Analysis of Manufacturing Expenses for power cable cost
Manufacturing expenses for power cables can be broken down into several components which include the cost of raw materials, labor, and overhead costs. The cost of raw materials includes the cost of copper or aluminum used as the conductor, insulation material, shielding material, and other necessary components.
The cost of labor involves the salaries and wages paid to the workers involved in the manufacturing process. This includes process engineers, machine operators, quality control personnel, and other staff. The cost of labor could also include employee benefits, such as health insurance, paid leave, and retirement benefits.
The overhead costs include the expenses required to maintain the production facility and other indirect expenses. Overhead expenses consist of rent, utilities, insurance, equipment maintenance and repair, and administrative expenses, as well as any other expenses that are not directly attributable to a particular product.
In summary, manufacturing expenses for power cables depend on the cost of raw materials, labor costs, and overhead expenses. To lower the manufacturing expenses, manufacturers can consider using alternative materials for insulation and shielding or explore ways to automate production, which could reduce labor costs. Manufacturers must also strive to optimize their operations to reduce wastage, as well as minimize the costs of overhead expenses while ensuring product quality is not compromised.
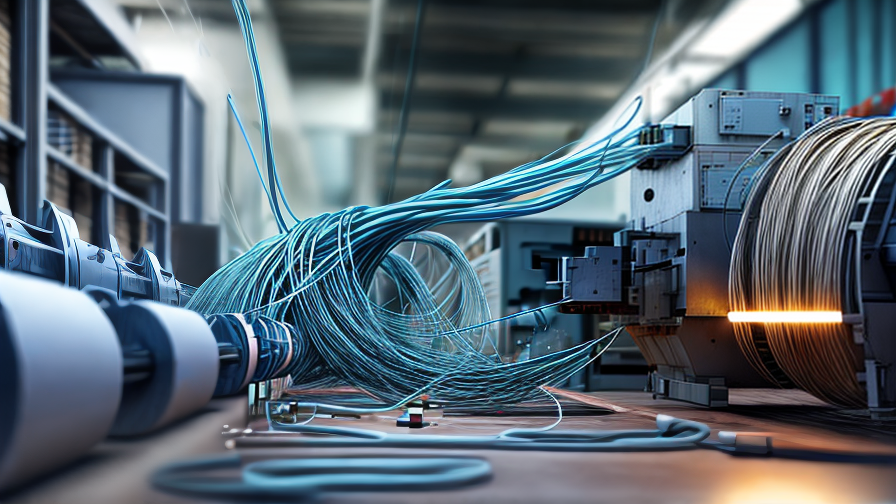
Understanding the Components that Contribute to the Price of power cable cost
The components that contribute to the price of power cable cost include both the material costs and the manufacturing costs. In terms of material costs, the type and quality of the materials used play a significant role. For example, copper is commonly used as a conductor in power cables, but the price of copper fluctuates based on global supply and demand.
The insulation and jacket materials also impact the price. Insulation materials can range from PVC to XLPE (cross-linked polyethylene), and the latter is generally more expensive due to its high heat resistance and durability. The jacket material, which provides protection for the cable, can also vary based on the application and environment. For example, cables used in harsh outdoor environments might use a heavy-duty polyethylene jacket that is more expensive than a standard PVC jacket.
In addition to material costs, the manufacturing process can also contribute to the price. The complexity of the cable design, the length of the cable, and the number of cables being produced all impact the manufacturing cost. Specialized manufacturing processes, such as adding armored layers for increased protection against damage, can also increase the overall cost.
Finally, the market demand and competition play a role in determining the price. When there is a high demand for power cables, prices tend to rise. Conversely, when there is low demand, prices may decrease. The number of manufacturers and suppliers of power cables can also impact pricing, as increased competition can lead to more competitive pricing.
Overall, the price of power cables is influenced by a variety of factors, including material costs, manufacturing process, market demand, and competition.
Comparing the Wholesale and Retail Prices of power cable cost in China
The power cable cost in China varies between wholesale and retail prices. Wholesale prices are the prices that are offered to businesses or individuals who purchase large quantities of power cables. Retail prices, on the other hand, are the prices that are charged to consumers who purchase power cables in small quantities.
The wholesale prices of power cables in China are usually lower than the retail prices. This is because wholesalers can purchase power cables in bulk directly from the manufacturers at a lower cost. By doing so, they are able to save on the cost of transportation and other overhead costs. In addition, wholesalers can negotiate for lower prices since they are purchasing in large quantities.
Retail prices, on the other hand, are higher than wholesale prices because of the added costs that come with selling small quantities. These costs include transportation, marketing, packaging, and handling costs. Retailers may also have to pay higher prices to wholesalers if they are purchasing smaller quantities.
Overall, the price difference between wholesale and retail prices for power cables in China can be significant. It is important to note that the price of power cables can also vary depending on factors such as the quality of the cable, the brand, and the materials used in manufacturing. Buyers should do their research and compare prices from different wholesalers and retailers before making a purchase to ensure they are getting the best deal.

Understanding Shipping and Logistics for power cable cost from China
Shipping and logistics are critical factors to consider when calculating the cost of importing power cables from China. There are several modes of transportation available, including air, ocean, and rail. Each mode has its advantages and disadvantages and consequent impacts on pricing.
When comparing the costs of shipping power cables, it’s essential to consider several factors that can influence the final pricing, such as origin and destination ports, weight, size, type of product, and volume. For example, shipping heavy and bulky power cables by air is generally more expensive than by sea freight. However, air freight is faster and more reliable, making it an excellent option for urgent shipments.
Sea freight is the most commonly used method for shipping power cables from China, as it is more cost-effective for large volumes. However, it’s also important to note that sea freight takes longer to arrive at the destination, and it is subject to congestions, port delays and weather conditions, which can extend the lead time and increase the cost of shipping.
Additionally, the cost of logistics and handling also plays a significant role in determining the total cost of importing power cables from China. Examples of these costs include customs clearance, warehousing, insurance, and packaging.
To ensure the lowest possible shipping costs, you will need to work closely with your logistics provider and freight forwarder to find the most efficient and cost-effective method to transport your power cables. Taking care of all the details and working with trustworthy partners will help ensure that your power cables arrive on time and in good condition while minimizing transportation costs for your business.
Potential Tariffs or Import Taxes on power cable cost Purchased from China
The United States government has proposed several tariff increases and import taxes on power cable cost purchased from China. The tariffs range between 10% to 25%, depending on the type of power cable, location of origin, and other factors. The motivation behind these tariffs is to encourage more domestic manufacturing and reduce the nation’s reliance on foreign goods.
These tariffs are expected to increase the cost of power cables for American buyers, which could result in higher prices for consumers and businesses. Additionally, the tariffs could negatively impact Chinese businesses that export power cables to the United States, potentially leading to job losses and slower economic growth in China.
Many American manufacturers of power cables have opposed the proposed tariffs, arguing that they will negatively impact their businesses as well. They argue that these tariffs will not only increase the cost of imported power cables but also increase costs for domestic manufacturers that rely on raw materials imported from China.
Overall, the proposed tariffs on power cables will have significant economic implications for both China and the United States. While the tariffs may encourage more domestic manufacturing of power cables in the United States, they also have the potential to increase the costs of power cables and harm the competitiveness of American companies in the global market.

Impact of Market Demand and Competitive Environment on power cable cost
Market demand and competitive environment have a significant impact on power cable cost. The demand for power cables depends on the growth in the energy sector, including the generation and consumption of electricity. Changes in market demand are likely to affect the price of copper, aluminum, and other raw materials used in the manufacture of power cables. When demand is high, the price of raw materials tends to increase, leading to higher power cable costs.
Another factor that affects power cable cost is the competitive environment. The power cable market is highly competitive, with many players offering similar products. Manufacturers compete based on price, quality, and service. In a competitive environment, companies strive to keep their prices low to attract buyers. Therefore, a decrease in the cost of manufacturing power cables directly affects the price.
The cost of power cables must be analyzed from various perspectives to understand the dynamics of the market. Companies that manufacture power cables should consider the cost of raw materials, labor, and machinery, among other factors, when pricing their products. Further, forecasting the demand for power cables is necessary to prevent overproduction or underproduction.
In conclusion, the market demand and competitive environment significantly impact power cable cost. The cost of manufacturing, including raw materials, labor, and machinery, is passed down to the buyer, ultimately determining the price. Manufacturers must understand the market dynamics to set appropriate prices, as overpricing or underpricing can significantly affect profitability.
FAQ about power cable cost with multiple answers
Q: How much does a power cable cost?
A: The cost of a power cable varies depending on the length, thickness, and material used. On average, a basic power cable can cost between $5 to $20.
Q: Can the cost of a power cable differ based on its usage?
A: Yes, it can. For example, power cables with higher voltage ratings are made with heavy-duty materials, such as copper, which makes them more expensive than cables for lower voltages.
Q: Are power cables from well-known brands more expensive?
A: Yes, cables from well-known brands can be more expensive due to their reputation, quality of materials used, and after-sales service. However, there are budget-friendly options that perform just as well.
Q: Does the location affect the cost of power cables?
A: The location can impact the cost of power cables due to shipping and transportation costs. For instance, cables that need to be imported may cost more than those that are locally produced or readily available.
Q: Is it cost-effective to buy cheaper power cables?
A: It depends on where and how you’re using the power cable. Cheaper power cables may be prone to breaking and require frequent replacements. Thus, it is advisable to invest in a quality cable for long-term use, especially when it comes to electronics and household appliances.
Q: Can I negotiate the price of a power cable?
A: Some retailers may allow for negotiations, especially if you’re buying in bulk. It’s always worth asking if there’s any room for negotiation. Nonetheless, it’s necessary to do research on reputable brands and the ideal price range to avoid getting scammed.
In conclusion, the cost of a power cable is dependent on several factors. When shopping for a power cable, it’s essential to consider the length, thickness, material used, location, and most importantly, your usage. It is recommended to invest in quality power cables to avoid frequent repairs and replacements.