Introduce about material manufacturing guide,Qulity,Cost,Supplier,Certification,Market,Tips,FAQ
The material manufacturing guide is a comprehensive resource that provides essential information on various aspects related to material manufacturing. This guide covers topics such as quality, cost, suppliers, certifications, market trends, tips, frequently asked questions, and more.
Quality is a crucial factor in material manufacturing as it determines the performance and durability of the end product. The guide provides insights into various quality control processes and techniques to ensure that the materials meet the desired standards.
Cost plays a significant role in material manufacturing decisions. The guide offers valuable information on cost analysis, budgeting, and cost-saving strategies. It also highlights factors that can influence material costs, such as raw material prices, production volume, and labor expenses.
Finding reliable suppliers is essential for successful material manufacturing. The guide provides guidelines on selecting suppliers based on factors like reliability, reputation, production capacity, and cost-effectiveness. It also offers insights on establishing and maintaining good relationships with suppliers.
Certifications are essential to comply with quality and safety standards. The guide showcases various certifications relevant to different industries, such as ISO, UL, FDA, and RoHS. It helps manufacturers understand the certification requirements and guide them through the certification process.
Understanding market trends is crucial to stay competitive in the material manufacturing industry. The guide provides insights into market analysis, emerging technologies, and changing consumer preferences. This information can help manufacturers adapt their strategies and develop innovative materials to meet market demand.
In addition to the aforementioned topics, the guide also offers tips and best practices for material manufacturing, including process optimization, waste reduction, and sustainability initiatives. It also includes a frequently asked questions section to address common queries and concerns.
Overall, the material manufacturing guide serves as a valuable resource for manufacturers, enabling them to make informed decisions, enhance product quality, control costs, find reliable suppliers, comply with certifications, stay updated with market trends, and optimize their manufacturing processes.
Types of material manufacturing
Material manufacturing is a crucial process in the production of various goods and products. It involves transforming raw materials into finished materials suitable for use in construction, electronics, automotive, and other industries. There are several types of material manufacturing, each with its unique methods and characteristics.
1. Metal Manufacturing: Metal manufacturing involves the shaping and forming of various metallic materials like steel, aluminum, and copper. Processes such as casting, forging, stamping, and welding are employed to produce a wide range of metal components and structures, including car parts, machinery, and construction materials.
2. Plastic Manufacturing: Plastic manufacturing refers to the production of plastic products through processes like injection molding, extrusion, blow molding, and thermoforming. These methods are used to create a wide range of consumer and industrial products, from packaging materials and furniture to medical equipment and automotive components.
3. Composite Manufacturing: Composite materials are formed by combining two or more materials to create a new material with enhanced properties. They often consist of a reinforcement material, such as fiberglass or carbon fiber, embedded in a matrix material, such as epoxy resin. Composite manufacturing methods include lay-up, filament winding, compression molding, and pultrusion. Composite materials find applications in aerospace, construction, and sporting goods.
4. Ceramic Manufacturing: Ceramic manufacturing involves shaping and firing clay-based materials at high temperatures to produce a wide range of products such as pottery, tiles, and refractory materials. Techniques include slip casting, pressing, and extrusion. Ceramics are known for their high strength, heat resistance, and electrical insulation properties.
5. Glass Manufacturing: Glass manufacturing consists of melting and shaping silica-based materials, often with the addition of other oxides, to produce various types of glass products, including windows, bottles, and optical fibers. Techniques include blowing, rolling, and pressing. Glass materials possess properties such as transparency, hardness, and resistance to chemical corrosion.
6. Textile Manufacturing: Textile manufacturing encompasses processes like spinning, weaving, knitting, and dyeing to produce fabrics from natural or synthetic fibers. Textiles are used in clothing, home furnishings, and industrial applications such as filtration and reinforcement materials.
These are just a few of the many types of material manufacturing processes. Each method has specific advantages and limitations, allowing for the production of diverse materials to meet the needs of various industries.
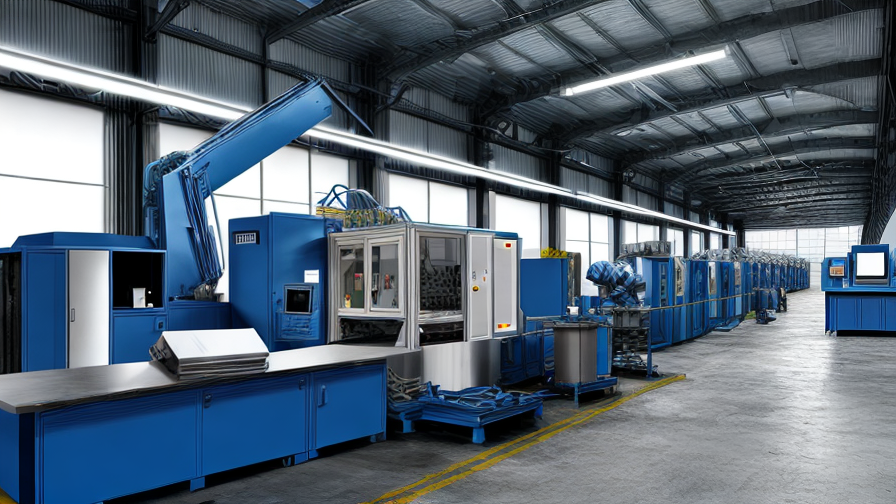
Pros and Cons of Using material manufacturing
Material manufacturing refers to the process of creating various materials, such as metals, plastics, ceramics, and composites, for a wide range of applications. Like any other manufacturing process, it has its pros and cons. Here are some important aspects to consider:
Pros:
1. Precision and consistency: Material manufacturing allows for the precise control of material properties, dimensions, and quality. Manufacturers can create materials with specific characteristics to meet the desired requirements, ensuring uniformity and consistency in the final product.
2. Customization: With material manufacturing, it is possible to create materials tailored to specific applications. This flexibility enables the production of materials with unique properties, allowing for customization based on the specific needs of different industries and products.
3. Efficiency and cost-effectiveness: Material manufacturing technologies have advanced significantly, leading to improved efficiency and reduced costs. Mass production techniques, such as injection molding and extrusion, enable large-scale production of materials, resulting in economies of scale and lower production costs.
4. Enhanced performance: Material manufacturing processes can enhance the properties of materials, making them stronger, more durable, and resistant to wear and tear. Through advanced techniques like heat treatment, alloying, and surface treatments, manufacturers can improve material performance beyond what is naturally available.
Cons:
1. Environmental impact: Material manufacturing can have a significant environmental footprint. The extraction of raw materials, energy consumption, waste generation, and emissions associated with various manufacturing processes can contribute to environmental degradation and climate change.
2. High initial investment: Setting up material manufacturing facilities often requires substantial capital investment in machinery, equipment, and infrastructure. This can pose a barrier to entry for small-scale manufacturers and startups.
3. Waste generation: The manufacturing process can generate significant amounts of waste, such as excess material, scrap, and toxic byproducts. Proper disposal and management of these wastes are essential to minimize environmental impact.
4. Dependency on non-renewable resources: Many material manufacturing processes rely on non-renewable resources, such as fossil fuels and minerals. In the long run, this dependency can pose challenges as these resources become scarcer or more costly.
In conclusion, material manufacturing offers numerous advantages, such as precision, customization, efficiency, and improved performance. However, it also presents significant challenges in terms of environmental impact, initial investment, waste generation, and resource dependency. By considering these pros and cons, manufacturers can make informed decisions and strive for more sustainable production practices.
material manufacturing Reference Specifications (varies for different product)
Material manufacturing reference specifications can vary depending on the specific product being manufactured. These specifications outline the required characteristics and properties of the materials used in the manufacturing process. Here is a general overview of the reference specifications for material manufacturing:
1. Material Type: The reference specifications specify the desired material type for the product. This can include metals, polymers, ceramics, composites, or any other specific material category.
2. Material Composition: The reference specifications outline the required composition of the material. This includes the ratios and percentages of different elements or components that need to be present in the material.
3. Physical Properties: The reference specifications define the physical properties that the manufactured material should possess. This includes properties like tensile strength, hardness, flexibility, conductivity, density, and thermal resistance.
4. Chemical Resistance: The reference specifications may include requirements for the material’s resistance to chemicals, including acids, alkalis, solvents, or specific substances the product is expected to encounter.
5. Surface Finish: The reference specifications may specify the desired surface finish of the material, such as smooth, textured, or specific roughness values, depending on the application requirements.
6. Dimensions and Tolerances: The reference specifications define the required dimensions and tolerances for the material. This includes specifications for length, width, thickness, diameter, or any other relevant dimensions.
7. Testing Standards: The reference specifications may include references to specific testing standards that need to be followed to evaluate the material’s properties. These standards can be specific to the industry or product type and ensure consistent quality control.
8. Environmental Considerations: The reference specifications may also include guidelines for the material’s sustainability and environmental impact. This can involve using recyclable or biodegradable materials or complying with certain environmental regulations.
It is important to note that these reference specifications can vary significantly depending on the specific product and industry. Manufacturers should carefully review and adhere to the relevant specifications to ensure the production of high-quality materials that meet the desired product requirements.
Applications of material manufacturing
Material manufacturing refers to the process of creating materials or products from various raw materials. This process provides numerous applications across various industries, enhancing various aspects of our lives. Here are some key applications of material manufacturing:
1. Automotive industry: Material manufacturing plays a crucial role in the automotive sector, enabling the production of lightweight materials like aluminum, carbon fiber, and advanced composites. These materials improve fuel efficiency, reduce emissions, and enhance vehicle safety. Additionally, material manufacturing techniques such as 3D printing enable the production of complex automotive parts with higher precision and efficiency.
2. Aerospace industry: The aerospace sector relies heavily on material manufacturing for developing lightweight, high-strength materials that can withstand extreme conditions. This includes the production of advanced alloys, composite materials, and additive manufacturing techniques. These materials reduce aircraft weight, increase fuel efficiency, enhance maneuverability, and improve overall performance.
3. Medical industry: Material manufacturing has revolutionized the medical field by enabling the production of artificial organs, prosthetics, implants, and medical devices. Advanced materials like biocompatible polymers and biomaterials offer better compatibility with the human body, improving patient outcomes. Additionally, 3D printing allows customization and rapid production of patient-specific medical devices, leading to personalized treatments and faster recovery times.
4. Electronics industry: Material manufacturing has greatly influenced the electronics industry, with applications ranging from semiconductors and batteries to flexible electronics. The development of new materials, such as graphene, has improved the efficiency and performance of electronic devices. Material manufacturing also facilitates miniaturization and integration of electronic components, enabling the production of smaller, more powerful devices.
5. Construction industry: Material manufacturing offers innovative solutions in the construction sector, including the production of high-performance concrete, lightweight insulation materials, and advanced coatings. These materials improve structural integrity, energy efficiency, durability, and sustainability of buildings. Additionally, additive manufacturing techniques like 3D printing allow for the construction of complex structures with reduced waste and faster construction times.
6. Energy sector: Material manufacturing has applications in renewable energy technologies such as solar panels and wind turbines. Advanced materials improve energy conversion efficiency, durability, and reduce production costs. Additionally, material manufacturing techniques enable the development of energy storage systems like lithium-ion batteries, improving the integration of renewable energy into the grid.
In conclusion, material manufacturing plays a vital role in various industries, leading to advancements in automotive, aerospace, medical, electronics, construction, and energy sectors. The continuous development of new materials and manufacturing techniques will drive further innovations, enhancing the overall quality of our daily lives.
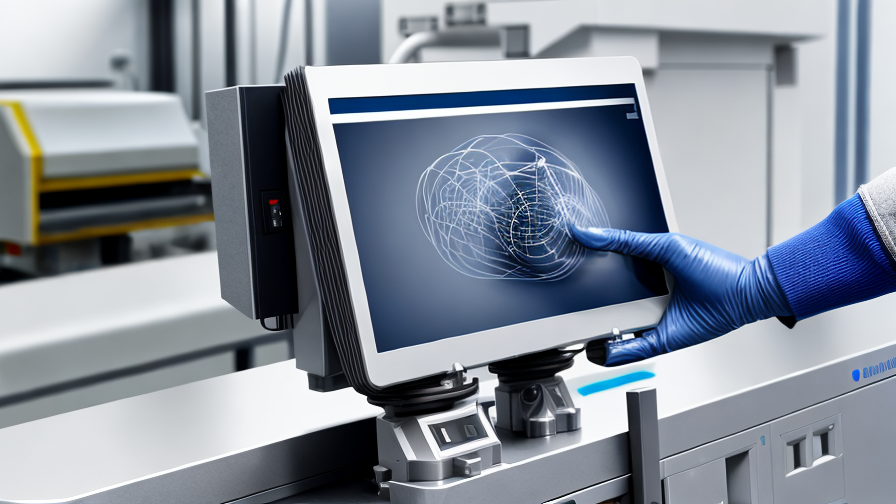
The Work Process and how to use material manufacturing
Material manufacturing is a complex process that involves various steps and techniques to create different types of materials. The work process typically starts with the selection of raw materials, which can range from metals and polymers to ceramics and composites. These raw materials are chosen based on their desired properties and application requirements.
Once the raw materials are selected, they are processed in various ways to form the desired shape and structure. This can involve heating, melting, mixing, or forming the materials through casting, extrusion, or molding processes. The specific method used depends on the material type and the desired final product.
After the initial processing, the materials may undergo additional treatment steps, such as heat treatment, surface finishing, or coating, to enhance their properties or improve their performance. Quality control measures are implemented throughout the manufacturing process to ensure that the materials meet the required specifications and standards.
Once the materials are manufactured, they can be used in various applications across industries such as automotive, aerospace, construction, electronics, and healthcare, among others. For example, metals can be used to make structural components, polymers for packaging materials, and ceramics for electronic substrates.
To effectively use material manufacturing, it is essential to understand the properties and characteristics of the chosen materials and match them to the desired application requirements. This involves considering factors such as strength, durability, corrosion resistance, electrical conductivity, thermal conductivity, and cost.
Furthermore, it is important to follow proper design guidelines and consider factors such as load-bearing capacity, environmental conditions, and manufacturing constraints. Collaborating with material engineers and manufacturers can help ensure that the chosen materials are suitable for the intended application and optimize the manufacturing process.
Overall, material manufacturing is a crucial aspect of product development and plays a significant role in determining the performance, reliability, and lifespan of the final product. By understanding the work process and effectively utilizing material manufacturing techniques, manufacturers can produce high-quality products that meet customer needs and industry standards.
Quality Testing Methods for material manufacturing and how to control the quality
Quality testing in material manufacturing is crucial to ensure that products meet the required standards and specifications. Various testing methods are employed to control quality throughout the manufacturing process.
1. Visual Inspection: Visual examination of materials is the simplest and most widely used method for quality control. It involves inspecting materials for defects, surface imperfections, color inconsistencies, and other visual abnormalities.
2. Mechanical Testing: Mechanical tests evaluate the physical properties of materials, such as strength, hardness, toughness, elasticity, and fatigue resistance. Examples of mechanical tests include tensile, compressive, impact, and hardness testing.
3. Chemical Analysis: Chemical analysis involves determining the elemental and chemical composition of materials. Techniques such as spectroscopy, chromatography, and mass spectrometry are employed to assess the presence of impurities, contaminants, and trace elements.
4. Non-Destructive Testing (NDT): NDT techniques assess material properties and detect defects without damaging the sample. Common NDT methods include ultrasound, X-ray, magnetic particle inspection, eddy current testing, and thermography.
5. Dimensional Inspection: Ensuring accurate dimensions and tolerances is essential in material manufacturing. Dimensional inspection techniques employ precision measurement tools, such as calipers, micrometers, coordinate measuring machines (CMM), or laser scanners.
6. Environmental Testing: Environmental testing assesses material performance under various environmental conditions, including temperature, humidity, corrosion, and UV exposure. These tests evaluate durability, stability, and resistance to environmental factors.
To control quality effectively, manufacturing companies employ several measures:
1. Quality Management Systems: Implementing a robust quality management system, following industry standards like ISO 9001, ensures consistent quality control across all manufacturing processes.
2. Statistical Process Control (SPC): SPC involves studying process variation through data analysis to track trends and identify potential issues. By monitoring key quality indicators, manufacturers can take corrective actions promptly.
3. Supplier Evaluation: Assessing and selecting reliable suppliers is crucial to ensure consistent material quality. Conducting audits, performance reviews, and quality assessments helps identify and collaborate with trustworthy suppliers.
4. Standard Operating Procedures (SOPs): Clearly defined SOPs outline manufacturing processes and quality test procedures, ensuring uniformity and consistency in production.
5. Continuous Improvement: Regularly reviewing and evaluating quality control processes, identifying areas for improvement, and implementing corrective actions help enhance product quality over time.
In summary, a combination of visual inspection, mechanical testing, chemical analysis, NDT techniques, dimensional inspection, and environmental testing are employed to maintain quality standards in material manufacturing. Implementing quality management systems, utilizing statistical process control, evaluating suppliers, following SOPs, and embracing continuous improvement principles aids in effectively controlling the quality of materials.
material manufacturing Sample Policy and Post-Purchase Considerations for material manufacturing from China
Policy:
1. Quality Assurance: Before placing an order with a material manufacturing supplier in China, it is important to establish their quality assurance policies. Ensure that they follow strict quality control standards and have processes in place to address any defects or discrepancies in the delivered materials. Request samples and conduct independent testing if necessary.
2. Environmental Standards: Verify that the material manufacturer complies with international environmental standards and regulations. This includes proper waste management, use of eco-friendly materials, and adherence to sustainable manufacturing practices. Request relevant certifications such as ISO 14001.
3. Ethical Manufacturing: Choose suppliers who demonstrate commitment to ethical manufacturing practices. Ensure that they follow fair labor standards, provide safe working conditions, and do not engage in child labor. Inquire about certifications like Social Accountability International’s SA8000.
4. Intellectual Property Protection: Protect your intellectual property rights by working with material manufacturers who respect intellectual property laws and have effective measures in place to prevent unauthorized use or distribution of your designs or technology.
5. Communication and Transparency: Establish clear lines of communication with the material manufacturer to address any queries, concerns, or updates. Request regular updates on the progress of the manufacturing process and be transparent about your expectations and requirements.
Post-Purchase Considerations:
1. Quality Inspection: Conduct a thorough inspection of the materials upon delivery to ensure they meet the agreed-upon specifications. Identify any defects or deviations and coordinate with the manufacturer for resolution.
2. Packaging and Shipping: Evaluate the packaging and shipping processes to ensure that the materials are adequately protected and handled to prevent damage during transportation. Provide feedback to the manufacturer if improvements are needed.
3. Supplier Evaluation: After receiving the materials, assess the overall performance of the supplier. Consider factors such as quality, communication, adherence to standards, and compliance with ethical guidelines. Maintain a record of your evaluation to inform future purchasing decisions.
4. Feedback and Collaboration: Provide constructive feedback to the supplier, highlighting areas of improvement and commendation. This fosters a collaborative relationship, encourages continuous improvement, and enhances future business interactions.
5. Managing Inventory: Develop a system to manage inventory effectively. Monitor the quality and durability of the supplied materials over time, and keep track of reorder points to ensure consistent supply.
By implementing these policies and post-purchase considerations, you can establish a reliable and sustainable relationship with material manufacturers from China, ensuring quality materials and efficient supply chains.
Sourcing material manufacturing from China: Opportunities, Risks, and Key Players
Sourcing material manufacturing from China presents both opportunities and risks for businesses. China has a well-established manufacturing sector and is known for its competitive pricing, efficient production capabilities, and vast supplier networks. These factors make it an attractive destination for companies looking to reduce production costs and access a wide range of materials.
One of the main opportunities of sourcing from China is cost savings. Labor costs in China are typically lower compared to many other countries, allowing businesses to manufacture products at a lower cost. Moreover, China has a vast supplier network, providing a wide variety of materials at competitive prices, which can further contribute to cost efficiency.
Another opportunity is the efficiency of production capabilities. China has a robust infrastructure for manufacturing, including advanced factories and technologies. This enables companies to benefit from streamlined and high-quality production processes, leading to faster time to market.
However, there are also risks associated with sourcing material manufacturing from China. One of the major risks is the lack of intellectual property protection. Intellectual property infringement is a common concern, with cases of counterfeiting and infringement being reported. Maintaining strict control over designs, patents, and proprietary information is crucial when engaging in manufacturing partnerships in China.
Quality control is another risk. While China offers a vast supplier network, the quality of products can be inconsistent. It is essential to establish strong relationships with reliable suppliers and conduct thorough quality checks to ensure consistent product quality.
Key players in material manufacturing in China include established manufacturers and trading companies. Some notable players include Foxconn Technology Group, BYD Company, and Huawei Technologies. These companies have strong manufacturing capabilities and diverse product portfolios, making them important players in the material manufacturing sector.
In conclusion, sourcing material manufacturing from China provides opportunities in terms of cost savings and efficient production capabilities. However, businesses need to be aware of the associated risks such as intellectual property infringement and quality control. By carefully selecting reliable partners and implementing stringent control measures, companies can harness the benefits of sourcing material manufacturing from China while mitigating potential risks.
How to find and select reliable material manufacturing manufacturers in China,use google search manufacturers and suppliers
Finding and selecting reliable material manufacturing manufacturers in China can be a daunting task, but with the right approach and a thorough search, it is possible to find trustworthy and high-quality suppliers. One effective method is to utilize Google search and follow these steps:
1. Start by conducting a general search using relevant keywords. Use specific terms related to the material you are looking to manufacture, such as “steel manufacturing manufacturers in China” or “plastic material suppliers in China.”
2. Browse through the search results and visit the websites of various manufacturers. Look for key information like company background, production capabilities, certifications, and customer reviews or testimonials. This will give you an initial impression of their reliability and expertise.
3. Narrow down your list of potential manufacturers by checking if they have a physical address, contact information, and a valid website domain. Reputable manufacturers will have a professional online presence with up-to-date information.
4. Verify the authenticity of the manufacturer by searching for their company name, address, or contact details on reliable platforms like Alibaba, Global Sources, or Made-in-China. These platforms often highlight verified and trusted suppliers.
5. Look for any industry certifications or quality management systems that the manufacturer holds. Certifications like ISO 9001 or ISO 14001 indicate a commitment to quality control and environmental standards.
6. Reach out to a shortlisted few manufacturers and request more detailed information such as product samples, production processes, pricing, and lead times. Prompt and professional responses are a good indicator of a reliable manufacturer.
7. You can also utilize online business directories or trade platforms specific to your industry to find suppliers that are specialized in the material you require.
8. Consider attending trade shows and exhibitions in China, where you can meet potential manufacturers face-to-face, inspect their products, and establish personal connections that enhance trust.
9. Lastly, request references from the manufacturers’ existing clients to gain insights into their reputation, product quality, and reliability.
Remember to conduct thorough due diligence, consider multiple factors, and conduct quality checks before finalizing any manufacturing partnership.
How to check material manufacturing manufacturers website reliable,use google chrome SEOquake check if ranking in top 10M
If you want to verify the reliability of a material manufacturing manufacturer’s website, you can follow these steps using Google Chrome and SEOquake:
1. Install Google Chrome: If you don’t already have it, download and install Google Chrome on your computer. This browser extension is compatible with Chrome.
2. Install SEOquake: Go to the Chrome Web Store and search for the SEOquake extension. Click on “Add to Chrome” and follow the instructions to install it.
3. Open the manufacturer’s website: Visit the website of the material manufacturing manufacturer you want to check for reliability.
4. Run SEOquake: Click on the SEOquake extension icon in the top-right corner of your browser toolbar. A dropdown menu will appear.
5. Set parameters: In the SEOquake dropdown menu, navigate to “Display Parameters” and select “Google PageRank” and “Alexa Rank.” This will help you evaluate the website’s ranking and popularity.
6. Check rankings: After selecting the desired parameters, SEOquake will display information related to the website you are visiting. Look for the website’s Google PageRank and Alexa Rank. A higher PageRank indicates a website’s authority, while a lower Alexa Rank signifies higher popularity.
7. Verify top 10M ranking: If the manufacturer’s website has a Google PageRank within the top 10 million, it suggests a reasonable level of reliability. If it’s not within this range, it might be worth further investigation.
Remember, while SEOquake can provide some insights into a website’s reliability, it’s important to consider other factors such as user reviews, certifications, testimonials, and the manufacturer’s reputation within the industry.
Top 10 material manufacturing manufacturers in China
China is globally recognized as a leading manufacturing hub and is home to numerous material manufacturing manufacturers. Here, we present a list of top 10 material manufacturing companies in China:
1. China Baowu Steel Group Corporation Limited: As the largest steel producer in China, Baowu Steel mainly engages in the production of various steel products including plates, sheets, and coils.
2. Sinopec Group: Sinopec is a prominent chemical and energy company in China, specializing in the production of petrochemical materials, including plastics, rubber, and fibers.
3. China National Building Material Group Corporation (CNBM): CNBM is a state-owned enterprise that focuses on the production of building materials such as cement, glass, and gypsum boards.
4. ChinaMinmetals Corporation: ChinaMinmetals is a major non-ferrous metals and minerals supplier in China, involved in the production of copper, aluminum, zinc, and other metal materials.
5. China Petroleum & Chemical Corporation (Sinopec): Sinopec is one of the largest petroleum and petrochemical companies in China, manufacturing various chemical materials, fertilizers, and plastics.
6. China Northern Rare Earth Group High-Tech Co., Ltd.: This company is a leading manufacturer of rare earth materials used in electronics, magnets, and energy-efficient applications.
7. Anhui Conch Cement Company Limited: As the largest cement producer in China and one of the largest globally, Anhui Conch Cement specializes in the manufacturing of cement and related building materials.
8. China Fiberglass Co., Ltd.: This company is a pioneer in the production of fiberglass and related composite materials for various industries, including construction, aerospace, and automotive.
9. China Minmetals Rare Earth Co., Ltd.: It is a subsidiary of China Minmetals Corporation and is engaged in the mining, processing, and sales of rare earth materials.
10. Pingdingshan Tianan Coal Mining Co., Ltd.: This company is a key producer of coal and related energy materials in China, contributing to the country’s energy sector.
These top 10 material manufacturing manufacturers in China are instrumental in various industries, providing key materials for construction, energy, automotive, and other sectors both in China and globally.
Background Research for material manufacturing manufacturers Companies in China, use qcc.com archive.org importyeti.com
China is known for its vast manufacturing capabilities and has become a hub for material manufacturing. When researching material manufacturing manufacturers in China, several websites can be utilized to gather valuable information.
qcc.com is a Chinese business information search engine that provides detailed company profiles and records. It offers insights into the legal status, registration information, financials, and management of companies. The website also includes contact information and the scope of business activities. By using qcc.com, researchers can obtain a comprehensive overview of material manufacturing manufacturers in China.
archive.org is a widely recognized website that allows users to access archived web pages. It can be utilized to trace the historical data and evolution of companies’ websites over time. This information is particularly valuable when studying the growth and development of material manufacturing manufacturers in China. It can help researchers identify changes in product offerings, company strategies, and market presence, thus providing a detailed historical perspective.
importyeti.com is an online platform that provides data about import and export activities of companies. Researchers can utilize this website to gain insights into the trading activities of material manufacturing manufacturers. It offers information on the types of materials imported and exported, trading partners, and volumes. This data can help researchers understand the global reach of the manufacturers, key markets they serve, and their competitiveness in the international market.
When utilizing these websites, it is important to be concise and focused to gather relevant information within the given limit of 300 words. Researchers can selectively search for specific companies, filter information based on requirements, and extract important details such as company profiles, historical data, and trading activities to get a comprehensive understanding of material manufacturing manufacturers in China.
Leveraging Trade Shows and Expos for material manufacturing Sourcing in China
Trade shows and expos are excellent platforms for businesses looking to source materials for manufacturing in China. These events provide numerous benefits and opportunities for companies in search of reliable and cost-effective suppliers. By effectively leveraging trade shows and expos, businesses can find the right materials suppliers and establish long-term partnerships.
Firstly, trade shows and expos in China gather a wide range of material manufacturers and suppliers under one roof. This concentrated environment allows businesses to explore multiple options and compare different suppliers, saving both time and resources. Exhibitors showcase their products, display samples, and share information about production capabilities, quality control measures, and pricing structures. This enables businesses to directly interact and engage with potential suppliers, leading to informed decision-making.
Additionally, trade shows and expos offer an opportunity to meet face-to-face with suppliers, fostering trust and building relationships. Personal interactions can help businesses assess the credibility and reliability of potential suppliers, in turn reducing the risks associated with sourcing materials from unknown sources. Furthermore, by visiting the exhibitors’ booths, businesses can physically inspect samples, assess the quality of materials, and evaluate production capabilities.
Another advantage of trade shows and expos is the access to industry insights and trends. These events often feature seminars, workshops, and panel discussions where industry experts share their knowledge and expertise. Participating in these educational sessions can provide valuable insights into the latest technological advancements, industry best practices, and emerging market trends, helping businesses make informed decisions when choosing suppliers.
To maximize the benefits of trade shows and expos for material sourcing in China, businesses should come prepared. They should conduct thorough research beforehand to identify the most relevant events and exhibitors. It is crucial to set clear objectives and establish a strategy for identifying potential suppliers and gathering relevant information. Following up with the selected suppliers after the event is also crucial to continue building relationships and successfully negotiate contracts.
In conclusion, trade shows and expos in China offer an effective platform for businesses to source materials for manufacturing. By attending these events, companies can explore multiple suppliers, assess their credibility, inspect samples, and stay updated on industry trends. Leveraging trade shows and expos can significantly streamline the sourcing process and lead to successful partnerships with reliable material manufacturers.
The Role of Agents and Sourcing Companies in Facilitating material manufacturing Purchases from China
Agents and sourcing companies play a crucial role in facilitating material manufacturing purchases from China. As businesses increasingly look for cost-effective solutions and access to high-quality materials, these intermediaries serve as valuable resources to navigate the complexities of the Chinese market.
One of the primary roles of agents and sourcing companies is to serve as a bridge between buyers and manufacturers. They establish strong relationships with reliable manufacturers, conducting thorough due diligence to ensure credibility and quality. By acting as intermediaries, these entities can effectively communicate the buyer’s requirements and specifications to the manufacturer, minimizing misunderstandings and potential errors.
Agents and sourcing companies also provide comprehensive market knowledge and expertise. They possess in-depth understanding of China’s manufacturing landscape, keeping up with industry trends, regulations, and best practices. Leveraging their knowledge, they can help businesses identify suitable manufacturers, negotiate prices, and select the most appropriate manufacturing techniques and materials for their specific needs.
In addition, these intermediaries handle the logistics and supply chain management aspects of the purchasing process. They oversee the timely delivery of materials, arrange for quality inspections, and ensure all legal and regulatory requirements are met. This expertise extends to customs clearance, documentation, and transportation, minimizing potential delays or complications.
Furthermore, agents and sourcing companies mitigate potential risks associated with international trade. They conduct rigorous assessments of manufacturers to verify their legitimacy, reputation, and compliance with international standards. This reduces the likelihood of encountering unscrupulous or non-compliant suppliers. Moreover, they can help businesses overcome language barriers and cultural differences, facilitating effective communication and fostering successful relationships.
Overall, agents and sourcing companies offer invaluable support to businesses seeking to procure materials from China. Their expertise, market knowledge, and established networks streamline the purchasing process, ensuring reliable suppliers, high-quality materials, and efficient logistics. By leveraging their services, businesses can effectively navigate the challenges of sourcing materials from China and maximize the benefits of cost-effective manufacturing solutions.
Price Cost Research for material manufacturing manufacturers Companies in China, use temu.com and 1688.com
When it comes to conducting price cost research for material manufacturing manufacturers in China, two websites that come to mind are temu.com and 1688.com. These platforms provide a wealth of information and resources for individuals and businesses looking to source materials from China.
Temu.com is a popular online platform that specializes in connecting buyers with Chinese manufacturers. It offers a wide range of products, including raw materials for manufacturing, and provides detailed information about each supplier. Users can browse through various categories, compare prices, and even request quotations directly from the suppliers. The website also features user reviews and ratings, allowing potential buyers to gauge the credibility and reliability of the manufacturers.
1688.com, on the other hand, is an online marketplace owned by Alibaba Group, specifically tailored for the domestic Chinese market. This platform primarily caters to wholesalers and bulk buyers and offers competitive prices for a vast array of products, including materials for manufacturing. Users can search for suppliers, view product details, compare prices, and place orders directly through the website. It is essential to note that 1688.com is predominantly in Chinese, which may require the use of translation tools for non-Chinese speakers.
To conduct efficient price cost research using these platforms, it is advisable to follow a structured approach. Begin by identifying the specific materials needed for your manufacturing requirements. Then, search for suppliers on both websites, considering factors such as price, quality, minimum order quantity, and customer reviews. Utilize the search filters and refine the results to narrow down suitable options.
Once potential manufacturers are shortlisted, it is crucial to contact them directly to gather more information, negotiate prices, and clarify any queries. Request for samples, if necessary, to assess the quality of the materials before making bulk orders. It is also advisable to communicate in a clear and concise manner and ensure that all terms and conditions are agreed upon before finalizing the transaction.
In conclusion, temu.com and 1688.com are valuable resources for conducting price cost research when sourcing materials from China. By utilizing these platforms efficiently and comparing multiple suppliers, businesses can achieve optimal pricing while maintaining desired quality standards.
Shipping Cost for material manufacturing import from China
The shipping cost for importing materials for manufacturing from China can vary depending on several factors. These factors include the weight and dimensions of the shipment, the shipping method chosen, the distance between China and the destination country, and any additional services required during the shipping process.
Typically, there are three primary shipping methods for importing goods from China: air freight, sea freight, and courier services. Air freight is generally the fastest option but also the most expensive. Sea freight is more economical for larger shipments but takes longer to arrive. Courier services are convenient for smaller shipments but can be costlier.
To get a better estimate of the shipping cost, it is important to have the accurate weight and dimensions of the shipment. Freight companies typically calculate shipping charges based on the chargeable weight, which can be the actual weight or dimensional weight, depending on which one is higher. Dimensional weight is calculated by multiplying the length, width, and height of the package and then dividing it by a factor determined by the carrier.
Additional services such as insurance, customs clearance, and handling fees should also be taken into account. These services ensure a smooth customs process and secure handling of the goods but may add to the overall shipping cost.
Lastly, the distance between China and the destination country plays a significant role in determining the shipping cost. Generally, longer distances result in higher shipping charges.
In summary, the shipping cost for importing materials for manufacturing from China can range from a few hundred dollars to several thousands, depending on the factors mentioned above. It is essential to consider the weight, dimensions, shipping method, additional services, and distance to get an accurate estimate. Consulting with freight forwarders or shipping companies can provide more specific cost details and help optimize the shipping process.
Compare China and Other material manufacturing Markets: Products Quality and Price,Visible and Hidden Costs
China is the world’s largest manufacturing country and is renowned for its low-cost production capabilities. However, when comparing China to other material manufacturing markets, several factors need to be considered, including product quality and price, visible and hidden costs.
When it comes to product quality and price, China has developed a reputation for offering a wide range of products, from low-cost options to high-quality goods. The country’s manufacturing sector has the ability to cater to various price points based on the desired quality. This flexibility has made China an attractive choice for businesses seeking cost-effective options. However, it is important to note that product quality can vary significantly depending on the manufacturer and specifications provided.
In contrast, other material manufacturing markets, such as Germany or Japan, are known for their focus on high-quality products. These markets have a long-standing reputation for precision engineering and superior craftsmanship. While products from these markets may be pricier, they often offer exceptional performance, durability, and innovation. Businesses that prioritize product quality and are willing to pay a premium may find these markets more suitable.
Moving on to visible and hidden costs, choosing China as a manufacturing partner offers cost advantages due to its low labor and production costs. China’s large-scale production capabilities enable economies of scale, resulting in competitive prices for bulk orders. However, businesses need to carefully assess hidden costs, such as shipping, customs, tariffs, and intellectual property protection. These additional expenses can impact the overall cost advantage, particularly for smaller orders or time-sensitive production.
Other material manufacturing markets may have higher visible costs due to higher labor wages and operational expenses. However, they offer certain advantages in terms of reduced shipping costs for nearby markets, shorter lead times, and more favorable intellectual property protection laws. These factors can potentially offset the higher visible costs and provide a more efficient and secure manufacturing process.
In summary, China is renowned for its low-cost production capabilities, offering a wide range of products at different price points. However, other material manufacturing markets such as Germany or Japan stand out for their focus on high-quality products. When choosing a manufacturing partner, businesses should consider not only product quality and price but also visible and hidden costs associated with each market. Ultimately, the decision should align with the business objectives, priorities, and requirements.
Understanding Pricing and Payment Terms for material manufacturing: A Comparative Guide to Get the Best Deal
Pricing and payment terms are crucial factors to consider when engaging in material manufacturing, as they directly impact the overall cost and profitability of a project. This comparative guide aims to provide valuable insights and strategies for obtaining the best deal.
When negotiating pricing with material manufacturers, it is essential to have a clear understanding of the market rates for the desired materials. Conduct thorough research to determine the average prices and identify any fluctuations in the market that can impact the costs. This knowledge will enable you to negotiate more effectively and identify potential opportunities for cost savings.
Consider obtaining multiple quotes from different manufacturers to compare prices and evaluate their capabilities. While price is an important factor, it should not be the sole determining factor. Assess the quality of the materials, reliability of the manufacturer, and their ability to deliver within the required timeframe before finalizing a deal.
Payment terms also play a crucial role in managing cash flow and ensuring a smooth manufacturing process. Negotiate favorable payment terms that align with your financial capabilities. It is common to negotiate a deposit upon placing an order, with the remaining payment due upon completion or delivery. However, manufacturers may offer discounts for upfront payments or shorter-term payment options. Carefully evaluate these options to determine which best suits your financial situation.
Additionally, consider negotiating credit terms for future orders. Establishing a solid relationship with a manufacturer may facilitate more flexible payment arrangements in subsequent orders. This can help to enhance cash flow and provide financial stability over time.
It is advisable to include penalty clauses in the contract to safeguard against late deliveries or sub-standard materials. Ensure that these clauses are fair and reasonable, providing adequate protection while being mindful of manufacturer circumstances.
Regularly review your pricing and payment terms to reassess their effectiveness and adjust them as necessary. Industry dynamics may change, affecting costs, and manufacturers may adjust their pricing structures. Staying informed and proactive will enable you to secure the best deals in an ever-changing market.
In conclusion, understanding pricing dynamics, comparing quotes, and negotiating favorable payment terms are essential in obtaining the best deal for material manufacturing. By conducting thorough research, fostering relationships with manufacturers, and staying proactive in monitoring market changes, businesses can optimize their cost-efficiency and profitability in material procurement.
Chinese Regulations and Industry Standards Certifications for material manufacturing,Import Regulations and Customs for material manufacturing from China
Chinese Regulations and Industry Standards Certifications for material manufacturing ensure the quality and safety of products exported from China. The Chinese government has implemented various regulations and certifications to maintain high standards in the manufacturing industry.
One of the key certifications is the China Compulsory Certification (CCC) mark. It is a mandatory certification for products in various industries, including material manufacturing. The CCC mark indicates that the products meet the required safety, quality, and environmental standards set by the Chinese government.
In addition to the CCC mark, there are specific industry standards and certifications for different materials. For example, for steel products, the China Steel Structure Association (CSSA) certification ensures that the products meet industry-specific standards. Similarly, for chemical products, the China National Chemical Information Center (CNCIC) provides certifications to ensure compliance with safety and quality requirements.
Importing materials from China also requires compliance with import regulations and customs procedures. Importers need to be aware of the following key aspects:
1. Import Licensing: Some materials may require specific import licenses or permits from the relevant government authorities. Importers must ensure compliance with these requirements to avoid any legal issues.
2. Customs Documentation: Accurate and complete customs documentation is crucial for smooth customs clearance. The necessary documents typically include a commercial invoice, packing list, bill of lading, and customs declaration form.
3. Customs Duties and Taxes: Importing materials into another country may incur customs duties and taxes. Importers should be aware of the applicable rates and ensure timely payment to avoid delays in clearance.
4. Compliance with Import Regulations: Importers should be knowledgeable about the specific import regulations for their materials, such as restrictions or requirements related to safety, quality, labeling, and environmental standards.
To conclude, Chinese Regulations and Industry Standards Certifications play a vital role in ensuring the quality and safety of materials manufactured in China. Importers must also adhere to the relevant import regulations and customs procedures to successfully import materials into their respective countries.
Sustainability and Environmental Considerations in material manufacturing Manufacturing
Sustainability and environmental considerations are becoming increasingly important in material manufacturing as we strive to minimize the negative impact on our planet. The manufacturing industry has a significant role to play in addressing environmental issues, such as reducing greenhouse gas emissions, conserving resources, and minimizing waste generation.
One important aspect of sustainability in material manufacturing is the choice of raw materials used. Manufacturers are now opting for more environmentally friendly materials, such as recycled or biodegradable options, to reduce the extraction of finite resources. Additionally, sustainable materials can be sourced locally, reducing the energy consumed in transportation and supporting local economies.
Another crucial consideration is energy consumption. Manufacturing processes often require substantial amounts of energy, which contribute to greenhouse gas emissions. To address this concern, manufacturers are implementing energy-efficient technologies and practices, such as optimizing equipment and adopting renewable energy sources. By minimizing energy consumption, manufacturers can reduce their carbon footprint and contribute to a more sustainable future.
Waste generation is another significant concern. Traditional manufacturing processes often result in the production of large amounts of waste, including pollutants and non-recyclable materials. However, sustainability-focused manufacturers are implementing strategies like waste reduction, recycling, and reuse to minimize the environmental impact. By employing closed-loop manufacturing systems, where waste materials are recycled back into the production process, manufacturers can reduce their reliance on virgin resources and minimize waste sent to landfills.
Water usage is another critical aspect of sustainability in material manufacturing. Manufacturers are increasingly adopting water-saving technologies and practices, such as water recycling and purification systems, to minimize their impact on freshwater sources. Additionally, manufacturers are exploring alternative water sources, such as rainwater harvesting, to reduce reliance on traditional water supplies.
Furthermore, sustainable manufacturing involves considering the entire lifecycle of a product. This includes designing products that are long-lasting, easily repairable, and recyclable at the end of their life. By prioritizing durability and recyclability, manufacturers can reduce waste and extend the lifespan of products, leading to a more sustainable manufacturing industry.
In conclusion, sustainability and environmental considerations are essential in material manufacturing to minimize the negative impact on the planet. By choosing environmentally friendly materials, optimizing energy consumption, reducing waste generation, and considering product lifecycle, manufacturers can contribute to a more sustainable future. Adopting these practices not only benefits the environment but also creates a positive brand image and attracts environmentally conscious consumers.
List The Evolution history of “material manufacturing”
The evolution of material manufacturing can be traced back to prehistoric times when humans used natural resources such as stone, wood, and bones to fashion tools and weapons. This period is commonly known as the Stone Age, which lasted for thousands of years. During this time, early humans discovered how to shape and manipulate these materials by using simple tools and techniques like chipping, grinding, and polishing.
The next significant advancement in material manufacturing came with the discovery of metalworking around 6000 BCE. Copper was one of the first metals to be used, followed by the more widely available and durable bronze. These advancements allowed for the production of more complex tools and weapons with increased functionality and durability.
The Iron Age, which began around 1200 BCE, marked a remarkable shift in material manufacturing. With the discovery of iron metallurgy, iron tools and weapons became more widely available. This development played a crucial role in the growth of civilizations such as the Roman Empire, which heavily relied on iron for construction, weaponry, and transportation.
Fast-forward to the late 18th century, a new era of material manufacturing began with the Industrial Revolution. This period saw the introduction of mechanized production processes, fueled by the invention of steam power and the development of new machinery. It led to the rise of factories and mass production, enabling the production of textiles, metals, and other materials on a much larger scale.
In the 19th century, the discovery and utilization of new materials like rubber, plastic, and synthetic fibers revolutionized manufacturing once again. Rubber, for example, transformed the transportation industry with the invention of the pneumatic tire, greatly improving comfort and efficiency. Plastics also emerged as a versatile and inexpensive material, leading to a wide range of applications across industries.
The late 20th century witnessed the rise of advanced materials and manufacturing techniques. Nanotechnology, for instance, allowed scientists to manipulate materials at the atomic and molecular level, resulting in the creation of stronger, lighter, and more durable substances like carbon fibers and graphene.
Today, material manufacturing continues to evolve with the advent of 3D printing, also known as additive manufacturing. This cutting-edge technology has the potential to transform various industries by enabling the production of complex and customized objects with reduced waste and faster production times.
In summary, the evolution of material manufacturing started with the use of natural resources in prehistoric times, advanced to metallurgy during the Bronze and Iron Ages, experienced a significant shift during the Industrial Revolution, and continues to progress with the discovery and development of new materials and manufacturing techniques.
The Evolution and Market Trends in material manufacturing Industry
The material manufacturing industry has been evolving rapidly in recent years, driven by advancements in technology and changing market trends. This evolution has had a significant impact on the way materials are produced, leading to increased efficiency and the development of innovative products.
One of the key trends in the material manufacturing industry is the shift towards sustainable and eco-friendly materials. With growing awareness of the environmental impact of traditional manufacturing processes, companies are now focusing on developing materials that are recyclable, bio-degradable, and require less energy to produce. This trend has not only gained popularity among consumers but has also been encouraged by government regulations and incentives, leading to a surge in demand for sustainable materials.
Another market trend in the material manufacturing industry is automation and digitization. Technological advancements such as artificial intelligence, robotics, and data analytics are being increasingly integrated into manufacturing processes to enhance productivity, reduce costs, and improve quality control. Automation allows for faster production times, fewer errors, and the ability to handle complex designs and customization, thereby catering to the evolving needs of customers.
Additionally, the material manufacturing industry has witnessed a rise in the development of advanced materials with enhanced properties. For instance, the demand for lightweight materials has grown significantly, driven by the aerospace and automotive sectors. Advanced composites, such as carbon fiber reinforced polymers (CFRP), are being used extensively in these industries due to their high strength-to-weight ratio. Moreover, materials with superior heat resistance, conductivity, and durability are being increasingly sought after in sectors like electronics and energy.
Furthermore, the adoption of additive manufacturing, also known as 3D printing, has revolutionized the material manufacturing industry. This technology allows for the production of highly complex and customizable parts with reduced waste and lead times. Additive manufacturing is particularly popular in industries such as healthcare, aerospace, and automotive, providing opportunities for cost-effective prototyping, on-demand production, and customization.
In conclusion, the material manufacturing industry has witnessed a significant evolution in recent years, driven by changing market trends and advancements in technology. The industry has embraced sustainable materials, automation, advanced materials, and additive manufacturing, all of which have had a transformative impact on the way materials are produced and utilized. These trends are expected to continue shaping the industry as it strives for greater efficiency, cost-effectiveness, and sustainability.
Custom Private Labeling and Branding Opportunities with Chinese material manufacturing Manufacturers
China is globally renowned as a hub for material manufacturing, offering an array of custom private labeling and branding opportunities. Chinese manufacturers provide a vast range of materials, including textiles, electronics, plastics, and more, making it an ideal choice for businesses looking to create their own unique products.
One significant advantage of partnering with Chinese manufacturers is their ability to offer custom private labeling. Businesses can collaborate with manufacturers to design and create products that embody their brand identity. With the help of advanced production techniques and state-of-the-art equipment, Chinese manufacturers can tailor products to meet specific requirements and ensure brand consistency.
Moreover, Chinese manufacturers offer extensive branding opportunities. Businesses can not only include their logo or brand name on the product but also customize packaging, labels, and tags. This level of customization enhances brand visibility and recognition, helping businesses stand out in a competitive market. Chinese manufacturers are adept at implementing branding elements efficiently, ensuring that products are aligned with the company’s overall marketing strategy.
Additionally, Chinese manufacturers typically have a wide range of materials to choose from, allowing businesses to select the most suitable option for their products. Whether it’s textiles for apparel, plastic for packaging, or electronics for gadgets, Chinese manufacturers have access to an abundant supply of materials to meet diverse industry needs.
Working with Chinese manufacturers also offers cost advantages. China’s manufacturing sector has developed cost-effective solutions for mass production, making it an attractive option for businesses looking to optimize their production costs. Moreover, the scale of manufacturing in China allows for bulk orders, providing economies of scale that further reduce expenses.
In conclusion, partnering with Chinese material manufacturing manufacturers presents an excellent opportunity for businesses seeking custom private labeling and branding. With a wide range of materials, customization options, and cost advantages, China offers a competitive edge in the global market.
Tips for Procurement and Considerations when Purchasing material manufacturing
When it comes to procurement and purchasing of material for manufacturing, there are several considerations that should be taken into account in order to ensure a successful and cost-effective process. Here are some tips and considerations:
1. Define your requirements: Clearly outline the specifications and quality standards for the materials you need. Consider factors such as durability, functionality, and environmental impacts.
2. Supplier selection: Conduct thorough research and evaluate potential suppliers based on their reputation, reliability, quality standards, and pricing. Consider obtaining samples or conducting audits to assess their capabilities.
3. Cost analysis: While price is an important factor, it should not be the sole determinant. Conduct a comprehensive cost analysis that considers factors like transportation costs, lead times, potential risks, and long-term value.
4. Negotiation: Engage in negotiation with suppliers to secure the best possible terms, including prices, delivery schedules, and payment terms. Seek to establish mutually beneficial relationships that promote long-term collaboration.
5. Supply chain visibility: Ensure that your supply chain is transparent, with accurate inventory tracking and real-time visibility. This helps to prevent disruptions and meet production demands effectively.
6. Risk management: Assess and mitigate risks associated with procurement, such as potential supply chain disruptions, quality issues, or reliability concerns. Have contingency plans in place to address any unforeseen circumstances.
7. Sustainability considerations: Incorporate sustainability factors into your procurement strategy. Assess suppliers’ environmental policies, ethical practices, and consider recyclability of materials.
8. Quality control: Implement stringent quality control measures to ensure that the purchased materials meet your specifications and standards. Conduct regular inspections and audits as part of the quality assurance process.
9. Long-term partnerships: Cultivate long-term relationships with your suppliers, which can lead to better pricing, improved collaboration, and increased reliability. Regularly evaluate supplier performance to ensure they continue to meet your needs and expectations.
10. Continuous improvement: Continuously evaluate your procurement process and identify areas for improvement. Monitor market trends, technological advancements, and emerging materials to stay ahead of the competition and enhance your manufacturing process.
By considering these tips and taking a proactive, strategic approach to procurement, businesses can optimize their material purchasing process, reduce costs, and maintain a competitive edge.
FAQs on Sourcing and Manufacturing material manufacturing in China
1. Why do companies choose to source and manufacture materials in China?
Companies often choose to source and manufacture materials in China due to the country’s lower labor costs compared to other countries. China has an abundant and skilled workforce that can produce goods at a lower cost, enabling companies to save on manufacturing expenses. Additionally, the country has well-established industrial areas and infrastructure, allowing for efficient production and transportation.
2. What are the common challenges in sourcing materials from China?
One common challenge in sourcing materials from China is the language barrier. This can cause difficulties in communication, leading to misunderstandings or misinterpretations of requirements. Quality control is another challenge, as there can be variations in product quality. It is crucial for companies to establish quality control procedures and conduct regular inspections to ensure consistent product standards.
3. How can I ensure the quality of materials manufactured in China?
To ensure the quality of materials manufactured in China, companies can undertake the following measures:
– Conduct thorough due diligence on potential suppliers, including their manufacturing facilities, certifications, and quality management systems.
– Implement quality control procedures and specifications that suppliers must adhere to.
– Regularly inspect the manufacturing process and final products to detect any quality issues.
– Establish clear communication channels with suppliers to address any concerns or issues promptly.
4. Are there any legal or regulatory considerations when sourcing materials from China?
Yes, there are legal and regulatory considerations when sourcing materials from China. Companies must ensure compliance with import and export regulations, including customs duties and documentation requirements. It is essential to understand the intellectual property laws and ensure proper protection of proprietary information to avoid counterfeiting or unauthorized use.
5. How long does it take to manufacture materials in China?
The manufacturing timeline in China can vary depending on factors such as the complexity of the product, order quantity, and supplier’s production capacity. While lead times can range from a few weeks to several months, it is advisable to establish a clear production timeline with the supplier to avoid any delays and plan inventory accordingly.
6. How can I find reliable suppliers in China?
Finding reliable suppliers in China can be challenging but not impossible. One effective way is to attend trade shows and exhibitions where Chinese manufacturers showcase their products. Online sourcing platforms and directories can also help identify potential suppliers. Conducting background checks, communicating extensively, and requesting samples or references are crucial steps in assessing a supplier’s reliability.
7. What are the potential risks of manufacturing in China?
Some potential risks of manufacturing in China include intellectual property theft, quality control issues, cultural and communication barriers, and fluctuations in government regulations. These risks can be mitigated through proper due diligence, clear contractual agreements, regular inspections, and establishing strong relationships with trustworthy suppliers.
In conclusion, sourcing and manufacturing materials in China can be beneficial in terms of cost-effectiveness and access to a skilled workforce. However, companies should be aware of potential challenges and risks and take necessary measures to ensure quality, compliance, and reliable sourcing.
Why contact sourcifychina.com get free quota from reliable material manufacturing suppliers?
Sourcifychina.com is a platform that connects businesses with reliable material manufacturing suppliers in China. The website offers a unique feature where businesses can obtain a free quota from these suppliers. There are several reasons for this:
1. Attracting customers: By offering a free quota, Sourcifychina.com aims to attract businesses who are searching for reliable material manufacturing suppliers. This free quota allows businesses to test the services and capabilities of various suppliers without any financial commitment.
2. Building trust: China being a major manufacturing hub, it can be challenging for businesses to identify trustworthy suppliers. Sourcifychina.com’s free quota helps in building trust by allowing businesses to interact with multiple suppliers and evaluate their expertise, product quality, and service before making a long-term commitment.
3. Streamlining the sourcing process: The free quota enables businesses to streamline their sourcing process by easily comparing different suppliers’ offers. It helps them in getting a comprehensive understanding of the prices, lead times, and production capacities of various suppliers in a single platform.
4. Cost-saving opportunity: The free quota offers businesses a cost-saving opportunity as they can obtain quotes from different suppliers without incurring any charges. This allows businesses to negotiate better pricing and terms with the suppliers based on the obtained quotations.
5. Easy access to suppliers: Sourcifychina.com aims to simplify the sourcing process by providing businesses with easy access to a wide network of reliable material manufacturing suppliers. The free quota feature ensures that businesses can connect with these suppliers effortlessly and explore potential partnerships.
In summary, offering a free quota to businesses is a strategic move by Sourcifychina.com to attract, build trust, streamline the sourcing process, offer cost-saving opportunities, and provide easy access to reliable material manufacturing suppliers in China.