Types and Applications of membrane filter
Membrane filters are thin sheets of material with extremely small pore sizes used to separate and concentrate particles or molecules from a liquid or gas. There are several types of membrane filters that are used in various industries, each with their own distinct pore sizes and applications.
Microfiltration membranes are the most common type of membrane filter, with pore sizes ranging from 0.1 to 10 microns. They are primarily used in the food and beverage industry to remove bacteria, yeast, and other microorganisms from liquids such as beer, wine, and juice. They are also used in the pharmaceutical and biotechnology industries to separate cell cultures from their growth media.
Ultrafiltration membranes have smaller pore sizes, ranging from 0.001 to 0.1 microns, and can be used for the separation of proteins, viruses, and other macromolecules from liquids. They are commonly used in the dairy industry to separate milk protein from whey, as well as in the pharmaceutical and biotechnology industries for the separation of antibodies and enzymes.
Nanofiltration membranes have even smaller pore sizes, ranging from 0.001 to 0.01 microns, and are often used to separate salts and other small molecules from water. They are used in desalination plants to produce drinking water from seawater and in the production of semiconductors.
Reverse osmosis membranes are the most advanced type of membrane filter, with extremely small pore sizes ranging from 0.0001 to 0.001 microns. They are used to remove salts, minerals, and other dissolved solids from water, and are commonly used in the production of bottled water, as well as in the food and beverage industry for the concentration of juices and other liquids.
In conclusion, membrane filters play an important role in various industries such as food and beverage, pharmaceutical, biotechnology, and water treatment industries. The choice of the membrane filter depends on the application and the level of separation required.
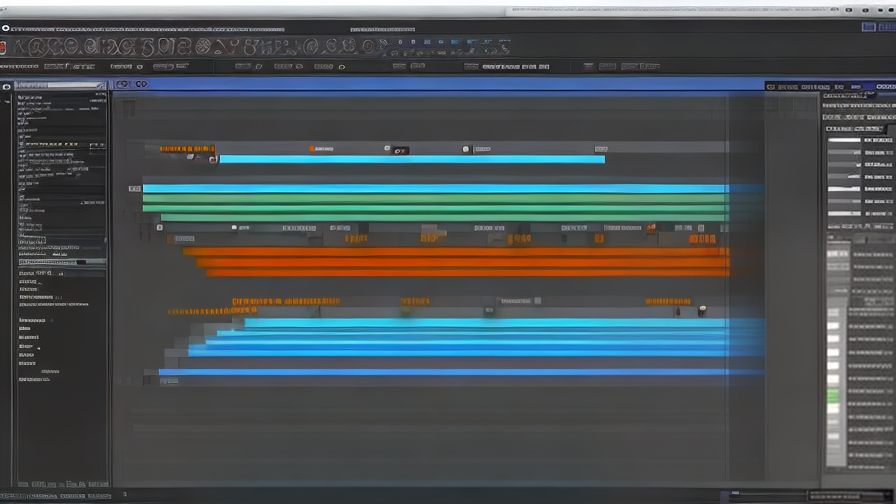
Benefits and Feature of Utilizing membrane filter
Membrane filters are an essential component of many laboratory processes and applications. They are used to filter out particles and microorganisms to produce clean and sterile fluids. Here are some benefits and features of using membrane filters:
1. High Efficiency: Membrane filters are highly efficient in the removal of bacteria, viruses, and other particles. They have pore sizes ranging from 0.1 to 10 microns, which helps to separate the required components from the sample.
2. Precise Separation: Membrane filters can be used to separate different components of a sample based on their size. This allows for selective filtration of desired components, while leaving behind the unwanted particles.
3. Sterilization: Membrane filters are designed for use in sterilization processes. They are capable of retaining microorganisms, thereby ensuring that the filtered output is free of contamination.
4. Reduced Sample Loss: Membrane filters minimize sample loss during filtration. They are designed with narrow pore structures, which prevents the sample from passing through the filter.
5. Easy to Use: Membrane filters are easy to handle and can be used in a variety of laboratory settings. They are available in various formats, such as syringe filters and vacuum filters, making them suitable for a wide range of applications.
6. Cost-effective: Compared to other filtration methods, membrane filters offer a cost-effective solution for particle separation. Their high efficiency means that they can filter large volumes of samples without incurring high costs.
In conclusion, membrane filters are a versatile laboratory tool that offers high efficiency, precise separation, and cost-effective particle filtration. They are ideal for use in sample preparation, sterilization, and other laboratory processes that require particle separation.
The Process of membrane filter
Membrane filtration is a process of removing impurities from liquids or gases using a membrane, which is a semi-permeable material. This process operates based on the size exclusion principle, which involves passing the impure fluid through the membrane that only allows certain substances to pass through and retains others. The membrane filtration process is widely used in industries for several applications, including water treatment, wastewater treatment, food and beverage processing, pharmaceutical manufacturing, and biotechnology.
The membrane filtration process involves several steps, which include pretreatment, filtration, and post-treatment. The pretreatment step involves removing larger impurities from the fluid that could clog the filter and reduce its efficiency. This step could involve settling, sedimentation, coagulation, or flocculation. The next step involves feeding the fluid through the membrane where the impurities are retained while the purified liquid passes through the membrane. This filtration step can be achieved through several methods, including pressure-driven, vacuum-driven, or gravity-driven filtration. The filtered liquid is then collected and further processed or disposed of depending on the application. The post-treatment step involves cleaning and maintaining the membrane to ensure optimal performance for future filtration processes. This step could involve backwashing, chemical cleaning, or replacing the membrane if necessary.
The membrane filtration process offers many advantages over other filtration methods, including low energy consumption, high flow rates, and minimal chemical use. It also provides more efficient removal of impurities than alternative methods. However, the process also has some limitations, such as high capital costs, the need for skilled operators, and the potential for membrane fouling. In conclusion, the membrane filtration process is a highly effective method of removing impurities from liquids and gases, and it is widely used in various industries to achieve high-quality products and meet regulatory standards.

How to use membrane filter
Membrane filters are widely used in various industries including pharmaceuticals, microbiology, food and beverage, and environmental analysis. They are thin and porous films made of various materials like nylon, cellulose acetate, and polycarbonate that are used to separate particles and microorganisms from liquids and gases. The membrane filter is known for its high filtration precision and superior permeability, making it a popular choice for many applications.
The first step in using a membrane filter is to select an appropriate pore size according to the size of the target particle or microbe to be removed. The filter cartridge is then inserted into a filtration device such as a vacuum filtration system or a syringe filter holder. The filtration device is then connected to a vacuum or pressure source, which forces the liquid or gas to be filtered through the membrane pores.
The filtration process can be carried out either by aseptic techniques or non-aseptic techniques. In aseptic techniques, the membrane filter is sterilized before use, and all the filtration procedures should be carried out in a sterile environment or a laminar flow hood. In contrast, non-aseptic techniques could be used when a sterile environment is not critically required.
After filtration, the membrane filter is typically discarded, and the filtrate is collected for further analysis. The membrane filter could also be removed from the filtration device and placed onto an agar plate, which is then incubated to enable the growth of any trapped microorganisms.
In summary, membrane filters are versatile tools that enable the separation of particles and microorganisms from liquids and gases. Proper selection of pore size, choice of suitable filtration device, and appropriate handling of the filter will ensure an effective and successful filtration process.
membrane filter Manufacturer,Supplier and Wholesale
A membrane filter is a device designed to remove impurities and particles from a fluid by passing it through a porous membrane. These filters are used in a variety of industries, including water treatment, food and beverage production, pharmaceuticals, and biotechnology.
As a leading membrane filter manufacturer, supplier, and wholesaler, we specialize in producing high-quality, durable filters that meet the unique needs of our customers. Our filters are made from a variety of materials, including polyamide, PTFE, and cellulose acetate, and are available in a range of sizes and configurations to fit any application.
We pride ourselves on our commitment to quality and customer satisfaction. We use only the highest quality materials and manufacturing techniques to ensure that our filters are reliable and long-lasting. Our experienced team of engineers and technicians work closely with customers to develop customized solutions that meet their unique filtration needs.
In addition to manufacturing and supplying membrane filters, we also offer a range of related services, including filter testing and validation, technical support, and maintenance and repair services. Our goal is to provide our customers with the highest level of service and support possible, and we are committed to working with them to solve any filtration challenges they may face.
Whether you are in need of a single membrane filter or a large-scale filtration system, we have the expertise and resources to provide you with a solution that meets your needs. Contact us today to learn more about our products and services, and to discuss how we can help you meet your filtration needs.

membrane filter Price
Membrane filters are widely used in various industries for their effectiveness in separating particles and contaminants from liquids and gases. The price of membrane filters ranges depending on the material, size, and quantity needed. In general, they are more expensive than other filter types due to their advanced technology and performance.
Membrane filters are made from different materials such as cellulose acetate, nitrocellulose, PVC, nylon, and polytetrafluoroethylene (PTFE). Each material has its own unique properties, cost, and compatibility with the liquid or gas being filtered. For instance, cellulose acetate is commonly used for microbiological analysis of water samples, while nylon and PTFE are suitable for filtering organic solvents and corrosive chemicals.
The size of the membrane filter is also a key factor that affects its price. Larger filters require more material and production costs, which ultimately increases the overall price. In addition, the pore size of the membrane filter determines its filtration performance and price. Smaller pore sizes provide better filtration accuracy but come at a higher cost.
The quantity of membrane filters required for a specific application also influences the price. Manufacturers offer discounts for bulk orders, making it more cost-effective to purchase filters in larger quantities.
In summary, membrane filters are highly effective but relatively expensive filtration solutions. The price depends on factors such as the material, size, pore size, and quantity required. It is essential to consider the specific filtration needs and choose the most suitable membrane filter based on cost-effectiveness and quality.
FAQ sourcing membrane filter manufacturer from China with multiple answers
Q: How can I source a reliable membrane filter manufacturer in China?
A: China is home to a wide range of membrane filter manufacturers, making it challenging to identify the best one for your company’s needs. The following are some of the most popular ways to source a reliable membrane filter manufacturer in China:
1. Online Searches: You can start by conducting online searches using popular B2B websites like Alibaba or Made-in-China. These platforms allow you to filter your search results based on product specifications, supplier type, and location.
2. Trade fairs: China hosts several trade fairs and exhibitions every year where membrane filter manufacturers showcase their products and innovations. Attending these events can help you meet with multiple suppliers under one roof and learn more about their offerings.
3. Referrals: Ask for referrals from friends, colleagues, or other businesses in your industry who have experience sourcing membrane filters from China. They may be able to point you in the direction of a trustworthy manufacturer that they have worked with before.
4. Third-party sourcing agents: Consider working with a third-party sourcing agent who has experience working with Chinese manufacturers. These professionals can help verify the quality of different manufacturers, translate communication, and negotiate pricing on your behalf.
Whatever approach you choose, it’s important to verify the manufacturer’s quality control processes, product certifications, and reliability before placing an order. Conducting a background check on the company and its management team, as well as communicating your requirements and expectations clearly, will go a long way in finding a trustworthy business partner.