Introduce about parts of a cnc mill guide,Qulity,Cost,Supplier,Certification,Market,Tips,FAQ
A CNC mill, also known as a computer numerical control mill, is a machine tool that uses computerized controls to precisely remove material from a workpiece. It is widely used in manufacturing industries due to its efficiency and accuracy. Understanding the various parts of a CNC mill is essential for a successful milling process.
1. Quality: The quality of a CNC mill greatly influences its performance and durability. High-quality components ensure smooth operation, minimal maintenance, and precise machining results.
2. Cost: The cost of a CNC mill varies depending on factors such as its size, features, and brand. It is crucial to consider your budget and requirements when selecting a mill that delivers optimal value for money.
3. Supplier: Choosing a reliable and reputable supplier is essential to ensure you receive a CNC mill of high quality and excellent customer service. Research and compare suppliers to find the one that meets your specific needs.
4. Certification: Ensuring that the CNC mill meets industry standards and safety regulations is crucial. Look for certifications such as ISO, CE, or UL to guarantee a reliable and compliant machine.
5. Market: The CNC mill market is highly competitive, with numerous manufacturers offering a wide range of models. Evaluate the market trends, customer reviews, and feedback to make an informed decision about the most suitable mill for your application.
6. Tips: Seek advice from experts or experienced machinists to understand the best practices and techniques for operating a CNC mill effectively. Learn about tooling, programming, and maintenance to optimize productivity.
7. FAQ: Frequently Asked Questions provide valuable insights and answers to common queries about CNC mills. Frequently visit websites, forums, or consult suppliers’ customer support to broaden your knowledge and address any concerns.
In conclusion, when considering a CNC mill, it is crucial to evaluate the quality, cost, and certification of the machine. Choosing a reputable supplier and staying informed about the market trends can lead to a successful purchase. Familiarizing yourself with tips, frequently asked questions, and seeking advice from experts will help you optimize the use of your CNC mill.
Types of parts of a cnc mill
A CNC mill, or computer numerical control mill, is a machine tool used to shape solid materials such as metal or wood by removing material from a workpiece using rotating cutters. It consists of several key parts that work together to enable precise and efficient machining operations.
1. Bed: The bed is the base of the machine that supports all the other components. It provides stability and rigidity and is usually made of cast iron or steel to ensure durability.
2. Column: The column is mounted on the bed and provides vertical motion to the spindle. It houses the spindle motor, allowing it to move up and down, while maintaining the required stability and accuracy.
3. Spindle: The spindle is the main rotating component that holds the cutting tool. It provides the rotational motion needed to remove material from the workpiece. Spindles may have different power ratings, speed ranges, and tool holding mechanisms depending on the specific application.
4. Tool Changer: CNC mills often feature an automatic tool changer that allows for the rapid exchange of different cutting tools. The tool changer is typically located on the side of the machine and holds a carousel of tool holders. It enables the mill to automatically switch between tools, reducing downtime for manual tool changes.
5. Control Panel: The control panel is where operators interact with the CNC mill. It houses the user interface, enabling the input of tool paths, speeds, feeds, and other machining parameters. Operators can also monitor the machining process and make adjustments as necessary.
6. Worktable: The worktable is where the workpiece is secured for machining. It can typically move in multiple directions, allowing for various cutting operations. Worktables can have manual or automatic movement capabilities, depending on the complexity of the CNC mill.
7. Linear Guides: Linear guides provide smooth and precise motion to the various moving components of the CNC mill, such as the worktable and the spindle head. They ensure accuracy and repeatability by minimizing any unwanted movement or vibration during machining.
8. Coolant System: CNC mills often employ a coolant system to regulate the temperature of the cutting tool and workpiece during the machining process. The coolant can be a liquid or air, and it helps to extend tool life, improve surface finish, and evacuate chips.
These are some of the key parts that make up a CNC mill, working together to deliver efficient and accurate machining operations. Each part plays a vital role in ensuring the machine’s performance and versatility, allowing for a wide range of applications in industries such as manufacturing, aerospace, and automotive.
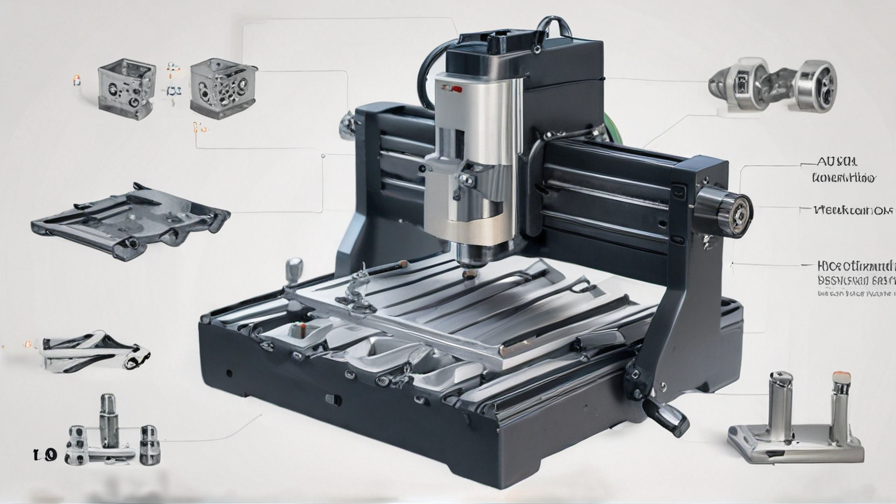
Pros and Cons of Using parts of a cnc mill
Using parts of a CNC mill can have several advantages and disadvantages. Here are some pros and cons to consider:
Pros:
1. Cost-effective: Utilizing parts of a CNC mill can be a cost-effective option compared to purchasing a brand new mill. It allows businesses or individuals with a limited budget to access the advantages of CNC machining without investing heavily.
2. Flexibility: By using parts of a CNC mill, you have the freedom to customize and adapt the machine according to your specific needs. You can select parts that best suit your requirements, such as the spindle, controller, or axis configuration, allowing for a more versatile setup.
3. Upgradability: As technology advances, industries often require more advanced features and capabilities in their CNC machines. By using parts from a CNC mill, you can easily upgrade specific components to keep pace with evolving needs, enhancing the overall performance and functionality.
4. Reduced lead times: Since most parts of a CNC mill are readily available, you can significantly reduce lead times compared to manufacturing or ordering a complete machine. This can be advantageous for urgent projects or when you need to replace parts quickly.
Cons:
1. Compatibility issues: Mixing different parts from various CNC mills may lead to compatibility issues. Not all components are designed to work seamlessly with each other, which can result in functionality problems or reduced efficiency of the machine.
2. Limited warranty or support: When using parts from different sources, it may be difficult to find a comprehensive warranty or technical support. This can be problematic if components fail or if you require assistance during the assembly or troubleshooting process.
3. Quality concerns: The quality of the parts may vary depending on their source. It’s crucial to carefully inspect and evaluate the components to ensure their reliability, durability, and compatibility. Poor-quality parts may affect the accuracy, precision, or overall performance of the CNC mill.
4. Time-consuming assembly: Assembling a CNC mill using parts from different sources can be time-consuming and require advanced technical knowledge. Proper alignment, calibration, and integration of the various components may be challenging for individuals without prior experience, potentially resulting in operational issues.
In conclusion, utilizing parts of a CNC mill can be a cost-effective and flexible solution, enabling customization and upgradability. However, it is important to consider potential compatibility issues, limited warranty or support, as well as the quality and time required for assembly.
parts of a cnc mill Reference Specifications (varies for different product)
A CNC mill, also known as a Computer Numerical Control mill, is a machining device that uses computerized controls to operate and manipulate cutting tools to shape and mold various materials. It is widely used in industries such as aerospace, automotive, and manufacturing for its precision and efficiency.
A typical CNC mill consists of several essential components that work together to perform various machining operations. These components include:
1. Control Panel: This is where the operator sets and adjusts the machining parameters, such as cutting speed, tool selection, and tool path. The control panel also displays real-time information and diagnostics.
2. Axis System: The axis system is responsible for moving the cutting tool along three main axes – X, Y, and Z. It consists of motorized servo or stepper motor-driven linear guides and ball screws to precisely control tool movement.
3. Spindle: The spindle is the primary rotating component that holds the cutting tool. It provides the necessary speed and power to cut a wide range of materials. Spindles can be equipped with various tool holders and can rotate at high speeds to achieve optimal cutting performance.
4. Tool Changer: A CNC mill often has an automatic tool changer, which can store multiple cutting tools and quickly switch between them during operations. This allows for the continuous machining of complex parts without manual intervention.
5. Worktable: The worktable is a flat surface where the material to be machined is secured. It can be moved along the X and Y axes to position the workpiece accurately. Some mill models also have a rotary table to enable the machining of cylindrical or curved surfaces.
6. Coolant System: To ensure efficient cutting and prevent tool wear, a CNC mill is equipped with a coolant system that sprays a coolant onto the cutting area. This helps to dissipate heat, lubricate the tool, and remove chips and debris.
7. Safety Features: CNC mills are equipped with safety systems to protect operators and the machine itself. These may include interlocking doors, emergency stop buttons, and sensors to detect potential malfunctions or collisions.
In conclusion, a CNC mill consists of various components such as the control panel, axis system, spindle, tool changer, worktable, coolant system, and safety features. These elements work harmoniously to execute precision machining operations and cater to specific industry requirements.
Applications of parts of a cnc mill
CNC (Computer Numerical Control) milling machines are versatile tools that are used in a wide range of industries for various applications. They consist of several parts that work together to shape and cut materials with precision. Here are some key parts of a CNC mill and their applications:
1. Spindle: The spindle is responsible for rotating the cutting tool. It can be equipped with different types of cutting tools such as end mills, drills, or ball nose cutters. The spindle speed and direction can be controlled for tasks like drilling holes, creating pockets, or carving intricate details.
2. Cutting Tool: The cutting tool is a crucial part that determines the type of operation that can be performed. End mills, for example, can remove material through cutting and carving, while drills are used for creating holes. The choice of tool depends on the material being machined and the desired outcome.
3. Bed: The bed is the platform on which the workpiece is secured. It ensures stability during the machining process. Different materials like metals, plastics, or wood can be placed on the bed to be shaped or cut according to the programmed design.
4. Worktable: The worktable can be adjusted in various directions to position the workpiece accurately. It allows for different axis movements (X, Y, and Z) to achieve intricate designs or complex geometries.
5. Controls and Software: CNC mills are operated using computerized controls and a software program that contains the cutting instructions. The operator can input the desired dimensions, shapes, or patterns, and the machine translates those instructions into precise movements of the cutting tool.
Overall, the applications of a CNC mill are extensive. They are commonly used in industries such as manufacturing, aerospace, automotive, and prototyping. CNC milling machines can be employed for tasks like creating precise metal components, milling PCBs (Printed Circuit Boards), engraving intricate designs on materials, or producing custom furniture pieces. The accuracy, repeatability, and versatility of CNC mills make them indispensable tools in modern manufacturing processes.
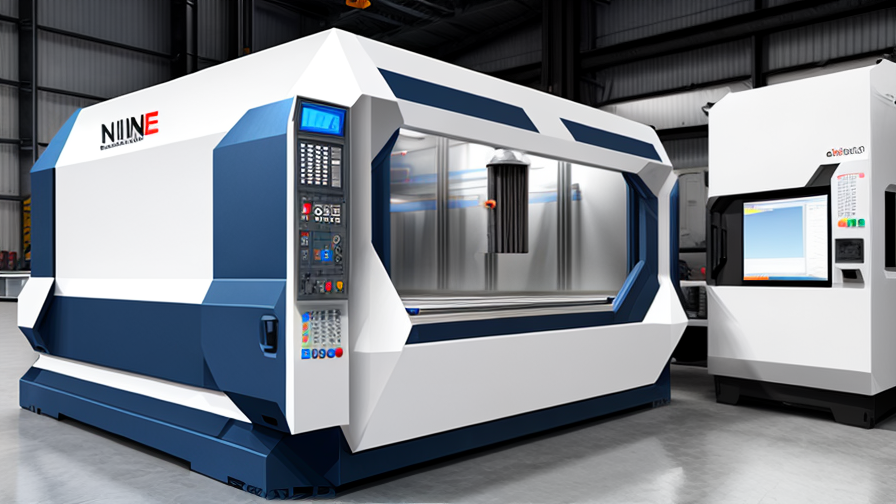
The Work Process and how to use parts of a cnc mill
The work process of a CNC mill involves various stages from preparing the design to operating the machine. Here are the key steps and how to use different parts of a CNC mill:
1. Design Preparation: Begin by creating a digital model of the desired part using Computer-Aided Design (CAD) software. This design should include dimensions, features, and any specific instructions.
2. CAM Programming: Once the design is ready, convert it into machine-readable code using Computer-Aided Manufacturing (CAM) software. This code contains instructions for the CNC mill, specifying tool paths, cutting depths, feed rates, and other parameters.
3. Machine Setup: Ensure that the CNC mill is properly set up for the job. This involves securing the workpiece onto the mill’s table using vises, clamps, or fixtures. Align the workpiece accurately using edge finders, dial indicators, or probing systems.
4. Tool Selection: Choose the appropriate cutting tools for the job based on the material and design requirements. Install the selected tools into the tool holders, ensuring they are securely tightened.
5. Zeroing and Work Offsets: Establish the machine’s reference points by zeroing the tool and work offsets. This involves determining the origin point (X, Y, and Z coordinates) where the cutting tool will start the operation. Set these offsets in the CNC mill’s controller using the provided interface.
6. Workpiece Alignment: Perform a test run to check if the tool’s path aligns with the design on the workpiece. Adjust the alignment if necessary by modifying the work offsets.
7. Cutting Operations: Start the CNC mill by loading the previously generated code into the controller. The machine will then begin executing the programmed tool paths, cutting, drilling, or milling the workpiece as required.
8. Monitoring and Troubleshooting: Continuously monitor the cutting operation, ensuring that the machine is running smoothly and the workpiece is progressing as intended. Be prepared to troubleshoot any unexpected issues, such as tool breakage or incorrect cuts.
9. Finishing and Inspection: After completing the machining process, remove the finished part from the CNC mill. Inspect it for any defects or deviations from the desired specifications. Make any necessary adjustments or corrections as needed.
By following these steps and familiarizing yourself with the various parts of a CNC mill, you can successfully operate the machine and produce precise and accurate parts. Remember to always follow safety guidelines and best practices when working with CNC mills.
Quality Testing Methods for parts of a cnc mill and how to control the quality
Quality testing methods for parts of a CNC mill include dimensional inspection, surface finish evaluation, material testing, and functional testing. These methods ensure that the parts meet the required specifications and perform optimally.
Dimensional inspection involves using measuring instruments such as calipers, micrometers, and coordinate measuring machines to verify the dimensions of the machined parts. This ensures that the parts are within the specified tolerances and meet the design requirements.
Surface finish evaluation is performed using techniques like profilometers and surface roughness testers to assess the smoothness and texture of the machined surfaces. This ensures that the parts have the desired surface finish, which is crucial for their function and aesthetics.
Material testing involves verifying the material properties of the parts, such as hardness, tensile strength, and ductility. Material testing ensures that the parts are made from the appropriate materials and possess the necessary mechanical properties for their intended application.
Functional testing is performed by assembling the CNC mill and running it to ensure that all the parts function correctly and perform their intended tasks. This involves testing the movement of axes, spindle performance, accuracy of tool positioning, and overall machine functionality.
To control the quality, it is essential to implement a robust quality management system. This includes defining quality standards, establishing inspection protocols, and training operators on quality requirements. Regular calibration of measuring instruments is necessary to ensure accurate measurements.
Implementing statistical process control techniques, such as control charts and process capability analysis, can help monitor the quality and identify any process variations. Any deviations from the desired quality standards should be addressed promptly, and corrective actions should be taken to prevent the recurrence of defects.
Supplier management and quality audits are crucial to maintain the quality of the parts. Regular audits of suppliers’ processes and quality management systems enable effective control of the supply chain and ensure that the parts received from suppliers meet the required quality standards.
By implementing these quality testing methods and control measures, manufacturers can ensure that the parts of their CNC mills are of high quality, which leads to improved performance, reliability, and customer satisfaction.
parts of a cnc mill Sample Policy and Post-Purchase Considerations for parts of a cnc mill from China
Sample Policy:
When purchasing parts for a CNC mill from China, it is essential to establish certain guidelines to ensure quality and minimize potential risks. The following sample policy can be implemented:
1. Supplier Qualification: Thoroughly research potential suppliers and assess their experience, reputation, and certifications in the CNC mill industry. Request samples or visit their facilities to verify their manufacturing capabilities and quality control processes.
2. Quality Assurance: Implement a stringent quality control system that includes pre-shipment inspections, testing procedures, and traceability of parts. Ensure that the supplier adheres to international standards and can provide certifications such as ISO 9001.
3. Intellectual Property Protection: Clearly define intellectual property ownership and require the supplier to sign a non-disclosure agreement to protect proprietary information and prevent counterfeiting.
4. Warranty and Returns: Establish a clear warranty policy with the supplier, including repair, replacement, or refund options for defective or non-conforming parts. Specify the duration of the warranty period and the required documentation for returns and refunds.
5. Communication and Language: Ensure effective communication by clarifying language requirements. If language barriers exist, consider employing an interpreter or utilizing translation services to minimize misunderstandings or miscommunications.
Post-Purchase Considerations:
After purchasing parts for a CNC mill from China, several considerations should be taken into account to ensure a smooth transition and optimal machine performance:
1. Inventory Management: Create an inventory management system to track parts and reorder when necessary. Maintain an appropriate inventory level to prevent downtime in case of unexpected part failures.
2. Documentation and Manuals: Request comprehensive technical documentation and user manuals from the supplier to assist in installation, troubleshooting, and maintenance. Translate these documents if necessary to ensure understanding.
3. Training and Support: Arrange for training sessions or seek expert assistance to ensure that personnel responsible for CNC mill operation and maintenance have the necessary skills and knowledge. Consult the supplier for support or engage professional technicians when required.
4. Spare Parts Availability: Enquire about the availability and lead time of spare parts from the supplier. Stocking critical spare parts in advance can prevent prolonged downtime in case of unexpected failures.
5. Continuous Improvement: Periodically evaluate machine performance and parts quality. Provide feedback to the supplier for any identified issues or areas for improvement. Maintain a relationship with the supplier by regular communication, fostering a collaborative partnership for future business endeavors.
By following a comprehensive sample policy and considering important post-purchase factors, the procurement of parts for a CNC mill from China can be efficient, cost-effective, and yield long-term reliability and performance.
Sourcing parts of a cnc mill from China: Opportunities, Risks, and Key Players
Sourcing parts of a CNC mill from China can offer various opportunities, including cost savings, a wide range of suppliers, and access to advanced manufacturing technologies. China has become a global manufacturing hub, offering competitive pricing due to its lower labor costs and economies of scale. This can significantly reduce the overall production costs of a CNC mill.
In addition, China boasts a vast network of suppliers, making it easier to find specific parts and components required for a CNC mill. This, coupled with its efficient supply chain management, allows for shorter lead times and faster product delivery.
China also leads in the adoption and development of advanced manufacturing technologies. This means that sourcing parts from China can provide access to cutting-edge CNC mill components and innovations, giving businesses a competitive edge in terms of performance and efficiency.
However, there are certain risks associated with sourcing parts from China. One significant concern is the quality of the parts. It is essential to carefully assess and verify the credibility and reliability of suppliers to ensure that the parts meet the required standards. Additionally, communication challenges, such as language barriers and cultural differences, may arise, which can affect effective negotiation and timely response to queries or issues.
When it comes to key players in the Chinese CNC mill parts market, some prominent manufacturers and suppliers include Shanghai SIEG Machinery Co., Ltd, Shenzhen Joint Industry Co., Ltd, and Ningbo Blin Machinery Co., Ltd. These companies have built a solid reputation and offer a wide range of CNC mill components, ranging from motors and spindles to ball screws and control systems.
In conclusion, sourcing parts for a CNC mill from China presents opportunities for cost savings, access to a wide range of suppliers, and advanced manufacturing technologies. However, it is crucial to carefully assess risks related to quality control and communication challenges. Being aware of key players in the market is also essential when seeking reliable sources for CNC mill parts in China.
How to find and select reliable parts of a cnc mill manufacturers in China,use google search manufacturers and suppliers
When searching for reliable CNC mill manufacturers in China, using Google search is indeed a great starting point. Here are some key steps to take:
1. Begin by searching for relevant keywords like “CNC mill manufacturers in China” or “CNC mill suppliers in China.” This will provide you with a list of potential companies to explore further.
2. Next, visit the websites of these manufacturers/suppliers to gather information about their background, experience, production capabilities, and product offerings. Look for essential details such as company history, certifications, available machinery, and any testimonials or case studies.
3. While on their website, check if they have a dedicated page for their CNC mill products. Here you can find information about the types of CNC mills they produce, their specifications, and performance attributes. Pay attention to the quality of the technical information provided, such as details about the materials used, precision levels, and manufacturing processes.
4. Look for any accreditation or certifications on their website. Reliable manufacturers will often have certifications related to quality management systems, such as ISO 9001, which ensures that they adhere to strict quality standards.
5. It is also important to assess the manufacturer’s production capacity and capabilities. Look for indications that they are well-rounded and capable of handling your specific requirements, such as having a wide range of CNC milling machines, sufficient workforce, and an advanced quality control system.
6. During your search, aim to find customer reviews or testimonials. Independent reviews can provide insights into the manufacturer’s reputation, the reliability of their products, and the level of customer satisfaction.
7. Contact the shortlisted manufacturers and inquire about their products, their ability to customize CNC mills according to your specific needs, lead times, pricing, and shipping terms. This will also give you an opportunity to assess their responsiveness and customer service.
8. Ask for samples or inquire about the possibility of visiting their factory. This will allow you to see firsthand the quality of the CNC mills they produce and evaluate their manufacturing processes.
By following these steps and conducting thorough research, you can confidently select a reliable CNC mill manufacturer in China that meets your specific requirements and quality standards.
How to check parts of a cnc mill manufacturers website reliable,use google chrome SEOquake check if ranking in top 10M
When trying to determine the reliability of a CNC mill manufacturer’s website, there are several steps you can follow. One useful tool is Google Chrome’s SEOquake extension, which can help analyze a website’s search engine ranking and popularity. Here is a step-by-step guide using SEOquake:
1. Install SEOquake: Open Google Chrome and search for “SEOquake Chrome extension.” Install the plugin by following the instructions.
2. Visit the manufacturer’s website: Open the website you want to check for reliability. Ensure that you browse various sections to get an overall understanding of the content and offerings.
3. Analyze Google search ranking: With the website open, activate the SEOquake extension by clicking on its icon in the toolbar. A summary of SEO data will appear on the right-hand side of the screen.
4. Check for Alexa Rank: Within the SEOquake summary, find the Alexa Rank section. This will provide an estimate of the website’s popularity based on global traffic. A lower Alexa Rank generally indicates higher popularity and reliability.
5. Verify if ranking in the top 10 million: SEOquake also provides the website’s approximate ranking in the top 10 million websites. If the website ranks within this range, it signifies a good level of popularity and activity.
6. Evaluate other SEO factors: SEOquake offers additional metrics that can help assess the website’s optimization and reliability. Pay attention to factors like the number of pages indexed by search engines, domain age, and the presence of backlinks.
7. Consider user experience: Apart from SEO, it is essential to evaluate the website’s overall user experience. Check for clear information about the company, detailed product descriptions, contact information, and reputable customer reviews or testimonials.
By following these steps, you can swiftly assess the reliability of a CNC mill manufacturer’s website. However, it’s important to note that this process provides a general indication and should be complemented with other research methods for a comprehensive evaluation.
Top 10 parts of a cnc mill manufacturers in China with each 160 words introduce products,then use markdown create table compare
1. Haas Automation Inc.: Haas is a leading CNC mill manufacturer based in China. Their products are known for their high precision, durability, and reliability. Haas offers a wide range of CNC mills, including vertical mills, horizontal mills, and 5-axis mills. These machines are widely used in industries like automotive, aerospace, and medical.
2. DMG Mori: With a strong presence in the global market, DMG Mori is another top CNC mill manufacturer in China. Their machines are known for their advanced technology, superior performance, and high efficiency. DMG Mori offers a diverse range of CNC mills, such as universal milling machines, vertical machining centers, and horizontal machining centers.
3. Mazak: Mazak is a well-established CNC mill manufacturer with a strong presence in China. Their machines are known for their exceptional quality, precision, and productivity. Mazak offers a wide range of CNC mills, including vertical centers, horizontal centers, and multi-tasking machines.
4. Doosan: Doosan is a renowned CNC mill manufacturer in China, known for their high-quality machines. Doosan’s CNC mills are known for their excellent performance, stability, and durability. They offer a wide range of CNC mills, including vertical mills, horizontal mills, and double column mills.
5. Fanuc: Fanuc is a leading manufacturer of CNC mills in China. Their machines are known for their exceptional precision, speed, and reliability. Fanuc offers a range of CNC mills, including vertical mills, horizontal mills, and 5-axis mills.
6. Okuma: Okuma is a well-known CNC mill manufacturer that has a strong presence in China. Their machines are known for their high accuracy, stability, and durability. Okuma offers a diverse range of CNC mills, including vertical mills, horizontal mills, and multitasking machines.
7. Makino: Makino is a reputable CNC mill manufacturer in China, specializing in high-performance machining solutions. Their machines are known for their superior precision, quality, and efficiency. Makino offers a range of CNC mills, including vertical mills, horizontal mills, and 5-axis mills.
8. Brother: Brother is a well-established CNC mill manufacturer in China, offering a range of high-quality machines. Their CNC mills are known for their high-speed machining capabilities, reliability, and versatility. Brother offers a wide range of CNC mills, including vertical mills, horizontal mills, and multi-tasking machines.
9. Taiwan Takisawa: Taiwan Takisawa is a leading CNC mill manufacturer in China, specializing in high-precision machines. Their CNC mills are known for their exceptional accuracy, stability, and productivity. Taiwan Takisawa offers a diverse range of CNC mills, including vertical mills, horizontal mills, and 5-axis mills.
10. Chiron: Chiron is a renowned CNC mill manufacturer known for their cutting-edge technology and innovative solutions. Their machines are known for their high precision, speed, and versatility. Chiron offers a diverse range of CNC mills, including vertical mills, horizontal mills, and multitasking machines.
| Manufacturer | Key Features |
|——————-|—————————————————————————————————|
| Haas Automation Inc. | High precision, durability, and reliability, wide range of vertical, horizontal, and 5-axis mills. |
| DMG Mori | Advanced technology, superior performance, and high efficiency, offering universal to 5-axis mills.|
| Mazak | Exceptional quality, precision, and productivity, range of vertical, horizontal, and multitasking mills. |
| Doosan | High-quality machines, excellent performance, stability, and durability, variety of vertical, horizontal, and double column mills. |
| Fanuc | Exceptional precision, speed, and reliability, range of vertical, horizontal, and 5-axis mills. |
| Okuma | High accuracy, stability, and durability, offering vertical, horizontal, and multitasking mills. |
| Makino | Superior precision, quality, and efficiency, range of vertical, horizontal, and 5-axis mills. |
| Brother | High-speed machining capabilities, reliability, and versatility, variety of vertical, horizontal, and multi-tasking mills. |
| Taiwan Takisawa | Exceptional accuracy, stability, and productivity, offering vertical, horizontal, and 5-axis mills. |
| Chiron | Cutting-edge technology, high precision, speed, and versatility, range of vertical, horizontal, and multitasking mills. |
Background Research for parts of a cnc mill manufacturers Companies in China, use qcc.com archive.org importyeti.com
When it comes to finding information about CNC mill manufacturers in China, there are several reliable sources that can be used for background research. These include QCC.com, Archive.org, and Importyeti.com. These platforms provide valuable insights into the companies, their history, products, and reputation. Here is a brief overview of each source:
QCC.com is a business information platform in China that offers data on companies, including their registration details, financial information, and legal records. It can be used to verify the legitimacy of a CNC mill manufacturer, such as checking their business license, ownership, and any legal disputes they may have been involved in.
Archive.org is an online platform that archives web pages, allowing users to view snapshots of websites at different points in time. This is particularly useful when researching CNC mill manufacturers in China, as it provides access to past versions of a company’s website. By comparing different snapshots, one can track the company’s development, product range, and any changes in their business direction over time.
Importyeti.com is a platform that provides detailed import/export records, including shipment data, for various companies in China. This database can be used to investigate the export activities of CNC mill manufacturers, such as their customer base, shipment frequency, and destinations. It helps assess their experience in international trade and potential reliability as a supplier.
These sources should be utilized efficiently, focusing on important information about the company, such as its establishment date, manufacturing capabilities, product certifications, export experience, and customer reviews or testimonials. It is recommended to condense the research into concise points, using not more than 300 words, to provide a brief yet informative background on the CNC mill manufacturers in China.
Leveraging Trade Shows and Expos for parts of a cnc mill Sourcing in China
Trade shows and expos are excellent platforms for sourcing parts of a CNC mill in China. These events provide a unique opportunity to connect with numerous manufacturers, suppliers, and industry professionals under one roof. By leveraging trade shows and expos, businesses can optimize their sourcing process and find quality components for their CNC mill projects.
To make the most of these events, it is crucial to plan and research the trade shows and expos that are relevant to CNC mill parts sourcing. Identifying events that specifically cater to manufacturing, machinery, or technology will help in targeting the right exhibitors and suppliers.
When attending trade shows and expos, it is important to come prepared with a comprehensive list of required CNC mill parts and specifications. This will allow for productive conversations with exhibitors, enabling them to understand the specific needs and offer suitable solutions. Take the opportunity to establish strong relationships with potential suppliers, as it can lead to long-term partnerships for future sourcing needs.
One key advantage of attending these events is the ability to physically inspect the parts and assess their quality. This minimizes the risk of receiving substandard components by ensuring they meet the required standards and specifications. Discussions with suppliers can also help in understanding their production processes, quality control measures, and delivery timelines.
Furthermore, trade shows and expos often feature seminars, workshops, and demonstrations, providing invaluable insights into the latest trends and advancements in CNC mill technology. These knowledge-sharing sessions enable businesses to stay updated on industry developments and make informed decisions during sourcing.
In conclusion, trade shows and expos in China offer an efficient and effective approach to sourcing parts for CNC mills. By leveraging these events, businesses can connect with a wide range of suppliers, examine product quality firsthand, establish meaningful relationships, and stay informed about industry trends. Successfully exploiting these opportunities can lead to cost-effective and reliable sourcing solutions for CNC mill components.
The Role of Agents and Sourcing Companies in Facilitating parts of a cnc mill Purchases from China
Agents and sourcing companies play a crucial role in facilitating the purchase of CNC mill parts from China. These intermediaries act as a bridge between the suppliers in China and the buyers, making the procurement process more efficient and manageable.
Firstly, agents and sourcing companies have an extensive network of suppliers in China. They have already established relationships with these suppliers, which allows them to access a wide range of options for CNC mill parts. This enables buyers to have access to a diverse pool of products, ensuring that they can find the components that meet their specific requirements.
Furthermore, agents and sourcing companies have local market knowledge and expertise. They understand the intricacies of the Chinese manufacturing industry, such as the quality standards, pricing structures, and regulatory requirements. This knowledge is invaluable in ensuring that the buyers receive high-quality products at competitive prices and in compliance with the necessary regulations.
Another advantage of using agents and sourcing companies is that they can provide support in terms of negotiation and communication. They are fluent in the Chinese language and are well-versed in the cultural norms and business practices. This enables effective communication with suppliers, ensuring that the buyers’ needs and expectations are clearly understood and addressed. Additionally, agents can negotiate the best terms, including pricing, lead times, and shipping arrangements, on behalf of the buyers, leveraging their expertise and relationships.
Moreover, agents and sourcing companies also play a vital role in quality control and inspection of the purchased parts. They can conduct factory audits, quality checks, and pre-shipment inspections to ensure that the products meet the required standards. This helps buyers to mitigate the risk of receiving faulty or subpar components and ensures that the entire procurement process is transparent and reliable.
In summary, agents and sourcing companies are indispensable in facilitating the purchase of CNC mill parts from China. Their extensive network, local market knowledge, negotiation skills, and quality control capabilities streamline the procurement process, enabling buyers to acquire the required components efficiently and effectively.
Price Cost Research for parts of a cnc mill manufacturers Companies in China, use temu.com and 1688.com
When it comes to sourcing parts for CNC mill manufacturers in China, temu.com and 1688.com are two popular platforms that can provide valuable price and cost research data. These platforms enable businesses to connect with numerous suppliers and manufacturers, offering a wide range of CNC mill parts.
Temu.com, also known as the “Global Mechanical and Electrical Equipment Supplier Platform,” provides access to a vast directory of verified suppliers, allowing businesses to search for specific CNC mill parts based on their requirements. The platform offers a variety of tools and features to facilitate price and cost research, such as product specification details, supplier ratings and reviews, and real-time communication options.
1688.com, on the other hand, is a comprehensive online marketplace owned by Alibaba Group, primarily catering to the domestic market in China. It connects buyers with a vast network of suppliers and manufacturers, offering an extensive range of products, including CNC mill parts. Businesses can use the platform to research product specifications, compare prices from different sellers, and analyze the cost of bulk orders.
Both platforms support various search parameters, such as product type, material, dimensions, and quantity, enabling businesses to narrow down their search for CNC mill parts based on specific requirements. This helps in obtaining accurate price quotes and estimating the overall cost of procurement.
By leveraging temu.com and 1688.com, CNC mill manufacturers can effectively research the prices and costs associated with sourcing parts from numerous suppliers. They can evaluate different options, assess the quality and reliability of suppliers through ratings and reviews, and make informed decisions to optimize their supply chain and improve cost-efficiency.
In conclusion, temu.com and 1688.com are reputable online platforms in China that provide valuable price and cost research data for CNC mill parts. By utilizing these platforms, manufacturers can streamline their sourcing process and enhance their overall profitability.
Shipping Cost for parts of a cnc mill import from China
When importing parts of a CNC mill from China, shipping costs play a significant role. Several factors influence the shipping cost, including the weight and dimensions of the parts, the shipping method chosen, and any additional services required.
The weight and dimensions of the parts are primary determinants of shipping cost. As CNC mill parts are typically heavy and bulky, they may fall into a higher weight category, resulting in increased shipping fees. It is crucial to accurately measure and weigh the parts to estimate the shipping cost correctly.
The shipping method chosen is another crucial consideration. There are several shipping options, such as air freight, sea freight, and express delivery. Air freight is often the fastest but most expensive option, suitable for urgent or time-sensitive shipments. Sea freight is more cost-effective but has a longer transit time. Express delivery services like DHL or FedEx can strike a balance between speed and cost for smaller shipments.
It is also essential to take into account any additional services required. These may include customs clearance, insurance, or delivery to a specific location. Customs clearance involves paperwork and fees associated with customs regulations. Insurance is crucial to protect the goods in transit, and the cost is usually a percentage of the total value being shipped. Lastly, if the destination requires delivery to a specific location, such as a residential address, additional fees may be incurred.
To estimate shipping costs accurately, it is recommended to consult with freight forwarders or shipping companies. They can provide detailed quotations based on the specific requirements and negotiate the best rates for the shipment. Comparing multiple quotes can help in selecting the most cost-effective shipping option.
In conclusion, when importing parts of a CNC mill from China, one should consider the weight and dimensions of the parts, choose a suitable shipping method, and account for any additional services required. Consulting freight forwarders and obtaining multiple quotations can aid in keeping shipping costs within budget.
Compare China and Other parts of a cnc mill Markets: Products Quality and Price,Visible and Hidden Costs
China has emerged as a major player in the CNC mill market, with its products being known for their competitive prices. However, when comparing China to other parts of the world, there are several factors to consider, including product quality, price, and visible and hidden costs.
In terms of product quality, China has made significant strides in recent years. Chinese manufacturers now offer CNC mills that can meet global quality standards. However, it is still important to conduct thorough research and choose reliable suppliers to ensure consistent quality. Other parts of the world, such as Europe and the United States, have long-standing reputations for producing high-quality CNC mills. These markets are often associated with more rigorous quality control processes, resulting in reliable and durable products.
When it comes to price, China is known for cost competitiveness. Chinese manufacturers leverage economies of scale and lower labor costs to offer CNC mills at relatively lower prices compared to other markets. This cost advantage makes Chinese CNC mills attractive for price-sensitive customers. On the other hand, other parts of the world often prioritize quality and precision over price, resulting in higher-priced CNC mills. Customers willing to invest more for superior performance and durability may opt for these alternatives.
Visible costs, such as the initial purchase price, are generally comparable across markets. However, it is the hidden costs that should be carefully considered. These include shipping and import duties, warranty and maintenance costs, and potential language or communication barriers. China’s proximity to most global markets gives it an advantage in terms of lower shipping costs, especially for customers located in Asia. However, import duties and taxes can offset this advantage in certain countries. Additionally, for customers who value post-purchase support, the availability and cost of warranty and maintenance services should be factored into the decision-making process.
In conclusion, China’s CNC mill market offers competitive products in terms of quality and price. Chinese manufacturers have made significant progress in meeting global quality standards, but careful supplier selection is crucial. China’s cost advantage and proximity can make it an attractive option for certain customers. However, customers prioritizing product longevity, precision, and post-purchase support may opt for other parts of the world, where higher-quality CNC mills are available, albeit at a higher price point. Regardless of the market chosen, it is essential to consider both visible and hidden costs that may impact the overall value proposition.
Understanding Pricing and Payment Terms for parts of a cnc mill: A Comparative Guide to Get the Best Deal
When it comes to purchasing parts for a CNC mill, understanding pricing and payment terms is essential to ensure you get the best deal. Here is a comparative guide to help you navigate through this process:
1. Pricing:
– Compare prices from multiple suppliers: Contact different suppliers and request quotes for the required parts. This will give you an idea of the average market price.
– Consider quality vs. price: Cheaper parts may save you money upfront, but they could be of lower quality and wear out quickly. Balance the cost with the desired quality to make a wise decision.
– Volume discounts: Inquire about potential discounts for bulk orders. Many suppliers offer reduced prices for larger quantities.
– Refurbished or used parts: If on a tight budget, consider purchasing refurbished or used parts. However, ensure they are in good condition and come with a warranty if possible.
2. Payment Terms:
– Payment methods: Understand the available payment methods offered by the suppliers. This could include credit cards, wire transfers, or payment platforms like PayPal. Choose the method that is most convenient and secure for you.
– Payment schedule: Negotiate payment terms based on order size and supplier policy. Some suppliers may require partial payment upfront and the remainder upon delivery or acceptance of the parts.
– Trade credit: Establishing a good relationship with a supplier may lead to flexible payment terms, such as trade credit. This grants you a specified period to pay invoices after receiving the goods.
– Financing options: Explore financing options if the total order value is substantial. Some suppliers may offer installment plans or partner with financial institutions to provide loans at competitive rates.
Remember to thoroughly research potential suppliers and read customer reviews before making a final decision. Additionally, consider factors such as shipping costs, delivery time, and after-sales support when evaluating the overall value of a deal.
In conclusion, understanding pricing and payment terms is crucial when purchasing parts for a CNC mill. Take the time to compare prices, consider quality, inquire about discounts, and negotiate favorable payment terms. By following this comparative guide, you’ll be well-equipped to secure the best deal for your CNC mill parts.
Chinese Regulations and Industry Standards Certifications for parts of a cnc mill,Import Regulations and Customs for parts of a cnc mill from China
When it comes to Chinese regulations and industry standards certifications for parts of a CNC mill, several important guidelines must be followed. The main standard reference for CNC machine tools in China is the GB/T 4347.2-2015, which outlines the general technical conditions for precision machine tools. This standard covers various aspects such as design, manufacturing, installation, testing, and operation.
In addition to the general standards, specific industry standards for different types of parts within a CNC mill may also apply. For instance, the CNC machine spindle may need to comply with the GB/T 30149-2013 standard, which focuses specifically on the technical requirements for machine tool spindles.
Moreover, the production and sale of CNC mill parts in China require certain certifications to ensure compliance with safety and quality standards. The most common certification for mechanical products in China is the China Compulsory Certification (CCC) mark. This mark helps ensure that the products meet essential safety, environmental, and quality requirements set by the Chinese government.
When importing parts of a CNC mill from China, it is crucial to be aware of the import regulations and customs procedures. The first step is to classify the imported goods according to the Harmonized System (HS) code, which will determine the applicable import duties and regulations.
Additionally, it is necessary to provide all relevant documentation for customs clearance. This includes commercial invoices, packing lists, bill of lading or airway bill, and other supporting documents such as certificates of origin, inspection reports, and certificates of conformity. It is important to note that certain CNC mill parts may require additional import licenses or permits depending on their nature or specific regulations in the importing country.
To ensure a smooth import process, it is highly advisable to work with a reliable customs broker or freight forwarder who can guide you through the necessary procedures and help navigate any potential challenges or complications.
In conclusion, adhering to Chinese regulations and industry standards certifications is crucial when dealing with parts of a CNC mill. Additionally, understanding import regulations and customs procedures is vital to successfully import these parts from China. Collaborating with experienced professionals in the field can ensure compliance and simplify the importation process.
Sustainability and Environmental Considerations in parts of a cnc mill Manufacturing
Sustainability and environmental considerations play a crucial role in the manufacturing process of CNC mills. CNC mills, or Computer Numerical Control mills, are machines used to fabricate various parts and components with high precision and accuracy. Here are some key areas where sustainability and environmental factors are addressed in the CNC mill manufacturing process:
1. Material Selection: CNC mills are typically constructed using a variety of materials such as metals and plastics. In the context of sustainability, manufacturers must consider the ecological impact of their material choices. Opting for more environmentally friendly materials, such as recycled or renewable resources, can help reduce the overall carbon footprint of the CNC mill.
2. Energy Efficiency: CNC mills consume significant amounts of energy during operation. Manufacturers can incorporate design features that enhance energy efficiency, such as advanced motor systems and optimized power management. Additionally, integrating renewable energy sources into the manufacturing plant can further reduce carbon emissions associated with the CNC mill’s energy consumption.
3. Waste Reduction: CNC milling generates waste, including scrap metal shavings and plastic remnants. Implementing waste management strategies, such as recycling and reuse programs, can significantly minimize the amount of waste produced during the manufacturing process. Recycling materials not only reduces environmental impact but also helps lower costs by decreasing the need for new raw materials.
4. Emissions Control: Manufacturing processes, including CNC milling, can produce air and water pollution. To mitigate environmental impact, manufacturers can incorporate emission control technologies. Advanced filtration systems can remove harmful particles from air emissions, while wastewater treatment processes can effectively manage any pollutants discharged from the milling process.
5. Product Lifecycle Analysis: Sustainability considerations extend beyond the manufacturing phase. Conducting a comprehensive lifecycle analysis of CNC mills helps identify areas for improvement throughout their lifespan. Companies can enhance product durability, promote repairability, and facilitate end-of-life recycling, allowing for a more sustainable product.
In conclusion, sustainability and environmental considerations are vital in CNC mill manufacturing. Companies should focus on material selection, energy efficiency, waste reduction, emissions control, and product lifecycle analysis to ensure that CNC mills are manufactured with minimal environmental impact. By incorporating sustainability into their practices, manufacturers can contribute to a more environmentally sustainable future.
List The Evolution history of “parts of a cnc mill”
The history of CNC milling machines can be traced back to the early 1950s when the concept of computer numerical control (CNC) was introduced. However, the evolution of the various parts of a CNC mill can be seen through the following stages:
1. Manual Milling Machines: Before CNC technology, milling machines operated manually. Operators would use specialized tools to manipulate the workpiece and milling cutters to carve out desired shapes.
2. Numerical Control (NC) Systems: In the late 1940s, the first numerical control systems were developed. These systems used punched paper tapes or magnetic tapes to control the movement of milling machine axes. This marked the beginning of automation in milling operations.
3. Computer-Aided Manufacturing (CAM): In the 1960s, computer technology began to be integrated into milling machines. CAM software was developed to generate instructions for the milling machine based on computer models of the desired part. This eliminated the need for manual programming and improved accuracy.
4. Servo Drives: In the 1970s, servo drives were introduced, replacing the traditional drive systems. Servo drives improved precision and allowed for more complex movements of the milling machine axes, resulting in enhanced machining capabilities.
5. CAD/CAM Integration: With the advancement of computer-aided design (CAD) software, CAD/CAM integration became more prevalent in the 1980s. This enabled seamless transfer of digital designs to the milling machine, reducing manual intervention and increasing efficiency.
6. Multi-Axis Machining: As technology progressed, the number of axes on milling machines increased. Traditional 3-axis machines evolved into 4, 5, and even 6-axis machines, allowing for more intricate part designs and enhanced versatility.
7. High-Speed Machining: In the 1990s, high-speed machining became a significant development in CNC milling. With advancements in spindle and tooling technology, milling machines were able to achieve faster cutting speeds without compromising accuracy.
8. CNC Controller Advancements: The development of more powerful and sophisticated CNC controllers allowed for increased processing capabilities and improved user interfaces. Today, intuitive touchscreens and advanced software greatly simplify the programming and operation of CNC mills.
In summary, CNC milling machines have evolved from manual operations to highly automated and precise machines. Numerical control, computer-aided manufacturing, servo drives, CAD/CAM integration, multi-axis machining, high-speed machining, and advanced CNC controllers have all contributed to the modern CNC mill’s capabilities in machining complex parts efficiently and accurately.
The Evolution and Market Trends in parts of a cnc mill Industry
The CNC milling industry has experienced significant evolution and market trends over the years, driven by advancements in technology and changing consumer demands.
One key evolution in the industry is the shift towards automation and improved efficiency. CNC mills have become more automated, with the integration of advanced control systems and computer-aided programming. This has led to increased precision, faster production times, and reduced human error. Additionally, the use of robotics and artificial intelligence has further enhanced the automation process, allowing for continuous operation and improved overall productivity.
Moreover, the market trends in the CNC milling industry have been influenced by the demand for customization and complex designs. Today, consumers are seeking unique and personalized products, which has led manufacturers to invest in advanced CNC mills capable of producing intricate and customized components. This trend has also been fueled by the rise of 3D printing technology, which complements CNC milling by offering additional design flexibility and prototyping capabilities.
Another market trend in the CNC milling industry is the growing focus on sustainability and environmentally-friendly practices. Manufacturers are increasingly adopting eco-friendly machining techniques and utilizing recycled materials. This not only addresses environmental concerns but also aligns with the changing preferences of consumers who are becoming more conscious of sustainability.
Furthermore, the industry has witnessed a consolidation of market players, with larger companies acquiring smaller ones to expand their market share and enhance their technological capabilities. This consolidation has led to increased competition, driving manufacturers to continually innovate and improve their CNC mills to stay ahead in the market.
In conclusion, the CNC milling industry has evolved significantly over time, with automation, customization, sustainability, and consolidation being key market trends. As technology continues to advance, we can expect further evolution in CNC mills, with improved precision, efficiency, and the integration of emerging technologies like machine learning and virtual reality.
Custom Private Labeling and Branding Opportunities with Chinese parts of a cnc mill Manufacturers
When it comes to custom private labeling and branding opportunities with Chinese manufacturers specializing in CNC milling parts, there are a plethora of options available. With a rapidly growing market for CNC milling machines, teaming up with Chinese manufacturers can provide significant advantages for businesses looking to expand their product offerings or establish their own brand identity.
One of the key benefits of partnering with Chinese manufacturers is the affordability and high-quality production they offer. Chinese manufacturers have expertise in producing CNC milling parts, utilizing advanced machinery and technology at competitive prices. They can provide businesses with a cost-effective solution for custom private labeling and branding, allowing them to stay competitive in the market.
Chinese manufacturers also offer flexibility in catering to unique branding requirements. Whether it’s customizing the design, adding branding elements, or incorporating specific features, they can efficiently cater to individual needs. Businesses can work closely with Chinese manufacturers to create personalized and branded CNC milling parts, ensuring the final product aligns with their specific vision and requirements.
In addition, Chinese manufacturers are experienced in international trade and possess a deep understanding of global markets. They can offer expert guidance on branding strategies and market insights, assisting businesses in effectively establishing their brand presence. This includes logo placement, packaging design, and incorporating unique branding features that resonate with target customers.
Furthermore, Chinese manufacturers often have an extensive network of suppliers, allowing businesses to source ancillary products required for their CNC milling parts. By streamlining the entire production process, businesses can maximize efficiency and minimize costs while maintaining consistent quality and branding.
Overall, partnering with Chinese manufacturers for custom private labeling and branding opportunities for CNC milling parts opens up a world of possibilities for businesses. They can leverage the expertise, cost-effectiveness, flexibility, and market insights offered by Chinese manufacturers to establish their own brand identity and expand their market reach. With the potential to create unique, high-quality products at affordable prices, businesses can stay competitive in the fast-paced world of CNC milling.
Tips for Procurement and Considerations when Purchasing parts of a cnc mill
When it comes to procurement for purchasing parts of a CNC mill, there are several tips and considerations to keep in mind. Here are some key points to help guide your purchasing process:
1. Identify your requirements: Determine the specific parts you need for your CNC mill, taking into account the machine’s specifications, such as its size, power requirements, and compatibility.
2. Research suppliers: Look for reputable suppliers who specialize in CNC mill parts. Consider factors such as their experience in the industry, quality of products, pricing, and customer reviews.
3. Quality assurance: Ensure that the parts you are purchasing meet industry standards and have proper quality certifications. Request samples or review previous customer testimonials to assess the quality of the supplier’s products.
4. Pricing and cost-effectiveness: Compare prices from different suppliers to ensure you are getting the best value for your money. However, keep in mind that quality and reliability should not be compromised solely for cost considerations.
5. Delivery time and logistics: Discuss the estimated delivery timelines with the supplier, as delays in receiving the parts can impact your production schedule. Additionally, check if the supplier provides reliable and efficient shipping options.
6. After-sales support: Inquire about the supplier’s customer service and support offerings. A supplier that provides assistance with installation, troubleshooting, and basic maintenance can save you time and hassle in the long run.
7. Compatibility and interchangeability: Ensure that the parts you are purchasing are compatible with your existing CNC mill and any other components or accessories you plan to use. Check for interchangeability options to increase flexibility and future upgrades.
8. Warranty and return policy: Understand the supplier’s warranty terms and conditions, including coverage duration and any specific limitations. Familiarize yourself with the return policy to address any potential issues or concerns with the purchased parts.
9. Technical support and documentation: Check if the supplier offers comprehensive technical documentation, including user manuals, assembly guides, and troubleshooting guides. Having access to these resources can assist in the maintenance and troubleshooting process.
10. Future expansion and upgrade options: Consider the potential for future expansions or upgrades to your CNC mill. Look for suppliers who offer a wide range of compatible parts and accessories, allowing for easy integration and scalability.
By following these tips and considering these factors, you can make an informed procurement decision when purchasing parts for your CNC mill while ensuring its optimal performance and longevity.
FAQs on Sourcing and Manufacturing parts of a cnc mill in China
1. Why should I consider sourcing and manufacturing parts of a CNC mill in China?
Sourcing and manufacturing parts of a CNC mill in China can offer several advantages. Firstly, China has a huge and experienced manufacturing industry with a wide range of capabilities. This allows for a comprehensive selection of high-quality parts at competitive prices. Additionally, China’s infrastructure and logistics networks support smooth export and delivery processes. Moreover, Chinese manufacturers often provide flexible production options, enabling customization and quick response to changing requirements.
2. How can I find suitable suppliers in China?
To find suitable suppliers, various methods can be employed. Online platforms like Alibaba, Global Sources, or Made-in-China offer extensive directories of verified manufacturers. It is important to thoroughly research potential suppliers, check their credentials, and read reviews before committing to any partnership. Additionally, attending trade shows in China, such as the Canton Fair, presents an opportunity to meet potential suppliers in person and evaluate their capabilities.
3. What should I consider when selecting a supplier?
When selecting a supplier, it is crucial to consider factors such as quality control processes, production capacity, lead times, pricing structure, communication skills, and the ability to handle any necessary certifications or regulations. Requesting samples or visiting the supplier’s facilities can help assess their manufacturing capabilities and quality standards. It is also wise to check if the supplier has experience in the specific type of part you require.
4. What are common challenges when manufacturing in China?
Language and cultural barriers can pose challenges in communication and understanding. It is advisable to have clear and detailed specifications, drawings, and written agreements to minimize misinterpretation. Quality control and ensuring consistent product quality can also be a concern, so implementing regular inspections and quality checks throughout the production process is crucial. Additionally, there may be occasional delays due to factors like holidays, unexpected regulations or logistics issues, which should be factored into the project timeline.
5. How can I ensure the protection of intellectual property?
Protecting intellectual property (IP) when manufacturing in China is a valid concern. It is recommended to work with reputable manufacturers that have proven records of IP protection. Non-disclosure agreements (NDAs) and confidentiality clauses should be in place to safeguard sensitive information. Registering trademarks, patents, or design rights in China can provide additional legal protection. Regular audits and monitoring of production processes can also help identify any potential IP infringements.
In conclusion, sourcing and manufacturing parts of a CNC mill in China can offer numerous benefits, including access to a vast manufacturing industry, competitive pricing, and flexibility. However, thorough research, supplier evaluation, and proper IP protection strategies are essential to ensure a successful and reliable manufacturing partnership.
Why contact sourcifychina.com get free quota from reliable parts of a cnc mill suppliers?
SourcifyChina.com offers a free quota from reliable parts of CNC mill suppliers for several reasons. Firstly, the company strives to build a trustworthy and reliable platform for sourcing products from China. As the CNC mill industry is highly specialized and requires precision and quality, SourcifyChina.com aims to connect buyers with reliable suppliers who can provide high-quality parts for CNC mills.
By providing a free quota, SourcifyChina.com allows buyers to evaluate the capabilities and pricing of different suppliers without any upfront costs. This enables buyers to make informed decisions about the most suitable supplier for their CNC mill parts sourcing needs, ensuring a smooth and successful procurement process.
Furthermore, offering a free quota allows SourcifyChina.com to differentiate itself from competitors and attract potential customers. By removing the financial barriers associated with obtaining quotes, SourcifyChina.com positions itself as a user-friendly and accessible platform for buyers, encouraging them to explore sourcing options without any monetary risk.
In addition, providing a limited quota of up to 300 words encourages buyers to submit clear and concise requests, which helps suppliers understand the requirements more efficiently. This streamlines the quotation process, saving time for both buyers and suppliers and increasing the overall efficiency of the sourcing experience.
Overall, SourcifyChina.com offers a free quota from reliable parts of CNC mill suppliers to establish trust, facilitate informed decision-making, attract customers, and streamline the quotation process. This approach aligns with their goal of providing a reliable and efficient platform for sourcing products from China.