly machining techniques and materials, further shaping the future of the industry.
Globalization has also had a significant impact on the machining work industry, with companies facing increased competition from international markets. To stay competitive, companies are embracing new technologies such as IoT and data analytics to optimize their production processes and reduce costs.
In conclusion, the machining work industry is continuously evolving to meet the demands of a rapidly changing market. Companies that stay ahead of the curve by investing in technology, sustainability, and innovation will be best positioned to succeed in this dynamic industry.
Custom Private Labeling and Branding Opportunities with Chinese machining work Manufacturers
Chinese machining work manufacturers offer great opportunities for custom private labeling and branding for businesses. With their expertise, advanced technology, and cost-effective production capabilities, these manufacturers are able to meet the tailored needs of various industries.
Custom private labeling allows businesses to have their own brand name, logo, and design on the products they sell. This helps build brand recognition, customer loyalty, and a distinct market presence. Chinese machining work manufacturers can facilitate this process by integrating custom labeling and branding options into their production lines. They can create products with unique designs, colors, and packaging that align with the brand identity of the business.
One advantage of working with Chinese manufacturers for private labeling and branding is their ability to offer cost-effective solutions. They have access to a wide range of materials, technologies, and machinery, enabling them to produce high-quality products at competitive prices. This allows businesses to maintain profitability while building their brand image.
Additionally, Chinese machining work manufacturers often have extensive experience in international trade and understand the specific requirements and regulations of different markets. They can help businesses navigate through these complexities, ensuring compliance and smooth delivery of custom-labeled products worldwide.
Furthermore, China’s manufacturing sector has embraced digitalization and automation, resulting in increased efficiency and shorter lead times. This enables businesses to quickly fulfill custom orders, reducing time-to-market and improving customer satisfaction.
In conclusion, Chinese machining work manufacturers offer excellent opportunities for businesses looking to enhance their branding through private labeling. Their expertise, cost-effective production capabilities, and knowledge of international trade make them ideal partners for businesses seeking custom solutions. With their help, businesses can build a strong brand identity, establish market presence, and achieve success in the competitive global market.
Tips for Procurement and Considerations when Purchasing machining work
When purchasing machining work, there are several important considerations to keep in mind to ensure you get high-quality service and value for your money. Here are some tips to help you make informed decisions when procuring machining services:
1. Define your requirements: Clearly outline your machining needs, including the type of parts or components you need to be produced, desired tolerances and finishes, and any specific materials or processes required.
2. Research potential suppliers: Look for reputable machining companies with a track record of delivering quality work within budget and on time. Consider factors such as experience, certifications, and customer reviews when selecting a supplier.
3. Request quotes: Obtain multiple quotes from different machining suppliers to compare pricing and capabilities. Be sure to provide detailed drawings or specifications to ensure accurate quotes.
4. Evaluate quality control measures: Inquire about the supplier’s quality control processes to ensure the finished products meet your specifications and standards. Ask about inspection equipment, certifications, and quality guarantees.
5. Consider lead times and capacity: Determine the supplier’s production capabilities and lead times to ensure they can meet your project timeline. Consider factors such as equipment availability, capacity, and manpower when making your decision.
6. Communication and flexibility: Choose a machining supplier that communicates effectively, is responsive to your inquiries, and is willing to accommodate changes or modifications to your project if needed.
By following these tips and considerations, you can make an informed decision when purchasing machining work and ensure you receive high-quality products that meet your specifications and requirements.
FAQs on Sourcing and Manufacturing machining work in China
Q: Why should I consider sourcing and manufacturing machining work in China?
A: There are several reasons to consider sourcing and manufacturing machining work in China. Firstly, China has a well-established manufacturing industry with a vast number of experienced and skilled machinists. This ensures high-quality work at lower labor costs compared to many other countries. Moreover, China has a large supply chain network, which means that sourcing raw materials and components for machining projects is usually convenient and cost-effective. Additionally, with advancements in communication and logistics, collaborating with Chinese manufacturers has become easier, making it feasible to oversee the production process effectively.
Q: What are the potential cost savings when manufacturing machining work in China?
A: One of the main advantages of sourcing and manufacturing machining work in China is the potential cost savings. Labor costs in China are generally lower compared to many other countries, resulting in significant savings on machining projects. Additionally, raw materials and components can often be sourced at lower prices due to China’s extensive supply chain network. However, it is crucial to consider other factors such as shipping and import duties, which may affect overall costs.
Q: How can I find reliable machining manufacturers in China?
A: Finding reliable machining manufacturers in China involves thorough research and due diligence. One approach is to utilize online platforms and directories that provide a list of verified manufacturers. You can also attend trade shows and exhibitions dedicated to the machining industry to meet potential suppliers face-to-face and assess their capabilities. Additionally, seeking recommendations from industry associations or professionals who have previously sourced from China can provide valuable insights and help identify reliable manufacturers.
Q: What should I consider when selecting a machining manufacturer in China?
A: When selecting a machining manufacturer in China, several factors should be considered. These include the manufacturer’s experience and expertise in machining, the quality control measures they have in place, their production capacity and lead times, their ability to communicate effectively in English or your desired language, and their willingness to provide samples or references. Additionally, it is essential to consider the manufacturer’s certifications and compliance with relevant quality standards, as well as their ability to meet your specific requirements regarding materials, tolerances, and finishing.
Q: How can I effectively communicate my requirements and ensure product quality when manufacturing in China?
A: Effective communication is crucial when manufacturing machining work in China. To ensure your requirements are well understood, it is advisable to provide detailed engineering drawings, specifications, and any specific instructions. Clear and concise communication is essential to avoid misunderstandings and potential rework. Regular communication channels, such as emails and video conferences, should be established to address any concerns or provide clarifications throughout the production process. Additionally, implementing quality control measures and inspections at different stages of manufacturing can help ensure the desired product quality.
Why contact sourcifychina.com get free quota from reliable machining work suppliers?
Sourcifychina.com offers a convenient and efficient sourcing platform for businesses looking for reliable machining work suppliers in China. By contacting Sourcifychina.com, companies can easily request a free quota from a curated list of trusted and experienced machining suppliers.
The benefit of utilizing Sourcifychina.com is that it streamlines the process of finding the right supplier for your machining work needs. With just a few simple steps, companies can submit their project requirements and receive competitive quotes from pre-vetted suppliers. This saves time and effort in the supplier selection process, ensuring that you are connected with reputable suppliers that can meet your specific machining requirements.
Sourcifychina.com’s network of reliable suppliers is carefully screened to ensure high-quality service and products. By requesting a free quota through Sourcifychina.com, companies can access a pool of trusted machining suppliers that have been thoroughly vetted for their capabilities, reliability, and quality standards.
Overall, contacting Sourcifychina.com for a free quota from reliable machining work suppliers offers businesses a convenient and effective way to connect with top-quality suppliers in China. This streamlined sourcing process can help save time, reduce costs, and ensure that your machining work is completed to the highest standards.