Introduce about metal stamping press guide,Qulity,Cost,Supplier,Certification,Market,Tips,FAQ
Metal stamping press guide is a comprehensive resource that provides information and guidance on using metal stamping presses effectively. It covers various aspects such as operation, maintenance, safety protocols, and troubleshooting techniques. This guide aims to enhance the efficiency and productivity of metal stamping operations.
Quality is a vital consideration in metal stamping presses. The guide highlights the importance of selecting high-quality machines that are durable, reliable, and capable of delivering accurate results. It emphasizes the utilization of advanced technologies and materials to ensure precise stamping outputs.
Cost is another crucial factor discussed in the guide. It provides insights into the overall expenses associated with metal stamping operations, including equipment, raw materials, maintenance, and energy consumption. Tips on reducing costs without compromising quality are also included.
Choosing a reliable supplier is essential to guarantee the delivery of superior metal stamping presses. The guide advises conducting thorough research, comparing different suppliers, and seeking recommendations. Factors such as experience, customer reviews, and after-sales support should be considered before making a final decision.
Certification is a significant aspect when selecting metal stamping presses. The guide emphasizes the importance of procuring machines from certified suppliers who adhere to industry standards and regulations. Recognized certifications ensure the machines’ reliability and compliance with quality control protocols.
Market analysis and trends are also addressed in the guide to provide an understanding of the current metal stamping press market. It covers emerging technologies, key players, and industry growth projections. This information helps businesses stay updated and make informed decisions.
Tips and frequently asked questions (FAQ) sections aim to address common challenges and provide solutions to enhance metal stamping operations. It includes suggestions on improving productivity, troubleshooting common issues, optimizing maintenance schedules, and ensuring operator safety.
In conclusion, the metal stamping press guide serves as a valuable resource that covers various aspects of using metal stamping presses effectively. It highlights quality, cost, suppliers, certifications, market analysis, tips, and FAQs to assist businesses in maximizing their metal stamping operations.
Types of metal stamping press
Metal stamping press machines are widely used in industries for shaping and forming metal components. These machines use a combination of force and die to cut, pierce, bend, or shape the metal sheets. There are several types of metal stamping press machines available, each designed for specific applications. Here are some common types:
1. Mechanical Press: These presses use a flywheel to generate mechanical energy, which is then transferred to the metal through the operation of a crankshaft. Mechanical presses are suitable for high-speed operations and can deliver consistent force over a long time.
2. Hydraulic Press: Hydraulic presses use hydraulic cylinders to generate force. They are known for their high force capabilities and are ideal for heavy-duty stamping applications. Hydraulic presses are often used when high force, accurate control, and flexibility are required.
3. Servo Press: Servo presses are advanced machines that combine mechanical and servo technology. They use an electric motor instead of a flywheel and provide precise control over force, speed, and stroke length. Servo presses offer improved energy efficiency, accuracy, and flexibility and are often used in automotive and electronics industries.
4. Mechanical Servo Press: This type of press combines the speed of a mechanical press with the precision of a servo press. Mechanical servo presses are capable of delivering high force at high speed while maintaining accuracy. They are commonly used in high-volume production and applications requiring high-speed operations.
5. Pneumatic Press: Pneumatic presses use compressed air to generate force. They are lightweight, portable, and cost-effective. Pneumatic presses are commonly used for small-scale stamping and light-duty operations where high force is not required.
6. Gap Frame Press: Gap frame presses have an open-front design that allows easy access for loading and unloading materials. They provide versatility in terms of die space and can accommodate larger and irregularly shaped components.
7. Straight Side Press: Straight side presses have a rigid frame construction that provides stability and accuracy during the stamping process. They are capable of high force applications and are commonly used in precision metal forming.
These are some of the common types of metal stamping press machines available. The selection of a particular type depends on factors such as the nature of the application, required force, precision, speed, and cost-effectiveness.
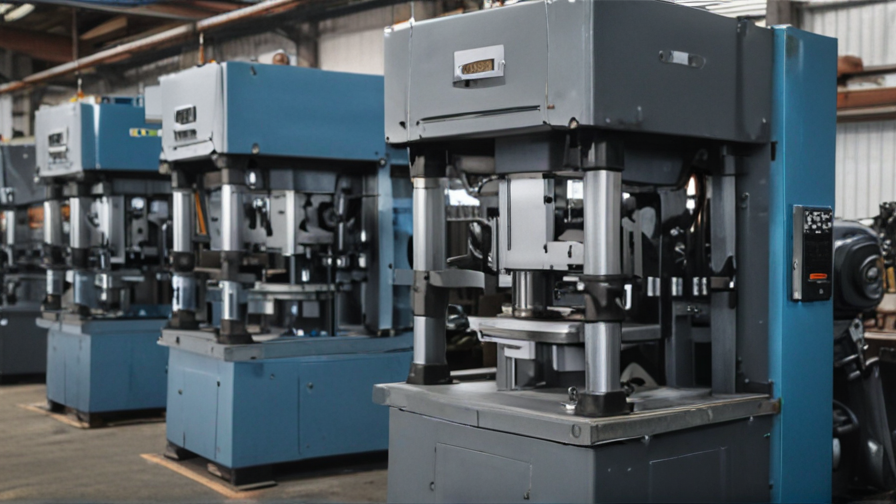
Pros and Cons of Using metal stamping press
Metal stamping presses are widely used in various industries for their ability to efficiently shape and form metal components. Here are some pros and cons of using metal stamping presses:
Pros:
1. Cost-effective: Metal stamping presses offer high production rates, reducing labor costs and overall production expenses. The automation and precision of the process minimize material waste, resulting in cost savings.
2. Versatile: These presses can handle a wide range of materials, including steel, aluminum, brass, and copper. Different shapes, sizes, and thicknesses can be effortlessly produced, making metal stamping presses suitable for diverse applications.
3. High productivity: With their high-speed operation, metal stamping presses can produce a large volume of parts in a short period. This increased productivity leads to faster production turnaround times and enhanced efficiency.
4. Improved accuracy and consistency: Metal stamping presses offer excellent repeatability and precision, ensuring that each part produced is identical. The application of consistent force and pressure during the stamping process results in high-quality, dimensionally accurate components.
5. Complex formations: These presses can create intricate and complex shapes, including bends, contours, extrusions, and depressions. Advanced stamping dies and progressive stamping techniques allow for the production of intricate parts that may otherwise be challenging to manufacture using other methods.
Cons:
1. Initial setup costs: Setting up a metal stamping press requires the design and manufacturing of specific dies or tooling. This initial investment can be expensive, especially for custom or specialized components. However, the cost is often offset by the long-term benefits and savings from mass production.
2. Limited flexibility: Metal stamping presses are optimized for high-volume production, making them less suitable for low-volume or prototyping projects. The setup and die changes required for different part designs can be time-consuming and costly, making them less flexible for small-scale production runs.
3. Material limitations: While metal stamping presses can process a wide range of materials, they may not be suitable for some materials with high elasticity or brittleness. These materials may be prone to cracking or deformation during the stamping process, requiring alternative manufacturing methods.
4. Maintenance and die lifespan: The dies used in metal stamping presses have a limited lifespan and may require regular maintenance. Replacing or repairing worn or damaged dies can result in additional costs and production downtime.
In summary, the use of metal stamping presses provides a cost-effective, highly productive, and versatile means of manufacturing metal components. While there may be limitations and initial setup costs, these drawbacks are often outweighed by the advantages in terms of quality, efficiency, and repeatability.
metal stamping press Reference Specifications (varies for different product)
Metal stamping press reference specifications can vary greatly depending on the specific product being manufactured. However, there are some general specifications that can be considered in the design and operation of a metal stamping press.
Firstly, the press capacity is an important specification. This refers to the maximum force or tonnage that the press is capable of exerting on the metal being stamped. Higher capacity presses are typically used for thicker or harder metals, while lower capacity presses are suitable for thinner or softer metals.
The bed size or working area of the press is another important specification. This determines the maximum size of the metal sheets that can be accommodated on the press. It is essential to ensure that the working area is compatible with the size of the metal blanks to be stamped.
The stroke length is a critical specification that affects the efficiency and versatility of the press. It refers to the distance the press ram travels from its upmost position to its downmost position. The stroke length must be chosen carefully to accommodate the thickness of the material being stamped and the depth of the required impression.
The press speed, which is typically measured in strokes per minute (SPM), is another specification to consider. The speed should be optimized to achieve the desired production rate without compromising the quality of the stamped parts. High-speed presses are suitable for higher production volumes, while slower speeds may be required for more intricate stamping processes.
Other important specifications include the type of drive system, such as hydraulic or mechanical, as well as the type of control system used to operate the press. Safety features, such as guards and emergency stop buttons, should also be incorporated into the press design to ensure the protection of the operators.
In conclusion, metal stamping press reference specifications can vary depending on the product being manufactured. These specifications include press capacity, bed size, stroke length, press speed, drive system, control system, and safety features. Each of these specifications should be carefully considered to ensure optimal performance and operation of the metal stamping press.
Applications of metal stamping press
Metal stamping presses are versatile machines used in a wide range of industries for various applications. Here are some key applications of metal stamping presses:
1. Automotive Industry: Metal stamping presses are crucial in the automotive sector for the production of car parts, including body panels, brackets, hinges, and engine components. They ensure precise shaping of metal sheets into required forms to maintain quality standards and meet design specifications.
2. Aerospace Industry: Metal stamping presses play a vital role in manufacturing aircraft components and structures such as fuselages, wing panels, and control surfaces. The high accuracy and repeatability of the stamping process ensure the desired dimensional accuracy and surface finish required for airworthiness.
3. Electrical and Electronics Industry: Stamping presses are utilized to manufacture electrical contacts, connectors, terminals, printed circuit boards (PCBs), and other electronic components. They ensure cost-effective mass production with consistent precision, enabling efficient electrical connectivity and optimal performance.
4. Appliances Manufacturing: Manufacturing household appliances, such as refrigerators, washing machines, and air conditioners, often involves metal stamping presses. They are used to create housing components, brackets, hinges, and other metal parts that are crucial for functionality and aesthetic appeal.
5. Construction Industry: Metal stamping presses are employed in construction for shaping and forming metal parts like roofing panels, facade elements, and structural components. These presses enable the production of large-scale, high-strength metal parts needed for various building projects.
6. Consumer Goods: Many consumer goods, including furniture, cookware, and hardware items, require metal stamping presses to create intricate designs or precise shapes. These presses ensure the consistent production of high-quality products at a competitive price.
7. Defense and Military: Metal stamping presses are used to manufacture components for defense and military applications, including ammunition casings, firearm parts, armored vehicle components, and hardware for military equipment.
8. Medical Equipment: Metal stamping is instrumental in the production of medical devices such as surgical instruments, implants, and diagnostic equipment. The high precision and repeatability of the stamping process ensure the desired functional and aesthetic qualities necessary for medical applications.
In conclusion, metal stamping presses are extensively used in various industries for a wide range of applications, including automotive, aerospace, electrical, appliances, construction, defense, consumer goods, and medical equipment manufacturing. They provide cost-effective and efficient means of shaping metal, enabling the production of high-quality and precision-driven products.
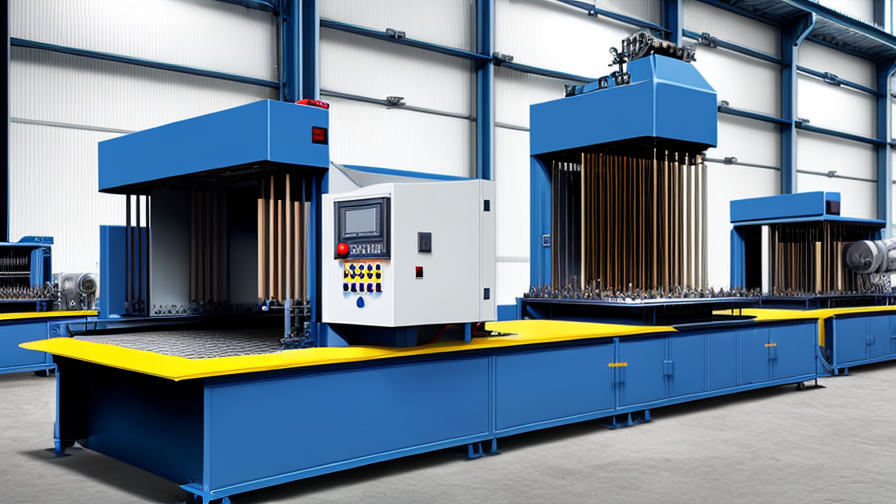
The Work Process and how to use metal stamping press
Metal stamping press is a highly efficient tool used in various industries to shape, cut, and form metal sheets and parts. The work process involves several steps and requires careful operation to ensure accuracy and safety.
The first step is to prepare the metal sheet for stamping. This involves cleaning and degreasing the sheet to remove any impurities that could affect the stamping process.
Next, the sheet is positioned and secured in the stamping press. This can be done manually or with the help of alignment tools and fixtures. It is vital to ensure that the sheet is accurately aligned to avoid any errors during stamping.
Once the sheet is properly positioned, the stamping process begins. The stamping press uses a combination of high pressure and specially designed dies to shape the metal. The metal sheet is sandwiched between the dies, and the press applies immense force to reshape or cut the metal.
During this process, it is important to monitor the progress and make adjustments as needed. This can include adjusting the pressure, speed, and position of the stamping press to achieve the desired results. Operators should also be vigilant for any signs of misalignment, deformation, or other abnormalities.
After the stamping process is complete, the newly formed parts or finished product are carefully removed from the stamping press. This is usually done manually using tools such as tongs or robotic arms, taking care to avoid any sharp edges or hot surfaces.
Lastly, the stamped metal parts may undergo additional processes such as deburring, cleaning, or surface treatment, depending on the intended application.
To effectively use a metal stamping press, operators must undergo proper training and strictly adhere to safety protocols. This includes wearing appropriate protective equipment such as gloves, safety glasses, and hearing protection. Regular maintenance and inspection of the press is also necessary to ensure its optimal performance and longevity.
In conclusion, metal stamping press is a valuable tool for shaping and forming metal sheets. By following the work process and taking necessary precautions, operators can utilize this machinery effectively and safely, resulting in high-quality stamped metal parts.
Quality Testing Methods for metal stamping press and how to control the quality
Metal stamping presses are commonly used in the manufacturing industry to shape and form metal components. Ensuring high-quality standards in metal stamping press operations is crucial to avoid defects and maintain product integrity. Here are some quality testing methods and measures to control the quality of metal stamping presses.
One of the primary quality testing methods for metal stamping presses is dimensional inspection. This involves measuring the stamped components using precision measuring instruments such as calipers, micrometers, or coordinate measuring machines. By comparing the measurements with the specified tolerances, any dimensional variations can be identified and addressed promptly.
Material testing is another essential quality control measure. This involves analyzing the material properties of the metal being stamped, such as strength, hardness, and ductility. Various methods, including tensile testing or hardness testing, can be employed to ensure the metal meets the required specifications.
In addition to material testing, visual inspection is crucial for identifying surface defects such as scratches, dents, or uneven stamping. Utilizing visual inspection tools such as magnifying lenses or visual inspection machines can help identify these defects and take corrective actions.
Machine performance monitoring is also vital to ensure quality in metal stamping presses. This can be achieved by routinely checking and calibrating the press parameters such as tonnage, speed, or die set-up. Monitoring these parameters can help detect any abnormalities or variations that could affect product quality, allowing adjustments to be made accordingly.
Implementing a robust process control system is another key measure to ensure quality in metal stamping presses. This involves developing and documenting standard operating procedures, including specific parameters for each stamping operation. Regular audits and inspections should be conducted to ensure adherence to these procedures, helping to maintain consistency and reduce the risk of defects.
In conclusion, ensuring quality in metal stamping press operations involves employing various testing methods and quality control measures. These include dimensional inspection, material testing, visual inspection, machine performance monitoring, and implementing a robust process control system. By effectively utilizing these methods, manufacturers can maintain the desired quality standards and minimize product defects.
metal stamping press Sample Policy and Post-Purchase Considerations for metal stamping press from China
Sample Policy:
1. Pre-purchase samples: Requesting samples before placing a bulk order is essential to evaluate the quality and performance of the metal stamping press. Ensure that the supplier offers a reasonable sample policy, allowing for inspection and testing of the product.
2. Quality assurance: Verify that the manufacturer adheres to international quality standards such as ISO 9001. Request documentation and certifications to guarantee the quality and reliability of the metal stamping press.
3. Warranty: Ensure that the supplier provides a warranty on the metal stamping press to cover any potential defects or malfunctions during a specified period. Clear understanding of the terms and conditions of the warranty is crucial to avoid any future disputes.
4. Customization options: Inquire about the supplier’s ability to customize the metal stamping press according to specific requirements. This would allow customization of features like tonnage, stroke length, speed, and automation, ensuring the press suits the particular needs of the business.
Post-Purchase Considerations:
1. Installation and training: Arrange for professional installation and comprehensive training for the operators of the metal stamping press. This will maximize efficiency, productivity, and safety while operating the machine.
2. Spare parts availability: Inquire about the availability of spare parts for the metal stamping press. A reliable supplier should be able to provide readily accessible spare parts, minimizing downtime in case of any component failure.
3. Technical support: Ensure that the supplier offers responsive technical support in case of any troubleshooting or operational concerns. This will help resolve issues promptly and maintain uninterrupted production.
4. Regular maintenance: Establish a regular maintenance schedule to prolong the lifespan of the metal stamping press. Consult the supplier for recommended maintenance procedures and guidelines to ensure smooth operation and prevent any unexpected breakdowns.
5. Feedback and reviews: Provide feedback and reviews about the purchased metal stamping press to the supplier. This will help them improve their product quality and customer service while also benefiting potential buyers in making informed decisions.
By considering these sample policies and post-purchase considerations, businesses can ensure a smooth purchase process and maximize the benefits of the metal stamping press purchased from China.
Sourcing metal stamping press from China: Opportunities, Risks, and Key Players
Sourcing metal stamping presses from China offers significant opportunities for businesses looking for cost-effective solutions and advanced technology. China is the largest producer of metal stamping presses globally and boasts a wide range of manufacturers catering to different industries.
Opportunities:
1. Cost Advantage: Chinese metal stamping presses can be obtained at a lower cost compared to other countries due to lower labor and production costs. This makes them an attractive option for businesses aiming to reduce manufacturing expenses.
2. Advanced Technology: Many Chinese manufacturers have made significant investments in research and development, resulting in advanced metal stamping press technology. These innovative solutions can enhance production efficiency and quality.
3. Diverse Product Range: China offers a wide range of metal stamping presses, including mechanical, hydraulic, and servo presses, catering to various requirements and budgets. This variety allows buyers to choose the most suitable option for their specific needs.
Risks:
1. Quality Concerns: Although China has made significant progress in improving product quality, some manufacturers may still produce substandard or counterfeit products. It is crucial to conduct thorough due diligence and select reputable suppliers to mitigate this risk.
2. Intellectual Property Protection: China’s intellectual property protection laws and enforcement can be a concern. Companies must take proper precautions to protect their designs and technologies when sourcing metal stamping presses.
3. Supply Chain Challenges: Dependence on a single source can lead to supply disruptions, especially during unforeseen events. Diversifying the supply chain or maintaining buffer inventory can mitigate this risk.
Key Players:
1. AIDA Engineering: A Japanese-Chinese joint venture, AIDA Engineering offers high-quality stamping presses with advanced technology and customization options.
2. JFY Machine: JFY Machine is a leading Chinese manufacturer specializing in servo-driven metal stamping presses. They provide innovative solutions with high precision and energy efficiency.
3. Yizumi Precision Machinery: Yizumi is a well-known Chinese manufacturer that produces a wide range of metal stamping presses, including hydraulic, mechanical, and servo presses, catering to various industries.
In conclusion, sourcing metal stamping presses from China presents several opportunities, such as cost advantages, advanced technology, and diverse product offerings. However, it is essential to consider the associated risks, including quality concerns and intellectual property protection. By selecting reputable manufacturers and taking appropriate precautions, businesses can leverage the benefits of China’s metal stamping press industry.
How to find and select reliable metal stamping press manufacturers in China,use google search manufacturers and suppliers
When searching for reliable metal stamping press manufacturers in China, Google search can be a useful tool. Here are some steps to follow while using Google search to find and select these manufacturers:
1. Use relevant keywords: Begin by using specific keywords like “metal stamping press manufacturers in China” or “custom metal stamping press suppliers.” These keywords will help narrow down the search results to manufacturers specializing in metal stamping press production.
2. Verify reputation and credibility: Look for manufacturers with a strong reputation and credibility. Check if they have certifications like ISO 9001 or other industry certifications that ensure quality control. Reading customer reviews and testimonials can also provide insights into their reliability.
3. Evaluate experience and expertise: Explore the manufacturer’s website or company profiles to understand their experience in the industry. Look for companies that have been in the metal stamping press manufacturing business for a considerable amount of time. This indicates their expertise and understanding of the manufacturing process.
4. Range of capabilities: Check if the manufacturer offers a wide range of metal stamping press capabilities. This includes different press types, sizes, and production volumes. Having a diverse range of capabilities ensures that the manufacturer can cater to your specific requirements effectively.
5. Quality control measures: Ensure that the manufacturer has stringent quality control measures in place. This ensures that the manufactured products meet the desired specifications and adhere to international quality standards.
6. Communication and language: Consider the language barrier while selecting a manufacturer from China. Look for manufacturers that have proficient English-speaking staff or provide dedicated translators to ensure smooth communication throughout the manufacturing process.
7. Request for samples and quotes: Before finalizing a manufacturer, request samples of their finished products to assess their quality. Additionally, ask for detailed quotes that clearly state all costs involved, including shipping and other additional fees.
8. Compare multiple manufacturers: Shortlist and compare multiple manufacturers to make an informed decision. Evaluate factors like pricing, lead times, quality, reputation, and customer service to find the most reliable option.
Remember, thorough research and due diligence are crucial when it comes to selecting a reliable metal stamping press manufacturer in China.
How to check metal stamping press manufacturers website reliable,use google chrome SEOquake check if ranking in top 10M
When you want to check the reliability of a metal stamping press manufacturer’s website, there are a few steps you can take. One of the first things you can do is use Google Chrome and install the SEOquake extension. This tool allows you to gather important information about a website’s ranking and other SEO factors.
Once you have installed SEOquake, simply enter the manufacturer’s website URL into your browser’s search bar. SEOquake will then provide you with details about the website’s ranking, such as its position in the top 10 million websites globally. If the website ranks well within this range, it indicates that it receives a significant amount of traffic and is likely more reliable.
However, relying solely on ranking may not always be sufficient to determine the website’s reliability. Hence, it’s advisable to consider other factors as well. Look for clear and detailed information about the company, including its history, experience, and credentials. A reputable manufacturer typically provides these details to demonstrate their expertise and credibility.
You should also check if the website provides comprehensive information about the metal stamping presses they offer, including specifications, capabilities, and any certifications. This demonstrates that the manufacturer is knowledgeable about their products and is committed to providing transparent information to potential customers.
Additionally, look for customer testimonials or reviews on their website or other reputable platforms. Positive feedback from satisfied customers can offer insights into the manufacturer’s reliability and the quality of their products.
In summary, using Google Chrome with the SEOquake extension to check a manufacturer’s ranking within the top 10 million websites is a good starting point. However, it is important to consider other factors such as the company’s history, credentials, detailed product information, and customer testimonials to ensure you are dealing with a reliable metal stamping press manufacturer.
Top 10 metal stamping press manufacturers in China with each 160 words introduce products,then use markdown create table compare
1. Nide Machinery Co., Ltd.
Nide Machinery specializes in manufacturing metal stamping presses with a focus on precision, durability, and productivity. Their range includes mechanical, hydraulic, and servo presses suitable for various applications. These presses are equipped with advanced features such as programmable control systems, in-process monitoring, and automatic material feeding. Nide Machinery’s products are known for their high efficiency, accuracy, and low maintenance requirements.
2. Yawei Nisshinbo Group
Yawei Nisshinbo Group is a leading manufacturer of metal stamping presses in China. With a wide product range, they offer mechanical, hydraulic, and servo presses suitable for different industries. Their presses are known for their robust construction, energy efficiency, and enhanced safety features. Yawei Nisshinbo Group’s advanced technology ensures high precision, speed, and productivity, making them ideal for mass production applications.
3. Chin Fong Machine Industrial Co., Ltd.
Chin Fong is a renowned metal stamping press manufacturer in China, providing mechanical and hydraulic presses with capacities ranging from 25 tons to 3,000 tons. Their presses are designed for high precision, minimal deflection, and efficient production. Chin Fong presses are widely used in automotive, electronics, and appliance industries, offering excellent repeatability, reliability, and ease of operation.
4. YIZUMI Group
YIZUMI is a leading metal stamping press manufacturer offering a diverse range of mechanical, hydraulic, and servo presses. Their presses are designed to handle various materials and applications, ensuring high productivity with improved accuracy. YIZUMI’s advanced technology and precision components result in enhanced production efficiency, reduced downtime, and increased quality control.
5. Haiwei Industries Co., Ltd.
Haiwei Industries specializes in the production of high-speed precision stamping presses, including hydraulic, mechanical, and servo presses. These machines are designed to deliver high accuracy, quick mold changing, and reliable performance. Haiwei Industries’ stamping presses are widely used in industries such as automotive, electronics, and home appliances, greatly improving production efficiency and product quality.
6. Yangli Group
Yangli Group is a renowned manufacturer of metal stamping presses, offering a wide range of hydraulic and mechanical presses. Their presses are known for their high rigidity, stability, and precision. Yangli Group’s stamping presses are widely used in industries such as automobile, aerospace, and household appliances, ensuring efficient production and excellent product quality.
7. AIDA Group
AIDA Group is a well-known manufacturer of metal stamping presses globally, including China. They provide a comprehensive range of mechanical and servo presses, known for their high productivity, precision, and longevity. AIDA Group’s stamping presses incorporate innovative technologies for enhanced production efficiency and reduced maintenance requirements, making them ideal for demanding industrial applications.
8. World Precise Machinery Group
World Precise Machinery Group specializes in the production of high-quality mechanical, hydraulic, and servo presses suitable for a wide range of metal stamping applications. Their presses are designed with durability, precision, and versatility in mind. World Precise Machinery Group’s stamping presses guarantee high production speed, accuracy, and operational stability, meeting the varying needs of different industries.
9. TRUMPF (China) Co., Ltd.
TRUMPF is a well-established manufacturer of metal stamping presses, providing innovative solutions for efficient and accurate production. Their range includes hydraulic, mechanical, and servo presses, featuring advanced control systems for optimal performance. TRUMPF’s stamping presses are renowned for their high energy efficiency, durability, and productivity, offering seamless integration into various manufacturing processes.
10. Amada (China) Co., Ltd.
Amada, a global leader in metal processing machinery, also provides high-performance metal stamping presses in China. Their range includes mechanical, hydraulic, and servo presses, offering exceptional durability, precision, and productivity. Amada’s stamping presses are capable of handling various materials and thicknesses, guaranteeing high-quality products in industries like automotive, aerospace, and electronics. These presses feature advanced automation and control systems for efficient operation and minimized downtime.
| Manufacturer | Press Types | Key Features |
| —————————-| —————————————— | ————————————————————— |
| Nide Machinery Co., Ltd. | Mechanical, Hydraulic, Servo | Precision, durability, high efficiency |
| Yawei Nisshinbo Group | Mechanical, Hydraulic, Servo | Robust construction, energy efficiency |
| Chin Fong Machine Ind. Co. | Mechanical, Hydraulic | High precision, minimal deflection, efficient production |
| YIZUMI Group | Mechanical, Hydraulic, Servo | Enhanced productivity, improved accuracy |
| Haiwei Industries Co., Ltd. | Mechanical, Hydraulic, Servo | High-speed precision, quick mold changing |
| Yangli Group | Mechanical, Hydraulic | High rigidity, stability, precision |
| AIDA Group | Mechanical, Servo | High productivity, longevity |
| World Precise Machinery Grp.| Mechanical, Hydraulic, Servo | Versatility, operational stability |
| TRUMPF (China) Co., Ltd. | Mechanical, Hydraulic, Servo | Innovative control system, energy efficiency |
| Amada (China) Co., Ltd. | Mechanical, Hydraulic, Servo | Durability, precision, high productivity |
Background Research for metal stamping press manufacturers Companies in China, use qcc.com archive.org importyeti.com
When it comes to metal stamping press manufacturers in China, there are several reputable companies worth considering. Three websites that can provide valuable information and insights into these manufacturers are qcc.com, archive.org, and importyeti.com.
Qcc.com is a Chinese business directory that allows users to search for specific companies and access their profiles. It provides details such as the company’s registered address, contact information, registration status, and key personnel. This information is useful for understanding the background and legitimacy of the manufacturers. Additionally, Qcc.com may provide insights into the scale of operations and customer feedback through ratings and reviews.
Archive.org, also known as the Wayback Machine, is an online platform that allows users to access archived versions of web pages. This can be particularly useful for researching manufacturers’ websites in China as it provides access to their historical information. By reviewing previous iterations of the websites, users can gain insights into the company’s development, range of products, certifications, and any changes over time. This can help determine the manufacturer’s experience and level of expertise in metal stamping press manufacturing.
Importyeti.com is a platform that provides import and export data for specific products and suppliers. Users can search for metal stamping press manufacturers in China and access information such as shipment records, prices, and even names of companies that have imported from the manufacturer. This data can help identify popular and trusted manufacturers, as well as their international reach and reputation.
By utilizing these three websites, researchers can gather comprehensive information about metal stamping press manufacturers in China. This includes background details from qcc.com, historical insights from archive.org, and import-export data from importyeti.com. It is important to analyze this information collectively to make an informed decision about potential suppliers.
Leveraging Trade Shows and Expos for metal stamping press Sourcing in China
Trade shows and expos are excellent platforms for sourcing metal stamping presses in China. These events provide a unique opportunity for businesses to connect with hundreds of suppliers under one roof, saving time and effort in the sourcing process.
One of the most prominent trade shows in China for metal stamping press sourcing is the China International Industry Fair (CIIF). This event attracts thousands of exhibitors from various sectors, including machinery and equipment manufacturing. Metal stamping press suppliers from all over China showcase their latest products and technologies, allowing buyers to compare options and negotiate deals face-to-face.
Attending trade shows also enables businesses to assess the quality and capabilities of potential suppliers. Many exhibitors demonstrate their equipment in action, giving buyers a firsthand experience of the performance and precision of their metal stamping presses. This hands-on approach helps in determining the most suitable supplier to fulfill specific manufacturing requirements.
In addition to CIIF, there are several specialized expos and fairs focusing on metalworking, such as the Shanghai Metalworking Technology Fair and the Guangzhou International Sheet Metal and Metal Processing Exhibition. These events provide a more concentrated and specific platform to find suppliers solely dedicated to metal stamping presses.
To maximize the effectiveness of attending these trade shows and expos, businesses should have a clear understanding of their metal stamping press requirements beforehand. Conducting thorough research and creating a checklist of essential features will enable buyers to identify potential suppliers that match their needs.
Furthermore, networking plays a crucial role in leveraging trade shows for metal stamping press sourcing. Engaging with industry professionals, participating in seminars, and joining business matchmaking sessions can yield valuable connections and insights. Establishing relationships with reliable suppliers and industry experts can streamline future sourcing efforts and ensure long-term partnerships.
In conclusion, trade shows and expos in China offer an immersive and efficient approach to source metal stamping presses. By attending these events, businesses can evaluate suppliers, compare products, and build valuable relationships, ultimately enhancing their sourcing capabilities and driving success in the metal stamping industry.
The Role of Agents and Sourcing Companies in Facilitating metal stamping press Purchases from China
Agents and sourcing companies play a crucial role in facilitating metal stamping press purchases from China. They act as intermediaries between buyers and manufacturers, providing valuable assistance throughout the sourcing process. Here is how they support the purchase process:
1. Supplier identification and evaluation: Agents and sourcing companies leverage their knowledge and network to identify reputable manufacturers or suppliers of metal stamping presses in China. They conduct thorough evaluations by considering factors such as quality control systems, production capabilities, and facility conditions.
2. Negotiation and price comparison: These intermediaries assist buyers in negotiating the best possible prices with manufacturers, leveraging their experience and market knowledge. They also help in comparing prices from multiple suppliers to ensure competitiveness.
3. Quality control and inspection: Agents and sourcing companies ensure that the purchased metal stamping presses meet quality standards. They conduct regular inspections at different stages of the production process, including material sourcing, manufacturing, and final product assessment. They also provide detailed quality inspection reports to buyers.
4. Logistics and shipping: Facilitating smooth logistics and shipping arrangements is another key task undertaken by agents. They handle all aspects of shipping, including documentation, customs clearance, and transportation, ensuring that the purchased metal stamping presses are delivered to the desired location on time and in good condition.
5. Language and cultural barrier bridging: Agents and sourcing companies bridge the language and cultural gaps between buyers and Chinese manufacturers. They are fluent in both English and the local language, enabling effective communication during negotiations, production, and after-sales support.
6. Risk mitigation and dispute resolution: Agents and sourcing companies protect buyers from potential risks associated with international purchases. They help in drafting comprehensive contracts, protecting intellectual property rights, and mediating any disputes that may arise during the sourcing process.
Overall, agents and sourcing companies act as reliable partners in facilitating metal stamping press purchases from China. By providing expertise, local market knowledge, and strong supplier networks, they streamline the sourcing process, saving time and resources for the buyers while ensuring quality and apt delivery.
Price Cost Research for metal stamping press manufacturers Companies in China, use temu.com and 1688.com
When conducting price cost research for metal stamping press manufacturers in China, two reliable sources to consider are temu.com and 1688.com. These platforms provide comprehensive information about various suppliers, allowing businesses to compare prices and evaluate the cost-effectiveness of different options.
Temu.com is a reputable online B2B platform that connects global buyers with Chinese suppliers. It offers a wide range of products, including metal stamping presses, ensuring that businesses have access to a diverse pool of manufacturers to choose from. The platform enables users to obtain quotes from different suppliers, negotiate prices, and communicate directly with potential partners. This facilitates transparent price comparisons and helps businesses identify the most competitive deals.
1688.com, on the other hand, is a popular and trusted wholesale marketplace in China. While the website is primarily in Chinese, it is a valuable resource for price cost research due to its extensive selection of factories and manufacturers offering metal stamping presses. Despite the language barrier, third-party translation tools like Google Translate can be utilized to navigate the platform effectively. Additionally, businesses may consider partnering with a local agent or interpreter when using 1688.com to enhance communication and streamline the negotiation process.
By leveraging both temu.com and 1688.com, companies can obtain a comprehensive overview of the pricing and cost structures available from metal stamping press manufacturers in China. They can compare quotes, evaluate manufacturing capabilities, and assess the quality standards of different suppliers. This research can help businesses make informed decisions regarding the most suitable manufacturer that aligns with their budgetary requirements and quality standards.
To ensure efficient price cost research, businesses should take advantage of the search filters provided by these platforms. Parameters such as price range, product specifications, and manufacturing capabilities can be utilized to narrow down the options and save time. It is also recommended to carefully review supplier profiles, customer reviews, and past transactions to ensure the credibility and reliability of potential manufacturers.
In conclusion, conducting price cost research for metal stamping press manufacturers in China can be effectively undertaken by utilizing temu.com and 1688.com. These platforms offer extensive options, facilitating transparent price comparisons and enabling businesses to find the most cost-effective and reliable supplier for their manufacturing needs.
Shipping Cost for metal stamping press import from China
The cost of importing a metal stamping press from China can vary depending on various factors. Typically, shipping costs for heavy machinery like a metal stamping press are calculated based on the weight, dimensions, and distance that the shipment needs to travel.
To determine the shipping cost from China, it is essential to consider the mode of transportation, either by sea or air. Sea freight is usually more economical but takes longer, while air freight is faster but more expensive.
For a metal stamping press, sea freight is commonly preferred due to its cost efficiency. The freight charges are calculated based on the volume and weight of the machine. The larger and heavier the press, the higher the shipping cost will be. Additionally, shipping costs can also be affected by the origin and destination ports, and any additional services required such as insurance, customs clearance, or local handling fees.
To provide a rough estimate, the shipping cost for a metal stamping press from China to an average international port could range between $2,000 to $10,000 USD. However, these costs are subject to change based on the factors mentioned earlier.
It is crucial to note that the given estimate does not include any import duties, taxes, or tariffs that may apply in the destination country. It is advisable to consult a freight forwarder or shipping agent who can provide a more accurate estimate based on your specific requirements and destination.
In conclusion, the cost of shipping a metal stamping press from China depends on various factors such as the weight, dimensions, mode of transportation, and additional services required. Obtaining quotes from multiple shipping companies or freight forwarders is necessary to find the most competitive shipping cost.
Compare China and Other metal stamping press Markets: Products Quality and Price,Visible and Hidden Costs
China is a dominant player in the metal stamping press market, but it is essential to compare its products’ quality and prices with other markets. Quality refers to the reliability, durability, and performance of the metal stamping press. China has made significant strides in improving the quality of its products over the years, especially in terms of materials and construction. However, it is still widely perceived that the quality of metal stamping presses from Western markets, such as Germany and Japan, is superior. These markets have established reputations for precision engineering and adherence to strict quality standards.
In terms of price, China has a competitive advantage due to its lower labor and production costs. As a result, Chinese metal stamping presses are generally more affordable compared to those from other markets. However, this lower price sometimes comes at the expense of quality. There have been instances where Chinese manufacturers have compromised on materials or manufacturing processes to offer a cheaper product. Therefore, while they may be cost-effective initially, the long-term reliability and durability of these products may be questionable.
When considering quality and price, it is important to assess both visible and hidden costs associated with metal stamping presses. Visible costs include the initial purchase price, spare parts, and maintenance services. China’s lower labor costs often result in cheaper spare parts and maintenance services, making it an attractive option from a visible cost perspective. However, hidden costs such as downtime, repair frequency, and productivity losses must also be considered. If a cheap Chinese metal stamping press requires frequent repairs and extended downtime, it may end up being more costly in the long run.
Ultimately, the decision to choose a metal stamping press from China or other markets depends on the specific needs and priorities of the buyer. If price is the primary concern, Chinese products may be more appealing. However, if quality and long-term reliability are crucial, other markets might offer better options. It is crucial to conduct thorough research, consider visible and hidden costs, and assess the reputation and track record of manufacturers before making a purchase decision.
Understanding Pricing and Payment Terms for metal stamping press: A Comparative Guide to Get the Best Deal
Pricing and payment terms for metal stamping presses can vary greatly depending on several factors, including the type and size of the press, the manufacturer, the quality and materials used, and the market demand. It is essential to understand these factors and conduct a comparative analysis to get the best deal possible.
When it comes to pricing, it is important to consider the initial cost of the press, as well as any additional costs such as shipping, installation, and training. Some manufacturers may include these costs in the overall price, while others may charge them separately. It is crucial to clarify these details upfront to avoid any surprises later on.
Additionally, it is important to compare pricing from different manufacturers to ensure that you are getting a competitive offer. Requesting quotes from multiple manufacturers and evaluating the features, specifications, and warranties provided can help in making a well-informed decision.
Payment terms are another crucial aspect to consider. Understanding the payment structure and terms offered by different manufacturers is essential to plan your budget and finances accordingly. Common payment terms can include upfront payment, installment payments, or leasing options. Assessing the financial implications of each option is vital to choose the most suitable payment method.
Furthermore, it is advisable to negotiate with the manufacturer to achieve the best pricing and payment terms. Manufacturers may be willing to offer discounts or adjust payment schedules to meet your requirements. Building a good relationship with the manufacturer can also help in negotiating favorable terms.
Finally, it is crucial to thoroughly review any warranties, guarantees, or after-sales services offered by the manufacturer. Understanding the coverage and duration of these benefits can give you peace of mind and protect your investment in the long run.
In conclusion, understanding pricing and payment terms for metal stamping presses requires a comparative approach. Comparing prices, assessing payment options, and negotiating with manufacturers can help in obtaining the best possible deal. Additionally, reviewing warranties and after-sales services is crucial to ensure a satisfactory purchase experience.
Chinese Regulations and Industry Standards Certifications for metal stamping press,Import Regulations and Customs for metal stamping press from China
Chinese Regulations and Industry Standards Certifications for metal stamping press:
1. CCC Certification: The China Compulsory Certification (CCC) is a mandatory certification program for various products, including metal stamping presses. It ensures that the product meets safety, quality, and environmental protection standards set by the Chinese government.
2. ISO 9001: This internationally recognized certification ensures that the manufacturer has implemented a quality management system to consistently provide products that meet customer and regulatory requirements.
3. GB/T Standards: The metal stamping press industry in China follows the GB/T standards, which are national standards for various products, including machinery. These standards define technical specifications, performance requirements, and testing methods.
4. Occupational Health and Safety Standards: Metal stamping press manufacturers must comply with Chinese occupational health and safety standards, such as GB/T 28001, to ensure a safe working environment for employees.
Import Regulations and Customs for metal stamping press from China:
1. Import Duties and Tariffs: Importing metal stamping presses from China may attract customs duties, taxes, and Value Added Tax (VAT) depending on the country of import. Importers should verify the applicable duties and obtain proper customs classification for accurate duty calculation.
2. Customs Documentation: Importers need to provide necessary customs documentation, such as commercial invoice, packing list, bill of lading/airway bill, and a certificate of origin. These documents are required to clear customs and fulfill legal import requirements.
3. Compliance with Import Regulations: Metal stamping press importers should ensure compliance with import regulations related to product safety, labeling, and packaging standards set by the importing country. Importers may seek the assistance of customs brokers or import compliance specialists to navigate these requirements.
4. Intellectual Property Rights (IPR) Protection: Importers should be cautious about potential Intellectual Property Rights (IPR) infringements. It is essential to verify that the metal stamping press manufacturer owns the rights to the product design and has not copied or imitated any patented designs.
It is advisable for importers to consult with legal professionals or industry experts for up-to-date information on Chinese regulations, standards certifications, and import customs procedures.
Sustainability and Environmental Considerations in metal stamping press Manufacturing
Sustainability and environmental considerations play a crucial role in metal stamping press manufacturing. This sector includes the production of machines used in metal forming processes, such as cutting, bending, and shaping steel sheets. Several key aspects need to be taken into account to ensure sustainability and minimize the environmental impact of these manufacturing processes.
Firstly, energy efficiency is a primary concern. Metal stamping presses are high-power machines that consume a significant amount of electricity. Implementing energy-efficient technologies, such as variable speed drives, can optimize energy usage by regulating the motor speed according to the required load. This can help reduce energy consumption and lower carbon emissions.
Secondly, waste reduction and recycling should be prioritized. Metal stamping processes generate waste materials, including metal shavings and scrap. Proper waste management practices, such as implementing recycling programs and collecting swarf and scrap materials for reuse, can minimize landfill waste and conserve resources.
Moreover, the choice of materials used in manufacturing metal stamping presses is critical. Opting for sustainable materials, such as recycled steel or lightweight alloys, can reduce the carbon footprint associated with raw material extraction and production. Additionally, selecting materials that are easily recyclable at the end of their life cycle ensures a circular economy approach.
In terms of manufacturing processes, adopting lean manufacturing principles can significantly enhance sustainability. Minimizing material handling, optimizing production flows, and reducing process waste can contribute to resource efficiency and lower environmental impacts.
Furthermore, implementing environmentally friendly technologies, such as water-based lubricants instead of oil-based ones, can reduce the use of hazardous substances and minimize pollution risks. Additionally, the proper maintenance and regular calibration of metal stamping presses can ensure optimal performance, extend their lifespan, and minimize the need for replacements.
In conclusion, sustainability and environmental considerations are fundamental in metal stamping press manufacturing. By focusing on energy efficiency, waste reduction and recycling, material selection, lean manufacturing principles, and environmentally friendly technologies, manufacturers can contribute to a more sustainable and eco-friendly industry.
List The Evolution history of “metal stamping press”
Metal stamping press, also known as a stamping machine, is a highly versatile and efficient tool used in the manufacturing industry for shaping metal sheets and parts. The evolution of metal stamping press can be traced back to the early 19th century when it was first designed and manufactured.
In its earliest form, the metal stamping press consisted of a manual lever or a foot-operated pedal mechanism used to generate the necessary force to shape the metal. However, these machines were limited in their capacity and required significant human effort.
With the advent of the industrial revolution in the late 1800s, metal stamping presses underwent significant advancements. Steam-powered and hydraulic presses were introduced, revolutionizing the manufacturing process. These new machines provided increased force and precision, enabling the production of more complex and intricate metal parts.
In the early 20th century, the development of electric-powered stamping presses further improved the efficiency and productivity of the manufacturing process. These machines eliminated the need for external power sources such as steam engines, making them more convenient and cost-effective.
The mid-20th century saw the introduction of mechanical stamping presses driven by electric motors and flywheels. These machines offered higher speeds and greater control over the stamping process, allowing for greater precision and repeatability.
In recent decades, computer numerical control (CNC) technology has revolutionized metal stamping press design and operation. CNC-controlled press machines can be programmed to perform complex operations automatically, reducing human error and increasing productivity. Integrated sensors and feedback systems ensure precise control and measurement of the stamping process, enhancing product quality and consistency.
Furthermore, advancements in material science and engineering have led to the development of specialized stamping presses for specific industries. High-speed stamping machines, progressive die presses, and transfer presses are examples of specialized stamping technologies that cater to different manufacturing requirements.
Today, metal stamping presses continue to evolve with the introduction of robotics, machine learning, and automation technologies. These advancements aim to further enhance productivity, efficiency, and safety in the manufacturing industry.
In conclusion, metal stamping press technology has come a long way from its humble beginnings in the 19th century. From manual levers to advanced CNC-controlled machines, these tools have transformed the manufacturing process, enabling the production of complex metal parts efficiently and accurately.
The Evolution and Market Trends in metal stamping press Industry
The metal stamping press industry has
experienced significant evolution and
market trends over the years. Metal
stamping presses are machines used to
shape and cut metal sheets into desired
forms. These presses have come a long
way in terms of technology and
capabilities, as well as the market
demand for products made by these
machines.
One of the evolutionary aspects of the metal stamping press industry is the advancement in press technology. These machines have become more sophisticated, with improved features such as computer numerical control (CNC) systems, which provide precise and automated control over the stamping process. This allows for faster production and higher quality output. Additionally, the use of hydraulic and servo-electric drives has increased the efficiency and flexibility of these machines.
Another significant trend in the metal stamping press industry is the growing demand for lightweight materials. As industries, such as automotive and aerospace, increasingly focus on fuel efficiency and environmental sustainability, there is a rising need for components made from lightweight metals like aluminum. Metal stamping presses are capable of shaping thin sheets of these materials accurately, making them crucial in meeting this market demand.
Market trends also indicate a shift towards cost-effective and time-efficient manufacturing processes. Metal stamping presses provide an economical solution for mass production, as they can rapidly produce large quantities of parts with high precision. This advantage has contributed to the increased adoption of metal stamping processes by various industries, including automotive, electronics, and appliances.
Besides, there is a growing focus on automation and robotics in the metal stamping press industry. Robotic systems integrated with stamping presses improve efficiency, reduce labor costs, and enable complex processes. Automation also ensures consistent quality control and enhances workplace safety. This trend is expected to continue as industries increasingly embrace Industry 4.0 technologies.
In conclusion, the metal stamping press industry has evolved significantly over the years. Advancements in press technology, the demand for lightweight materials, a shift towards cost-effective and time-efficient manufacturing, and the adoption of automation and robotics have shaped the industry’s evolution. Businesses in this industry must continuously adapt to these market trends to remain competitive and meet the changing demands of various industries.
Custom Private Labeling and Branding Opportunities with Chinese metal stamping press Manufacturers
Chinese metal stamping press manufacturers offer excellent opportunities for custom private labeling and branding. With their expertise in metal stamping press manufacturing, these manufacturers are well-equipped to cater to the specific branding needs of businesses across different industries.
One of the key advantages of working with Chinese manufacturers is their ability to provide custom private labeling. They can help businesses create their own unique brand identity by incorporating custom logos, designs, and labels on the metal stamping products. This allows businesses to establish a strong brand presence and recognition in their target markets.
Chinese manufacturers also offer branding opportunities through customization. They can tailor the metal stamping press to meet the specific requirements and preferences of businesses. This includes options such as different sizes, finishes, and features. By collaborating with manufacturers, businesses can ensure that their metal stamping press aligns perfectly with their brand image and values.
Moreover, Chinese manufacturers often have a wide range of production capabilities, allowing businesses to manufacture products in bulk quantities. This is beneficial for branding purposes as it enables consistent supply and availability of branded metal stamping products in the market. Additionally, Chinese manufacturers often offer competitive pricing, making it cost-effective for businesses to establish a strong brand presence without compromising on quality.
In conclusion, Chinese metal stamping press manufacturers provide attractive opportunities for custom private labeling and branding. By leveraging their expertise, businesses can create a unique brand identity and tailor their metal stamping products to meet their specific needs. Working with Chinese manufacturers also offers the advantages of efficient bulk production and cost-effectiveness, making it a strategic choice for businesses looking to establish their brand in the market.
Tips for Procurement and Considerations when Purchasing metal stamping press
When purchasing a metal stamping press, there are several important considerations and tips that can help ensure you make the right procurement decision. Here are some key points to keep in mind:
1. Determine your specific requirements: Understand your production needs and the type of metal stamping tasks you will be performing. Identify the features, capabilities, and specifications required from the press.
2. Quality and reliability: Look for a press that is highly reliable and can consistently deliver high-quality stamped parts. Consider the durability of the materials used and the overall construction of the press.
3. Capacity and size: Consider the size and capacity of the metal stamping press. Ensure it can accommodate the size and thickness of the materials you will be working with. Evaluate the tonnage capacity to match your production requirements.
4. Speed and productivity: Assess the speed and productivity of the press. Evaluate the stroke rate, automation capabilities, and the ease of setup and operation. Look for features that can optimize production efficiency.
5. Safety features: Prioritize the safety features of the press. Look for systems that protect operators and prevent accidents. Features like emergency stop buttons, safety guards, and overload protection are essential.
6. Maintenance and serviceability: Consider the ease of maintenance and the availability of spare parts. Choose a press that has a good reputation for after-sales service and support. This will ensure minimal downtime and quick resolution of any technical issues.
7. Cost: Set a budget and evaluate the cost-effectiveness of the press. Consider the initial investment, operational costs, and potential return on investment in terms of improved productivity and efficiency.
8. Vendor reputation: Do thorough research on the manufacturer or supplier of the metal stamping press. Check their reputation, customer reviews, and track record in delivering quality equipment.
9. Warranty and support: Inquire about the warranty and support provided by the manufacturer or supplier. A comprehensive warranty and reliable customer support can provide peace of mind and ensure long-term satisfaction.
10. Consider future needs: Anticipate any future requirements or changes in your production processes. Choose a metal stamping press that can be easily upgraded or customized to adapt to evolving needs.
In summary, careful consideration of your specific requirements, quality, capacity, speed, safety, maintenance, cost, vendor reputation, warranty, support, and future needs will help you make the right procurement decision for a metal stamping press.
FAQs on Sourcing and Manufacturing metal stamping press in China
1. Why should I consider sourcing and manufacturing metal stamping press in China?
Sourcing and manufacturing metal stamping press in China can be highly advantageous due to several factors. China has a vast manufacturing infrastructure with a wide range of specialized factories and suppliers offering competitive pricing. The country’s extensive supply chain and skilled labor force make it a preferred destination for metal stamping press production. Additionally, China offers economies of scale, quick turnaround times, and access to advanced technologies, ensuring high-quality products at affordable prices.
2. How can I find a reliable metal stamping press manufacturer in China?
To find a reliable metal stamping press manufacturer in China, it is essential to conduct thorough research and due diligence. Start by identifying reputable manufacturing companies through online directories, industry associations, and trade shows. Visit these manufacturers in person or through virtual meetings to assess their facilities, equipment, and production capabilities. Request references and check their track record in delivering quality products on time. Collaboration with sourcing agents or third-party inspection companies can also help in verifying manufacturers and ensuring a smooth sourcing experience.
3. What are the key considerations while sourcing metal stamping press in China?
When sourcing metal stamping press in China, key considerations include product specifications, quality control measures, pricing, lead times, and communication. Clearly communicate your requirements and specifications to manufacturers, ensuring they have the necessary expertise and capacity to meet your expectations. Implement stringent quality control measures by conducting on-site inspections and testing during production and before shipment. Negotiate pricing diligently, considering factors such as product complexity, order volume, and production materials. Maintain effective communication channels with manufacturers to address any concerns, provide regular updates, and ensure a successful collaboration.
4. Are there any risks associated with sourcing from China?
While sourcing from China can be highly beneficial, there are inherent risks that need to be considered. These include language and cultural barriers, intellectual property protection, product quality consistency, and logistical challenges. However, thorough research, strong partnerships, proper due diligence, and legal contracts can mitigate these risks effectively.
5. How can I ensure compliance with international quality standards when manufacturing metal stamping press in China?
To ensure compliance with international quality standards, collaborate with manufacturers who possess relevant certifications such as ISO 9001. Implement quality control processes, conduct regular inspections, and implement third-party quality checks during the production process. Clearly communicate your quality requirements and request samples and prototypes for evaluation. Engage in continuous communication and feedback loops with manufacturers to address any quality issues promptly and efficiently.
In summary, sourcing and manufacturing metal stamping press in China offer numerous advantages including cost-effectiveness, advanced technology, and a vast supply chain. However, it is essential to conduct thorough research, due diligence, and maintain effective communication to find reliable manufacturers and ensure compliance with international quality standards.
Why contact sourcifychina.com get free quota from reliable metal stamping press suppliers?
SourcifyChina.com is able to provide a free sourcing quota from reliable metal stamping press suppliers due to several reasons. Firstly, SourcifyChina.com has established strong partnerships and networks with numerous metal stamping press suppliers in China. These suppliers have been thoroughly vetted and evaluated to ensure their reliability, credibility, and the quality of their products.
Through these partnerships, SourcifyChina.com is able to negotiate and secure competitive prices and favorable terms from the suppliers. Consequently, they can pass on these benefits to their clients by offering a free sourcing quota without compromising quality.
Secondly, SourcifyChina.com operates on a model that charges service fees to manufacturers who successfully place orders through their platform. By offering a free sourcing quota upfront, they can attract a higher volume of manufacturers to use their services, which helps them generate revenue through the service fees.
Furthermore, SourcifyChina.com aims to build long-term relationships with manufacturers and establish themselves as a trusted sourcing partner. By providing a free quota, they can demonstrate their commitment to customer satisfaction and help manufacturers streamline their procurement process.
Additionally, SourcifyChina.com recognizes the competitive nature of the sourcing industry and the importance of providing value-added services. Offering a free quota allows manufacturers to assess the potential cost savings and benefits they can obtain through SourcifyChina.com’s services before making a financial commitment.
In conclusion, SourcifyChina.com offers a free sourcing quota from reliable metal stamping press suppliers by leveraging their partnerships, operating on a service fee model, aiming for long-term relationships, and providing value-added services. This approach allows manufacturers to confidently evaluate the advantages of utilizing SourcifyChina.com’s services without incurring any upfront costs.