Introduce about pipe welding machine guide,Qulity,Cost,Supplier,Certification,Market,Tips,FAQ
A pipe welding machine is a crucial tool for joining pipes in various industries like construction, oil, and gas, and manufacturing. A reliable welding machine guide ensures smooth and precise welds, reducing the chances of leaks and ensuring the structural integrity of the pipes.
When looking for a pipe welding machine, quality is paramount. High-quality machines will deliver consistent and durable welds, ensuring the longevity of the pipes. Consider factors like welding speed, accuracy, and ease of operation when evaluating the quality of a welding machine.
Cost is also a significant factor to consider when choosing a pipe welding machine. While it’s essential to stick to your budget, don’t compromise on quality for a lower price. Look for a balance between cost and quality to get the best value for your investment.
There are numerous suppliers of pipe welding machines in the market, so do thorough research to find a reputable and reliable supplier. Check for certifications like ISO and CE to ensure the quality and safety standards of the machine.
The market for pipe welding machines is growing steadily due to the increasing demand for welded pipe products. With the right machine and skills, you can tap into this lucrative market and expand your business.
Lastly, consider these tips when using a pipe welding machine: ensure proper machine setup, use the appropriate welding technique, and regularly maintain the machine for optimal performance.
Frequently asked questions about pipe welding machines include the types of welding processes, the materials that can be welded, and the maintenance requirements. Consult with experts or suppliers to get the answers to these questions and make an informed decision about purchasing a pipe welding machine.
Types of pipe welding machine
There are several types of pipe welding machines that are commonly used in the industry:
1. Manual pipe welding machines: These are basic machines that require the welder to manually control the welding process. They are simple to operate and are suitable for small-scale welding jobs.
2. Semi-automatic pipe welding machines: These machines have some automated features, such as a wire feeder, which can help to speed up the welding process. They are more efficient than manual machines and are suitable for medium-sized welding jobs.
3. Automatic pipe welding machines: These machines have fully automated features, such as computer-controlled welding parameters and robotic arms that can manipulate the welding torch. They are highly efficient and are suitable for large-scale welding jobs.
4. Orbital pipe welding machines: These machines are specifically designed for welding pipes in a circular motion. They are precise and consistent, making them ideal for high-quality welding jobs.
5. TIG pipe welding machines: Tungsten Inert Gas (TIG) welding machines use a non-consumable tungsten electrode to create the weld. They produce high-quality welds with minimal spatter and are suitable for welding a variety of materials.
6. MIG pipe welding machines: Metal Inert Gas (MIG) welding machines use a consumable wire electrode to create the weld. They are versatile and can be used to weld a wide range of materials, making them popular in many industries.
Each type of pipe welding machine has its own advantages and limitations, so it is important to choose the right machine for the specific welding job at hand. By selecting the appropriate machine, welders can increase efficiency, improve weld quality, and reduce overall costs.
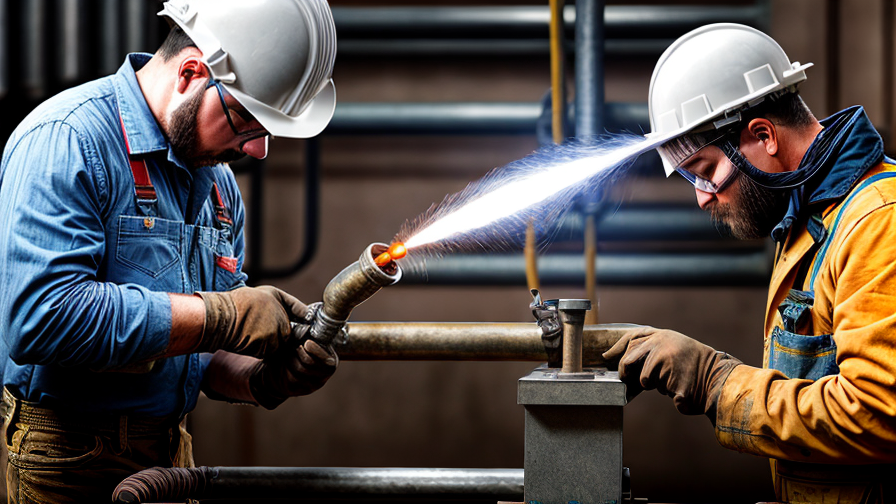
Pros and Cons of Using pipe welding machine
Pros of Using Pipe Welding Machine:
1. Efficiency: Pipe welding machines are designed to increase productivity by providing fast and efficient welding processes. They have advanced features like automatic feeding and positioning, which accelerates the welding process and reduces the overall welding time. This allows more pipes to be welded in less time, increasing productivity and reducing labor costs.
2. Accuracy: Pipe welding machines use advanced technology and precision control systems to ensure accurate welding results. They are equipped with sensors and monitors that monitor the welding parameters, ensuring that the weld is performed with consistently high quality. This eliminates the risk of human error and produces strong and reliable welds.
3. Safety: Pipe welding machines are designed with safety features to protect the operator and other personnel. They have protective shields and barriers to prevent exposure to sparks, heat, and harmful fumes. They also have built-in safety mechanisms that automatically shut down the machine in case of any malfunction or emergency.
Cons of Using Pipe Welding Machine:
1. Cost: Pipe welding machines are a significant investment and can be expensive to purchase or rent. Additionally, they may require regular maintenance and calibration, adding to the overall cost of operation. This can be a significant financial burden for small businesses or individuals who have limited budgets.
2. Complexity: Pipe welding machines are complex pieces of equipment that require proper training and knowledge to operate. Operating the machine without proper training can lead to errors or accidents. The complexity of the machine also means that troubleshooting and repairing any issues may require specialized expertise, further adding to the overall complexity and cost.
3. Limited Flexibility: Pipe welding machines are designed specifically for welding pipes and may not be suitable for other types of welding projects. This limits their versatility and may require additional equipment for other welding tasks. The size and weight of pipe welding machines can also make them less portable and adaptable to different worksite environments.
In conclusion, the pros of using pipe welding machines include increased efficiency, accuracy, and safety, while the cons include high cost, complexity, and limited flexibility. Before using a pipe welding machine, it is essential to assess the specific requirements of the project and consider these pros and cons to determine if the machine is the right choice.
pipe welding machine Reference Specifications (varies for different product)
The reference specifications for a pipe welding machine may vary depending on the specific product. However, there are some common parameters that are important for ensuring the proper functioning and efficiency of the machine.
One crucial specification is the power supply requirement. Pipe welding machines typically require a stable and reliable source of power, which is usually indicated in terms of voltage and frequency. The voltage requirement may vary, but common values include 220V, 400V, or 480V. The frequency is often 50Hz or 60Hz.
Another essential specification is the welding current range. This parameter determines the minimum and maximum current that the machine can deliver for different welding applications. It usually spans a wide range, such as 10A to 500A, allowing for flexibility in various welding tasks.
The welding machine’s duty cycle is also a critical specification. It refers to the amount of time the machine can operate continuously within a 10-minute period without overheating. Duty cycles are typically expressed as a percentage, such as 60% or 80%, indicating the ratio of welding time to rest time.
The welding process capability is another vital consideration. Pipe welding machines may support different welding processes, such as shielded metal arc welding (SMAW), gas metal arc welding (GMAW), or tungsten inert gas welding (TIG). The capability to perform specific welding processes may vary based on the product variant.
Additionally, the machine’s dimensions and weight are significant specifications for practicality and mobility. These factors determine the portability and ease of transportation during welding operations.
Furthermore, safety features and certifications should be considered. Pipe welding machines often have built-in safety features like thermal overload protection, short circuit protection, and voltage surge protection. Compliance with relevant international safety standards, such as CE, UL, or CSA certifications, may also be specified.
Finally, the user interface and control features should be mentioned. Pipe welding machines may have an LCD display to provide a clear view of the welding parameters, as well as control knobs or buttons to adjust settings like current, voltage, or wire speed.
In conclusion, reference specifications for a pipe welding machine encompass power supply requirements, welding current range, duty cycle, welding process capability, dimensions and weight, safety features, certifications, and user interface. These specifications ensure the machine’s proper operation, versatility, safety, and ease of use in various pipe welding applications.
Applications of pipe welding machine
Pipe welding machines are used in a variety of industries where pipe fabrication and installation are required. These machines are essential for creating strong and durable welds on pipes, ensuring they can withstand high pressure, harsh environments, and other demanding conditions. Some common applications of pipe welding machines include:
1. Oil and gas industry: Pipe welding machines are crucial for building pipelines that transport oil and gas from extraction sites to refineries and distribution centers. These pipelines need to be able to handle high pressures and corrosive materials, making high-quality welds essential.
2. Construction industry: Pipe welding machines are used in construction projects to connect pipes for water, sewage, and HVAC systems. They are also used in the installation of sprinkler systems in commercial buildings and fire protection systems in industrial settings.
3. Manufacturing industry: Pipe welding machines are used in the manufacturing of various products that require pipes, such as boilers, pressure vessels, heat exchangers, and process piping. These machines help ensure that the pipes are properly welded to meet industry standards and specifications.
4. Automotive industry: Pipe welding machines are used in the fabrication of exhaust systems, fuel lines, and other components for vehicles. These components need to be securely welded to prevent leaks and ensure optimal performance.
5. Aerospace industry: Pipe welding machines are used in the manufacturing of aircraft parts and components, such as hydraulic systems, fuel lines, and air ducts. These components must be welded to withstand extreme temperatures and pressures, making precise and reliable welds critical.
In conclusion, pipe welding machines play a vital role in various industries where the fabrication and installation of pipes are required. These machines help ensure that pipes are properly welded to meet industry standards and specifications, making them essential for the safe and efficient operation of pipelines, systems, and components.
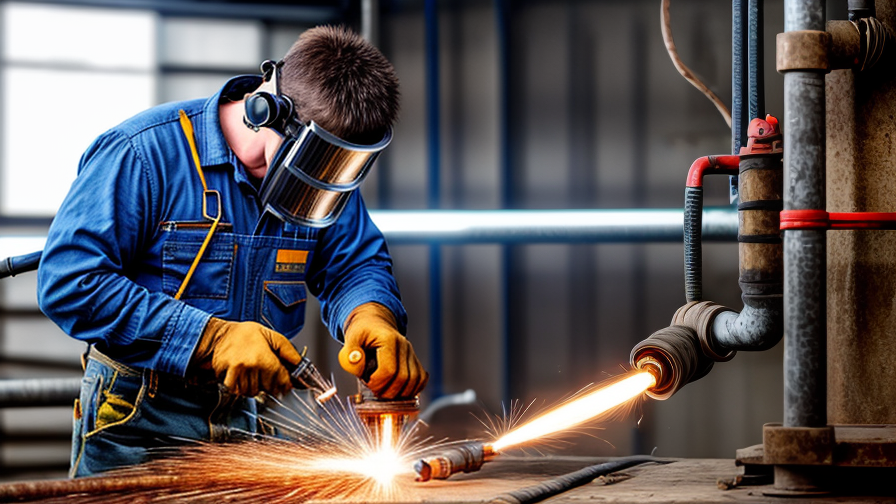
The Work Process and how to use pipe welding machine
The work process of pipe welding using a pipe welding machine involves several key steps. First, the pipes to be welded are prepared by cleaning them thoroughly to remove any dirt, rust, or debris that could affect the weld quality. Next, the pipes are aligned and secured in place using clamps or a welding jig to ensure they are in the correct position for welding.
Once the pipes are properly aligned, the welding machine is set up and the appropriate welding parameters are selected based on the type of metal being welded and the thickness of the pipes. The welding machine is then turned on, and the welding electrode or wire is fed into the welding arc to create the weld. The welder moves the welding torch along the seam of the pipes, creating a strong and durable weld.
It is important to maintain a steady hand and consistent welding speed to ensure a uniform and high-quality weld. Additionally, proper ventilation and safety measures should be in place to protect the welder from fumes and sparks generated during the welding process.
After the welding is completed, the weld should be inspected for any defects or imperfections. Any defects should be repaired promptly to ensure the weld meets the required standards.
In conclusion, using a pipe welding machine requires careful preparation, proper setup, steady hands, and attention to detail. By following these steps and best practices, a strong and reliable weld can be achieved.
Quality Testing Methods for pipe welding machine and how to control the quality
There are several quality testing methods for a pipe welding machine, including visual inspection, ultrasonic testing, radiographic testing, and dye penetrant testing.
Visual inspection involves visually examining the welded joints for any defects, such as cracks or lack of fusion. Ultrasonic testing uses high-frequency sound waves to detect flaws or defects in the welds. Radiographic testing takes X-ray images of the welded joints to check for any internal defects. Dye penetrant testing involves applying a dye to the welded joints, which then seeps into any cracks or defects, making them visible under ultraviolet light.
To control the quality of pipe welding machine, it is important to ensure that all welders are properly trained and certified in the specific welding processes being used. Additionally, regular maintenance and calibration of the welding machine is necessary to ensure accurate and consistent results. Proper cleaning and preparation of the welded surfaces before welding also play a crucial role in ensuring quality.
It is essential to establish a quality control plan that outlines the specific testing methods to be used, the frequency of testing, and the acceptance criteria for the welds. Monitoring and documenting the results of the quality testing is also important to ensure that any defects are identified and corrected in a timely manner.
In conclusion, by utilizing a combination of quality testing methods, enforcing proper training and maintenance procedures, and implementing a thorough quality control plan, the quality of the pipe welding machine can be effectively controlled.
pipe welding machine Sample Policy and Post-Purchase Considerations for pipe welding machine from China
When purchasing a pipe welding machine from China, it is important to have a clear understanding of the supplier’s sample policy and post-purchase considerations.
Sample Policy: Before placing a bulk order, it is advisable to request a sample of the pipe welding machine to ensure its quality and suitability for your specific requirements. Many Chinese suppliers offer samples at a discounted rate or even for free, with the buyer usually responsible for shipping costs. Make sure to clarify if the sample cost will be deducted from the final order and inquire about the lead time for receiving the sample.
Post-Purchase Considerations: After purchasing the pipe welding machine, there are several important post-purchase considerations to keep in mind. Firstly, consider the warranty and after-sales service provided by the supplier. Ensure that you have a clear understanding of the warranty terms, including the duration and coverage of repairs or replacements. Additionally, inquire about the availability of spare parts and technical support in case of any issues with the machine.
Furthermore, establish a communication channel with the supplier to address any concerns or queries that may arise after the purchase. It is beneficial to maintain a good relationship with the supplier for future orders or potential issues that may require assistance.
In conclusion, it is essential to pay attention to the sample policy and post-purchase considerations when purchasing a pipe welding machine from China. By clarifying these aspects with the supplier, you can ensure a smooth and satisfactory transaction.
Sourcing pipe welding machine from China: Opportunities, Risks, and Key Players
Sourcing pipe welding machines from China can offer numerous opportunities for businesses looking for cost-effective solutions and access to advanced technology. China is known for its manufacturing prowess and offers a wide range of machine options, including pipe welding machines, at competitive prices.
One of the main advantages of sourcing from China is the cost advantage. The lower labor costs and economies of scale allow Chinese manufacturers to offer products at lower prices compared to their counterparts in other countries. This can help businesses save significantly on their procurement costs, making it an attractive option for small and large enterprises alike.
Another opportunity lies in the availability of advanced technology. China has been investing heavily in research and development, resulting in the production of high-quality, technologically advanced pipe welding machines. These machines come with features such as automation, precision, and efficiency, enabling businesses to enhance their welding processes and improve productivity.
However, there are certain risks associated with sourcing from China. Quality control is a crucial factor to consider, as the market is vast and comprises various manufacturers. It is essential to select reliable and reputable suppliers that adhere to international quality standards. Conducting thorough due diligence, including requesting product samples, inspecting manufacturing facilities, and checking references, can help mitigate these risks.
Additionally, communication and language barriers can pose challenges during the sourcing process. Engaging with suppliers who have English-speaking staff or arranging for translators can help bridge this gap and ensure effective communication.
When sourcing pipe welding machines from China, some key players to consider include Huawei, Suzhou Hanxin Machinery Equipment Co., Ltd, Hangzhou Haizhu MIM Products Co., Ltd, and Jiangsu Soho International Group Yangzhou Co., Ltd. These companies have a strong presence in the market and offer a range of pipe welding machines to suit different requirements.
In conclusion, sourcing pipe welding machines from China presents opportunities for cost savings and access to advanced technology. However, it is crucial to conduct proper due diligence and select reliable suppliers. Engaging with key players in the market can help businesses find the right machine and ensure a successful sourcing process.
How to find and select reliable pipe welding machine manufacturers in China,use google search manufacturers and suppliers
When looking for reliable pipe welding machine manufacturers in China, the best place to start is by using Google search to find manufacturers and suppliers. You can simply type in keywords like “pipe welding machine manufacturers in China” or “China pipe welding machine suppliers” to get a list of potential companies to consider.
Once you have a list of manufacturers, it is important to do your due diligence in researching each company. Look for reviews and feedback from past customers to gauge the reliability and quality of their products. Check if they have certifications or quality assurance measures in place to ensure the durability and safety of their machines.
It is also recommended to reach out to the manufacturers directly to ask about their experience, production capabilities, and any specific requirements you may have for your project. This will give you a better sense of the manufacturer’s professionalism and ability to meet your needs.
Consider factors such as price, delivery time, warranty, and after-sales service when selecting a manufacturer. It is important to choose a company that not only offers high-quality products but also provides excellent customer support throughout the purchasing process.
By thoroughly researching and vetting potential pipe welding machine manufacturers in China, you can ensure that you select a reliable and reputable company to supply you with the equipment you need for your project.
How to check pipe welding machine manufacturers website reliable,use google chrome SEOquake check if ranking in top 10M
One way to check the reliability of a pipe welding machine manufacturer’s website is to use Google Chrome’s SEOquake tool to see if the website ranks in the top 10 search results for relevant keywords. Websites that consistently appear in the top search results are more likely to be reputable and trustworthy.
To use SEOquake, first install the SEOquake extension in Google Chrome. Then, enter relevant keywords related to pipe welding machines in the search bar and see if the manufacturer’s website appears in the top 10 search results. If the website does not rank in the top 10, it may not be as reliable or trustworthy as other websites that do.
Additionally, you can also look for testimonials, reviews, and certifications on the manufacturer’s website to further validate its credibility. A reliable manufacturer will often provide detailed information about their products, certifications, and customer reviews to showcase their expertise and reputation in the industry.
In summary, using Google Chrome’s SEOquake tool to check if a pipe welding machine manufacturer’s website ranks in the top search results can help determine its reliability. Additionally, looking for testimonials, reviews, and certifications on the website can also provide further validation of the manufacturer’s credibility.
Top 10 pipe welding machine manufacturers in China with each 160 words introduce products,then use markdown create table compare
1. Huizhou Shengyang Industrial Co., Ltd. specializes in the production of pipe welding machines, including automatic tube welding machines and robotic pipe welding machines. These machines are known for their high efficiency and precision in welding various types of pipes.
2. Hangzhou Grand Technology Co., Ltd. offers a range of pipe welding machines, such as orbital welding machines and automatic pipe welding machines. These machines are designed for industrial applications and ensure consistent and reliable welds.
3. Wuxi ABK Machinery Co., Ltd. manufactures pipe welding machines, including spiral pipe welding machines and longitudinal pipe welding machines. These machines are known for their superior performance and durability in welding large diameter pipes.
4. Shanghai TAYOR Heavy Industry Group Co., Ltd. produces a variety of pipe welding machines, such as portable pipe welding machines and automated pipe welding systems. These machines are widely used in the construction and manufacturing industries for their ease of use and high quality welds.
5. Jiangsu Soho International Group Wuxi Co., Ltd. offers pipe welding machines, including manual pipe welding machines and automatic pipe welding machines. These machines are designed for welding a variety of pipes with different materials and thicknesses.
| Manufacturer | Products | Features |
| — | — | — |
| Huizhou Shengyang Industrial Co., Ltd. | Automatic tube welding machines, robotic pipe welding machines | High efficiency, precision welding |
| Hangzhou Grand Technology Co., Ltd. | Orbital welding machines, automatic pipe welding machines | Consistent and reliable welds |
| Wuxi ABK Machinery Co., Ltd. | Spiral pipe welding machines, longitudinal pipe welding machines | Superior performance, durability |
| Shanghai TAYOR Heavy Industry Group Co., Ltd. | Portable pipe welding machines, automated pipe welding systems | Ease of use, high quality welds |
| Jiangsu Soho International Group Wuxi Co., Ltd. | Manual pipe welding machines, automatic pipe welding machines | Versatile welding capabilities |
Background Research for pipe welding machine manufacturers Companies in China, use qcc.com archive.org importyeti.com
When looking for pipe welding machine manufacturers in China, you can start by using platforms such as qcc.com, archive.org, and importyeti.com to conduct background research on potential companies. These platforms provide valuable information on the companies’ history, products, certifications, and customer reviews, helping you make an informed decision.
Qcc.com is a professional platform that provides detailed company profiles, including contact information, business scope, and registration details. By accessing this platform, you can verify the legitimacy of pipe welding machine manufacturers in China, ensuring that you are dealing with reliable and reputable companies.
Archive.org is a valuable tool for researching the history of pipe welding machine manufacturers in China. By accessing archived web pages of the companies’ websites, you can track their growth and development over time, as well as view any past products or services they may have offered.
Importyeti.com is a comprehensive database that provides real-time data on import and export activities of companies in China. By using this platform, you can gather valuable information on the market presence and international reputation of pipe welding machine manufacturers, helping you assess their competitiveness and reliability.
By utilizing these platforms, you can easily conduct background research on pipe welding machine manufacturers in China, ensuring that you partner with a trustworthy and capable company for your welding needs.
Leveraging Trade Shows and Expos for pipe welding machine Sourcing in China
Trade shows and expos present excellent opportunities for sourcing pipe welding machines in China. These events bring together numerous manufacturers, suppliers, and industry professionals under one roof, making it easier for businesses to explore and connect with potential suppliers. By attending trade shows and expos, companies can leverage the following benefits for sourcing pipe welding machines in China.
1. Extensive Supplier Network: Trade shows and expos feature a diverse range of exhibitors, including manufacturers, suppliers, and distributors specializing in pipe welding machines. This provides businesses with a wide array of options to explore and compare different products, specifications, and pricing.
2. Face-to-Face Communication: Trade shows and expos facilitate direct face-to-face interaction between buyers and suppliers. This allows businesses to discuss their specific requirements, negotiate prices, and establish personal connections with potential suppliers. Such communication is crucial for building trust and ensuring a reliable supply chain.
3. Hands-on Product Inspection: Trade shows and expos offer the opportunity to physically examine and test the pipe welding machines. Companies can evaluate the build quality, functionality, and performance of the machines, ensuring they meet their specific needs and quality standards.
4. Stay Updated with Industry Trends: Trade shows and expos showcase the latest advancements in pipe welding technology. By attending these events, businesses can stay informed about the latest trends, innovations, and techniques in the industry, enabling them to make informed sourcing decisions.
5. Gather Market Intelligence: In addition to sourcing pipe welding machines, trade shows and expos provide valuable insights into the market landscape. Companies can gather information on market trends, competitor analysis, and emerging technologies, helping them develop a competitive advantage.
To maximize the effectiveness of attending trade shows and expos, companies should be prepared with clear sourcing objectives, establish a budget, and conduct thorough research on the exhibitors. Additionally, networking with industry peers and attending relevant seminars or conferences can provide additional opportunities for sourcing pipe welding machines in China.
The Role of Agents and Sourcing Companies in Facilitating pipe welding machine Purchases from China
Agents and sourcing companies play a crucial role in facilitating pipe welding machine purchases from China by acting as intermediaries and guiding customers through the entire process. These professionals have in-depth knowledge of the Chinese market, including suppliers, manufacturers, and pricing trends. They help customers navigate the complexities of sourcing products from China, including language barriers, cultural differences, and unfamiliar business practices.
Agents and sourcing companies connect customers with reliable and reputable suppliers, ensuring that they are getting high-quality products at competitive prices. They also handle negotiations, contract agreements, quality control, and product inspections on behalf of the customer, saving them time and resources. By leveraging their network of contacts and relationships with Chinese manufacturers, agents and sourcing companies can help customers access a wide range of pipe welding machine options and customize orders to meet their specific needs.
Additionally, agents and sourcing companies can provide valuable guidance and support throughout the purchasing process, from sourcing and procurement to shipping and delivery. They act as a trusted partner and advocate for customers, ensuring that their interests are protected and that the entire transaction is completed smoothly and efficiently. Overall, agents and sourcing companies are instrumental in facilitating pipe welding machine purchases from China by streamlining the process, reducing risks, and ultimately helping customers make informed decisions and secure the best possible deals.
Price Cost Research for pipe welding machine manufacturers Companies in China, use temu.com and 1688.com
When conducting price cost research for pipe welding machine manufacturers in China, websites like temu.com and 1688.com can be valuable resources. These platforms provide a wide range of suppliers and allow for efficient comparison shopping. Here is a brief overview of how to conduct research and keep within a 300-word limit:
To begin, visit temu.com and search for pipe welding machine manufacturers in China. Browse through the list of suppliers and make note of their product offerings, certifications, and any relevant customer reviews. Pay attention to the overall reputation of the manufacturers and their experience in the industry. Look for manufacturers with a solid track record of producing high-quality machines.
Next, visit 1688.com, a popular Chinese B2B website. Conduct a similar search for pipe welding machines and explore the options available. Take note of the prices listed by different manufacturers. Look for features, such as welding capacity, power consumption, and automation capabilities. Consider the warranty and after-sales support provided by the manufacturers.
When comparing prices on both platforms, it is essential to consider the quality and reliability of the machines offered. While some manufacturers may offer lower prices, they might compromise on quality. Look for manufacturers that strike a balance between affordability and quality.
Additionally, pay attention to any additional costs that may be involved in purchasing from China, such as shipping fees, import duties, and taxes. These factors can significantly impact the overall cost of the machine. It’s advisable to contact different manufacturers directly to inquire about shipping and any applicable fees.
Lastly, gather all the relevant information and narrow down your options based on price, quality, and reputation. Reach out to selected manufacturers to request a detailed quotation that includes all the necessary specifications and terms of sale.
In conclusion, temu.com and 1688.com are valuable platforms to conduct price cost research for pipe welding machine manufacturers in China. By considering factors such as reputation, product quality, additional costs, and warranty, you can make an informed decision within the 300-word limit.
Shipping Cost for pipe welding machine import from China
The shipping cost for importing a pipe welding machine from China can vary depending on several factors such as the weight of the machine, the dimensions of the package, the shipping method chosen, and the destination country.
Typically, for a standard-sized pipe welding machine weighing around 500 kg, the shipping cost from China to most Western countries can range from $800 to $2000. Air freight is generally the fastest but most expensive option, while sea freight is more cost-effective but takes longer.
It is recommended to obtain quotes from different shipping companies or freight forwarders to compare prices and services. Some companies may offer discounts for bulk shipments or have special rates for certain destinations.
Additionally, it is important to consider other import-related costs such as customs duties, import taxes, insurance, and handling fees. These additional fees can significantly increase the overall cost of importing the machine.
Overall, it is crucial to carefully plan and budget for all shipping and import-related costs to ensure a smooth and cost-effective import process for the pipe welding machine from China.
Compare China and Other pipe welding machine Markets: Products Quality and Price,Visible and Hidden Costs
China is a significant player in the pipe welding machine market, but how does it compare to other markets in terms of product quality and price, as well as visible and hidden costs? Let’s explore these factors below.
In terms of product quality, China’s pipe welding machines have witnessed significant improvements over the years. Chinese manufacturers have invested in research and development to enhance the technology and performance of their machines. While the quality may not be as high as some other established markets like Germany or Japan, Chinese manufacturers have made strides in narrowing the gap. However, it’s important to note that some lower-quality products may also be available in the Chinese market due to the wide range of manufacturers and suppliers.
When it comes to price, China offers a competitive advantage. Chinese pipe welding machines are generally more affordable compared to those from other markets. The lower labor and production costs in China contribute to this price advantage. This affordability has made Chinese machines attractive to buyers worldwide, especially in price-sensitive markets. However, it’s crucial to carefully evaluate the balance between price and quality to ensure the optimal investment in a pipe welding machine.
Visible costs, such as the initial purchase price, are relatively straightforward to compare between China and other markets. The lower prices of Chinese machines are advantageous in this aspect. However, when considering hidden costs, there may be additional factors to consider. For instance, warranty and after-sales service are essential elements to analyze. While Chinese manufacturers have been improving their customer service, some customers have reported challenges in terms of communication and response time. Additionally, it’s important to consider the availability and cost of spare parts, as well as the longevity and durability of the machines.
In summary, China’s pipe welding machine market has made significant strides in terms of product quality, although it may still lag behind established players. However, China’s prices are generally more competitive, offering an advantage in affordability. Visible costs, such as the initial purchase price, lean towards China’s favor, but hidden costs such as after-sales service and spare parts availability should be considered in the decision-making process. Buyers should carefully evaluate their requirements and expectations to strike a balance between quality, price, and overall costs.
Understanding Pricing and Payment Terms for pipe welding machine: A Comparative Guide to Get the Best Deal
When it comes to purchasing a pipe welding machine, understanding the pricing and payment terms is crucial to ensure you get the best deal. This comparative guide aims to provide essential insights into the pricing structure and payment options available, helping you make an informed decision within the confines of 300 words.
1. Pricing Structure:
The first step is to understand the different pricing structures utilized by vendors. Typically, pipe welding machines have a base price that includes the basic machine without any additional accessories or customization. However, some vendors may bundle additional features and accessories into their base price. It is essential to compare the base price of different vendors to gauge the value offered.
2. Customization Costs:
If you require any specific customization to meet your project requirements, there may be additional costs involved. It is crucial to clarify the customization options and associated costs upfront with the vendor to avoid any surprises later.
3. Additional Accessories and Consumables:
Apart from the machine itself, it is essential to consider the cost of additional accessories such as welding torches, wires, and consumables like shielding gas. These costs can vary greatly across vendors, so compare the prices of these accessories to understand the overall cost of ownership.
4. Financing and Payment Options:
Evaluate the financing and payment options available to determine the most suitable arrangement for your budget. Some vendors offer financing options, such as installment plans or leasing, which can help distribute the upfront cost over a specified period. Compare the interest rates and terms offered by different vendors to choose the most cost-effective option.
5. Warranty and After-sales Support:
Consider the warranty provided by the vendor and the availability of after-sales support. A longer warranty period can be indicative of a higher-quality product. Additionally, vendors offering extensive after-sales support can be more beneficial in case of any technical issues or maintenance requirements.
In conclusion, when purchasing a pipe welding machine, compare the base price and customization costs among different vendors, consider additional accessories and consumables’ prices, evaluate financing and payment options, and assess the warranty and after-sales support offered. By understanding these elements and conducting thorough market research, you can secure the best deal for your pipe welding machine, meeting both your budget and project requirements effectively.
Chinese Regulations and Industry Standards Certifications for pipe welding machine,Import Regulations and Customs for pipe welding machine from China
Chinese Regulations and Industry Standards Certifications for pipe welding machines include the GB/T 15579.1-2005 standard, which specifies performance requirements for welding machines used in the production of pipes. The use of GB/T 15579.1-2005 certified machines ensures compliance with safety and quality standards in China’s welding industry.
Import Regulations and Customs for pipe welding machines from China require adherence to customs regulations and documentation. Importers must obtain the necessary permits and licenses, such as the Import License of Industrial Products and the China Compulsory Certification (CCC) for certain products. Additionally, importers must comply with China’s customs regulations, including correct labeling, packaging, and declaration of imported goods.
Importers of pipe welding machines from China should also be aware of any additional requirements specific to their country of import. For example, some countries may have restrictions on certain types of machinery, require additional testing or certification, or have tariffs and import duties that must be paid.
Overall, compliance with Chinese Regulations and Industry Standards Certifications, as well as attention to Import Regulations and Customs requirements, is essential for a smooth import process of pipe welding machines from China. Importers should work closely with customs agents and legal advisors to ensure compliance with all relevant regulations and standards.
Sustainability and Environmental Considerations in pipe welding machine Manufacturing
Sustainability and environmental considerations play a crucial role in the manufacturing of pipe welding machines. These considerations not only help in reducing the negative impact on the environment but also contribute to the long-term sustainability of the manufacturing process.
One important aspect is the selection of materials. Using eco-friendly materials in the production of pipe welding machines can significantly reduce the carbon footprint. Manufacturers can opt for materials that are recyclable, have lesser energy-intensive production processes, and emit lower levels of greenhouse gases.
Efficient energy consumption is another key factor. Implementing energy-saving measures in the manufacturing process, such as using energy-efficient machinery, can reduce the overall energy consumption. This results in a lower environmental impact and also provides cost savings for the manufacturer.
Waste management is an integral part of sustainable manufacturing. Employing proper waste management techniques, such as recycling scrap metals and other waste materials, can help minimize landfill waste and reduce the need for additional raw materials. Additionally, using environmentally friendly cleaning agents and processes further reduces pollution and waste generation.
Transportation and logistics also contribute to the overall sustainability of pipe welding machine manufacturing. Manufacturers can try to reduce the distance traveled by optimizing the supply chain. This includes sourcing materials and components locally and utilizing efficient transportation methods. This not only reduces greenhouse gas emissions but also supports local economies.
Furthermore, manufacturers can prioritize the development of products that have a longer lifespan and require minimal maintenance. By producing durable and reliable pipe welding machines, manufacturers can reduce the need for frequent replacements, thereby reducing the consumption of resources and the generation of waste.
In conclusion, sustainability and environmental considerations are essential in pipe welding machine manufacturing. By focusing on material selection, energy efficiency, waste management, transportation, and product durability, manufacturers can minimize their environmental impact and contribute to a more sustainable future.
List The Evolution history of “pipe welding machine”
Pipe welding machines have evolved significantly over the years, with new technologies and techniques that have revolutionized the welding industry. From manual processes to automated systems, here is a brief history of the evolution of pipe welding machines:
1. Manual Welding: During the early days of pipe welding, the process was mainly manual, with welders using hand tools and torches to weld pipes together. This method required high skill levels and was time-consuming.
2. Shielded Metal Arc Welding (SMAW): In the mid-20th century, SMAW, also known as stick welding, became popular for pipe welding. This technique involved using a consumable electrode coated in flux, which provided shielding gas to protect the weld from atmospheric contamination.
3. Gas Tungsten Arc Welding (GTAW): In the 1960s, GTAW, also known as TIG (Tungsten Inert Gas) welding, gained popularity for pipe welding. This method used a non-consumable tungsten electrode and an inert gas, such as argon, to produce high-quality welds with precise control.
4. Submerged Arc Welding (SAW): Submerged arc welding was developed in the 1930s but gained popularity in pipe welding in the 1970s. It involved the formation of an arc between a continuously fed wire electrode and the workpiece, with a granular flux covering the weld during the process.
5. Automatic Welding: With advances in technology, semi-automatic and automatic pipe welding machines were developed. These machines incorporated motorized systems to control the welding process, reducing the manual effort and increasing productivity.
6. Robotic Welding Systems: In recent years, robotics have made significant contributions to pipe welding. Robotic welding systems use programmable robots to perform precise and repetitive welding tasks. These systems can follow weld paths with high accuracy and improve overall efficiency.
7. Orbital Welding: Orbital welding machines were introduced in the 1960s and gained popularity in the 1980s. They are mainly used for welding high-purity piping systems and consist of a power supply, control console, and a welding head that rotates around the pipe. Orbital welding offers excellent repeatability and is commonly used in industries like pharmaceuticals and food processing.
8. Hybrid Welding Systems: Modern pipe welding machines often combine various welding processes to achieve optimal results. For example, a machine may combine the advantages of GTAW and SAW to increase productivity and weld quality.
In conclusion, the evolution of pipe welding machines has gone from manual processes to automated and robotic systems, increasing productivity, precision, and efficiency. These advancements have transformed the welding industry and allowed for the fabrication of high-quality pipe systems in various industries.
The Evolution and Market Trends in pipe welding machine Industry
The pipe welding machine industry has experienced significant evolution in recent years, driven by advancements in technology and the increasing demand for high-quality, efficient welding solutions.
One of the major trends in the industry is the shift towards automated and robotic welding systems, which offer increased precision, speed, and consistency compared to manual welding methods. These machines are also equipped with advanced sensors and monitoring systems that can detect defects and adjust welding parameters in real-time, leading to higher welding quality and productivity.
Another key trend in the pipe welding machine industry is the integration of Industry 4.0 technologies, such as Internet of Things (IoT) connectivity and data analytics, into welding machines. This allows for remote monitoring and control of welding processes, predictive maintenance, and optimization of welding parameters, leading to improved efficiency and cost savings for manufacturers.
Furthermore, there is a growing emphasis on sustainability in the industry, with manufacturers developing pipe welding machines that use eco-friendly materials, consume less energy, and produce fewer emissions. This is in response to increasing regulations and consumer demand for greener manufacturing practices.
Overall, the pipe welding machine industry is experiencing rapid growth and innovation, driven by technological advancements, changing market demands, and a focus on sustainability. Manufacturers who can adapt to these trends and offer cutting-edge solutions will be well-positioned to succeed in this competitive market.
Custom Private Labeling and Branding Opportunities with Chinese pipe welding machine Manufacturers
Chinese pipe welding machine manufacturers offer custom private labeling and branding opportunities for businesses looking to establish their own identity in the market. These manufacturers have extensive experience in producing high-quality pipe welding machines and can cater to the specific requirements of their clients.
With custom private labeling, businesses can imprint their own brand name and logo on the welding machines, creating a unique and distinct identity for their products. This helps in brand recognition and differentiation from competitors. Chinese manufacturers have the necessary infrastructure and expertise to handle private labeling requests efficiently and effectively.
Additionally, these manufacturers also offer branding opportunities by providing customization options for the machines. This can include modifications in design, functionality, or features to align with the business’s specific needs. Manufacturers can work closely with clients to understand their requirements and create tailored pipe welding machines that reflect the brand’s vision and values.
Partnering with Chinese pipe welding machine manufacturers for private labeling and branding not only allows businesses to establish their own identity but also offers cost-effective solutions. Chinese manufacturers typically offer competitive pricing without compromising on the quality of the products.
The Chinese manufacturing industry is known for its efficiency, flexibility, and adaptability. This makes it an ideal choice for businesses looking to capitalize on custom private labeling and branding opportunities. By leveraging the capabilities of Chinese pipe welding machine manufacturers, businesses can enhance their market presence and establish themselves as a reliable and trusted brand within the industry.
Tips for Procurement and Considerations when Purchasing pipe welding machine
When purchasing a pipe welding machine, it is important to consider several factors to ensure you choose the right one for your needs. Here are some tips and considerations to keep in mind:
1. Welding Process: Determine the type of welding process needed for your specific application. Common processes include TIG (Tungsten Inert Gas), MIG (Metal Inert Gas), and Stick welding. Choose a machine that supports the desired welding process.
2. Power Source: Consider the power source available in your facility, such as electric or gas. Ensure the welding machine is compatible with the power source and can deliver the required output.
3. Welding Capacity: Evaluate the thickness and diameter of the pipes you will be welding. Choose a machine that can handle the specific pipe sizes and thicknesses you work with to avoid limitations.
4. Weld Quality: Look for a machine that can produce high-quality welds consistently. Check for features like digital controls, advanced welding settings, and programmable memory function for better weld performance.
5. Portability: If you require mobility, consider a portable welding machine that is lightweight and easy to transport. This is crucial for fieldwork or when working on multiple job sites.
6. Duty Cycle: Check the machine’s duty cycle, which refers to the amount of time it can operate continuously without overheating. Ensure the duty cycle aligns with your welding requirements.
7. Ease of Use: Look for a machine with user-friendly controls and interfaces. The ease of use will help reduce training time and increase productivity.
8. Durability and Maintenance: Choose a machine made from robust materials to ensure durability, as welding machines are subjected to harsh working conditions. Consider ease of maintenance and availability of spare parts.
9. Safety Features: Prioritize machines with built-in safety features like overload protection, thermal shut-off, and grounding options. Check if the machine complies with applicable safety standards.
10. Price and Warranty: Compare prices from different suppliers while considering the machine’s features and quality. Also, check the warranty offered by the manufacturer to safeguard against defects or malfunctions.
In summary, selecting the right pipe welding machine involves considering the welding process, power source, welding capacity, weld quality, portability, duty cycle, ease of use, durability, safety features, and price. Taking the time to research and evaluate these factors will help ensure you choose a machine that meets your specific welding needs.
FAQs on Sourcing and Manufacturing pipe welding machine in China
1. How do I find a reliable supplier for pipe welding machines in China?
You can start by researching online or attending trade shows to find potential suppliers. It is crucial to verify their reputation, inspect their facilities, and request samples or references before making a decision.
2. What are the key factors to consider when sourcing pipe welding machines from China?
Key factors to consider include price, quality, lead time, after-sales service, and the supplier’s experience in manufacturing welding machines. It is also essential to consider factors such as compliance with industry standards and certifications.
3. Can I customize pipe welding machines from Chinese suppliers?
Yes, many Chinese suppliers offer customization services to meet specific requirements such as welding capacity, pipe diameter, and welding processes. It is important to communicate your needs clearly to ensure the supplier can deliver a machine that meets your specifications.
4. How can I ensure the quality of pipe welding machines manufactured in China?
To ensure the quality of pipe welding machines, you can request product samples, visit the supplier’s facilities for inspection, check for certifications and compliance with industry standards, and ask for customer references. Regular communication with the supplier throughout the manufacturing process is also crucial to address any quality issues.
5. What are the advantages of sourcing pipe welding machines from China?
Sourcing pipe welding machines from China offers cost-effective solutions, access to a wide range of suppliers with expertise in manufacturing welding equipment, and the ability to customize machines according to your specific requirements. Additionally, China has a well-developed manufacturing infrastructure and supply chain that can support your sourcing needs.
Why contact sourcifychina.com get free quota from reliable pipe welding machine suppliers?
Sourcifychina.com is able to obtain a free quota from reliable pipe welding machine suppliers due to its strong partnership and reputation within the industry.
Firstly, Sourcifychina.com has built long-term relationships with various reputable pipe welding machine suppliers in China. These suppliers trust Sourcifychina.com as a reliable and efficient sourcing platform, and value the opportunity to showcase their products and capabilities to a wider audience. To incentivize Sourcifychina.com to continue bringing them business, these suppliers are willing to offer the platform a certain number of free quota, allowing Sourcifychina.com to source pipe welding machines without additional cost.
Secondly, Sourcifychina.com has proven itself to be a valuable channel for these suppliers to expand their reach and connect with potential customers worldwide. By listing their products on Sourcifychina.com, these suppliers are able to tap into a larger customer base, which in turn increases their chances of securing more orders and growing their business. Consequently, offering a free quota to Sourcifychina.com is seen as a marketing expense and investment to attract more customers, leading to a mutually beneficial partnership.
Furthermore, Sourcifychina.com boasts a strong track record of successfully sourcing high-quality products for its clients. The platform has a rigorous vetting process and only works with reliable and reputable suppliers who can meet strict quality standards. This commitment to quality ensures that the free quota offered by suppliers through Sourcifychina.com corresponds to reliable and dependable pipe welding machines.
In conclusion, the partnerships and reputation built by Sourcifychina.com within the industry have enabled them to obtain a free quota from reliable pipe welding machine suppliers. These suppliers value the platform as a reliable sourcing channel and view the free quota as an opportunity to expand their customer base and increase business prospects.