Introduce about precision machining part guide,Qulity,Cost,Supplier,Certification,Market,Tips,FAQ
Precision machining is a process that involves the creation of intricate and highly precise parts for various industries such as automotive, aerospace, medical, and electronics. This machining guide provides essential information on the quality, cost, suppliers, certifications, market trends, useful tips, and frequently asked questions related to precision machining parts.
Quality is paramount in precision machining parts, as they often require tight tolerances, accurate dimensions, and smooth finishes. To ensure quality, it is crucial to work with experienced machinists who possess the necessary skills and expertise. Additionally, advanced machining equipment and inspection methods, such as coordinate measuring machines (CMM), are employed to guarantee precision and adherence to specifications.
The cost of precision machining parts can vary depending on several factors, including the complexity of the part, material choice, tolerances, and volume required. Generally, machining complex parts or using exotic materials may increase costs. However, it is important to strike a balance between quality and cost to ensure that the final product meets the required standards without breaking the budget.
Finding reliable suppliers for precision machining parts is essential. It is recommended to choose suppliers with a proven track record, extensive industry experience, and state-of-the-art facilities. Conducting thorough research, reading customer reviews, and requesting samples can help in selecting the right supplier who can meet your specific requirements.
Certifications play a significant role in ensuring the quality and reliability of precision machining parts. Certifications such as ISO 9001:2015 demonstrate that a supplier has implemented quality management systems and adheres to international standards. Additionally, certifications specific to industries, such as AS9100 for aerospace, indicate compliance with industry-specific requirements.
The market for precision machining parts is constantly evolving due to advancements in technology, increasing demand for customized components, and emerging industries. It is essential to stay updated with the latest market trends to maintain a competitive edge and align with the evolving needs of customers.
Here are a few tips to optimize precision machining processes: communicate clearly with the supplier to ensure shared understanding of specifications, provide comprehensive technical drawings, prioritize precision over speed, establish a good working relationship with suppliers, and perform regular quality inspections.
Frequently Asked Questions (FAQ) about precision machining parts cover various topics such as turnaround time, minimum order quantities, material availability, surface finishes, secondary operations, and pricing options. These FAQs address common concerns and help customers make informed decisions when procuring precision machining parts.
Overall, precision machining part guide covers the essential aspects of quality, cost, supplier selection, certifications, market trends, useful tips, and FAQs to facilitate the procurement process and ensure successful outcomes in precision machining applications.
Types of precision machining part
Precision machining parts are crucial components used in a variety of industries, ranging from aerospace and automotive to electronics and medical. They are precisely produced using advanced machining techniques to meet strict tolerances and ensure high-quality end products. Here are some common types of precision machining parts:
1. CNC Machined Parts: Computer Numerical Control (CNC) machining is a widely used technique that utilizes computer-controlled machines to shape and cut materials with precision. CNC machined parts can be crafted from a variety of materials, including metals like aluminum, steel, and brass, as well as plastics.
2. Turned Parts: Turning is a machining process that involves the rotation of a workpiece while a cutting tool removes unwanted material. This technique is commonly used to create symmetrical cylindrical or conical shapes, such as shafts, spindles, and bushings.
3. Milled Parts: Milling is another essential machining process used to remove material from a workpiece. It involves rotating a cutting tool while moving it along multiple axes. Milling machines are capable of producing intricate shapes, holes, and slots on precision parts.
4. Swiss Turned Parts: Swiss turning, also known as Swiss machining or Swiss screw machining, is a specialized form of turning. This technique is primarily used to create small, precise parts with a high level of accuracy and tight tolerances. It is commonly employed in the production of watch components, medical devices, and electronic connectors.
5. Grinding Parts: Grinding is a versatile machining process that uses abrasive wheels to remove material and achieve tight tolerances. It is often employed for producing precision parts with a smooth surface finish, such as gears, bearings, and tools.
6. Laser Machined Parts: Laser machining involves the use of a focused laser beam to cut, engrave, or etch materials. This technique is highly precise, making it suitable for creating intricate designs on precision parts, as well as for drilling small holes and removing unwanted material.
7. Wire EDM Parts: Wire Electrical Discharge Machining (EDM) is a process that uses an electrically charged wire to cut through conductive materials. Wire EDM is capable of producing precise and intricate shapes, making it useful for manufacturing parts that require tight tolerances, such as dies, molds, and tooling components.
In conclusion, precision machining parts encompass a diverse range of components that require advanced techniques and machinery to achieve high levels of accuracy and quality. These parts play a vital role in various industries by ensuring the functionality, reliability, and performance of end products.
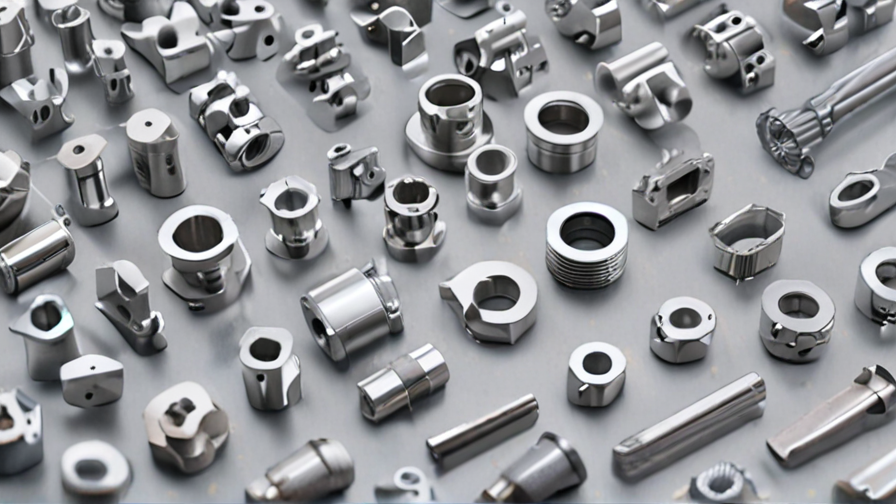
Pros and Cons of Using precision machining part
Precision machining parts have become an essential component in various industries due to their accuracy and ability to meet tight tolerances. However, as with any manufacturing process, there are pros and cons associated with using precision machining parts.
Pros:
1. Accuracy and Precision: Precision machining parts are manufactured using advanced technology and equipment, ensuring high levels of accuracy and precision. This allows for the production of intricate and complex parts that are crucial in industries such as aerospace and automotive.
2. Enhanced Efficiency: Precision machining parts are known for their ability to produce large quantities of identical parts with minimal variation. This leads to increased efficiency in the manufacturing process, reducing costs and time required for production.
3. Wide Range of Materials: Precision machining can be applied to a wide range of materials, including metals, plastics, and composites. This versatility enables manufacturers to produce parts for various applications across different industries.
4. Customization: Precision machining parts can be customized according to specific requirements. This allows for the production of unique and tailored components, which may be difficult to produce using other manufacturing methods.
Cons:
1. High Costs: Precision machining parts require specialized equipment and skilled operators, leading to higher production costs compared to other manufacturing methods. The cost of raw materials, maintenance, and the expertise required can make precision machining parts more expensive.
2. Longer Lead Time: The production of precision machining parts often involves several steps, including designing, programming, and testing. This elongated process can result in longer lead times compared to other manufacturing methods.
3. Design Complexity: While precision machining can produce intricate parts, it may face limitations in handling extremely complex designs. Some shapes or geometries may require additional processes or may not be cost-effective to produce using precision machining.
4. Limited Scalability: Scaling up the production of precision machining parts can be challenging. Expanding the operation may require additional machines, skilled labor, and increased costs, which can make scalability difficult.
In conclusion, precision machining parts offer numerous advantages, including accuracy, efficiency, material versatility, and customization. However, the drawbacks of precision machining include higher costs, longer lead times, design complexity limitations, and limited scalability. Before opting for precision machining, it is essential to evaluate these pros and cons to determine if it is the most suitable manufacturing process for a specific application.
precision machining part Reference Specifications (varies for different product)
Precision machining refers to the process of producing parts with tight tolerances and high surface finish, using cutting-edge manufacturing techniques. It involves the use of advanced machinery and tools to remove material from a workpiece, shaping it into the desired form and dimensions. The reference specifications for precision machining parts may vary depending on the specific product being manufactured.
In general, precision machining parts require a high level of accuracy and consistency. This means that the dimensions, geometries, and surface finish of the parts must meet the exact specifications outlined by the customer or the design requirements. The tolerances for precision machining parts are typically very tight, often ranging in the micron or sub-micron range.
To achieve such precision, manufacturers use a range of advanced machining techniques, including computer numerical control (CNC) machining, electrical discharge machining (EDM), and laser cutting. These methods allow for precise control over the cutting tools or energy sources used, resulting in accurate and repeatable machining processes.
The materials used in precision machining can vary widely, depending on the application and requirements of the part. Common materials include various metals like steel, aluminum, and titanium, as well as engineering plastics. The choice of material also affects the machining process, as different materials may require specific tooling and cutting parameters.
Quality control is a critical aspect of precision machining. Manufacturers employ various inspection techniques, including coordinate measuring machines (CMM), optical scanners, and surface profilometers, to verify the dimensions and surface finish of machined parts. Non-destructive testing methods, such as x-ray or ultrasonic testing, may also be employed for detecting any internal defects or irregularities.
In conclusion, precision machining parts require adherence to tight tolerances and specifications to ensure accurate dimensions and surface finish. The process involves advanced machining techniques and materials, and quality control is crucial to ensure the integrity and functionality of the final product. By using state-of-the-art machinery and employing skilled operators, manufacturers can deliver precision-machined parts that meet the high standards demanded by various industries.
Applications of precision machining part
Precision machining parts play a crucial role in a wide range of industries and applications, thanks to their accuracy, reliability, and intricacy. These parts are manufactured using advanced machining techniques that ensure their exact specifications and precise tolerances. Here are some of the key applications of precision machining parts:
1. Aerospace Industry: Precision machining parts are extensively used in the aerospace industry to manufacture critical components such as turbine blades, engine parts, landing gear, and structural elements. These parts need to be highly precise, durable, and able to withstand extreme temperatures and pressures.
2. Medical Industry: Precision machining parts are essential in the medical field for the manufacturing of surgical instruments, implants, prosthetics, and medical devices. The accuracy and reliability of these parts are crucial to ensuring the success of medical procedures and improving patient outcomes.
3. Automotive Industry: Precision machining parts are used in the automotive industry for the production of engines, transmission systems, braking systems, fuel injection systems, and other components. These parts need to meet stringent quality standards to ensure the safety and performance of vehicles.
4. Electronics Industry: Precision machining parts are vital for the fabrication of electronic components such as connectors, terminals, PCBs (Printed Circuit Boards), and semiconductor equipment. The precision and complexity of these parts are essential for the proper functioning of electronic devices.
5. Oil and Gas Industry: Precision machining parts are used in the extraction, refining, and distribution of oil and gas. They are employed in valves, pumps, drilling equipment, and other critical components. These parts must withstand harsh operating conditions such as high pressures, extreme temperatures, and corrosive environments.
6. Defense Industry: Precision machining parts are extensively used in the defense sector for the production of firearms, military vehicles, aircraft, and communication systems. These parts need to meet rigorous specifications to ensure the safety and effectiveness of defense equipment.
7. Robotics and Automation: Precision machining parts are essential for the manufacturing of robots and automated systems. They are used in the construction of robot arms, joints, gears, and other components that enable precise movements and high-speed operations.
In conclusion, precision machining parts find applications in numerous industries, including aerospace, medical, automotive, electronics, oil and gas, defense, and robotics. Their accuracy, reliability, and intricacy make them indispensable in the manufacturing of critical components that ensure the safety, performance, and efficiency of various systems and equipment.
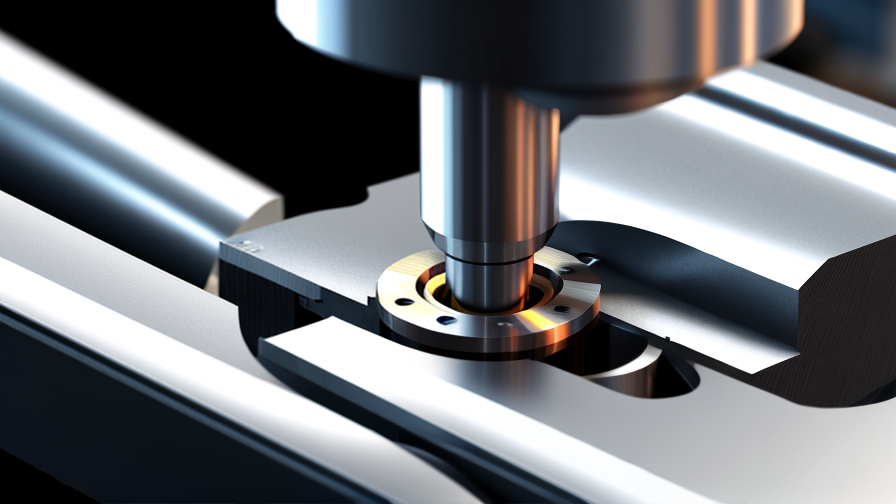
The Work Process and how to use precision machining part
Precision machining is a key process used in the manufacturing of various components across industries. It involves removing material from a raw piece through a controlled and precise grinding, cutting, or drilling process to create a finished product with high accuracy and tight tolerances. This process is highly crucial in industries like aerospace, automotive, medical, and electronics, where the quality and precision of parts are paramount.
The work process of precision machining starts with the design of the part to be manufactured using computer-aided design (CAD) software. The part’s specifications, dimensions, and tolerances are carefully defined during this stage. Once the design is finalized, it is transferred to computer-aided manufacturing (CAM) software that generates instructions for the precision machining equipment.
The next step involves selecting the appropriate machining method and equipment based on the part’s material, complexity, and quantity required. Common precision machining techniques include milling, turning, grinding, drilling, and electrical discharge machining (EDM). These methods employ various tools, cutting fluids, and machines to shape the raw material into the desired geometry accurately.
During the machining process, the operator follows the CAM instructions to load the raw material into the machine and secures it in place. The machine’s cutting tool then moves along the programmed path, removing material in a controlled manner. The operator monitors the process to ensure that the machine is operating correctly and the dimensions and tolerances are maintained consistently.
After the part is machined, it undergoes inspection and quality control to ensure it meets the required specifications. This can involve various non-destructive testing techniques, dimensional measurements using precision instruments, and visual inspection. Any deviations or defects are identified and rectified before the part is deemed acceptable for use.
Precision machining parts can be used in a wide range of applications. They are often critical components in machinery, engines, tools, and complex systems. Their high accuracy and tight tolerances enable them to function precisely and reliably in demanding environments. These parts provide numerous benefits to end-users, such as improved efficiency, increased durability, and superior performance.
In conclusion, precision machining is a meticulous process used in manufacturing to create high-quality parts with exceptional accuracy and tight tolerances. The process involves careful design, selection of appropriate machining methods, and rigorous inspection to ensure the final product meets the required specifications. Precision machining parts are widely used across industries due to their reliability and ability to enhance the performance of various systems and machinery.
Quality Testing Methods for precision machining part and how to control the quality
Precision machining parts are critical components in various industries, including aerospace, automotive, and medical. Hence, ensuring their quality is of utmost importance. There are several quality testing methods available for precision machining parts, and each method serves a specific purpose. Here are some commonly used quality testing methods for precision machining parts:
1. Dimensional Measurement: This method involves measuring the dimensions of the machined part using tools such as calipers, micrometers, and coordinate measuring machines (CMMs). It ensures that the part meets the specified tolerances.
2. Surface Roughness Measurement: Precision machining parts often require a specific surface finish. Surface roughness measurement is performed using profilometers or roughness testers to ensure the surface finish meets the required specifications.
3. Hardness Testing: Precision machining parts may need to possess specific hardness properties. Hardness testers are used to determine the hardness of the part, which indicates its strength and resistance to wear.
4. Visual Inspection: Visual inspection involves inspecting the part visually to detect any defects, such as cracks, chips, or surface imperfections. It is a crucial method to identify any visible anomalies that may affect the part’s performance.
5. Non-Destructive Testing (NDT): NDT methods, such as ultrasonic testing, magnetic particle testing, or liquid penetrant testing, are employed to identify hidden or subsurface defects in the part without causing damage. These methods are particularly useful for critical components with complex geometries.
To control the quality of precision machining parts, several measures can be implemented:
1. Strict Quality Control Processes: Implementing a robust quality control process ensures that each part undergoes thorough inspection at various stages of production. This includes inspections after raw material selection, during machining, and before final delivery.
2. Standardized Work Instructions: Providing clear and precise work instructions to machinists reduces human error during the machining process. Strict adherence to these instructions helps maintain consistent quality.
3. Calibration and Maintenance: Regular calibration of measuring tools and inspection equipment, based on international standards, ensures the accuracy of measurements. Additionally, timely maintenance and calibration of machining equipment help sustain the desired quality.
4. Training and Skill Development: Adequate training is essential for machinists to perform high-quality machining operations. Regular skill development programs ensure that machinists are up-to-date with the latest techniques and technologies.
5. Continuous Improvement: Implementing a culture of continuous improvement, such as Lean or Six Sigma methodologies, enables organizations to identify and rectify quality issues systematically. Regular data analysis and process optimization reduce variation and enhance overall quality.
By utilizing these quality testing methods and implementing strict quality control measures, precision machining part manufacturers can ensure consistent quality and meet the demanding requirements of diverse industries.
precision machining part Sample Policy and Post-Purchase Considerations for precision machining part from China
Sample Policy:
1. Quality Assurance: We understand the importance of high-quality precision machining parts. Therefore, we offer a sample policy to ensure customer satisfaction. Customers can request a sample of the part before making a bulk purchase. This allows them to assess the quality, accuracy, and precision of the machining part.
2. Customization: We offer customization services to meet the specific requirements of our customers. This includes providing technical drawings, specifications, and material selection options. We ensure that the final product adheres to the desired specifications.
3. Pricing: Our pricing is competitive and transparent. We provide detailed quotations that include all costs, such as material, machining, packaging, and shipping. Customers can request a breakdown of the pricing to fully understand the cost structure.
4. Lead Time: We have a reliable and efficient production process that allows us to deliver precision machining parts within the agreed-upon time frame. We provide customers with an estimated lead time at the time of order placement.
Post-Purchase Considerations:
1. Quality Inspection: Upon receiving the precision machining parts, customers are advised to perform a thorough quality inspection. This includes checking for any defects, dimensional accuracy, surface finish, and overall performance. If any issues are identified, they should be reported to us immediately.
2. Communication: We encourage open and timely communication with our customers throughout the post-purchase process. If any technical or operational support is required, we are available to assist.
3. Feedback: We value customer feedback as it helps us improve our products and services. We encourage customers to provide feedback on their overall experience, including the quality of the precision machining parts, packaging, and customer service.
4. Warranty and Returns: We offer a warranty on our precision machining parts against any manufacturing defects. If customers encounter any issues within the warranty period, we will take appropriate actions, such as repair or replacement, to resolve the problem.
5. Long-term Relationship: We strive to build long-term relationships with our customers. We offer ongoing support, repeat order discounts, and prioritize customer satisfaction to ensure a positive and lasting partnership.
Sourcing precision machining part from China: Opportunities, Risks, and Key Players
Sourcing precision machining parts from China can offer several opportunities for businesses looking to reduce costs and access a wide range of manufacturing capabilities. China has a well-established manufacturing industry with a large pool of skilled labor and advanced technologies, allowing for efficient and cost-effective production of precision machined parts.
One of the key opportunities of sourcing from China is the significant cost advantage. Labor costs in China tend to be lower compared to many other countries, resulting in considerable savings for businesses. Additionally, the country’s extensive supplier network and vertical integration capabilities allow for streamlined production processes and shorter lead times.
Furthermore, China has a vast array of manufacturers specializing in precision machining, offering a wide range of capabilities and certifications. From CNC milling and turning to grinding and EDM (Electrical Discharge Machining), Chinese manufacturers can accommodate various requirements and produce highly complex parts to meet specific specifications.
However, there are several risks associated with sourcing precision machining parts from China that businesses need to consider. Quality control can be a challenge due to inconsistencies in material sourcing and manufacturing processes. It is crucial for businesses to carefully select reliable suppliers and implement strict quality assurance measures to ensure the consistent production of high-quality parts.
Intellectual property protection is another risk to be mindful of when sourcing from China. While the country has made progress in improving its intellectual property laws, cases of intellectual property infringement and counterfeiting still exist. Businesses must take appropriate precautions to protect their designs and patents during the sourcing process.
Key players in China’s precision machining industry include Foxconn Technology Group, BYD Company Limited, and Huada Gene Group. These companies have established themselves as leaders in the manufacturing sector and are known for their extensive capabilities, quality products, and reliability.
In conclusion, sourcing precision machining parts from China offers opportunities for cost savings and access to diverse manufacturing capabilities. However, businesses should be cautious of the risks involved, such as quality control issues and intellectual property protection. By working with reputable suppliers and implementing strict quality assurance measures, businesses can benefit from China’s manufacturing expertise while mitigating potential risks.
How to find and select reliable precision machining part manufacturers in China,use google search manufacturers and suppliers
When searching for reliable precision machining part manufacturers in China, using Google search can be a helpful starting point. Here are a few steps to follow in order to find and select reputable manufacturers and suppliers:
1. Begin by performing a Google search using relevant keywords such as “precision machining part manufacturer China” or “CNC machining supplier China.” This will yield a list of potential manufacturers and suppliers.
2. Evaluate the search results and visit the websites of the companies that appear to be reliable and experienced. Look for information such as their history, expertise, machinery capabilities, and certifications. This will give you an initial idea of their credibility.
3. As you narrow down the list, check for customer reviews and testimonials. Look for feedback on their product quality, delivery time, customer service, and reliability. This will help further validate their reputation.
4. Contact the selected manufacturers and suppliers directly. Inquire about their manufacturing processes, quality control measures, and any specific requirements you have. A reliable manufacturer will be responsive and provide detailed answers to your queries.
5. Request samples or prototypes to assess the quality of their work. This will help you ensure that their precision machining parts meet your specifications and standards.
6. Seek information on the manufacturer’s production capacity and lead times. It is crucial to ensure that they can meet your volume requirements and provide timely delivery.
7. Confirm whether the manufacturer has the necessary certifications and complies with international standards such as ISO 9001. This is an indicator of their commitment to quality management systems.
8. Obtain multiple quotations from different manufacturers and compare them in terms of price, quality, and delivery time. However, be cautious of prices that seem too good to be true as they may compromise on quality.
9. Finally, consider visiting the selected manufacturers’ facilities in person if feasible. This will allow you to assess their manufacturing capabilities, equipment, and overall infrastructure.
By following these steps, you can find and select reliable precision machining part manufacturers in China who align with your requirements and standards.
How to check precision machining part manufacturers website reliable,use google chrome SEOquake check if ranking in top 10M
To check the reliability of precision machining part manufacturers’ websites, you can follow these steps:
1. Use Google Chrome: Start by opening the website in Google Chrome, as it offers various useful tools and extensions for checking website reliability.
2. Install SEOquake extension: Add the SEOquake extension to your Google Chrome browser. This tool provides helpful insights and data related to a website’s ranking and performance.
3. Check website ranking: Once the extension is installed, click on the SEOquake icon in your browser’s toolbar. A sidebar will appear on the left-hand side of the screen. Scroll down and locate the tab labeled “SEO” within the sidebar.
4. Analyze website ranking: Within the “SEO” tab, you will find a section called “Google Index.” Check if the website is ranking within the top 10 million (10M) websites. If the website is ranked within this range, it indicates that it receives a decent amount of traffic and is relatively popular.
5. Consider other factors: While the ranking is an essential factor, it should not be the sole criteria for determining reliability. Additionally, consider factors such as website design, content quality, customer reviews and testimonials, certifications, industry partnerships, and overall reputation.
6. Evaluate information and credibility: Look for relevant and accurate information about the precision machining parts offered by the manufacturer. Verify if the website provides detailed descriptions, specifications, and technical data sheets for their products. Check for certifications or affiliations within the precision machining industry to determine credibility.
7. Check customer feedback: Look for customer reviews and testimonials on the website or external platforms. Positive feedback and ratings from previous customers can enhance reliability.
8. Verify contact information: Ensure that the website provides valid contact information like a physical address, phone number, and email address. This helps ensure that you can reach out to them and verify their legitimacy.
Remember, while using Google Chrome and SEOquake to check website rankings can provide insights, it’s crucial to consider various other factors to determine the reliability and trustworthiness of a precision machining part manufacturer.
Top 10 precision machining part manufacturers in China with each 160 words introduce products,then use markdown create table compare
1. Foxron Precision Metal Parts Co., Ltd.
Foxron specializes in providing precision machining parts for various industries such as automotive, electronics, and medical. They offer a wide range of products including CNC turned parts, CNC milling parts, and CNC machining parts. With state-of-the-art facilities and advanced equipment, Foxron ensures high precision and quality in all their products. They also provide customized solutions to meet specific requirements, ensuring customer satisfaction.
2. Ningbo Target Machinery Co., Ltd.
Ningbo Target Machinery is a leading manufacturer of precision machining parts in China. They specialize in producing CNC machined parts, CNC milling parts, and custom machining components. Their expertise lies in providing high-quality products with tight tolerances and complex geometries. Ningbo Target Machinery serves industries like aerospace, defense, and automotive, delivering precise and reliable solutions.
3. Ever Hardware Industrial Limited
Ever Hardware Industrial Limited is renowned for its precision machining parts that cater to industries like telecommunications, electronics, and robotics. The company offers CNC machined parts, CNC turning parts, and custom metal parts tailored to customer specifications. With a focus on quality and efficiency, Ever Hardware prides itself on delivering precision parts with quick turnaround time.
4. China Best Machined Co., Ltd.
China Best Machined specializes in precision machining parts, including CNC machined parts, milling parts, and turning parts. They serve industries such as aerospace, medical, and automotive. The company’s products showcase high precision, tight tolerances, and a wide range of materials. China Best Machined also offers engineering support and custom solutions, ensuring complete customer satisfaction.
5. Dongguan Qy Hardware Mould Part Factory
Dongguan Qy Hardware Mould Part Factory excels in manufacturing precision machining parts for industries such as electronics, medical, and automotive. They offer CNC machined parts, milling parts, and turning parts with precise dimensions and finishes. The factory’s commitment to quality, competitive pricing, and timely delivery has earned them a reputable position in the market.
6. Shanghai Precision Machining Co., Ltd.
Shanghai Precision Machining Co., Ltd. is a leading manufacturer of precision machining parts in China. They specialize in CNC machined components, casting parts, and sheet metal fabrications. Serving industries like telecommunications, robotics, and energy, they focus on delivering high-precision solutions meeting international standards. Their state-of-the-art facility and extensive expertise ensure top-quality products.
7. Ningbo OEM Industry Manufacturer Ltd.
Ningbo OEM Industry Manufacturer Ltd. is a prominent supplier of precision machining parts, offering CNC machined parts, milling parts, and turning parts. Their comprehensive capabilities cater to industries like aerospace, automotive, and electronics. With advanced machinery and rigorous quality control, they assure precision, reliability, and consistency in their products.
8. Suzhou Shengding Precision Machinery Co., Ltd.
Suzhou Shengding Precision Machinery specializes in the production of precision machining parts for industries like electronics, medical, and automation. Their product range includes CNC machined parts, milling parts, and turning parts. The company’s expertise lies in providing high-quality products with complex geometries and tight tolerances.
9. Shenzhen Huameijia Hardware Industry Co., Ltd.
Shenzhen Huameijia Hardware Industry is a trusted manufacturer of precision machining parts in China. They offer CNC machined parts, milling parts, and turning parts with remarkable precision and tight tolerances. Serving industries such as automotive, aerospace, and robotics, they constantly strive to meet customer requirements with superior quality products.
10. Jiangyin Yolanda Metal Technology Co., Ltd.
Jiangyin Yolanda Metal Technology specializes in precision machining parts for industries like automotive, electronics, and energy. They provide CNC machined parts, milling parts, and turning parts made from a variety of materials. With a focus on customer needs and advanced production capabilities, they offer high-quality products that meet international standards.
| **Company** | **Specialization** | **Industries Served** |
| —————————————– | ————————————— | ——————————————– |
| Foxron Precision Metal Parts Co., Ltd. | CNC turned parts, milling parts, | Automotive, electronics, medical |
| Ningbo Target Machinery Co., Ltd. | CNC machined parts, CNC milling parts | Aerospace, defense, automotive |
| Ever Hardware Industrial Limited | CNC machined parts, CNC turning parts | Telecommunications, electronics, robotics |
| China Best Machined Co., Ltd. | CNC machined parts, milling parts | Aerospace, medical, automotive |
| Dongguan Qy Hardware Mould Part Factory | CNC machined parts, milling parts | Electronics, medical, automotive |
| Shanghai Precision Machining Co., Ltd. | CNC machined components, casting parts | Telecommunications, robotics, energy |
| Ningbo OEM Industry Manufacturer Ltd. | CNC machined parts, milling parts | Aerospace, automotive, electronics |
| Suzhou Shengding Precision Machinery Co. | CNC machined parts, milling parts | Electronics, medical, automation |
| Shenzhen Huameijia Hardware Industry Co. | CNC machined parts, milling parts | Automotive, aerospace, robotics |
| Jiangyin Yolanda Metal Technology Co., Ltd.| CNC machined parts, milling parts | Automotive, electronics, energy |
Background Research for precision machining part manufacturers Companies in China, use qcc.com archive.org importyeti.com
When it comes to precision machining part manufacturers in China, several resources can be utilized to gather background research. Three prominent platforms for this purpose are qcc.com, archive.org, and importyeti.com.
Qcc.com is a Chinese platform that provides comprehensive business information, including company profiles and registration details. Users can search for precision machining part manufacturers and access vital data such as their contact information, business scope, and legal status. This platform offers a reliable way to verify the authenticity and legitimacy of a manufacturer in China.
Archive.org, also known as the Wayback Machine, is an internet archive that captures and stores snapshots of websites at different points in time. This tool can be used to access historical information about precision machining part manufacturers’ websites and track their evolution over the years. It can be particularly helpful in assessing a manufacturer’s longevity, technological advancements, and overall growth trajectory.
Importyeti.com is a platform that focuses on import and export data. It provides information regarding a company’s import activities, including the products they import, the countries they trade with, and the volume of their imports. By using Importyeti.com, researchers can gain insights into the export capabilities and market reach of precision machining part manufacturers in China.
Together, these platforms offer a comprehensive approach to conducting background research on precision machining part manufacturers in China. By utilizing qcc.com, archive.org, and importyeti.com, researchers can gather valuable information on a manufacturer’s business details, evolution, and export activities.
Leveraging Trade Shows and Expos for precision machining part Sourcing in China
Trade shows and expos play a crucial role in precision machining part sourcing in China. These events provide a platform for connecting manufacturers, suppliers, and buyers, enabling them to establish business relationships and explore potential partnerships.
Attending trade shows and expos in China offers several advantages for sourcing precision machining parts. Firstly, it provides an opportunity to see and assess a wide range of products, technologies, and capabilities offered by different exhibitors. This allows buyers to compare quality, price, and innovation, and make informed decisions about potential suppliers.
Furthermore, trade shows and expos offer a chance to meet face-to-face with potential suppliers. Building personal relationships is crucial in Chinese business culture, and meeting suppliers in person helps to establish trust and credibility. It also allows buyers to discuss their specific requirements, negotiate terms, and get a better understanding of the manufacturing processes and capabilities.
Additionally, trade shows and expos often showcase the latest advancements in precision machining technologies, materials, and techniques. This provides buyers with valuable insights into industry trends and innovations, helping them identify potential opportunities for cost savings, efficiency improvements, or product enhancements.
Moreover, attending these events also allows buyers to network and learn from industry experts and peers. Seminars, workshops, and panel discussions provide valuable insights and knowledge-sharing opportunities, which can help buyers stay updated with industry trends, regulations, and best practices.
To make the most out of trade shows and expos, buyers should thoroughly research and plan their visit in advance. Identifying target suppliers, defining specific sourcing requirements, and scheduling appointments can help maximize the time spent at the event. It is also essential to follow up with potential suppliers after the event, solidifying relationships and ensuring a smooth sourcing process.
In conclusion, leveraging trade shows and expos for precision machining part sourcing in China offers numerous benefits. It provides a comprehensive view of available products and technologies, facilitates face-to-face meetings, showcases industry advancements, and enables networking opportunities. By effectively utilizing these events, buyers can find reliable suppliers, establish fruitful partnerships, and ultimately enhance their sourcing strategies.
The Role of Agents and Sourcing Companies in Facilitating precision machining part Purchases from China
Agents and sourcing companies play a pivotal role in facilitating precision machining part purchases from China. These entities act as intermediaries between buyers and suppliers, streamlining the procurement process and ensuring a successful transaction.
One key role of agents and sourcing companies is to identify and assess potential Chinese suppliers for precision machining parts. They have a wide network of contacts and extensive knowledge of the market, enabling them to identify reliable and reputable suppliers. By conducting thorough background checks, verifying certifications, and assessing production capabilities, they help buyers find suppliers that meet their requirements in terms of quality, pricing, and lead times.
Furthermore, agents and sourcing companies handle the negotiation process on behalf of the buyers, leveraging their expertise and knowledge of the Chinese market. They are skilled negotiators who can secure favorable terms for the buyers, such as competitive prices and flexible payment terms. Their understanding of the local business culture and language proficiency allows for effective communication, reducing the chances of misunderstandings and ensuring smooth collaboration between buyers and suppliers.
Additionally, agents and sourcing companies provide logistical support, including handling the transportation, customs clearance, and documentation processes. They have experience in navigating the complex logistics and regulatory landscape, ensuring that the precision machining parts reach the buyers in a timely manner and with all necessary certifications and paperwork.
Lastly, agents and sourcing companies also play a crucial role in quality control and inspection. They conduct regular factory visits, inspecting the production process, and ensuring that the parts meet the required quality standards. By acting as the buyer’s representative, they protect the buyer’s interests and help mitigate the risks associated with sourcing from overseas suppliers.
In conclusion, agents and sourcing companies simplify the process of purchasing precision machining parts from China by identifying reliable suppliers, negotiating favorable terms, providing logistical support, and ensuring product quality. Their expertise and local knowledge are invaluable in ensuring a successful and efficient procurement process.
Price Cost Research for precision machining part manufacturers Companies in China, use temu.com and 1688.com
When researching precision machining part manufacturers in China, two popular platforms to consider are Temu.com and 1688.com. These platforms offer a wide range of suppliers and products, allowing buyers to find the best manufacturing companies for their needs.
Temu.com is an online marketplace that connects buyers with precision machining part manufacturers from various industries. The platform offers a user-friendly interface, which makes it easy for buyers to search for suppliers and compare prices. Temu.com provides detailed product descriptions, including specifications and pricing information, enabling buyers to make informed decisions. Additionally, the platform offers a messaging system that allows buyers to directly communicate with manufacturers.
Another platform worth considering is 1688.com, which is one of the largest online sourcing platforms in China. It provides a vast range of suppliers, including precision machining part manufacturers. 1688.com allows buyers to search for products based on their specific requirements, making it easy to find the right manufacturers at competitive prices. The platform also provides supplier ratings and reviews, helping buyers ensure they are partnering with trustworthy and reputable manufacturers.
When conducting price cost research for precision machining part manufacturers in China, it is crucial to keep the following points in mind:
1. Compare prices: Both Temu.com and 1688.com allow buyers to compare prices from different manufacturers. This helps in finding the most cost-effective option without compromising on quality.
2. Communication: Utilize the messaging systems provided by these platforms to communicate directly with suppliers. This allows for clarifying any pricing details or negotiating for the best rates.
3. Shipping and logistics: Keep in mind that shipping costs, customs duties, and other logistics charges should be considered while researching prices. Confirm with manufacturers their ability to handle shipping and any associated costs.
4. Quality assurance: While price is important, ensuring product quality should be a priority. Look for reviews, certifications, and quality control measures implemented by the manufacturers to guarantee products meet your standards.
In conclusion, Temu.com and 1688.com are reliable platforms for conducting price cost research for precision machining part manufacturers in China. By utilizing these platforms and implementing the suggested strategies, buyers can efficiently find high-quality manufacturers at competitive prices.
Shipping Cost for precision machining part import from China
The shipping cost for importing precision machining parts from China depends on various factors such as the weight and dimensions of the shipment, the mode of transportation chosen, the destination, and any additional services required.
If the parts are small and lightweight, air freight might be the most suitable option. Air freight is generally faster but more expensive than sea freight. The cost of air freight is calculated based on chargeable weight, which is determined by either the actual weight or the volumetric weight – whichever is higher.
Sea freight is a more cost-effective option for bulky and heavy shipments. The cost is usually calculated per cubic meter or per container, depending on the volume and weight of the cargo. However, sea freight takes longer than air freight due to transit and customs clearance procedures.
Besides the transportation cost, other expenses to consider are customs duties, broker fees, documentation fees, insurance, and any extra services like door-to-door delivery or cargo tracking.
To estimate shipping costs accurately, it is advisable to consult a freight forwarder or shipping agent who can provide detailed quotes and assist with the necessary documentation and logistics. Additionally, freight forwarders may have negotiated rates with shipping carriers, allowing them to offer competitive prices.
It is crucial to plan ahead and consider all aspects while importing precision machining parts from China to ensure a smooth and cost-effective shipping process.
Compare China and Other precision machining part Markets: Products Quality and Price,Visible and Hidden Costs
China has emerged as a major player in the precision machining parts market. Its competitive advantage lies in its large pool of skilled labor, advanced infrastructure, and low manufacturing costs. However, when comparing China’s precision machining part market to other markets, several factors should be considered including products quality, price, visible and hidden costs.
In terms of product quality, China has made significant strides in improving its manufacturing processes and adopting advanced technologies. Chinese precision machining parts often meet international quality standards and are available in a wide range of specifications. However, it is essential to conduct thorough research and due diligence to ensure that the supplier has the necessary certifications and quality control measures in place.
Price is a crucial factor when comparing markets. China’s manufacturing costs are often lower compared to other countries due to its abundant labor force and economies of scale. Consequently, Chinese precision machining parts tend to be more cost-effective, making them attractive to buyers seeking competitive pricing options. However, it is important to consider additional costs such as shipping, customs duties, and import taxes, which can vary depending on the buyer’s location and the volume of the order.
Visible costs refer to the expenses that are clearly stated in the purchase agreement, such as the unit price of the precision machining parts. Chinese suppliers are known for their ability to offer low visible costs due to their cost efficiency and negotiation skills. On the other hand, hidden costs, which are often overlooked, can arise from issues such as quality defects, delays in delivery, and communication barriers. It is essential for buyers to carefully assess these factors and communicate their expectations clearly to minimize potential hidden costs.
In conclusion, China’s precision machining part market offers a competitive advantage in terms of product quality and price. However, buyers need to be cautious in assessing both visible and hidden costs associated with sourcing from China. Thorough research, due diligence, and effective communication with suppliers are vital for ensuring a successful procurement process.
Understanding Pricing and Payment Terms for precision machining part: A Comparative Guide to Get the Best Deal
When it comes to precision machining parts, understanding pricing and payment terms is crucial to get the best deal for your business. This comparative guide aims to provide insights into the factors that influence pricing and tips to negotiate favorable payment terms within a concise framework of 300 words.
Pricing for precision machining parts is influenced by several factors. Firstly, the complexity and intricacy of the part design impact the cost, as intricate parts require more time, expertise, and specialized equipment. Additionally, material selection is also a critical aspect, with exotic or rare materials usually demanding higher prices. Quantity and volume requirements can also affect pricing, as larger orders often benefit from economies of scale.
To get the best deal, it’s essential to obtain multiple quotes from different precision machining suppliers. Comparing prices and services allows you to identify competitive offers. However, it’s crucial not to make pricing the sole determining factor. Quality, expertise, lead time, and reputation are equally important considerations when selecting a supplier.
Negotiating favorable payment terms can also enhance your deal. Start by discussing your payment preferences and requirements early in the negotiation process. Suppliers may offer discounts for upfront payments or long-term contracts. Alternatively, you can propose payment milestones based on production progress to ensure quality and timely delivery.
Utilizing payment methods that provide buyer protection is advisable. Escrow services or letters of credit can help mitigate risks and build trust between buyer and seller. Additionally, clarify any extra costs such as tooling fees or changes in the order that may affect the final price.
Lastly, maintaining a positive and respectful relationship with your precision machining supplier is key. Communicating clearly and promptly, as well as providing feedback on their performance, can foster a long-term partnership and potentially lead to preferential pricing and payment terms in the future.
In conclusion, understanding pricing and payment terms for precision machining parts enables you to secure the best deal for your business. Considering factors such as part complexity, materials, quantity, and comparing multiple quotes are essential for favorable pricing. Negotiating payment terms based on your preferences and utilizing buyer protection methods can further enhance the deal. Building a positive relationship with your supplier also opens doors for future cost-saving opportunities.
Chinese Regulations and Industry Standards Certifications for precision machining part,Import Regulations and Customs for precision machining part from China
Chinese Regulations and Industry Standards Certifications for precision machining parts:
China has various regulations and industry standards certifications in place for precision machining parts to ensure high-quality manufacturing and to protect consumer interests. Some of these regulations and certifications include:
1. GB/T (Guobiao/Tuijian) Standards: The GB/T standards are industry standards set by the Standardization Administration of China (SAC). These standards cover a wide range of specifications and requirements for precision machining parts. Compliance with relevant GB/T standards ensures that the products meet quality and safety requirements.
2. ISO Certifications: Many precision machining part manufacturers in China obtain ISO certifications to demonstrate their adherence to international management and quality control standards. The most common ISO certifications for precision machining parts include ISO 9001 (quality management system), ISO 14001 (environmental management system), and ISO 45001 (occupational health and safety management system).
3. CCC Certification: The China Compulsory Certification (CCC) mark is a mandatory certification for products sold in China. While it is not specific to precision machining parts, certain components or electrical elements used in precision machining parts may require CCC certification to comply with safety regulations.
4. RoHS Compliance: The Restriction of Hazardous Substances (RoHS) directive restricts the use of hazardous substances in electrical and electronic equipment. Manufacturers of precision machining parts need to ensure compliance with RoHS regulations, which limit the presence of substances such as lead, mercury, cadmium, and certain flame retardants.
Import Regulations and Customs for precision machining parts from China:
When importing precision machining parts from China, importers need to comply with certain regulations and customs procedures. These may include:
1. Customs Declarations: Importers should accurately complete customs declarations by providing detailed product descriptions, quantities, values, country of origin, and other necessary information. It is crucial to classify the precision machining parts under the correct Harmonized System (HS) code for proper customs clearance.
2. Import Licenses: Certain precision machining parts may require import licenses or permits, depending on their nature and usage. Importers should consult with relevant authorities or agencies to determine if any specific licenses are necessary.
3. Customs Duties and Taxes: Importers will be responsible for paying customs duties and applicable taxes on imported precision machining parts. The rates may vary depending on the type of product and the country of import.
4. Product Compliance: Importers should ensure that the precision machining parts comply with the regulations and standards of the destination country. In some cases, additional certifications or testing may be required to meet local requirements.
It is essential for importers of precision machining parts to stay updated on any changes in regulations and customs procedures to ensure smooth and compliant imports from China. Consulting with experienced customs brokers or trade experts can provide valuable guidance in navigating the import process.
Sustainability and Environmental Considerations in precision machining part Manufacturing
Sustainability and environmental considerations play a crucial role in precision machining part manufacturing. This manufacturing process involves the creation of complex and intricate parts using various materials such as metals, plastics, and composites. Here are some key points highlighting the importance of sustainability and environmental considerations in precision machining part manufacturing:
1. Material Selection: Sustainable manufacturing starts with the selection of materials. Precision machining requires the use of raw materials, and opting for environmentally friendly alternatives can make a significant difference. Choosing recycled or eco-friendly materials reduces the overall environmental impact of the process.
2. Energy Efficiency: Precision machining part manufacturing often involves the use of energy-intensive machining equipment such as CNC machines. To reduce the energy consumption, manufacturers can adopt energy-efficient machines and technologies. Regular maintenance and optimization of machining processes can also enhance energy efficiency.
3. Waste Reduction: Precision machining generates considerable waste in the form of metal shavings, coolant, and sludge. To promote sustainability, manufacturers should implement waste reduction strategies. Recycling and reusing waste materials can minimize environmental impact while reducing costs associated with material procurement.
4. Environmental Compliance: Precision machining part manufacturers need to comply with environmental regulations and standards. Adhering to these regulations is essential to ensure that the manufacturing process does not harm the environment, surrounding ecosystems, or human health. Proper disposal of hazardous waste and compliance with emission limits are critical for sustainable manufacturing.
5. Life Cycle Assessment: Conducting a life cycle assessment (LCA) helps determine the environmental impact of precision machining part manufacturing. This assessment considers various stages, including material extraction, manufacturing, transportation, and end-of-life disposal. By analyzing the life cycle, manufacturers can identify potential environmental hotspots and implement sustainable solutions.
6. Collaboration and Innovation: Collaboration between manufacturers, suppliers, and customers is crucial to foster sustainable practices in precision machining part manufacturing. Sharing knowledge and experiences can lead to the development of innovative solutions and technologies that reduce environmental impact. Embracing new precision machining techniques, such as additive manufacturing, can also contribute to sustainability efforts.
In conclusion, sustainability and environmental considerations are vital for precision machining part manufacturing. By selecting eco-friendly materials, improving energy efficiency, minimizing waste, complying with regulations, conducting life cycle assessments, and promoting collaboration and innovation, manufacturers can reduce their environmental footprint and contribute to a more sustainable future.
List The Evolution history of “precision machining part”
Precision machining parts have evolved significantly over time as technology and manufacturing processes have advanced. The evolution history of precision machining parts can be summarized as follows:
1. Early Development (18th and 19th century): Precision machining initially started with the development of early machine tools, such as the lathe and milling machine. These machines were operated manually and were used for basic shaping and cutting tasks. The focus was on improving accuracy and repeatability.
2. Industrial Revolution (late 19th and early 20th century): With the advent of the Industrial Revolution, precision machining underwent a revolution. Steam-powered engines and mechanical systems allowed for the development of more advanced machine tools, such as the planer and grinder. Precision improved, allowing for more complex and precise parts to be manufactured.
3. Computer Numerical Control (CNC) (mid-20th century): The introduction of computers into machining brought about a significant advancement in precision machining. CNC technology enabled the automation of machining processes using precise mathematical instructions. This allowed for increased accuracy and repeatability of machining operations.
4. Advanced Materials and Technologies (late 20th and early 21st century): With the evolution of new materials, such as high-strength alloys and composites, precision machining had to adapt to meet the challenges posed by these materials. Advancements in cutting tool technology and machining techniques, such as high-speed machining and multi-axis machining, allowed for more efficient and precise machining of these materials.
5. Integration of Automation and Robotics (current era): The integration of automation and robotics into precision machining has further improved efficiency and accuracy. Robotics have made it possible to perform complex machining operations with minimal human intervention. Automation has also allowed for continuous, unmanned machining operations.
In summary, precision machining parts have evolved from manual, labor-intensive processes to highly automated and sophisticated systems. Advancements in technology, materials, and manufacturing processes have played a crucial role in driving this evolution. Today, precision machining plays a vital role in various industries, including aerospace, automotive, electronics, and medical, enabling the production of intricate and precise parts that meet the stringent requirements of modern applications.
The Evolution and Market Trends in precision machining part Industry
The precision machining part industry has experienced significant evolution and market trends over the years. Precision machining is the process of creating complex parts with high accuracy and precision using computer numerical control (CNC) machines.
One of the key evolutions in the industry has been the advancement of technology. CNC machines have become more sophisticated and capable of handling complex machining tasks. This has allowed precision machining part manufacturers to produce parts with higher precision and faster turnaround times. Additionally, advanced software programs and computer-aided design (CAD) have enhanced the design and manufacturing processes, leading to improved efficiency and reduced errors.
Another evolution in the industry is the increasing demand for miniaturization. As technology continues to advance, the demand for smaller and more intricate parts has grown. Precision machining part manufacturers have had to adapt to this trend by investing in advanced equipment and skills to meet the requirements of industries such as electronics, medical devices, and aerospace.
In terms of market trends, there has been a move towards outsourcing precision machining part manufacturing. Many companies, especially those in the automotive and aerospace industries, are choosing to outsource their machining needs to specialized machining shops. This allows them to focus on their core competencies while benefitting from the expertise and advanced capabilities of precision machining part manufacturers.
Additionally, there has been an increased emphasis on sustainability and environmental consciousness in the precision machining part industry. Manufacturers are adopting eco-friendly practices such as recycling materials, reducing energy consumption, and using environmentally friendly cutting fluids. This not only helps to minimize the industry’s impact on the environment but also demonstrates a commitment to sustainability, which is increasingly valued by customers.
In conclusion, the precision machining part industry has evolved through advancements in technology, increased demand for miniaturization, and a move towards outsourcing. Market trends include the focus on sustainability and environmental consciousness. These trends are likely to continue shaping the industry as it responds to the ever-changing needs and demands of various sectors.
Custom Private Labeling and Branding Opportunities with Chinese precision machining part Manufacturers
Chinese precision machining part manufacturers offer excellent opportunities for custom private labeling and branding. With their expertise and advanced production capabilities, they can help businesses create high-quality products tailored to their specific needs.
One of the key advantages of working with Chinese manufacturers is their ability to provide custom solutions. Whether it’s machining a unique part or modifying an existing design, they can deliver personalized products that align with a brand’s requirements. By leveraging their vast experience and technical know-how, manufacturers can produce precision components with exceptional accuracy and consistency.
Private labeling is another attractive option offered by Chinese manufacturers. Businesses can establish their brand identity by customizing the packaging, labeling, and product appearance. This allows companies to differentiate themselves from competitors and create a strong brand perception among customers. Chinese manufacturers understand the importance of branding and work closely with businesses to ensure their products reflect the desired image and message.
Moreover, Chinese manufacturers often provide cost-effective solutions due to their access to advanced machinery, skilled labor, and resource availability. This enables businesses to maintain competitive pricing while still offering customized products. Chinese manufacturers also have a large production capacity, which ensures scalability and timely delivery, even for large orders.
However, it is crucial to choose a reliable and reputable Chinese manufacturer to ensure quality control and protect intellectual property rights. Businesses should thoroughly research and vet potential partners, considering factors such as certifications, production capabilities, and track record.
In summary, Chinese precision machining part manufacturers offer attractive opportunities for custom private labeling and branding. Their expertise, production capabilities, cost-effective solutions, and ability to deliver tailored products make them an ideal choice for businesses looking to create unique and high-quality products.
Tips for Procurement and Considerations when Purchasing precision machining part
When it comes to purchasing precision machining parts, there are several considerations to keep in mind to ensure a successful procurement process. Here are some tips and factors to consider:
1. Quality: The most crucial aspect is the quality of the precision machining part. Look for suppliers or manufacturers with a strong reputation for producing high-quality components. They should have certified quality systems in place, such as ISO 9001, to ensure consistent quality standards.
2. Material and Design: The materials used in precision machining parts greatly impact their performance and durability. Consider the specific requirements of your project and select the appropriate material accordingly. Additionally, evaluate the design of the part to ensure it is optimized for functionality and efficiency.
3. Supplier Capability: Assess the capability and experience of the supplier. Do they have expertise in manufacturing precision machining parts? Can they accommodate your specific requirements and meet your production schedule? Consider their capacity, equipment, and technical proficiency before making a decision.
4. Cost and Pricing: While cost is an important consideration, it should not be the sole determining factor. Evaluate the pricing structure and consider the balance between quality and value for money. Cheaper options may compromise the overall quality and require frequent replacements, which can be costly in the long run.
5. Delivery Time: Consider the supplier’s ability to meet your desired delivery schedule. Precision machining parts are often critical components in a larger manufacturing process, and any delays can have significant impacts on production.
6. Communication and Support: Look for suppliers who maintain clear and efficient communication channels. Ensure they are responsive and provide timely updates throughout the procurement process. Additionally, consider post-sales support, such as warranty and customer service, as these can greatly contribute to a successful procurement experience.
7. Supplier Reputation: Research and evaluate the reputation of the supplier in the industry. Seek recommendations, read customer reviews, and check their track record to gauge their reliability and trustworthiness.
By considering these factors and following these tips, you can make an informed decision when purchasing precision machining parts. Remember to maintain open communication with your supplier, provide detailed specifications, and clarify any questions or concerns to ensure a successful procurement process.
FAQs on Sourcing and Manufacturing precision machining part in China
1. Why should I consider sourcing and manufacturing precision machining parts in China?
Sourcing and manufacturing precision machining parts in China can provide significant cost savings due to lower labor and production costs compared to many other countries. Additionally, China has a well-established manufacturing industry with a wide range of specialized machining capabilities and a vast supplier network, ensuring access to various materials and advanced technologies.
2. How can I find reliable manufacturers in China?
To find reliable manufacturers, it is crucial to conduct thorough research and due diligence. Utilize online platforms such as Alibaba, Global Sources, or Made-in-China.com to browse through manufacturers’ profiles, customer reviews, and certifications. Seeking recommendations from industry experts or attending trade shows in China can also provide valuable insight and networking opportunities.
3. What are the quality standards in China’s precision machining industry?
China’s precision machining industry has made significant advancements in terms of quality standards. Many Chinese manufacturers comply with international quality certifications such as ISO 9001, TS 16949, or AS9100, ensuring that their products meet rigorous quality requirements. Prioritize working with certified manufacturers to ensure adherence to quality standards.
4. How can I manage communication and language barriers when working with Chinese manufacturers?
Communication and language barriers can be overcome by employing translators, hiring local sourcing agents, or working with international trade consultants who possess a deep understanding of China’s manufacturing landscape. Clear and concise communication through written documentation can also help minimize misunderstandings and ensure accurate product specifications.
5. What is the typical lead time for precision machining parts manufactured in China?
Lead time can vary depending on the complexity of the part, order quantity, and manufacturer’s production capacity. However, Chinese manufacturers generally offer competitive lead times due to their efficient production processes and capability to handle large-scale manufacturing. Usually, lead times can range from a few weeks to a few months, so it is essential to discuss specific timelines with manufacturers upfront.
6. What are the potential challenges when sourcing and manufacturing in China?
Some challenges when sourcing and manufacturing in China include intellectual property concerns, quality control, cultural differences, and logistics. It is crucial to choose reputable manufacturers, establish clear contracts, protect intellectual property through patents or trademarks, conduct regular inspections, and partner with experienced logistics providers to mitigate these challenges effectively.
In summary, sourcing and manufacturing precision machining parts in China can offer cost savings, access to advanced technologies, and a vast supplier network. By conducting thorough research, ensuring quality certifications, managing communication effectively, and addressing potential challenges, successful sourcing and manufacturing ventures can be achieved in China.
Why contact sourcifychina.com get free quota from reliable precision machining part suppliers?
SourcifyChina.com offers a free quota to its users to connect them with reliable precision machining part suppliers in order to streamline the sourcing process and help businesses find the best sourcing solutions. The platform understands the challenges faced by companies in finding trustworthy suppliers that meet their specific requirements.
By offering a free quota, SourcifyChina.com aims to simplify the sourcing process and bridge the gap between buyers and suppliers. This allows businesses to access a network of pre-vetted suppliers that have been thoroughly checked for their capabilities, quality standards, and manufacturing expertise. This helps buyers save time, effort, and resources that are typically spent on researching and evaluating potential suppliers.
The free quota provided by SourcifyChina.com allows users to submit their sourcing requirements and specifications, which are then matched with the most suitable precision machining part suppliers from their extensive database. The suppliers are selected based on their ability to meet the buyer’s specific needs, such as manufacturing capabilities, quality certifications, production capacity, pricing, and delivery timelines.
By leveraging SourcifyChina.com’s network of reliable suppliers, businesses can ensure that they are connected to trustworthy manufacturers who can deliver high-quality precision machining parts. This reduces the risk of dealing with unreliable suppliers that may compromise on quality, pricing, or delivery commitments.
In conclusion, SourcifyChina.com offers a free quota to connect businesses with reliable precision machining part suppliers, enabling them to streamline the sourcing process and find the best suppliers that meet their specific requirements. This service helps businesses save time, effort, and resources, while ensuring they are connected to trustworthy manufacturers.