Introduce about pcb assembly manufacturing guide,Qulity,Cost,Supplier,Certification,Market,Tips,FAQ
PCB assembly manufacturing guide refers to the process of assembling printed circuit boards (PCBs) with electronic components to create functional electronic devices. It is crucial to follow a comprehensive guide to ensure the quality, cost-effectiveness, and efficiency of the production process.
Quality is a crucial aspect of PCB assembly manufacturing. It is essential to use high-quality components and follow strict quality control measures throughout the manufacturing process. This helps in producing reliable and durable electronic devices that meet industry standards.
Cost is another important consideration in PCB assembly manufacturing. Careful planning, efficient production processes, and bulk purchasing can help reduce manufacturing costs. Working closely with suppliers can also aid in cost reduction through negotiation and exploring cost-effective alternatives without compromising quality.
Selecting the right supplier is critical for successful PCB assembly manufacturing. Identifying reliable and experienced suppliers is crucial to ensure on-time delivery of components, competitive pricing, and quality services. Conducting thorough research, evaluating supplier capabilities, and checking their track record are vital in making an informed decision.
Certification is also an essential aspect of PCB assembly manufacturing. Look for suppliers and manufacturers who possess relevant certifications such as ISO 9001, ISO 13485, and IPC-A-600 to ensure compliance with industry standards and requirements.
Understanding the market trends and demands is vital for PCB assembly manufacturing. Stay updated with the latest technological advancements, emerging market opportunities, and customer preferences to stay competitive and cater to evolving consumer needs.
Tips for PCB assembly manufacturing include proper component sourcing, effective project management, designing for manufacturability, and regular communication with suppliers. These practices contribute to efficient production processes and optimal output.
Frequently Asked Questions (FAQ) can cover various aspects of PCB assembly manufacturing, such as lead times, minimum order quantities, quality control measures, cost factors, certification requirements, and shipping options.
Overall, a well-executed PCB assembly manufacturing process, adhering to quality standards, cost optimization, and engaging reliable suppliers, can result in the production of high-quality electronic devices that meet customer expectations and find success in the dynamic market.
Types of pcb assembly manufacturing
There are several types of PCB assembly manufacturing processes that are commonly used in the electronics industry. These processes can be categorized into three main types: through-hole assembly, surface mount assembly, and mixed technology assembly.
1. Through-hole assembly: This is one of the oldest and most traditional methods of PCB assembly. Through-hole assembly involves the insertion of electronic components into pre-drilled holes on the PCB. The component leads are then soldered on the opposite side of the board to create a mechanical and electrical connection. This process is generally used for components that require high mechanical strength, such as large capacitors and power connectors. It is also suitable for components that need to dissipate heat efficiently.
2. Surface mount assembly (SMT): SMT is a more modern and widely used method of PCB assembly. It involves the placement of components directly onto the surface of the PCB, rather than through drilled holes. SMT components are smaller, lighter, and have shorter leads than through-hole components. The components are attached to the board using solder paste, which is applied to the solder pads, and then heated to melt the solder and create a connection. SMT assembly allows for higher component density, improved signal integrity, and automation, making it suitable for high-volume production.
3. Mixed technology assembly: As the name suggests, mixed technology assembly combines both through-hole and surface mount components on a single PCB. This method is used when a combination of component types is required to meet the design requirements. For example, through-hole components may be used for high-power or high-voltage applications, while SMT components are used for smaller, low-power components. Mixed technology assembly allows for flexibility in component selection and placement, enabling efficient use of space and cost optimization.
In conclusion, through-hole assembly, surface mount assembly, and mixed technology assembly are the three main types of PCB assembly manufacturing processes. Each process has its own advantages and is chosen based on the specific requirements of the design, volume of production, and cost considerations. As technology advances, new assembly methods may be developed to cater to the evolving needs of the electronics industry.
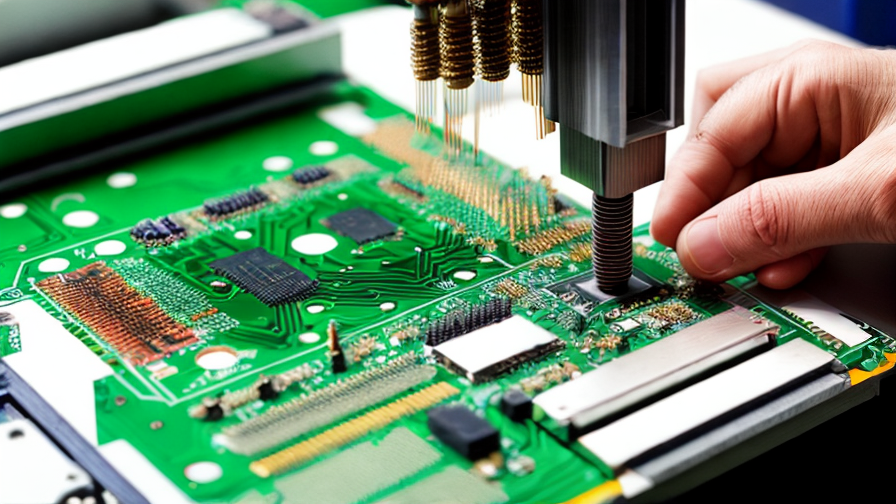
Pros and Cons of Using pcb assembly manufacturing
PCB assembly manufacturing, also known as printed circuit board assembly, is the process of mounting and soldering electronic components onto a PCB. This manufacturing method has become highly popular due to its efficiency and effectiveness. However, like any other manufacturing technique, there are some pros and cons associated with it.
Pros of PCB Assembly Manufacturing:
1. Efficiency: PCB assembly manufacturing is a highly efficient process as it allows for the mass production of printed circuit boards. This means that a large number of PCBs can be manufactured in a short period, which is crucial for meeting high-demand requirements.
2. Cost-effective: PCB assembly manufacturing offers cost advantages due to its ability to mass produce circuit boards. The economies of scale allow for competitive pricing, making it an affordable manufacturing option for businesses.
3. Quality control: By using automated machinery and advanced quality control measures, PCB assembly manufacturing ensures consistent and high-quality production. This reduces the chances of errors and faults, resulting in reliable and durable circuit boards.
4. Time-saving: PCB assembly manufacturing significantly reduces the time required for producing circuit boards. With the use of automated assembly machines, components can be soldered onto the PCB at a much faster rate, thus saving valuable time in the production process.
Cons of PCB Assembly Manufacturing:
1. Initial setup cost: The initial investment required for setting up a PCB assembly manufacturing facility can be high. The cost of equipment, machinery, and skilled labor can pose a financial challenge for small businesses or startups.
2. Prototype limitations: PCB assembly manufacturing is most suitable for high-volume production. It may not be cost-effective or practical for small-scale production or prototyping purposes, where flexibility and customization are essential.
3. Repairability challenges: In the event of a component failure or faulty connection, repairing a PCB assembled using surface mount technology (SMT) can be challenging. SMT components are small and densely packed, making it difficult to manually replace or repair them.
4. Design constraints: PCB assembly manufacturing imposes certain design constraints, especially when it comes to component sizes, spacing, and thermal management. These limitations may restrict the freedom of design and customization for certain electronic devices.
In conclusion, the use of PCB assembly manufacturing offers significant benefits in terms of efficiency, cost-effectiveness, quality control, and time-saving. However, it also comes with some limitations such as high setup costs, limitations for prototyping, repairability challenges, and design constraints. Businesses considering PCB assembly manufacturing should carefully weigh these pros and cons to make an informed decision based on their specific requirements and production volumes.
pcb assembly manufacturing Reference Specifications (varies for different product)
In PCB assembly manufacturing, reference specifications vary depending on the specific product being manufactured. These specifications are essential as they outline the required standards and guidelines to ensure the quality and reliability of the assembled PCBs.
The reference specifications typically cover various aspects of the manufacturing process, including design, materials, assembly, and testing. They provide detailed instructions to the manufacturer on how to produce the PCBs according to the desired requirements. Here are some key areas that may be addressed in the reference specifications:
1. Design: The reference specifications may specify the design requirements, such as the PCB layout, component placement, and signal integrity considerations. This ensures that the design is optimized for performance and manufacturability.
2. Materials: The specifications may specify the types and characteristics of the materials to be used for PCB fabrication, such as the substrate material, copper thickness, solder mask, and finish. These specifications ensure that the selected materials meet the desired quality and reliability standards.
3. Assembly: The specifications may outline the assembly process requirements, including component mounting, soldering techniques, and conformal coating. This ensures that the assembly is done correctly and meets the required industry standards.
4. Testing: The reference specifications may include testing requirements and procedures to verify the functionality and quality of the assembled PCBs. This may involve electrical testing, functional testing, and environmental testing to ensure that the PCBs meet the desired performance criteria.
It is important for manufacturers to closely adhere to these reference specifications to ensure consistency, quality, and reliability in the PCB assembly process. Deviating from these specifications may result in subpar performance, product failures, and customer dissatisfaction.
Each product may have its own unique set of reference specifications, tailored to its specific requirements. Manufacturers must carefully review and follow these specifications to ensure that the assembled PCBs meet the desired standards and customer expectations.
Overall, reference specifications in PCB assembly manufacturing are crucial documents that provide detailed guidance and instructions for producing high-quality and reliable PCB assemblies. They play a vital role in ensuring that the manufactured products meet the desired standards, performance criteria, and customer requirements.
Applications of pcb assembly manufacturing
PCB assembly manufacturing is a crucial process in the production of electronic devices. It involves the soldering of electronic components onto a printed circuit board (PCB), which serves as the foundation for the device’s functionality. There are several applications and industries that rely on PCB assembly manufacturing.
One of the main sectors is consumer electronics. This includes devices such as smartphones, tablets, laptops, televisions, and gaming consoles. PCB assembly manufacturing is essential in creating the intricate circuitry and connections required for these devices to function and communicate effectively.
Another vital application is in the automotive industry. Modern vehicles are equipped with various electronic components, from engine control units to entertainment systems. PCB assembly manufacturing ensures the reliable and efficient operation of these components, guaranteeing smooth driving experiences and enhanced vehicle functionalities.
The healthcare industry also heavily relies on PCB assembly manufacturing for medical devices and equipment. From diagnostic tools like MRI machines and ultrasound devices to life-saving equipment like pacemakers and defibrillators, PCB assembly plays a key role in ensuring the accuracy and safety of these devices.
Industrial automation is another field where PCB assembly manufacturing has significant importance. Automated factories and manufacturing plants employ various electronic devices and control systems to streamline operations and increase efficiency. PCBs are crucial in facilitating the communication and control of these automated processes, making operations more precise and reliable.
Furthermore, PCB assembly manufacturing is crucial in the aerospace and defense sectors. From communication systems and radar equipment to flight control systems and weapons guidance systems, PCBs enable the effective functioning of these critical applications. The reliability and durability of PCBs are crucial in ensuring the safety and success of these missions.
In conclusion, PCB assembly manufacturing has diverse applications and plays a fundamental role in various industries. From consumer electronics to automotive, healthcare, industrial automation, and aerospace and defense, PCBs are integral to the functionality and success of electronic devices and systems. As technology continues to advance, the demand for efficient and reliable PCB assembly manufacturing will only continue to grow.
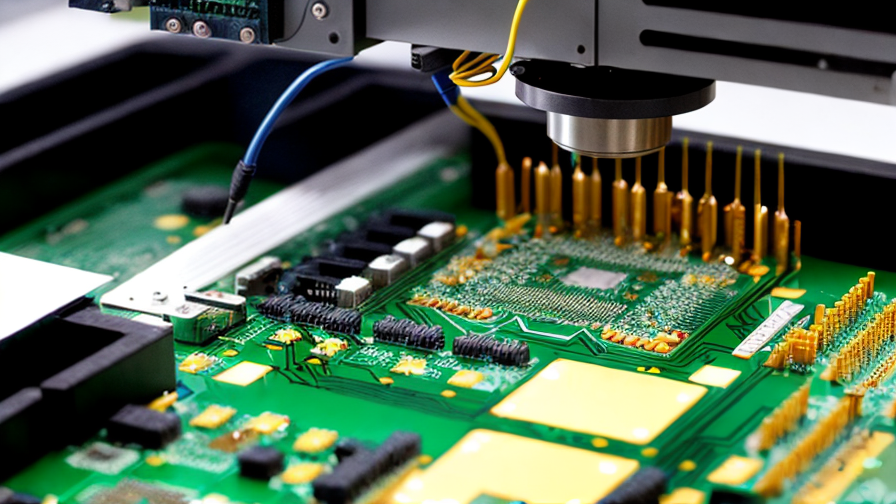
The Work Process and how to use pcb assembly manufacturing
PCB (Printed Circuit Board) assembly manufacturing involves the process of assembling various electronic components onto a PCB to create a functional electronic device. This process consists of several steps:
1. Designing the PCB: The initial step involves designing the PCB layout using computer-aided design (CAD) software. The design includes placing components, defining electrical connections, and assigning other specifications.
2. Component sourcing: Once the PCB layout is complete, the required electronic components are sourced. This includes choosing the right components based on the design requirements.
3. PCB fabrication: The PCB design is then transferred to a manufacturer who fabricates the PCB. This involves etching a copper-clad laminate to create the desired circuit pattern.
4. Solder paste application: Next, solder paste is precisely applied to the PCB using a stencil. The solder paste serves as an adhesive and helps to attach the components.
5. Component placement: The components are then picked and accurately placed onto the PCB using automated equipment like pick-and-place machines. This ensures precise positioning and alignment of the components.
6. Soldering: In this step, the PCB with components is subjected to a high-temperature reflow oven. The solder paste melts and forms a secure bond between the components and the PCB.
7. Inspection and testing: After soldering, the assembled PCB is inspected for any defects or soldering issues. Automated optical inspection (AOI) and X-ray inspection are commonly used methods for checking the quality of the assembly. Functional testing is also conducted to ensure that the PCB operates correctly.
8. Packaging and delivery: Once the inspection and testing are complete, the assembled PCBs are packaged appropriately, ensuring their protection during transportation. The PCBs are then delivered to the customer or the next stage of the manufacturing process.
To efficiently use PCB assembly manufacturing, it is crucial to provide clear and accurate design specifications, including component selection, layout, and electrical connections. Collaborating closely with the manufacturer throughout the process helps address any design or manufacturing challenges. Regularly reviewing and approving PCB prototypes and samples ensures the desired outcomes. Efficient communication and feedback exchanges enable timely adjustments and improvements. Finally, staying updated with the latest industry standards and best practices helps optimize the efficiency and reliability of the PCB assembly manufacturing process.
Quality Testing Methods for pcb assembly manufacturing and how to control the quality
When it comes to quality testing methods for PCB assembly manufacturing, there are several approaches that can be adopted to ensure the highest level of quality. These methods include automated optical inspection (AOI), X-ray inspection, functional testing, and in-circuit testing (ICT).
AOI is a popular method used to detect defects in assembled PCBs. It utilizes high-resolution cameras and advanced algorithms to inspect the components and solder joints for any anomalies. This method provides fast and accurate inspection, reducing the occurrence of human error.
X-ray inspection is another technique commonly used for quality control in PCB assembly manufacturing. It enables operators to check hidden defects such as solder joint integrity, shorts, or misplacements that cannot be easily detected by other methods. X-ray inspection is especially effective in ensuring the quality and reliability of products with high pin counts and complex component placements.
Functional testing involves testing the fully assembled PCBs to verify if they meet the desired functionality. This method evaluates the performance of the product under various conditions, simulating real-world usage. Functional testing helps identify any potential issues related to circuit design, components, or software, ensuring that the final product works as intended.
In-circuit testing (ICT) is a more extensive method that examines individual components and verifies their functionality. This testing technique involves the use of test probes, which make contact with specific points on the assembled PCB, allowing for precise measurements and analysis.
Apart from employing these quality testing methods, it is essential to establish robust quality control processes throughout the manufacturing process. This includes strict adherence to industry standards, such as IPC-A-610, which defines the acceptability criteria for electronic assemblies. Implementing comprehensive in-house quality control procedures, including thorough inspection of incoming materials, real-time defect tracking, and continuous process improvement initiatives, can help ensure consistent quality.
Furthermore, having a competent and trained workforce is crucial for maintaining high-quality standards. Regular training programs should be conducted to familiarize employees with quality control procedures, update them on new testing methods, and enhance their understanding of product specifications.
By implementing these quality testing methods and establishing effective quality control processes, manufacturers can ensure that their PCB assembly products meet the highest quality standards, resulting in customer satisfaction and continued business success.
pcb assembly manufacturing Sample Policy and Post-Purchase Considerations for pcb assembly manufacturing from China
Sample Policy and Post-Purchase Considerations for PCB Assembly Manufacturing from China:
At our company, we understand that PCB assembly manufacturing is a crucial part of your product development process. To ensure that you receive the highest quality products from our manufacturing facility in China, we have carefully laid out our sample policy and post-purchase considerations for your convenience and peace of mind.
Sample Policy:
1. We offer free samples of PCB assemblies for initial evaluation, allowing you to assess their quality and performance before placing a bulk order.
2. The number of free samples provided will depend on the complexity and cost of the assembly. Additional samples can be purchased at a reasonable cost.
3. Customers are responsible for bearing the shipping costs when requesting samples, but we can provide assistance in arranging reliable and cost-effective freight forwarding solutions.
Post-Purchase Considerations:
1. Our manufacturing experts are available to answer any questions or provide technical support throughout the production process.
2. We ensure on-time delivery of your PCB assemblies, adhering to the agreed-upon schedule and minimizing any potential delays.
3. Our quality control team meticulously inspects each assembly before shipment, guaranteeing that the final products meet your specifications and standards.
4. We offer a warranty period for any defects or malfunctions found in the PCB assemblies upon delivery. Our after-sales team will promptly address and resolve any issues in a professional and efficient manner.
While our manufacturing facility in China provides cost-effective solutions without compromising quality, we understand that concerns may arise regarding communication, potential language barriers, or cultural differences. To overcome these challenges, we have a dedicated customer support team proficient in English and experienced in intercultural communication to ensure smooth collaboration.
By implementing these sample policy and post-purchase considerations, we aim to provide a seamless experience for our customers engaging in PCB assembly manufacturing from China. With our commitment to high-quality products, technical support, and responsive customer service, we strive to build strong and mutually beneficial partnerships with our clients.
Sourcing pcb assembly manufacturing from China: Opportunities, Risks, and Key Players
Sourcing PCB assembly manufacturing from China can offer several opportunities to businesses. One of the major advantages is cost-effectiveness. China has a highly developed manufacturing sector with abundant raw materials and a large labor force, which results in lower production costs compared to many other countries. This cost advantage allows businesses to save significantly on their manufacturing expenses.
Another opportunity is the availability of a wide range of suppliers and manufacturers. China is home to numerous PCB assembly companies, offering a variety of services, capabilities, and technologies. This diversity provides businesses with access to a competitive market, allowing them to choose the most suitable manufacturer for their specific requirements.
However, sourcing PCB assembly manufacturing from China also comes with certain risks. One of the main concerns is product quality. While there are reputable and reliable manufacturers in China, there are also those who might compromise on quality to offer lower prices. It is crucial for businesses to carefully vet potential manufacturers, conduct thorough inspections, and establish quality control processes to ensure the final product meets their standards.
Additionally, there could be challenges in communication and language barriers. These can result in misunderstandings, delays, and even mistakes in the production process. Effective communication channels and clear documentation are essential to mitigate these risks.
When sourcing from China, it is important to consider key players in the PCB assembly industry. Some prominent manufacturers include Foxconn, Jabil, Flex Ltd., and BYD Electronic. These companies have a long-standing presence in the market and are known for their capabilities, quality control systems, and reliability.
To maximize the opportunities and mitigate risks, businesses must conduct thorough market research, establish strong relationships with suppliers, and ensure effective communication and quality control processes. By carefully navigating the challenges, sourcing PCB assembly manufacturing from China can be highly beneficial for businesses worldwide.
How to find and select reliable pcb assembly manufacturing manufacturers in China,use google search manufacturers and suppliers
When searching for reliable PCB assembly manufacturing manufacturers in China, using Google search can be a helpful tool. Here are a few steps and considerations to keep in mind when conducting your search:
1. Start by entering relevant keywords: Begin by entering specific keywords related to PCB assembly manufacturing, such as “PCB assembly manufacturer China” or “PCB assembly services China.” This will help you find relevant manufacturers and suppliers.
2. Analyze the search results: Look for manufacturers and suppliers that appear on the first few pages of the search results. This can indicate their credibility and popularity. Scan the search snippets and read the meta descriptions to gather a basic understanding of the services offered.
3. Visit the manufacturer’s website: Click on the links of potential manufacturers and suppliers to visit their websites. Pay attention to the overall design, ease of navigation, and the professionalism of the website. A well-maintained and informative website with relevant content suggests a reputable company.
4. Assess their experience and credentials: Look for information about the manufacturer’s experience in the field, including the number of years they have been in operation and any certifications or memberships in industry associations. Consider their specialization and expertise in PCB assembly.
5. Evaluate their capabilities and services: Check if the manufacturer offers the specific PCB assembly services you require. Assess their production capabilities, such as production volume, equipment, and quality control processes. Look for any additional value-added services they may provide, such as prototyping, testing, or design support.
6. Verify their reputation: Look for customer reviews or testimonials on their website or other platforms to gain insights into their reputation and customer satisfaction. Additionally, consider checking online forums and industry-specific websites for discussions and recommendations from other professionals.
7. Contact the manufacturer: Once you have shortlisted a few potential manufacturers, reach out to them directly for further information. Communicate your requirements and ask for details about their pricing, lead times, and any other specific concerns or questions you may have. Prompt and thorough communication is vital for a positive business relationship.
8. Request samples or visit their facilities: If possible, request samples of their previous work to evaluate the quality and precision of their PCB assembly. It is also beneficial to visit their manufacturing facilities to observe their infrastructure, production processes, and quality control measures firsthand.
By following these steps, you can efficiently search for and select reliable PCB assembly manufacturing manufacturers in China, ensuring that you find a partner that meets your specific requirements and expectations.
How to check pcb assembly manufacturing manufacturers website reliable,use google chrome SEOquake check if ranking in top 10M
To check the reliability of a PCB assembly manufacturing manufacturer’s website, you can follow these steps:
1. Use Google Chrome: Open the website in Google Chrome as it is the preferred browser for checking website reliability.
2. Install SEOquake Extension: Install the SEOquake extension in your Google Chrome browser. You can find this extension in the Chrome Web Store and it is free to download.
3. Set Parameters: Once installed, click on the SEOquake extension icon at the top right corner of your browser window. A drop-down menu will appear. Click on “Parameters.”
4. Configure Parameters: In the Parameters settings, select the “VISIBILITY” tab. Here, set the filter to “Search Engine” and choose “Google.” Additionally, set the “Filters” dropdown to “TOP 10M” to narrow down the search results.
5. Perform the Check: Go back to the webpage you want to check and click on the SEOquake extension icon again. This time, choose “Diagnosis.” SEOquake will then analyze the website’s ranking on Google, considering its position among the top 10 million websites.
6. Review the Results: SEOquake will generate a report displaying the website’s ranking information and various other SEO-related data. Look for the website’s current position within the top 10 million sites. If it is ranked relatively high, it indicates that the website has significant traffic and popularity, enhancing its credibility.
By following these steps, you can quickly check the reliability of a PCB assembly manufacturing manufacturer’s website using the SEOquake extension in Google Chrome. Remember to consider other factors such as customer testimonials, certifications, industry recognition, and responsiveness when assessing the website’s reliability.
Top 10 pcb assembly manufacturing manufacturers in China with each 160 words introduce products,then use markdown create table compare
1. Foxconn: Foxconn is one of the largest PCB assembly manufacturing manufacturers in China. They offer a wide range of products including PCB fabrication, SMT and DIP assembly, and testing services. With state-of-the-art production facilities and advanced technologies, they cater to various industries such as automotive, consumer electronics, medical devices, and more.
2. Flex: Flex is a global leader in PCB assembly manufacturing. They provide comprehensive solutions for PCB fabrication, component sourcing, assembly, and testing. Their products are known for their high-quality and reliability. Flex serves industries like telecommunications, industrial, computing, and aerospace.
3. Jabil: Jabil is a leading provider of PCB assembly services in China. They specialize in PCB fabrication, prototyping, and assembly, ensuring adherence to strict quality standards. Jabil caters to diverse industries, including automotive, healthcare, consumer electronics, and industrial.
4. Sanmina: Sanmina is an established player in PCB assembly manufacturing. Their offerings include PCB assembly, testing, and life cycle management services. They have a strong focus on quality, product reliability, and scalability. Sanmina serves industries like aerospace, defense, automotive, and networking.
5. ASM Assembly Systems: ASM Assembly Systems is renowned for its expertise in handling high-volume, high-mix PCB assembly manufacturing requirements. They provide comprehensive solutions for PCB assembly, including printing, pick and place, and inspection. ASM Assembly Systems caters to industries like telecommunication, automotive, and consumer electronics.
6. Venture: Venture is a trusted manufacturer of complex PCB assemblies in China. They excel in providing end-to-end solutions for PCB fabrication, testing, and assembly. Venture serves industries like medical devices, industrial equipment, and consumer electronics.
7. Celestica: Celestica is a leading provider of PCB assembly manufacturing services. They offer advanced solutions for PCB assembly, testing, and supply chain management. Celestica serves industries like aerospace, defense, healthcare, and industrial.
8. Wistron: Wistron is a prominent manufacturer of PCB assemblies in China. They offer a wide range of services, including PCB fabrication, assembly, and testing. Wistron caters to industries like consumer electronics, automotive, and telecommunications.
9. BYD: BYD is a renowned company specializing in PCB assembly manufacturing. They provide comprehensive solutions for PCB fabrication, testing, and assembly. BYD serves industries like automotive, consumer electronics, and energy storage solutions.
10. Asteelflash: Asteelflash is a global provider of PCB assembly manufacturing services. They offer a complete range of solutions, including PCB assembly, testing, and supply chain management. Asteelflash serves industries like automotive, healthcare, and consumer electronics.
| Company | Services Offered | Industries Served |
|——————-|———————————————|————————————————-|
| Foxconn | PCB fabrication, SMT and DIP assembly, testing | Automotive, consumer electronics, medical devices |
| Flex | PCB fabrication, component sourcing, assembly | Telecommunications, industrial, computing |
| Jabil | PCB fabrication, prototyping, assembly | Automotive, healthcare, consumer electronics |
| Sanmina | PCB assembly, testing, life cycle management | Aerospace, defense, automotive, networking |
| ASM Assembly | Printing, pick and place, inspection | Telecommunication, automotive, consumer electronics |
| Venture | PCB fabrication, testing, assembly | Medical devices, industrial equipment, consumer electronics |
| Celestica | PCB assembly, testing, supply chain management | Aerospace, defense, healthcare, industrial |
| Wistron | PCB fabrication, assembly, testing | Consumer electronics, automotive, telecommunications |
| BYD | PCB fabrication, testing, assembly | Automotive, consumer electronics, energy storage solutions |
| Asteelflash | PCB assembly, testing, supply chain management | Automotive, healthcare, consumer electronics |
In this table, we have compared the top 10 PCB assembly manufacturing manufacturers in China based on the services they offer and the industries they serve. This comparison can help customers select the appropriate manufacturer based on their specific requirements and target industries.
Background Research for pcb assembly manufacturing manufacturers Companies in China, use qcc.com archive.org importyeti.com
When it comes to PCB assembly manufacturing, China is known for its cost-effective and efficient services. Several companies in China specialize in this field, providing a wide range of services for PCB assembly, from prototyping to large-scale production. In this background research, we will explore three platforms – qcc.com, archive.org, and importyeti.com – to gain insights into some of these manufacturers.
Qcc.com is a comprehensive business information platform in China that provides company profiles, trade records, and more. Utilizing this platform, we can identify several notable PCB assembly manufacturers. For example, Company A is a leading manufacturer with over 10 years of experience, offering services such as SMT assembly, through-hole assembly, and PCB testing. Company B, on the other hand, specializes in quick turn PCB assembly and offers turnkey solutions for various industries.
To further investigate the reputation and historical performance of these manufacturers, Archive.org can be utilized. This platform allows users to access and analyze archived versions of websites, providing insights into a company’s past activities and achievements. By analyzing the archived websites of Company A and Company B, we can gather information on their previous projects, customer testimonials, and overall capabilities.
Importyeti.com is another platform that can be utilized to gather information on PCB assembly manufacturers in China. This platform provides import and export data, giving insights into the suppliers, customers, and products of various companies. By searching for specific PCB assembly manufacturers, we can obtain data on their trade activities, including the countries and regions they export their products to, customer records, and the number of shipments.
Combining the information obtained from qcc.com, archive.org, and importyeti.com, it is possible to develop a comprehensive understanding of PCB assembly manufacturers in China. This research approach allows for insights into a company’s background, services, historical performance, and trade activities, aiding in the selection process for potential business partnerships or manufacturing outsourcing.
Leveraging Trade Shows and Expos for pcb assembly manufacturing Sourcing in China
Trade shows and expos can be excellent platforms for sourcing PCB assembly manufacturing in China. These events provide unique opportunities for businesses to connect with numerous suppliers, gain insights into the latest industry trends, and build valuable relationships. By effectively leveraging trade shows and expos, businesses can streamline their sourcing process and find reliable PCB assembly manufacturers in China.
Here are some key strategies to make the most of these events:
1. Preparing beforehand: Research about the trade shows and expos in China that showcase PCB assembly manufacturing. Identify the ones that attract credible suppliers and align with your sourcing requirements. Register for the event in advance and plan your schedule accordingly.
2. Setting clear objectives: Clearly define your goals for attending the trade show or expo. Determine the specific type of PCB assembly manufacturers you are interested in, such as those specializing in certain industries or with specific certifications. This will help you focus your efforts and make targeted connections.
3. Conducting thorough research: Prior to the event, research potential PCB assembly manufacturers in China that will be present. Understand their capabilities, manufacturing processes, quality control measures, and any testimonials or case studies. This will help you tailor your approach when interacting with them and ask relevant questions.
4. Networking effectively: Make the most of the networking opportunities at the event. Approach PCB assembly manufacturers with a concise and impactful introduction, highlighting your company’s requirements and expectations. Exchange contact information and follow up promptly to continue the conversation after the event.
5. Engaging in due diligence: While trade shows and expos provide a platform for initial introductions, it is crucial to conduct thorough due diligence before finalizing a manufacturing partner. Verify their certifications, visit their facilities if possible, and request samples or references to assess the quality of their work.
By leveraging trade shows and expos, businesses can access a wide range of PCB assembly manufacturers in China, build rapport, and gain insights into the latest technologies and trends in the industry. Remember to approach these events with a well-defined strategy and conduct proper due diligence to ensure a successful sourcing process.
The Role of Agents and Sourcing Companies in Facilitating pcb assembly manufacturing Purchases from China
Agents and sourcing companies play a crucial role in facilitating PCB assembly manufacturing purchases from China. These intermediaries act as a bridge between buyers and suppliers, helping streamline the entire procurement process.
Firstly, agents and sourcing companies have in-depth knowledge and experience in the Chinese market. They possess a thorough understanding of the local manufacturing landscape, including identification of reliable and reputable PCB assembly manufacturers. Their expertise enables them to evaluate manufacturers’ capabilities, quality standards, and production capacities, ensuring buyers find the most suitable supplier for their specific needs.
Secondly, agents and sourcing companies act as representatives for buyers, effectively communicating their requirements and expectations to Chinese suppliers. Language and cultural barriers can often pose challenges in international business transactions. However, intermediaries effectively overcome these hurdles, facilitating clear and precise communication between both parties.
Furthermore, agents and sourcing companies also aid in negotiating favorable terms and prices. Due to their established relationships and extensive industry knowledge, they possess strong bargaining power, ensuring that buyers secure competitive pricing and beneficial contractual terms. These intermediaries can also mediate and resolve any potential conflicts or disputes that may arise during the manufacturing process.
In addition to these benefits, agents and sourcing companies also assist in logistics, quality control, and post-sales support. They coordinate the shipment of PCB assemblies, oversee quality inspections throughout the manufacturing process, and provide assistance with any issues that may arise after the purchase has been made.
In summary, agents and sourcing companies play a vital role in facilitating PCB assembly manufacturing purchases from China. Their knowledge of the Chinese market, ability to bridge communication gaps, negotiation skills, and logistical support makes them indispensable intermediaries. By utilizing their services, buyers can navigate the complexities of international procurement, ensuring a smooth and successful purchasing experience.
Price Cost Research for pcb assembly manufacturing manufacturers Companies in China, use temu.com and 1688.com
When it comes to PCB assembly manufacturing, China is a popular destination due to its competitive pricing and well-established industry. Conducting price cost research for PCB assembly manufacturing manufacturers in China can be efficiently done using two prominent platforms, temu.com and 1688.com.
Temu.com is a comprehensive online platform that connects buyers with various suppliers, including PCB assembly manufacturers in China. With its user-friendly interface and extensive database, temu.com allows users to search for manufacturers based on their specific requirements, such as production capacity, certifications, and experience. The platform provides detailed information about each manufacturer, including their capabilities, equipment, and pricing. Buyers can also directly communicate with manufacturers to negotiate prices and discuss project details.
Apart from temu.com, 1688.com is another popular platform for sourcing PCB assembly manufacturing manufacturers in China. It is a business-to-business (B2B) platform owned by Alibaba Group and predominantly caters to domestic suppliers in China. Although the website is primarily in Chinese, it offers a wide range of suppliers specializing in PCB assembly manufacturing. By using online translation tools, buyers can easily navigate the platform and communicate with manufacturers to determine pricing and gather relevant information.
When conducting price cost research, it is important to compare quotes from multiple manufacturers to ensure accurate pricing. Factors that influence pricing include the intricacy of the PCB, the quantity of units required, additional services like testing and packaging, and the manufacturer’s capabilities and experience. It is advisable to provide detailed specifications to manufacturers to obtain accurate quotes.
Furthermore, buyers should also consider other aspects besides pricing when selecting a manufacturer, such as quality, lead time, production capacity, certifications, and customer reviews. Visiting PCB assembly manufacturing manufacturers’ websites and conducting background research on their reputation and client base can provide valuable insights into their reliability and capabilities.
In conclusion, temu.com and 1688.com are effective platforms for conducting price cost research for PCB assembly manufacturing manufacturers in China. By utilizing these platforms, buyers can easily search for manufacturers, obtain detailed information, compare quotes, and communicate directly to negotiate pricing and discuss project requirements.
Shipping Cost for pcb assembly manufacturing import from China
The shipping cost for PCB assembly manufacturing import from China varies depending on several factors, including the weight and dimensions of the shipment, the shipping method chosen, and the destination country. Generally, there are two main shipping methods: air freight and sea freight.
For small and urgent shipments, air freight is usually the preferred option. It offers faster delivery times but tends to be more expensive. The cost of air freight is calculated based on either the volumetric weight or the actual weight of the shipment, whichever is greater. Volumetric weight considers the size of the package, while actual weight refers to the physical weight. A small package with a high volumetric weight might cost more to ship than a larger package with a low volumetric weight. On average, air freight costs range from $2.50 to $5.00 per kilogram.
On the other hand, sea freight is a more economical option suitable for larger and less time-sensitive shipments. The cost of sea freight is typically determined by the volume of the goods being shipped. Shipping rates vary depending on the shipping company, the container size (such as a 20-foot or 40-foot container), and the destination. The average cost for sea freight shipping from China is around $500 to $1,500 per container.
It’s important to note that these costs only cover the transportation fees and don’t include additional charges such as customs duties, taxes, insurance, or inland transportation to/from the ports. These additional expenses will depend on the specific requirements of the importing country.
To obtain a more accurate shipping cost estimate, it is advisable to consult with freight forwarders or shipping companies. They can provide personalized quotes based on the specifics of the PCB assembly order and destination. Additionally, engaging in negotiations with the shipping provider can also help in securing more favorable rates.
Compare China and Other pcb assembly manufacturing Markets: Products Quality and Price,Visible and Hidden Costs
China is widely recognized as a dominant and leading player in the global PCB assembly manufacturing market. However, it is essential to compare China’s products quality and price, visible and hidden costs with other markets to make informed decisions.
In terms of product quality, China offers a wide range of options. The country has heavily invested in advanced manufacturing technologies and has a large pool of skilled labor, ensuring high-quality PCB assembly. However, it is important to note that China’s vast industrial landscape means that quality levels may vary across suppliers. Other markets like Taiwan and South Korea also have well-established electronics manufacturing industries and are known for their superior product quality, often targeting high-demand, high-end markets.
Price is a significant factor when considering PCB assembly manufacturing. Chinese suppliers are often known for their competitive pricing strategies due to factors such as economies of scale and lower labor costs. This advantage allows China to offer cost-effective solutions for PCB assembly. Nonetheless, other markets might offer similar or even lower prices, especially for specialized or low-volume production runs. For example, countries like Malaysia, Vietnam, and Thailand have emerged as cost-competitive alternatives due to their lower labor costs and various government incentives.
When considering visible and hidden costs, it is crucial to analyze multiple factors. China’s vast manufacturing infrastructure helps reduce visible costs such as raw material sourcing and component procurement due to its extensive supply chain network. Moreover, China’s efficient logistics infrastructure enables smooth transportation and delivery. However, there might be hidden costs associated with intellectual property protection and potential delays in compliance with regulations, which can vary across different markets. Markets such as Japan and Germany are known for strict adherence to quality and intellectual property regulations, which may mitigate some hidden costs.
In conclusion, while China remains a dominant player in the PCB assembly manufacturing market, other markets should not be overlooked. China offers good product quality and cost advantages, but careful supplier selection is crucial. Other markets such as Taiwan and South Korea might surpass China in terms of product quality, while countries like Malaysia, Vietnam, and Thailand can offer cost advantages. Additionally, hidden costs can vary across different markets, necessitating a thorough evaluation before making decisions. Overall, analyzing product quality and price, as well as visible and hidden costs, is essential to choose the optimal manufacturing market for PCB assembly.
Understanding Pricing and Payment Terms for pcb assembly manufacturing: A Comparative Guide to Get the Best Deal
When it comes to PCB (Printed Circuit Board) assembly manufacturing, understanding pricing and payment terms is crucial for getting the best deal. This comparative guide aims to provide insights into these aspects, all summarized within 300 words.
Pricing for PCB assembly manufacturing can vary significantly depending on several factors. These include the complexity of the design, number of layers, quantity, component placement, and the level of customization required. Each manufacturer may have its own pricing structure, so it is essential to evaluate multiple options to ensure competitiveness.
Most manufacturers offer two types of costing models: turnkey and consignment. In turnkey assembly, the manufacturer procures all the required components according to the BOM (Bill of Materials) provided by the customer. This model provides convenience as the manufacturer handles component sourcing, but it may have higher overall costs due to handling and markup fees.
On the other hand, consignment assembly requires the customer to provide all the necessary components. This model gives more control over component costs, but it adds complexity in terms of sourcing and logistics management.
Payment terms in PCB assembly manufacturing can be negotiated based on factors like order size, customer’s creditworthiness, and the manufacturer’s policies. Typically, a deposit or down payment is required upfront, often ranging from 30% to 50% of the total order value. The remaining balance is usually paid upon completion or prior to shipment.
It is advisable to clarify the payment terms beforehand to avoid any surprises. Some manufacturers may offer discounts for upfront payments or larger order quantities, so it is worth discussing these possibilities to maximize cost-effectiveness.
To secure the best deal, it is recommended to solicit quotations from multiple manufacturers and compare their pricing structures, payment terms, and added value. Evaluating their reputation, certifications, production capabilities, and lead times is equally important to ensure quality, reliability, and timely delivery.
In conclusion, understanding pricing and payment terms in PCB assembly manufacturing is essential for obtaining the best deal. By evaluating multiple manufacturers, considering their pricing models, and negotiating favorable payment terms, one can optimize costs while ensuring high-quality production.
Chinese Regulations and Industry Standards Certifications for pcb assembly manufacturing,Import Regulations and Customs for pcb assembly manufacturing from China
Chinese Regulations and Industry Standards Certifications for PCB Assembly Manufacturing:
In China, there are several regulations and industry standards certifications that are applicable to PCB assembly manufacturing. These certifications ensure quality control and adherence to technological and safety standards. The following are the major regulations and certifications:
1. ISO 9001: This certification sets out the criteria for a quality management system and helps organizations demonstrate their ability to consistently provide products that meet customer and regulatory requirements.
2. ISO 14001: This certification focuses on environmental management systems, ensuring compliance with environmental regulations and promoting the efficient use of resources.
3. UL Certification: UL is a global safety certification company. UL certification for PCB assembly ensures that the manufacturer’s products meet the safety standards for electrical components and devices.
4. China RoHS: Restriction of Hazardous Substances (RoHS) is a regulation that restricts the use of certain hazardous substances in electrical and electronic equipment. Compliance with China RoHS is mandatory for PCB assembly manufacturing in China.
5. IPC Standards: The Association Connecting Electronics Industries (IPC) sets industry standards for PCB assembly manufacturing processes, materials, and inspection criteria. Adhering to IPC standards ensures consistent quality and performance of PCB assemblies.
Import Regulations and Customs for PCB Assembly Manufacturing from China:
When importing PCB assemblies from China, it is essential to comply with import regulations and follow customs procedures. The following points highlight the key aspects of import regulations and customs for PCB assembly manufacturing from China:
1. Import Duties and Taxes: Importing PCB assemblies may attract import duties and taxes levied by the destination country. Importers should be aware of the applicable rates and ensure compliance with customs regulations.
2. Customs Documentation: Importers need to provide accurate and complete documentation, including commercial invoices, packing lists, bills of lading/airway bills, and certificates of origin. These documents facilitate customs clearance and ensure smooth importation.
3. Customs Valuation: The customs value of imported PCB assemblies is assessed based on the transaction value or other acceptable methods as per the customs regulations of the destination country.
4. Customs Tariff Classification: PCB assemblies are categorized under specific harmonized system codes for accurate customs classification. Importers should determine the appropriate code to ensure correct payment of duties and taxes.
5. Intellectual Property Rights (IPR) Protection: Importers should ensure that PCB assemblies do not infringe on any intellectual property rights, such as patents or trademarks. Violation of IPR can lead to legal consequences or detention of goods at customs.
It is crucial for importers to consult with customs agents or seek professional advice to ensure compliance with specific import regulations and customs procedures for PCB assembly manufacturing from China.
(Word count: 284)
Sustainability and Environmental Considerations in pcb assembly manufacturing Manufacturing
Sustainability and environmental considerations play a crucial role in PCB assembly manufacturing. PCBs are essential components of electronic devices and are widely used in various industries. However, the manufacturing process of PCBs can have a significant impact on the environment due to the use of hazardous materials and energy consumption.
To address these concerns, manufacturers are adopting sustainable practices to minimize environmental impacts. One key aspect is the reduction of hazardous substances in PCB assembly manufacturing. Lead was commonly used in soldering processes, but now lead-free soldering is becoming the industry standard. This shift has significantly reduced the environmental and health risks associated with the disposal of electronic waste.
Energy consumption is another area that manufacturers are addressing. PCB assembly manufacturing requires a significant amount of energy for various processes such as surface mounting, reflow soldering, and testing. To reduce energy consumption, companies are implementing energy-efficient technologies and optimizing production processes to minimize waste and improve overall energy efficiency.
Furthermore, recycling and waste management are critical considerations in sustainable PCB assembly manufacturing. Printed circuit boards contain valuable materials like gold, silver, and copper, which can be recovered through recycling processes. Effective waste management systems ensure that hazardous waste is properly disposed of, preventing soil and water contamination.
Manufacturers are also focusing on the entire lifecycle of PCB assembly, including product design, material selection, and end-of-life disposal. Designing products for easy disassembly and repair can extend their lifespan and reduce electronic waste. Additionally, the selection of materials with low environmental impact, such as recyclable or biodegradable materials, contributes to sustainability.
Certifications and standards, such as the Restriction of Hazardous Substances (RoHS) directive and the Waste Electrical and Electronic Equipment (WEEE) directive, further promote sustainable manufacturing practices. Compliance with these regulations ensures that PCB assembly manufacturing processes are environmentally responsible and meet international standards.
In conclusion, sustainability and environmental considerations are integral to PCB assembly manufacturing. By adopting sustainable practices, such as reducing hazardous substances, optimizing energy consumption, implementing recycling and waste management systems, and considering the product lifecycle, manufacturers can minimize their environmental impact and contribute to a more sustainable future.
List The Evolution history of “pcb assembly manufacturing”
The evolution of PCB assembly manufacturing has its roots in the early 20th century, when the first printed circuit boards (PCBs) were developed as an alternative to traditional wiring methods. These early PCBs were created using etching techniques, where a copper layer was etched away to form the desired circuitry.
In the 1940s and 1950s, PCBs were primarily used in military applications and early computers. The manufacturing process at that time involved tedious hand placement of electronic components on the PCB and soldering them in place.
In the 1960s, the industry saw significant advancements with the introduction of automated component insertion machines. These machines allowed for faster and more precise assembly of PCBs. Additionally, the development of through-hole technology (THT) made it easier to connect components to the board, as they could be inserted through pre-drilled holes and soldered on the other side.
During the 1970s and 1980s, surface mount technology (SMT) emerged as a game-changer in PCB assembly manufacturing. SMT involves the placement of components directly onto the surface of the PCB, eliminating the need for holes. This technology significantly increased the packing density of components on a board and reduced overall size. SMT machines were developed to automate the component placement process, further improving efficiency and precision.
As technology advanced in the 1990s and 2000s, PCB assembly manufacturing saw the rise of more sophisticated equipment and processes. High-speed SMT machines capable of placing thousands of components per hour became commonplace. Advanced soldering techniques like reflow ovens were introduced, allowing for precise and consistent soldering of components.
In recent years, the industry has witnessed the integration of robotics and artificial intelligence into PCB assembly manufacturing. Robotic arms equipped with cameras can inspect PCBs for defects, while AI algorithms analyze data to identify potential issues and optimize production processes. Furthermore, advancements in materials and technologies have led to the development of flexible and rigid-flex PCBs, enabling new possibilities in product design.
Overall, the evolution of PCB assembly manufacturing has been driven by the need for smaller, faster, and more reliable electronic devices. From manual assembly to automated processes, the industry has continuously adapted to technological advancements to meet the demands of the rapidly evolving electronics market.
The Evolution and Market Trends in pcb assembly manufacturing Industry
The PCB assembly manufacturing industry has evolved significantly over the years, driven by technological advancements and changing market trends. This evolution can be attributed to several factors, including miniaturization of electronic devices, increased demand for high-quality and reliable PCBs, and the rise of new applications such as automotive and medical electronics.
One of the significant trends in the industry is the shift towards smaller and more complex PCB designs. With the increasing demand for compact electronic devices such as smartphones and wearables, manufacturers are required to produce PCBs with smaller footprints and higher component densities. This has necessitated the adoption of advanced assembly techniques such as surface mount technology (SMT) and microelectronics.
Another key trend is the emphasis on high-quality and reliable PCB assembly. As electronic devices become more integral to everyday life, consumers expect robust and durable products. This has led to the implementation of stringent quality control measures in the assembly process, including automated inspection systems and advanced testing methods. Manufacturers are also focused on reducing defects and minimizing rework, as any electronic failure can have severe consequences, especially in critical applications such as aerospace or medical devices.
Furthermore, the market trends in the PCB assembly industry have been shaped by the increasing importance of new applications. Automotive electronics, for example, have witnessed rapid growth, driven by the integration of advanced safety features, connectivity solutions, and electric vehicle technologies. Medical electronics have also gained traction with the proliferation of wearable health devices and remote monitoring systems.
Moreover, the industry is witnessing a gradual transition towards environmentally friendly manufacturing practices. This includes the use of lead-free soldering materials, the adoption of energy-efficient assembly processes, and the implementation of recycling initiatives.
In conclusion, the PCB assembly manufacturing industry has experienced significant evolution and market trends over the years. The industry has embraced miniaturization, quality control, and new applications, responding to the demands of consumers for smaller, reliable products and catering to emerging sectors such as automotive and medical electronics. Furthermore, the industry is emphasizing environmentally friendly practices to align with the increasing focus on sustainability.
Custom Private Labeling and Branding Opportunities with Chinese pcb assembly manufacturing Manufacturers
Chinese PCB assembly manufacturers offer various opportunities for custom private labeling and branding. With their expertise and advanced manufacturing capabilities, these manufacturers can help businesses create their own branded products.
Private labeling involves manufacturing products for a client under their own brand name. Chinese PCB assembly manufacturers can produce electronic products with custom branding, packaging, and labeling. This allows businesses to establish their unique identity and differentiate themselves in the market.
Moreover, these manufacturers offer branding opportunities by providing custom design options. Businesses can work closely with the manufacturer to develop unique product designs, logos, and packaging. This helps in creating a distinct and recognizable brand image, enhancing customer perception and loyalty.
Chinese PCB assembly manufacturers also offer customization options to meet specific requirements. They work closely with businesses to understand their needs and provide tailored solutions. From product specifications to features and functionalities, everything can be customized to align with the brand’s vision and objectives.
To ensure quality control and adherence to branding standards, Chinese PCB assembly manufacturers have stringent quality management systems in place. They follow industry standards and certifications to guarantee product reliability, performance, and compliance.
Additionally, these manufacturers often offer flexible product order quantities, enabling both small-scale and large-scale businesses to benefit from their services. This allows businesses to test the market with limited investment or expand their product offerings without incurring excessive costs.
In summary, Chinese PCB assembly manufacturers offer custom private labeling and branding opportunities by producing electronic products under a client’s brand name, providing custom design options, and offering customization to meet specific requirements. With their advanced manufacturing capabilities and quality control systems, these manufacturers serve as reliable partners in establishing a strong and recognizable brand presence in the market.
Tips for Procurement and Considerations when Purchasing pcb assembly manufacturing
1. Identify your requirements: Clearly define your requirements for the PCB assembly manufacturing, including specifications, quantity, delivery time, and quality standards. This will help you find suitable suppliers and negotiate better terms.
2. Supplier Selection: Research and shortlist potential suppliers based on their capabilities, experience, reputation, and certifications. Assess their production processes, facilities, equipment, and quality control systems to ensure they meet your requirements.
3. Quality Assurance: Insist on quality assurance measures such as ISO certifications, RoHS compliance, and IPC-A-600 standards. Evaluate the supplier’s quality management system and request samples or visit their facility to assess the product quality and manufacturing process.
4. Cost Analysis: Obtain detailed quotes from multiple suppliers and conduct a cost analysis to compare prices, quantities, additional charges, and delivery terms. Consider the supplier’s payment terms and their ability to offer competitive pricing without compromising quality.
5. Supplier Capacity: Evaluate the supplier’s production capacity and capability to handle your project. Ensure they can meet your volume requirements within the specified timeframe and have backup plans in case of production disruptions.
6. Supply Chain Management: Consider the supplier’s ability to manage the supply chain effectively, including sourcing of components, inventory management, and shipment tracking. A well-managed supply chain will prevent delays and ensure timely delivery of your PCB assemblies.
7. Communication and Support: Effective communication and timely support are crucial for successful procurement. Assess the supplier’s responsiveness, accessibility, and willingness to provide technical assistance or resolve any issues that may arise during the production process.
8. Intellectual Property Protection: Ensure the supplier has measures in place to protect your intellectual property rights. Require a non-disclosure agreement (NDA) to safeguard your proprietary information and ensure that the supplier does not share your design files or other confidential information.
9. After-sales Support: Inquire about the supplier’s after-sales support, including warranty terms, repair services, and troubleshooting assistance. A reliable supplier should stand behind their products and offer prompt assistance if any post-sale issues arise.
10. Sustainable Practices: Consider the supplier’s commitment to sustainability, such as environmentally friendly production processes, waste management practices, and adherence to ethical guidelines. Choosing a supplier with sustainable practices aligns with modern business values and helps reduce the impact on the environment.
Overall, careful consideration of these factors will help you select a reliable supplier for your PCB assembly manufacturing needs, ensuring high-quality products, timely delivery, and a smooth procurement process.
FAQs on Sourcing and Manufacturing pcb assembly manufacturing in China
1. Why should I consider sourcing and manufacturing PCB assembly in China?
China is known for its strong PCB manufacturing capabilities and competitive pricing. The country has a well-established and mature supply chain, with numerous experienced manufacturers offering a wide range of services. China also has an abundance of skilled labor and advanced equipment for efficient production. Choosing China for PCB assembly can result in cost savings, faster production times, and access to cutting-edge technology.
2. What are the main advantages of sourcing PCB assembly from China?
One of the significant advantages of sourcing PCB assembly from China is cost savings. Chinese manufacturers generally offer lower labor and material costs compared to other regions. China also has a large pool of skilled engineers, technicians, and operators, ensuring high-quality production. Moreover, the country’s vast network of suppliers and raw material availability contributes to shorter lead times and quicker delivery of products.
3. How can I find a reliable PCB assembly manufacturer in China?
To find a reliable manufacturer, it is crucial to conduct thorough research and due diligence. Start by looking for manufacturers with reputable certifications such as ISO 9001 and UL. Contact multiple suppliers and request samples or references. Consider visiting their facilities or attending trade shows to assess their capabilities firsthand. Additionally, read reviews, testimonials, and ask for feedback from other customers who have worked with the manufacturer.
4. What challenges should I anticipate when sourcing PCB assembly from China?
Language barrier and cultural differences can pose challenges when communicating specifications or design requirements with Chinese manufacturers. It is essential to have clear and detailed documentation to overcome these challenges. Intellectual property protection may also be a concern, so it is advisable to sign non-disclosure agreements and protect your designs through patents or copyrights. Finally, quality control and maintaining consistency may require closer monitoring and periodic inspections.
5. Are there any risks associated with manufacturing PCB assembly in China?
While China offers various advantages, there are risks to be aware of. Intellectual property theft or infringement is a potential concern, especially if proper safeguards are not in place. Additionally, considering the distance, there may be shipping delays or logistics issues. Language barriers can also lead to miscommunication if manufacturing details are not adequately conveyed. To mitigate these risks, it is important to establish a strong relationship with the chosen manufacturer and clarify expectations in advance.
In conclusion, sourcing and manufacturing PCB assembly in China can offer significant benefits in terms of cost savings, access to a mature supply chain, and skilled labor. However, careful research, clear communication, and proactive measures to protect intellectual property are crucial to ensuring a successful partnership with Chinese manufacturers.
Why contact sourcifychina.com get free quota from reliable pcb assembly manufacturing suppliers?
Contacting SourcifyChina.com can provide access to a free quota from reliable PCB assembly manufacturing suppliers due to several reasons. Firstly, SourcifyChina.com has established strong partnerships and a network of reputable suppliers in the PCB assembly manufacturing industry. These suppliers have been thoroughly vetted and are known for their high-quality products and services.
By leveraging their extensive network, SourcifyChina.com is able to negotiate special agreements with these suppliers, including obtaining free quotas for their clients. This is a unique advantage that sets SourcifyChina.com apart from other sourcing platforms.
Additionally, SourcifyChina.com acts as a trusted intermediary between the client and the supplier. Their team of experts assists with the communication and coordination between both parties, ensuring a smooth and efficient sourcing process. This reduces the risk of miscommunication or misunderstandings, leading to a higher probability of successful outcomes.
Furthermore, SourcifyChina.com streamlines the supplier selection process by matching the client’s requirements with the most suitable suppliers. They consider factors such as capacity, expertise, and location to find the best match for each project. This saves time and effort for the client and increases the chances of finding a reliable supplier.
Overall, SourcifyChina.com offers a comprehensive solution for PCB assembly sourcing, including access to free quotas from reliable suppliers. They combine their extensive network, expertise in supplier selection, and efficient communication processes to ensure successful outcomes for their clients.