Introduce about plastic injection guide,Qulity,Cost,Supplier,Certification,Market,Tips,FAQ
Plastic injection molding is a widely used manufacturing process for producing plastic parts in large volumes. This guide covers the basics of plastic injection molding, including the quality, cost, suppliers, certifications, market trends, tips, and frequently asked questions.
Quality is a crucial factor in plastic injection molding, as it affects the durability and functionality of the final products. High-quality molds, machines, and materials are essential for producing consistent and reliable plastic parts.
Cost is another important consideration in plastic injection molding, as it can vary depending on the complexity of the part, the quantity needed, and the materials used. Working with a reputable supplier can help reduce costs and maximize efficiency.
Choosing the right supplier is crucial for the success of a plastic injection molding project. Look for suppliers with experience, expertise, and a track record of producing high-quality plastic parts. It is also important to ensure that the supplier is certified and compliant with industry standards.
Certifications, such as ISO 9001, ensure that the supplier follows best practices and meets quality standards. This can help guarantee the quality and reliability of the plastic parts produced.
The plastic injection molding market is growing rapidly, driven by the demand for lightweight, durable, and cost-effective plastic parts in various industries. Keeping up with market trends can help manufacturers stay competitive and meet the needs of their customers.
Tips for successful plastic injection molding include designing parts for manufacturability, selecting the right materials, and optimizing the production process. Proper maintenance of molds and equipment is also important for ensuring consistent quality and efficiency.
Frequently asked questions about plastic injection molding include topics such as tooling, design considerations, material selection, and cost factors. Understanding these key aspects can help manufacturers make informed decisions and achieve optimal results in their plastic injection molding projects.
Types of plastic injection
There are several types of plastic injection molding processes that can be used to produce a wide range of plastic products. These processes each offer unique benefits and are suited to different manufacturing needs.
The most common type of plastic injection molding is known as thermoplastic injection molding. This process involves heating plastic pellets to a molten state and then injecting the material into a mold where it cools and solidifies to form the desired shape. Thermoplastic injection molding is popular because it allows for high production speeds, precise control over part dimensions, and the ability to produce complex shapes with intricate details.
Another type of plastic injection molding is thermoset injection molding. This process involves heating a thermosetting plastic resin to a specific temperature and then injecting it into a mold where it undergoes a chemical reaction to harden into a final shape. Thermoset injection molding is often used to produce parts that require high heat resistance or superior dimensional stability.
Liquid silicone rubber (LSR) injection molding is another type of plastic injection molding that is commonly used to produce parts that require flexibility, durability, and resistance to extreme temperatures. LSR injection molding involves injecting liquid silicone rubber into a mold where it is cured to form a final part. This process is popular for producing medical devices, automotive components, and consumer electronics.
In addition to these common types of plastic injection molding, there are also specialty processes such as overmolding, insert molding, and multi-shot molding that allow for the production of more complex parts with multiple materials or components. Each of these processes offers unique advantages and can be tailored to specific manufacturing requirements.
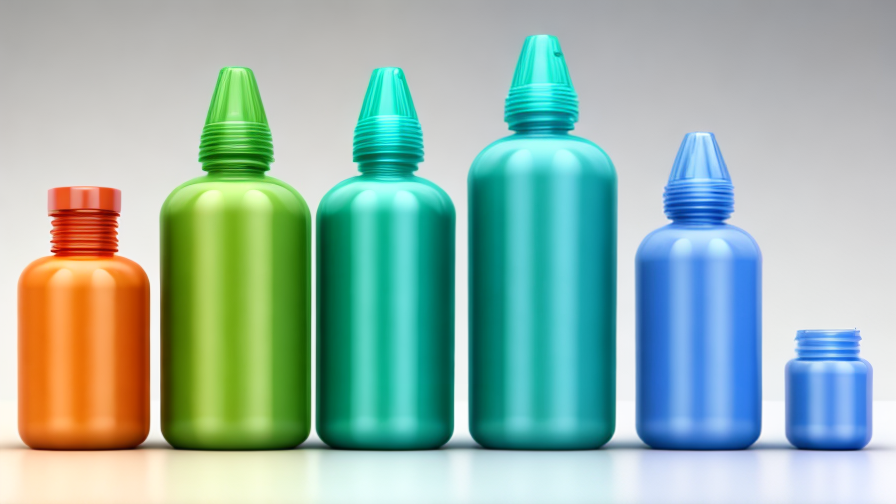
Pros and Cons of Using plastic injection
Plastic injection molding is a widely-used manufacturing process for producing plastic parts in large quantities. There are several pros and cons associated with using plastic injection molding.
Pros:
1. Cost-effective: Plastic injection molding is a cost-effective method for producing large quantities of identical plastic parts. The initial tooling costs can be high, but the unit cost of manufacturing each part is relatively low, making it a cost-effective solution for mass production.
2. Fast production: Plastic injection molding is a fast process, with cycle times ranging from a few seconds to a few minutes, depending on the size and complexity of the part. This results in high production output and quick lead times.
3. Design flexibility: Plastic injection molding allows for complex and intricate designs to be produced with high precision. It enables the production of parts with varying thicknesses, textures, and finishes.
4. Material variety: Plastic injection molding can be used with a wide range of thermoplastic and thermosetting materials, allowing for flexibility in choosing the material properties to suit the application requirements.
5. Minimal waste: Plastic injection molding generates minimal waste as scrap material can be recycled and reused in the production process.
Cons:
1. High initial costs: The initial tooling costs for plastic injection molding can be expensive, especially for complex and intricate parts. This can make it less suitable for small production runs or prototype development.
2. Design limitations: While plastic injection molding allows for complex designs, there are certain design limitations that need to be considered, such as draft angles, undercuts, and wall thickness variations.
3. Long lead times: Despite the fast production cycle times, the initial tooling and setup process for plastic injection molding can result in long lead times, especially for custom or complex parts.
4. Environmental impact: Plastic injection molding generates plastic waste, which can have a negative environmental impact if not properly managed and recycled. It is important to consider the sustainability aspects of using plastic materials in manufacturing processes.
In conclusion, plastic injection molding offers several advantages, such as cost-effectiveness, fast production, design flexibility, material variety, and minimal waste generation. However, there are also some drawbacks, including high initial costs, design limitations, long lead times, and environmental concerns. It is important for manufacturers to weigh these pros and cons when considering the use of plastic injection molding for their production needs.
plastic injection Reference Specifications (varies for different product)
Plastic injection reference specifications vary for different products, but they generally include specific requirements and guidelines to ensure the successful and optimal production of plastic components through the injection molding process.
One important aspect of these reference specifications is the material selection. Different plastic materials have varying properties, such as melt flow index, tensile strength, impact resistance, and heat resistance. The reference specifications define the specific material that should be used to meet the desired performance and functionality of the product.
The specifications also define the dimensional requirements of the plastic component. This includes details regarding the part’s size, shape, and tolerance limits. The reference specifications may specify critical dimensions that are crucial for the proper fit and assembly of the component into the final product.
Moreover, the reference specifications outline the cosmetic requirements for the plastic component. These requirements cover aspects such as surface finish, color, texture, and labeling. They ensure that the plastic parts meet the desired aesthetic appeal and branding requirements of the product.
In addition to material and dimensional requirements, the specifications also provide guidelines for the injection molding process itself. This includes the recommended injection pressure, temperature, cooling time, and cycle time. The specifications may also mention specific injection molding machine parameters or settings that should be used to achieve the desired quality and consistency of the plastic parts.
Furthermore, the reference specifications may include information on post-processing requirements. This could involve any additional operations, such as trimming, painting, or assembly, that need to be performed after the injection molding process. The specifications may provide instructions or limitations for these secondary processes to ensure the overall product quality.
By adhering to these plastic injection reference specifications, manufacturers can ensure that the final plastic components meet the desired quality, functionality, and appearance. These specifications act as a comprehensive guide throughout the entire production process, enabling consistent and reliable manufacturing of plastic products.
Applications of plastic injection
Plastic injection molding is a versatile manufacturing process that is used in various industries to produce a wide range of products. Some common applications of plastic injection include:
1. Automotive industry: Plastic injection molding is widely used in the automotive industry for manufacturing parts such as bumpers, dashboards, interior trim, and more. It is preferred for its ability to produce complex geometries with high precision and consistency.
2. Consumer goods: Plastic injection molding is used to produce a wide range of consumer goods such as toys, containers, household appliances, and electronic devices. The process allows for cost-effective production of large quantities of products with consistent quality.
3. Medical devices: Plastic injection molding is used in the medical industry to produce various devices such as syringes, tubes, containers, and surgical instruments. The process ensures sterile and precise manufacturing of medical products.
4. Packaging industry: Plastic injection molding is commonly used in the packaging industry to produce containers, caps, and closures for various products. The process allows for the production of lightweight and durable packaging solutions.
5. Aerospace industry: Plastic injection molding is used in the aerospace industry to manufacture components such as interior panels, ducting systems, and seating components. The process is preferred for its ability to produce lightweight and strong components.
Overall, plastic injection molding is a widely used manufacturing process that offers flexibility, efficiency, and cost-effectiveness in producing a wide range of products across different industries.
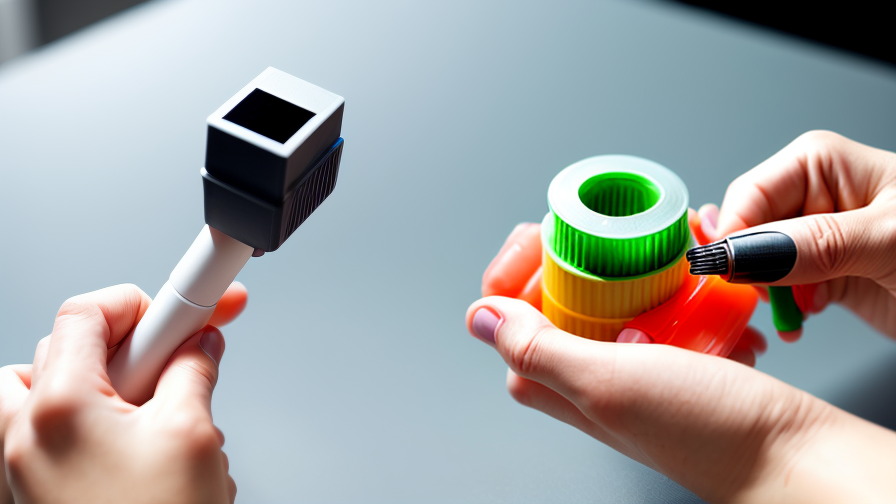
The Work Process and how to use plastic injection
Plastic injection is a manufacturing process used to produce plastic parts by injecting molten plastic material into a mold. This process is widely used in various industries due to its efficiency, versatility, and cost-effectiveness.
The work process of plastic injection involves several stages. First, the design of the plastic part is created using CAD (Computer-Aided Design) software. This design serves as the basis for creating the mold. Once the design is finalized, the mold is manufactured using CNC (Computer Numerical Control) machines. The mold is typically composed of two halves, an injection side, and an ejection side.
The next step is the preparation of the plastic material. Plastic pellets or granules are fed into a hopper and transported to the heating chamber of an injection molding machine. The pellets are then melted by heat and pressure, forming a molten plastic material.
After the plastic material has melted, it is injected into the mold cavity under high pressure. The mold holds the molten plastic in its desired shape and allows it to cool and solidify. Once the plastic has solidified, the mold opens, and the part is ejected using ejector pins or air blasts.
The final step of the plastic injection process is the finishing of the part. This may involve trimming excess material, removing any imperfections, or adding additional features through secondary operations such as machining or assembly.
To use plastic injection effectively, certain considerations must be taken into account. These include selecting the appropriate plastic material for the desired part properties, designing the mold with proper gating, venting, and cooling channels, and ensuring the injection molding machine is set up correctly for the specific material being used.
Plastic injection offers numerous advantages, such as the ability to produce complex shapes with high precision, fast production cycles, and the potential for high-volume manufacturing. It is commonly employed in industries like automotive, electronics, consumer goods, and medical devices.
In conclusion, plastic injection is a widely used manufacturing process that involves the injection of molten plastic into a mold to produce parts. Through careful design and optimization, this process can efficiently and effectively produce high-quality plastic parts for various applications.
Quality Testing Methods for plastic injection and how to control the quality
There are several quality testing methods for plastic injection that can help ensure the final product meets all necessary specifications. Some common methods include visual inspection, dimensional testing, mechanical testing, and material analysis.
Visual inspection involves visually examining the finished product for any defects such as warping, cracks, or surface blemishes. Dimensional testing checks the product’s dimensions to ensure they match the required specifications. Mechanical testing involves testing the product’s strength, flexibility, and durability to ensure it can withstand the necessary forces and conditions. Material analysis involves analyzing the chemical composition of the plastic material used to ensure it meets all necessary requirements.
To control the quality of plastic injection products, it is important to implement strict quality control measures throughout the manufacturing process. This can include monitoring the injection molding machine settings, regularly inspecting the molds for any wear or damage, and testing the final products for defects before they are shipped to customers.
Additionally, it is important to work closely with suppliers to ensure that the plastic material meets all necessary quality standards. Regularly training employees on proper manufacturing techniques and quality control procedures can also help maintain high-quality standards.
Overall, by implementing rigorous quality testing methods and closely monitoring the manufacturing process, the quality of plastic injection products can be effectively controlled to ensure they meet all necessary specifications.
plastic injection Sample Policy and Post-Purchase Considerations for plastic injection from China
Sample Policy:
When purchasing plastic injection products from China, it is important to establish a clear sample policy to ensure the products meet your specifications. Start by requesting a sample of the product before placing a bulk order. This will allow you to assess the quality, design, and functionality of the plastic injection products. Provide detailed specifications for the sample, including material, color, size, and any special features required. Once you have received the sample, evaluate it thoroughly and communicate any necessary modifications to the supplier. Ensure that the final product aligns with your expectations before proceeding with a larger order.
Post-Purchase Considerations:
After receiving your plastic injection products from China, there are several important considerations to keep in mind. Inspect the products upon arrival to ensure they meet the agreed upon specifications and quality standards. Address any issues or discrepancies with the supplier promptly to avoid any delays or misunderstandings. Consider developing a long-term relationship with the supplier to streamline future orders and maintain consistent product quality. Keep communication open and transparent to address any concerns or feedback. Additionally, consider implementing a quality control process to monitor the performance and durability of the plastic injection products over time. Regularly assess the supplier’s performance and product quality to ensure a successful partnership. By following these post-purchase considerations, you can ensure a smooth and successful experience when purchasing plastic injection products from China.
Sourcing plastic injection from China: Opportunities, Risks, and Key Players
Sourcing plastic injection from China offers numerous opportunities for businesses looking to benefit from cost-effective manufacturing and a wide range of suppliers. The country is home to many skilled and experienced plastic injection molding companies that can provide high-quality products at competitive prices. Additionally, China’s vast industrial base and advanced technology make it an attractive destination for companies seeking to outsource their plastic injection needs.
However, sourcing from China also comes with certain risks, such as quality control issues, intellectual property concerns, and logistical challenges. It is essential for businesses to conduct thorough due diligence on potential suppliers and establish clear communication channels to mitigate these risks effectively.
Some key players in the Chinese plastic injection industry include well-known companies such as Haier, Foxconn, and BYD. These companies have established a strong reputation for their manufacturing capabilities and have the resources and expertise to handle large-scale production orders.
In conclusion, sourcing plastic injection from China can be a lucrative business strategy for companies looking to take advantage of cost savings and a diverse supplier base. However, it is crucial to carefully evaluate risks and choose reputable partners to ensure a successful outsourcing experience.
How to find and select reliable plastic injection manufacturers in China,use google search manufacturers and suppliers
Finding reliable plastic injection manufacturers in China can be a daunting task, but here are a few steps you can follow using Google search:
1. Start by performing a Google search using keywords such as “plastic injection manufacturers in China” or “reliable plastic injection suppliers in China.” This will generate a list of potential manufacturers to explore further.
2. Visit the websites of the manufacturers that appear in your search results. Look for detailed information about their company background, manufacturing capabilities, certifications, and quality control processes. Reputable manufacturers usually have well-designed websites with clear and professional content.
3. Check for customer reviews or testimonials on the manufacturers’ websites or other online platforms. These reviews can provide insights into the manufacturer’s track record, reliability, and customer satisfaction.
4. Verify the manufacturer’s credentials and certifications. Look for industry certifications like ISO 9001, ISO 14001, or certifications specific to the plastic injection molding industry such as TS16949. These certifications indicate the manufacturer’s commitment to quality standards and continuous improvement.
5. Contact the manufacturers directly to discuss your project requirements and assess their responsiveness. Good manufacturers should be prompt in their communication, willing to answer your questions, and offer guidance or suggestions based on their expertise.
6. Request sample products or prototypes from a few selected manufacturers to evaluate their product quality, surface finish, and adherence to your specifications. This will give you a tangible understanding of their manufacturing capabilities.
7. Evaluate each manufacturer’s pricing structure and compare it with other manufacturers. Be cautious of prices that seem too good to be true, as they may indicate compromises in quality or subpar materials.
8. Consider visiting the manufacturer’s facility in China if feasible. This can provide a firsthand look at their production process, quality control measures, and overall manufacturing capabilities. However, due to time and cost constraints, a physical visit might not always be possible.
By following these steps, you can identify and select reliable plastic injection manufacturers in China for your business needs. Remember, thorough research and due diligence are crucial in ensuring a successful partnership with a reputable manufacturer.
How to check plastic injection manufacturers website reliable,use google chrome SEOquake check if ranking in top 10M
When considering the reliability of a plastic injection manufacturer’s website, you can follow a few steps to gather information using Google Chrome’s SEOquake extension and some general guidelines:
1. Evaluate the website’s ranking: Install the SEOquake extension on your Google Chrome browser. Go to the plastic injection manufacturer’s website and perform a search on Google using relevant keywords. Look for SEOquake’s data on the page and check if the website ranks within the top 10 million websites (a lower number indicates a more popular and potentially reliable site).
2. Assess website design and functionality: A professional and well-designed website often indicates a reliable manufacturer. Evaluate if the website is user-friendly, loads quickly, and provides a positive browsing experience. Ensure that the content is relevant and up to date.
3. Verify contact information and address: Check if the website prominently displays clear contact information, including a physical address, email, and telephone number. A reliable manufacturer is transparent about their location and readily provides ways to contact them.
4. Investigate the manufacturer’s reputation: Look for customer reviews, testimonials, or case studies on their website. Reliable manufacturers often showcase positive feedback from satisfied clients. Additionally, search for the manufacturer’s name online and visit relevant forums or review sites to see if there are any complaints or negative feedback.
5. Check for certifications and quality standards: Reputable manufacturers usually adhere to industry standards and possess certifications such as ISO 9001 or ISO 13485. Look for these certifications on their website to ensure their commitment to quality.
6. Evaluate company history and experience: Research the manufacturer’s background and how long they have been in the industry. A well-established manufacturer with years of experience is generally more reliable.
7. Consider their range of services and capabilities: Check if the manufacturer offers a comprehensive range of plastic injection services and caters to your specific needs. A diverse portfolio and expertise in various industries can be a positive sign of reliability.
8. Look for transparency and professionalism: A reliable manufacturer will provide clear information about their processes, capabilities, and quality control measures. Transparency in pricing and policies is also crucial.
Remember, while using SEOquake can give you an idea of a website’s popularity, it does not guarantee reliability. It is essential to combine your findings with other factors mentioned above to make an informed decision.
Top 10 plastic injection manufacturers in China with each 160 words introduce products,then use markdown create table compare
1. Sinotech Sinotech is a leading plastic injection manufacturer in China, specializing in producing a wide range of plastic products such as automotive parts, electronic components, and medical devices. With state-of-the-art equipment and a team of skilled technicians, Sinotech offers high-quality products at competitive prices.
2. Mold-Tech Mold-Tech is a renowned plastic injection manufacturer in China, known for its expertise in producing precision molds for various industries. Their products range from household goods to industrial parts, all meeting strict quality standards and specifications.
3. Hengtong Hengtong is a reliable plastic injection manufacturer in China, offering a comprehensive range of plastic products for different applications. Their focus on innovation and technology ensures that their products are cutting-edge and of the highest quality.
4. Dongguan Sincere Tech Dongguan Sincere Tech is a well-established plastic injection manufacturer in China, specializing in producing custom plastic parts for industries such as automotive, electronics, and medical. Their dedication to quality and customer satisfaction has earned them a stellar reputation in the industry.
5. Shenzhen RJC Shenzhen RJC is a leading plastic injection manufacturer in China, offering a variety of plastic products including household items, electronic components, and industrial parts. Their state-of-the-art facilities and experienced team ensure the highest quality products meeting customer requirements.
6. Xiamen LFT Xiamen LFT is a reputable plastic injection manufacturer in China, specializing in producing high-quality plastic products for industries such as automotive, aerospace, and consumer electronics. Their commitment to excellence and customer satisfaction sets them apart in the industry.
7. NICE Rapid NICE Rapid is a prominent plastic injection manufacturer in China, known for its efficient production processes and high-quality products. They offer a wide range of plastic parts for industries such as automotive, electronics, and medical.
8. TK Mold TK Mold is a well-known plastic injection manufacturer in China, specializing in producing precision molds and plastic parts for various industries. Their advanced technology and skilled workforce ensure optimum product quality and customer satisfaction.
9. PFMOLD PFMOLD is a trusted plastic injection manufacturer in China, focusing on producing custom plastic parts for industries such as automotive, electronics, and medical. With a strong emphasis on quality control and efficiency, they deliver excellent products to their clients.
10. ACO Mold ACO Mold is a leading plastic injection manufacturer in China, offering a comprehensive range of plastic products for industries such as automotive, electronics, and consumer goods. Their commitment to innovation and quality ensures top-notch products for their customers.
| Manufacturer | Specialization |
|——————-|—————————————–|
| Sinotech | Automotive parts, electronic components, medical devices |
| Mold-Tech | Precision molds for various industries |
| Hengtong | Comprehensive range of plastic products |
| Dongguan Sincere Tech | Custom plastic parts for industries |
| Shenzhen RJC | Household items, electronic components, industrial parts |
| Xiamen LFT | High-quality plastic products for various industries |
| NICE Rapid | Plastic parts for automotive, electronics, and medical |
| TK Mold | Precision molds and plastic parts for industries |
| PFMOLD | Custom plastic parts for automotive, electronics, and medical |
| ACO Mold | Plastic products for automotive, electronics, consumer goods |
Background Research for plastic injection manufacturers Companies in China, use qcc.com archive.org importyeti.com
China is widely recognized as one of the leading hubs for plastic injection manufacturers, known for its extensive production capabilities, cost-effectiveness, and technological expertise. To conduct background research on Chinese plastic injection manufacturers, a few online platforms such as qcc.com, archive.org, and importyeti.com can be utilized.
qcc.com is a comprehensive online business information platform in China. It provides company profiles, business registration details, financial data, and more. Researchers can leverage this platform to gather information on various plastic injection manufacturers in China, including their legal status, address, registration dates, and key personnel.
archive.org is a digital library that preserves web pages from the past. Researchers can access this platform to view old website snapshots of different Chinese plastic injection manufacturers. By analyzing these snapshots, one can uncover information such as company history, portfolio, past certifications, and significant milestones achieved in the industry.
importyeti.com is a platform that focuses on import and export data. It provides access to shipment records to track the trading activities of plastic injection manufacturers in China. Users can gain insights into the companies’ international business connections, the types and quantities of products being imported or exported, and the countries with which they engage in trade.
By utilizing these platforms, researchers can gain a comprehensive understanding of various aspects related to Chinese plastic injection manufacturers. They can gather information on a company’s background, history, financial status, products, certifications, and international trade activities. This knowledge can be valuable in assessing the credibility, reliability, and suitability of potential suppliers or manufacturing partners.
Leveraging Trade Shows and Expos for plastic injection Sourcing in China
Trade shows and expos are excellent opportunities to source plastic injection manufacturing services in China. These events bring together suppliers, manufacturers, and professionals in the industry, making it easy to connect with potential partners and suppliers.
When attending trade shows and expos in China, it is important to come prepared with a clear understanding of your sourcing needs and requirements. This will enable you to effectively communicate with potential suppliers and assess whether they are a good fit for your project.
Networking at trade shows and expos is also crucial for finding reliable and trustworthy suppliers. By connecting with other industry professionals and getting recommendations, you can narrow down your options and find reputable suppliers that meet your criteria.
Additionally, trade shows and expos provide opportunities to see samples of work, discuss pricing and production capabilities, and negotiate terms and conditions face-to-face. This can help build trust and establish a strong working relationship with potential suppliers.
In conclusion, leveraging trade shows and expos for plastic injection sourcing in China can be highly beneficial for finding quality suppliers, establishing connections, and ultimately, achieving successful partnerships. By being well-prepared, networking effectively, and utilizing the resources available at these events, you can streamline the sourcing process and find the right partner for your plastic injection manufacturing needs.
The Role of Agents and Sourcing Companies in Facilitating plastic injection Purchases from China
Agents and sourcing companies play a crucial role in facilitating plastic injection purchases from China. These entities act as intermediaries between the buyer and the Chinese manufacturers, helping to streamline the procurement process and mitigate potential risks.
Firstly, agents and sourcing companies possess extensive knowledge and experience in the Chinese market. They are familiar with the local business practices, trade regulations, and plastic injection manufacturing industry. This expertise allows them to provide valuable guidance to the buyer in terms of supplier selection, product specifications, and quality control standards.
Secondly, agents and sourcing companies have established networks of reliable and trustworthy manufacturers in China. They have extensive contacts and partnerships with a wide range of suppliers who specialize in plastic injection molding. This network enables them to quickly identify suitable suppliers that can meet the buyer’s specific needs and requirements.
Furthermore, agents and sourcing companies handle the entire sourcing process, from supplier qualification to production monitoring. They take care of supplier audits, factory visits, and due diligence checks to ensure that the manufacturer meets the buyer’s quality and compliance standards. This comprehensive service helps to minimize the risk of dealing with unscrupulous or low-quality suppliers.
In addition, agents and sourcing companies also handle logistics and shipping arrangements. They manage the transportation and customs clearance processes, ensuring that the products are delivered to the buyer’s location in a timely and cost-effective manner. This saves the buyer from the complexities of international trade logistics and allows them to focus on their core business activities.
Ultimately, the role of agents and sourcing companies in facilitating plastic injection purchases from China is to simplify the buying process, reduce risks, and ensure the buyer receives high-quality products at competitive prices. By leveraging their expertise, networks, and comprehensive services, these intermediaries play a vital role in connecting international buyers with reliable Chinese manufacturers.
Price Cost Research for plastic injection manufacturers Companies in China, use temu.com and 1688.com
When it comes to searching for plastic injection manufacturers in China, two popular platforms are Temu.com and 1688.com. These platforms provide extensive listings and information about manufacturers in China, allowing buyers to compare prices and choose the most suitable suppliers for their needs.
Temu.com is an online sourcing platform that connects global buyers with Chinese manufacturers. It offers a wide range of products, including plastic injection manufacturers. By using Temu.com, buyers can access detailed information about suppliers, such as company profiles, production capabilities, and certifications. The platform also allows buyers to directly contact manufacturers and negotiate prices.
1688.com, also known as Alibaba.cn, is one of China’s largest online wholesale marketplaces. It offers a vast range of plastic injection manufacturers and provides tools to search for suppliers based on product specifications, certifications, and location. Buyers can browse through supplier storefronts, which include product images, descriptions, and prices. The platform also provides a messaging system for buyers to communicate directly with manufacturers.
When conducting price-cost research on these platforms, buyers should consider several factors to ensure they get the best value for their money. Firstly, buyers need to compare prices from multiple suppliers to have a clear understanding of the market range for plastic injection manufacturing. This will help them identify any significant deviations in prices and negotiate accordingly.
Furthermore, buyers should assess the quality of the products offered by potential manufacturers, as choosing an unreliable supplier solely based on low prices might result in subpar products or delayed deliveries. It is also vital to consider the specific requirements and production capabilities of the manufacturers to ensure they can meet the desired specifications in terms of materials, design complexity, and production volume.
In conclusion, Temu.com and 1688.com are valuable platforms to research price costs for plastic injection manufacturers in China. By utilizing these platforms, buyers can access a wide range of suppliers, compare prices, and evaluate the quality and capabilities of potential manufacturers. Taking these factors into account will enable buyers to find the most suitable supplier that meets their needs while ensuring competitive pricing and high-quality products.
Shipping Cost for plastic injection import from China
The shipping cost for importing plastic injection products from China depends on various factors such as the volume and weight of the products, the shipping method chosen, and the destination country.
Generally, there are two common shipping methods for importing goods from China: air freight and sea freight.
Air freight is faster but more expensive compared to sea freight. The cost is usually calculated based on the weight or volumetric weight of the goods. Volumetric weight is calculated by multiplying the length, height, and width of the package and dividing it by a volumetric factor set by the airline. The higher value, either actual weight or volumetric weight, is used to calculate the shipping cost.
On the other hand, sea freight is more cost-effective for large shipments but slower. The cost is determined by the shipment’s volume or weight, the type of container used, and the shipping route. Full container load (FCL) and less-than-container load (LCL) options are available. FCL is recommended for large quantities to reduce shipping costs, while LCL is suitable for smaller quantities.
Apart from the shipping method, other charges may apply, including customs duties, taxes, import documentation fees, and handling charges. These charges are based on the import regulations and policies of the destination country.
To get an accurate shipping cost estimate, it is advisable to contact a freight forwarder or shipping agent who can provide detailed information based on the specific requirements and circumstances of the shipment. Comparing multiple quotes from different shipping providers can help find the most cost-effective option.
In conclusion, the shipping cost for plastic injection imports from China varies depending on several factors, including the shipping method chosen, shipment volume or weight, and destination country. Consulting with shipping experts and obtaining multiple quotes is essential to ensure the most suitable and cost-effective shipping solution.
Compare China and Other plastic injection Markets: Products Quality and Price,Visible and Hidden Costs
China is a competitive player in the global plastic injection market, known for providing high-quality products at a lower price compared to other markets. The availability of cheap labor and a well-established supply chain in China allows for cost-effective production of plastic injection products.
In terms of product quality, China has made significant advancements in technology and processes, ensuring that products meet international standards. However, there may still be concerns about the consistency and reliability of product quality due to varying standards and practices across manufacturers in China.
When it comes to pricing, China offers competitive rates due to lower labor costs and economies of scale. This makes it an attractive choice for companies looking to produce plastic injection products at a lower cost. However, there may be hidden costs such as shipping and import duties when sourcing products from China, which need to be taken into consideration.
Other plastic injection markets like the United States or Europe also provide high-quality products, but at a higher price point compared to China. While the products may come with a higher price tag, there is often more assurance of quality standards and consistency in these markets.
Overall, China is a strong contender in the plastic injection market with its combination of competitive pricing and improving product quality. Companies need to weigh the visible and hidden costs when choosing a market for their plastic injection needs, considering factors such as quality, price, and reliability in product sourcing.
Understanding Pricing and Payment Terms for plastic injection: A Comparative Guide to Get the Best Deal
When it comes to plastic injection, understanding pricing and payment terms is crucial to getting the best deal for your project. There are several factors to consider when negotiating pricing, including the complexity of the part, the material being used, and the quantity being produced.
One of the most common pricing models for plastic injection is cost-plus pricing, where the manufacturer adds a markup to the cost of production. This markup typically includes a profit margin for the manufacturer, as well as any additional costs such as tooling and overhead.
Another common pricing model is fixed pricing, where the manufacturer provides a set price for each part based on the specifications provided. This can be advantageous for buyers who want a clear understanding of the total cost upfront.
When it comes to payment terms, many manufacturers require a deposit upfront to cover the cost of tooling and materials. The remaining balance is typically due upon completion of the project or in installments as the project progresses.
It’s important to carefully review and negotiate pricing and payment terms to ensure you are getting the best deal possible. Be sure to compare quotes from multiple manufacturers, ask about any additional fees or charges, and clarify any uncertainties before moving forward with a supplier. By taking the time to understand pricing and payment terms, you can secure a favorable agreement and ensure the success of your plastic injection project.
Chinese Regulations and Industry Standards Certifications for plastic injection,Import Regulations and Customs for plastic injection from China
In China, plastic injection products are subject to various regulations and standards to ensure quality and safety. The industry standards certifications for plastic injection products include the GB/T 3840-2008 standard for plastic injection molded products, which specifies the technical requirements for materials, dimensions, and performance.
Import regulations for plastic injection products from China include compliance with local laws and regulations, such as obtaining import licenses and permits from the relevant authorities. Customs regulations require proper documentation, labeling, and packaging of the products for clearance at the port of entry.
Importers of plastic injection products from China should also be aware of potential trade barriers, such as anti-dumping duties or quotas, which could affect the cost and availability of imported goods. It is important to work with experienced import agents or customs brokers to navigate the complex regulations and ensure compliance with all requirements.
Overall, understanding and adhering to Chinese regulations and industry standards certifications are crucial for importing plastic injection products from China successfully. By following the necessary procedures and working with knowledgeable partners, importers can ensure smooth and efficient importation of these products.
Sustainability and Environmental Considerations in plastic injection Manufacturing
Sustainability and environmental considerations play a vital role in the plastic injection manufacturing process. Plastic injection manufacturing involves the production of plastic components through the injection of molten plastic material into a mold. Here are some key points to consider regarding sustainability and environmental impact in this manufacturing process.
1. Material selection: It is crucial to assess the environmental impact of the plastic material used in the injection process. Opting for biodegradable or recyclable materials can significantly reduce the ecological footprint associated with plastic waste. Alternatives like bioplastics or recycled plastics enable the manufacturing of sustainable products.
2. Energy efficiency: Implementing energy-efficient practices in plastic injection manufacturing can help minimize greenhouse gas emissions. Efficient machinery and optimized production processes can reduce energy consumption and associated carbon emissions. Incorporating technologies such as variable frequency drives and energy recovery systems can enhance energy efficiency.
3. Waste management: Proper management of plastic waste generated during the manufacturing process is vital. Implementing recycling programs, internal waste reduction initiatives, and promoting responsible waste disposal practices can minimize the environmental impact of plastic injection manufacturing. By reusing or recycling plastic waste, the industry can significantly contribute to sustainability efforts.
4. Water conservation: Water is used throughout the plastic injection manufacturing process, mainly for cooling purposes. To minimize water consumption, recycling cooling water, using closed-loop systems, and implementing water-saving measures are essential. Water treatment and recycling facilities can help conserve this precious resource.
5. Emissions control: Controlling and managing emissions, such as volatile organic compounds (VOCs) or particulate matter, is crucial for sustainability. Investing in emission control technologies, proper ventilation systems, and monitoring air quality can reduce the impact on both the environment and human health.
6. Life cycle assessment: Conducting a life cycle assessment (LCA) can help evaluate the environmental impact of the entire manufacturing process, from raw material extraction to end-of-life disposal. LCA provides insights into areas that require improvement and allows organizations to make informed decisions for a more sustainable process.
In conclusion, considering sustainability and environmental aspects in plastic injection manufacturing is essential for responsible industry practices. Through thoughtful material selection, energy efficiency, waste management, water conservation, emissions control, and life cycle assessment, the industry can reduce its ecological footprint and contribute to a more sustainable future.
List The Evolution history of “plastic injection”
Plastic injection molding, a manufacturing process that involves injecting molten plastic into a mold to create various products, has a rich evolution history. The development of modern plastic injection molding can be traced back to the 19th century.
In the mid-1800s, the production of celluloid, a type of plastic made from cellulose nitrate, gained recognition. This new material was initially used for making billiard balls, but as technology advanced, it was also used in other industries. However, celluloid had its limitations, such as being highly flammable, which led to the search for safer alternatives.
In the early 20th century, the focus shifted to developing more reliable types of plastic for injection molding. In 1907, Leo Hendrik Baekeland invented Bakelite, the first synthetic plastic. Bakelite was widely used for various applications, including electrical insulation, automotive parts, and consumer goods.
After World War II, the usage of plastic injection molding skyrocketed. This was primarily due to the discovery of new materials, such as polyethylene and polypropylene. These materials offered improved properties, making them ideal for injection molding. The process itself also saw significant advancements during this period, with the introduction of automated injection molding machines.
During the later part of the 20th century, continuous innovations focused on enhancing the precision and efficiency of plastic injection molding. This led to the development of computer-aided design (CAD) and computer-aided manufacturing (CAM) technologies. CAD allowed for the creation of complex 3D designs, while CAM enabled the translation of these designs into machine instructions.
In recent years, the evolution of plastic injection molding has been driven by sustainability and energy efficiency. The industry has embraced biodegradable, recycled, and plant-based plastics. Additionally, efforts are underway to reduce waste and implement more eco-friendly production processes.
The future of plastic injection molding looks promising, with ongoing research and development in areas like multi-material injection molding, micro-injection molding, and additive manufacturing techniques like 3D printing. These advancements aim to push the boundaries of design possibilities and reduce environmental impact.
In conclusion, plastic injection molding has come a long way since its inception in the 19th century. From celluloid to Bakelite, and now advanced polymers and sustainable materials, the process continues to evolve, driven by technological innovations and environmental considerations.
The Evolution and Market Trends in plastic injection Industry
The plastic injection industry has seen significant evolution and market trends in recent years. The use of advanced technologies such as computer-aided design (CAD) and computer-aided manufacturing (CAM) has revolutionized the way plastic products are designed and produced. These technologies have enabled manufacturers to create complex and intricate designs with high precision and consistency.
Another key trend in the plastic injection industry is the growing focus on sustainability and environmental responsibility. As consumers become more aware of the impact of plastic waste on the environment, there is a growing demand for eco-friendly and biodegradable plastics. Many manufacturers are now investing in research and development to create innovative solutions that reduce the environmental footprint of plastic products.
In terms of market trends, the plastic injection industry is experiencing steady growth, driven by increasing demand from various sectors such as automotive, packaging, electronics, and consumer goods. The rise of e-commerce and online shopping has also boosted the demand for plastic packaging materials. Additionally, the trend towards lightweight and durable materials in industries such as automotive and aerospace is driving the adoption of plastic components.
Overall, the plastic injection industry is poised for continued growth and innovation as manufacturers leverage advanced technologies and materials to meet the evolving demands of consumers and the market. The focus on sustainability and environmental responsibility will likely continue to drive innovation in the industry, leading to the development of more eco-friendly and efficient plastic products.
Custom Private Labeling and Branding Opportunities with Chinese plastic injection Manufacturers
Chinese plastic injection manufacturers offer custom private labeling and branding opportunities for businesses looking to create their own unique products. With years of experience and advanced technology, these manufacturers can produce high-quality plastic products that can be customized with your own branding and logos.
By partnering with a Chinese plastic injection manufacturer, you can take advantage of their expertise in creating custom molds and producing large quantities of products at competitive prices. Whether you are looking to create a new product line or add your branding to an existing product, these manufacturers can help bring your vision to life.
Additionally, Chinese manufacturers are known for their reliability and efficiency in production, ensuring that your orders are completed on time and to your specifications. They also offer flexible options for customization, allowing you to choose the colors, materials, and finishes that best represent your brand.
With their extensive capabilities and cost-effective solutions, Chinese plastic injection manufacturers provide a convenient and reliable option for businesses looking to create custom branded products. Contact a manufacturer today to explore the possibilities for your private labeling and branding needs.
Tips for Procurement and Considerations when Purchasing plastic injection
When purchasing plastic injection, there are several considerations and tips to keep in mind to ensure you are getting a high quality product that meets your specific requirements:
1. Define your requirements: Before making a purchase, clearly define the specifications and requirements for the plastic injection parts you need. This includes material type, size, shape, tolerances, and any other specific features needed for your application.
2. Research suppliers: Look for reputable suppliers with a track record of producing high quality plastic injection parts. Read reviews, ask for references, and check certifications to ensure you are working with a reliable supplier.
3. Consider quality and price: While price is important, it should not be the only factor in your decision. Consider the quality of the plastic injection parts, including the material used, manufacturing process, and accuracy of the parts. It is worth paying a little more for higher quality parts that will last longer and perform better.
4. Check production capabilities: Make sure the supplier has the capabilities to produce the quantity of parts you need within your required timeframe. Consider factors such as production capacity, lead times, and any additional services offered, such as design assistance or prototyping.
5. Communication and collaboration: Establish clear communication with the supplier before and during the production process. Provide detailed specifications, ask questions, and request regular updates on the progress of your order to ensure your requirements are being met.
6. Quality control: Ask about the supplier’s quality control processes and inquire about any certifications or standards they adhere to. Request samples or prototypes to ensure the parts meet your specifications before placing a larger order.
7. Consider sustainability: If sustainability is important to your organization, inquire about the supplier’s environmental practices and efforts to reduce waste and energy consumption in the manufacturing process.
By following these tips and considerations when purchasing plastic injection parts, you can ensure you are getting high quality, reliable parts that meet your specific requirements and deliver excellent performance.
FAQs on Sourcing and Manufacturing plastic injection in China
1. How do I find a reliable plastic injection manufacturer in China?
It is recommended to research and shortlist potential manufacturers based on their reputation, experience, and customer reviews. Attend trade shows, request quotes, and visit their facilities if possible to ensure they meet your requirements.
2. What factors should I consider when selecting a plastic injection manufacturer in China?
Some important factors to consider include the manufacturer’s expertise, capabilities, quality control measures, production capacity, pricing, lead times, and communication skills. It is also essential to ensure they have experience working with your specific industry and product requirements.
3. How can I ensure the quality of plastic injection products manufactured in China?
To ensure product quality, it is crucial to conduct thorough inspections and quality control checks throughout the manufacturing process. Develop detailed product specifications, establish clear communication channels, and work closely with the manufacturer to address any issues promptly.
4. What are the advantages of sourcing plastic injection manufacturing in China?
China is known for its cost-effective manufacturing solutions, advanced technology, diverse supplier network, and skilled workforce. By sourcing plastic injection manufacturing in China, you can benefit from competitive pricing, high-quality products, and efficient production processes.
5. How can I protect my intellectual property when sourcing plastic injection manufacturing in China?
To protect your intellectual property, it is recommended to sign confidentiality agreements, conduct background checks on potential manufacturers, and register your patents and trademarks in China. Working with reputable manufacturers and maintaining open communication can also help safeguard your intellectual property rights.
Why contact sourcifychina.com get free quota from reliable plastic injection suppliers?
Sourcifychina.com offers a convenient platform for businesses seeking reliable plastic injection suppliers in China. By contacting Sourcify China, businesses can benefit from obtaining a free quota from these trusted suppliers. This allows companies to access competitive pricing and reliable manufacturing services without the hassle of searching for suppliers on their own.
Sourcify China has established partnerships with a network of reputable plastic injection suppliers in China, ensuring that businesses receive high-quality products and services. By requesting a free quota through Sourcify China, companies can easily compare quotes from multiple suppliers and choose the one that best fits their requirements.
Moreover, contacting Sourcify China for a free quota can save businesses time and effort in sourcing and vetting potential suppliers. With Sourcify China’s pre-vetted network of suppliers, companies can trust that they are connecting with reliable and experienced manufacturers.
Overall, obtaining a free quota from reliable plastic injection suppliers through Sourcify China is a cost-effective and efficient way for businesses to streamline their sourcing process and secure high-quality manufacturing services in China.