Introduce about pressure forming guide,Qulity,Cost,Supplier,Certification,Market,Tips,FAQ
Pressure forming is a manufacturing process that involves heating a plastic sheet and then forming it with pressure against a mold. This technique is highly versatile and widely used in various industries, such as automotive, electronics, and packaging. In this guide, we will provide an overview of pressure forming, including its quality, cost, suppliers, certifications, market, tips, and frequently asked questions (FAQs).
Quality: Pressure forming offers excellent mold definition and detail, resulting in high-quality finished products. The process enables complex shapes, sharp corners, and fine textures, making it ideal for producing aesthetically appealing parts.
Cost: Pressure forming generally offers a cost advantage over other processes like injection molding for low to medium-volume production runs. The tooling costs are lower since pressure forming uses less pressure and lower temperatures than injection molding. Additionally, the process reduces material waste and offers faster production cycles, contributing to lower overall costs.
Suppliers: There are numerous pressure forming suppliers globally, ranging from large-scale manufacturers to smaller local companies. The choice of a supplier depends on factors such as location, production requirements, and cost considerations. It is advisable to select a supplier with a proven track record, expertise in the required materials, and the ability to meet specific quality standards.
Certification: Pressure forming suppliers can obtain various certifications, such as ISO 9001 (quality management), ISO 14001 (environmental management), and ISO 13485 (medical devices). These certifications ensure that the supplier adheres to industry best practices, maintains consistent quality, and meets regulatory requirements.
Market: Pressure forming is widely used in industries such as automotive, aerospace, medical, and consumer goods. The market for pressure-formed parts is growing rapidly, driven by the demand for lightweight, cost-effective, and visually appealing components.
Tips: When considering pressure forming, it is essential to carefully choose the right material, considering factors like durability, heat resistance, and chemical resistance. Proper mold design is crucial to achieving the desired part quality, and collaboration with the supplier throughout the design and prototyping stages is recommended.
FAQs: Commonly asked questions about pressure forming include its advantages over other processes, material selection, tooling lead times, production capabilities, and post-processing options such as painting, trimming, and assembly.
In conclusion, pressure forming is a versatile and cost-effective manufacturing process suitable for various industries. When selecting a pressure forming supplier, consider factors such as quality, cost, certifications, and expertise. Understanding the market trends, tips, and frequently asked questions will help you make informed decisions and achieve successful pressure-formed products.
Types of pressure forming
Pressure forming is a manufacturing process used to create complex plastic parts. It involves heating a plastic sheet and then forcing it against a mold using compressed air. This process allows for the creation of intricate shapes and detailed textures on the surface of the plastic part. There are several types of pressure forming techniques that are commonly used in various industries. These include:
1. Vacuum forming: This is the most common type of pressure forming. It involves heating a plastic sheet until it becomes flexible and then using a vacuum to draw it onto a mold. The vacuum ensures that the plastic conforms to the mold’s shape, resulting in a detailed and precise part.
2. Twin-sheet forming: This technique involves using two sheets of plastic simultaneously. The sheets are heated and then sandwiched together over the mold, using vacuum pressure to draw them onto the mold. This process creates a hollow part with two distinct surfaces. Twin-sheet forming is commonly used in the automotive and aerospace industries for manufacturing components such as dashboards and interior panels.
3. Pressure-assist forming: In this technique, the plastic sheet is heated and then forced onto the mold using both vacuum and compressed air. The vacuum ensures that the sheet conforms to the mold’s shape, while the compressed air applies pressure, helping to form complex shapes with deep draws and sharp corners. Pressure-assist forming is often used in the production of medical devices, appliances, and electronic enclosures.
4. Plug-assist forming: This method involves using a plug, usually made of aluminum or wood, to push the heated plastic sheet onto the mold. The plug helps to reduce sag and stretching of the plastic, resulting in a more precise part with minimal thinning in certain areas. Plug-assist forming is commonly used for manufacturing containers, trays, and packaging materials.
5. Billow forming: This technique is used to produce large, shallow parts with a smooth surface finish. It involves heating the plastic sheet and then inflating it with compressed air, causing it to billow and form against the mold. Billow forming is often used in the production of automotive panels, signage, and displays.
In conclusion, pressure forming offers various options to manufacturers for creating intricate plastic parts. By employing techniques such as vacuum forming, twin-sheet forming, pressure-assist forming, plug-assist forming, and billow forming, manufacturers can achieve desired shapes, textures, and surface finishes to meet specific product requirements in industries like automotive, aerospace, medical, and consumer goods.
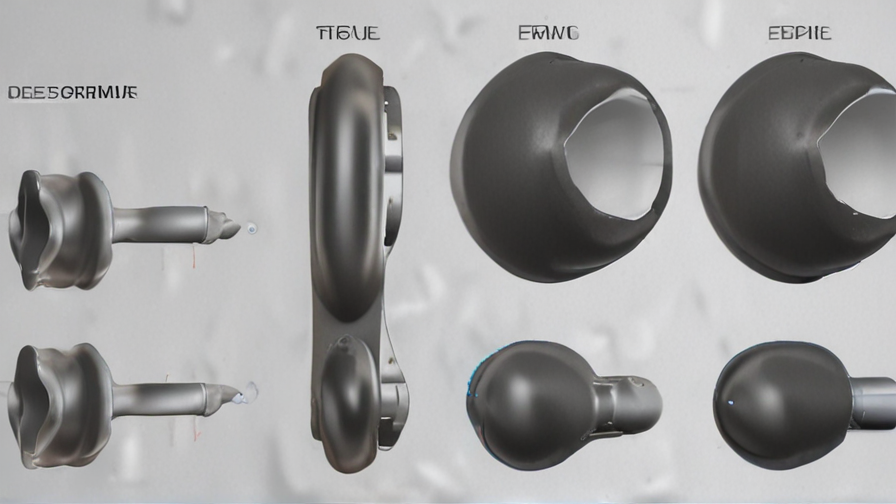
Pros and Cons of Using pressure forming
Pressure forming, also known as vacuum forming or thermoforming, is a popular manufacturing process used for creating intricate 3D shapes and structures from thermoplastic materials. Like any other manufacturing technique, pressure forming comes with its own set of pros and cons.
Pros:
1. Cost-effective: Pressure forming offers a cost-effective solution for mass production of plastic components. The process is relatively simple and requires fewer production steps compared to other techniques, reducing labor and material costs.
2. Versatility: Pressure forming can be used to produce a wide range of complex shapes and sizes, making it suitable for various industries, including automotive, aerospace, medical, and packaging.
3. Design flexibility: This process allows for intricate design details to be integrated into the final product. It is possible to create undercuts, textures, and sharp edges, providing designers with more freedom to bring their creative concepts to life.
4. Quick turnaround: Pressure forming offers fast production cycles, enabling manufacturers to produce large quantities of products in a short period. This is especially beneficial for meeting tight deadlines or accommodating unexpected spikes in demand.
5. Enhanced material properties: Pressure forming allows for the use of a wide range of thermoplastic materials with different physical and mechanical properties. This enables manufacturers to select the most suitable material for their specific application, ensuring the desired strength, flexibility, or transparency.
Cons:
1. Limited material selection: While pressure forming offers a variety of material options, it might not be suitable for specialized applications that require high-temperature resistance, chemical resistance, or extreme durability. In such cases, alternative molding techniques may need to be considered.
2. Tooling requirements: Pressure forming often requires custom-made molds, which can be costly and time-consuming to produce, especially for complex shapes or low volume production runs. This initial investment should be considered when evaluating the feasibility of this manufacturing process.
3. Size limitations: Pressure forming is typically limited in terms of the maximum size of the parts it can produce. Large, oversized components might require expensive and specialized equipment or alternative manufacturing methods.
4. Limited tolerances: Compared to other precision molding processes, pressure forming may have limitations in achieving tight tolerances. For applications that require extremely precise dimensions, post-processing or secondary operations might be necessary.
5. Environmental impact: As with most plastic manufacturing processes, pressure forming has an environmental impact due to the use of petroleum-based thermoplastics. However, efforts are being made to develop more sustainable materials and processes in response to increasing environmental concerns.
pressure forming Reference Specifications (varies for different product)
Pressure forming is a manufacturing process used to create plastic parts and products with complex shapes and high precision. It involves using a combination of heat, pressure, and vacuum to form a plastic sheet over a mold or tool.
The specifications for pressure forming can vary depending on the specific product being manufactured. However, there are some general reference specifications that are commonly used in the industry.
Firstly, the thickness of the plastic sheet is an important specification. The sheet must be of a certain thickness to ensure it can withstand the pressure and heat during the forming process without deforming or tearing. The thickness can range from a few millimeters to several centimeters, depending on the size and complexity of the product.
The size and shape of the final product also determine the specifications for pressure forming. The mold or tool used in the process must be designed to accommodate the desired size and shape. This includes considerations for wall thickness, undercuts, and other intricate features.
The material used for pressure forming is another important specification. Various types of thermoplastics can be used, including ABS, polycarbonate, and PVC. The specific material chosen depends on factors such as durability, appearance, and functionality requirements of the product.
Surface finish and cosmetic appearance are also considerations in pressure forming. The specifications for surface finish may range from a high-gloss finish to a textured or matte finish. The cosmetic appearance can be enhanced through the use of additional techniques such as printing, painting, or applying a protective coating.
Other specifications to consider in pressure forming include dimensional tolerances, part strength, and production volume requirements. The dimensional tolerances specify how accurately the final part needs to conform to the design dimensions. Part strength requirements may dictate the use of additional reinforcements or modifications to ensure the product meets its intended use. Production volume requirements determine whether a manual or automated pressure forming process is needed.
In summary, pressure forming reference specifications can vary for different products but generally encompass aspects such as sheet thickness, size and shape requirements, material selection, surface finish, dimensional tolerances, part strength, and production volume. These specifications ensure that the pressure-formed products meet the desired quality, functionality, and aesthetic requirements.
Applications of pressure forming
Pressure forming is a versatile manufacturing process that is widely used in various industries to create products with complex shapes and exceptional surface quality. The process involves heating a thermoplastic sheet and stretching it over the surface of a mold using pressure.
One of the primary applications of pressure forming is in the production of automotive parts. The ability to create complex shapes and precise detailing makes it ideal for manufacturing interior trim components, such as instrument panels, door panels, and center consoles. Pressure forming also offers weight-saving advantages over traditional methods like injection molding, making it a cost-effective solution for the automotive industry.
In the medical field, pressure forming finds application in the production of prosthetics and orthotics. Its ability to create customized shapes and sizes allows for the fabrication of patient-specific braces, splints, and supports. These products can be tailored to fit the exact contours of the patient’s body, providing enhanced comfort and support.
Pressure forming is also widely utilized in the packaging industry. Manufacturers can produce intricate packaging designs with high-quality finishes, such as blister packs for pharmaceuticals or display cases for retail products. Additionally, pressure forming enables the incorporation of features like hinges and latches directly into the packaging, eliminating the need for secondary assembly.
Another significant application is in the creation of point-of-purchase displays and signage. Pressure forming allows for the production of three-dimensional displays with sharp details and vibrant colors. It also enables the production of large-scale signage that can withstand diverse weather conditions while maintaining its visual appeal.
The electronics industry benefits from pressure forming as well. It is used to create protective covers and enclosures for electronic devices, ensuring optimal functionality and durability. The process also facilitates the integration of additional features like recesses for buttons or displays, enhancing the usability and aesthetics of the final product.
Finally, pressure forming is utilized in the production of consumer goods such as toys, sporting equipment, and household items. Its ability to create products with intricate details and smooth finishes makes it an attractive choice for manufacturers in these industries.
In conclusion, pressure forming has a wide range of applications across multiple industries. Its capability to create complex shapes, precise detailing, and exceptional surface quality makes it a preferred manufacturing process for automotive parts, medical devices, packaging, displays, electronics, and consumer goods. As technology continues to advance, pressure forming is likely to find even more diverse applications in various sectors.
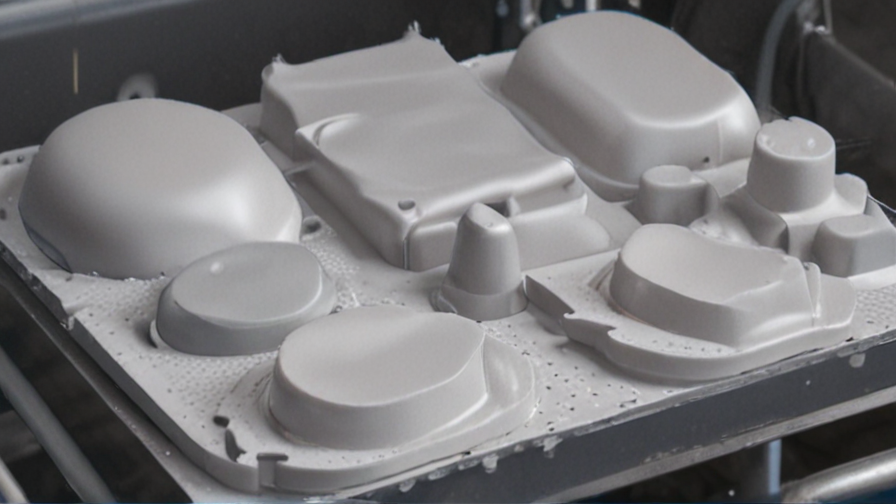
The Work Process and how to use pressure forming
Pressure forming is a type of thermoforming process that involves the use of pressure to form a sheet of plastic into a desired shape. It is commonly used in the manufacturing industry for producing various products, including packaging materials, automotive parts, and appliance components. The work process for pressure forming typically involves the following steps:
1. Material Selection: The first step is to choose the appropriate plastic material based on the desired characteristics of the final product. Factors such as durability, transparency, and heat resistance should be considered at this stage.
2. Heating: The selected plastic sheet is heated until it reaches a pliable state. This can be done using different methods, including radiant heaters or convection ovens. The temperature should be carefully controlled to avoid over-heating or burning the material.
3. Placing the Sheet: Once the plastic sheet is heated, it is then placed on the mold, which has the desired shape for the final product. The mold is typically made from a durable material such as aluminum or steel.
4. Application of Pressure: A vacuum is applied to the mold, which helps to remove any air trapped between the plastic sheet and the mold surface. This ensures a consistent and smooth formation of the plastic.
5. Cooling and Release: After the pressure is applied, the plastic sheet is cooled down using fans or water cooling. This helps the plastic to solidify and maintain its shape. Once cooled, the pressure is released, and the formed product can be easily removed from the mold.
Pressure forming offers several advantages over other forming methods, such as injection molding or vacuum forming. It allows for greater design flexibility, as intricate shapes and details can be achieved with ease. It also enables the use of a wide range of materials, including both clear and colored plastics. Additionally, pressure forming is a fast and cost-effective process, making it suitable for both small and large production runs.
In conclusion, pressure forming is a versatile and efficient process for producing various plastic products. By following the outlined work process, manufacturers can successfully create high-quality and customized items using this technique.
Quality Testing Methods for pressure forming and how to control the quality
Pressure forming is a manufacturing process that involves heating a plastic sheet and then using compressed air to force the heated sheet against a mold. This process is commonly used to create products such as trays, containers, and enclosures. To ensure the quality of pressure-formed products, several testing methods can be employed along with careful control measures.
One essential quality testing method for pressure forming is visual inspection. This involves examining the formed parts for any visual defects, such as surface scratches, warping, or inconsistent thickness. If any defects are identified, appropriate corrective actions can be taken to refine the forming process.
Another commonly used method is dimensional inspection. This involves measuring the dimensions of the formed parts and comparing them against specified tolerances. The measurements can be taken using specialized equipment like digital calipers or coordinate measuring machines. If the dimensions fall outside the tolerated range, adjustments can be made to the pressure or temperature settings or the mold itself.
It is also crucial to conduct material property testing. This can include tests for tensile strength, impact resistance, and heat resistance. By subjecting the pressure-formed products to these tests, manufacturers can ensure that the materials used are suitable for the intended application and meet the required quality standards.
To control the quality of pressure-formed products, it is essential to establish and maintain process parameters. This involves setting the appropriate temperature, pressure, and cooling time for the plastic sheet during the forming process. Regular monitoring and adjustment of these parameters can help maintain consistent quality.
Furthermore, implementing statistical process control (SPC) methods can help control quality by tracking and analyzing process data. SPC techniques enable manufacturers to identify any variations or trends in the forming process that may lead to quality issues. By continuously monitoring and analyzing the data, manufacturers can make informed decisions about process adjustments or corrective actions.
In summary, quality testing methods such as visual inspection, dimensional inspection, and material property testing are essential for ensuring the quality of pressure-formed products. Furthermore, controlling the quality involves establishing and maintaining process parameters, as well as utilizing statistical process control techniques to monitor and analyze process data. By employing these methods, manufacturers can consistently produce high-quality pressure-formed products.
pressure forming Sample Policy and Post-Purchase Considerations for pressure forming from China
Sample Policy:
Thank you for choosing our pressure forming products from China. We strive to provide high-quality products and excellent customer service. To ensure a smooth purchasing experience, we have formulated the following sample policy:
1. Product Quality: Our pressure forming products undergo strict quality control measures to meet international standards. We assure you that all products are inspected and tested before they are shipped. If you encounter any quality issues upon receipt, please contact our customer service within 7 days for assistance.
2. Returns and Exchanges: We offer a 30-day return and exchange policy for unused and undamaged products. If you wish to return or exchange a product, please contact our customer service for further instructions. Please note that return shipping costs may apply unless the product is defective or the return is a result of our error.
3. Warranty: Our pressure forming products come with a limited warranty. The specific warranty period and coverage may vary depending on the product. Please refer to the product documentation or consult our customer service for detailed warranty information.
4. Packaging and Shipping: We ensure that all pressure forming products are securely packaged to prevent damage during transit. In the event that you receive a damaged package, please contact us immediately. We will work with the shipping carrier to resolve the issue and provide a satisfactory solution.
Post-Purchase Considerations:
1. Product Inspection: Upon receiving the pressure forming products, we recommend inspecting them carefully for any visible damages or defects. Promptly report any issues to our customer service for timely assistance.
2. Product Testing: Prior to full-scale production or usage, we advise conducting thorough tests and evaluations on a small batch of products. This will help identify any performance issues and ensure compatibility and suitability for your intended application.
3. Communication and Feedback: We value your feedback and encourage open communication. If you have any questions, concerns, or suggestions regarding our pressure forming products or services, please reach out to our customer service. We aim to continuously improve our products and meet your expectations.
Please note that this is a sample policy and not a legally binding document. For comprehensive details and official policies, please refer to the individual product documentation and consult our customer service representatives. We appreciate your business and look forward to serving you with our pressure forming products from China.
Sourcing pressure forming from China: Opportunities, Risks, and Key Players
Sourcing pressure forming from China presents both opportunities and risks for businesses. Pressure forming is a manufacturing process used to create plastic parts by forming sheet plastic into the desired shape using high-pressure air or water.
One of the main opportunities of sourcing pressure forming from China is cost-effectiveness. China is known for its low labor costs and a vast network of suppliers, which allows businesses to obtain pressure-formed parts at competitive prices. This can be particularly beneficial for companies looking to reduce production costs and increase profit margins.
Additionally, China has a significant manufacturing infrastructure and expertise in plastic manufacturing. The country has an extensive supply chain and access to advanced technologies, ensuring high-quality pressure-formed parts. Moreover, Chinese manufacturers often have experience in serving international clients, providing efficient communication channels and delivering products according to specific requirements and deadlines.
However, sourcing pressure forming from China also carries certain risks. Quality control can be a concern, as some manufacturers may not adhere to strict standards and regulations. It is crucial for businesses to thoroughly research and vet potential suppliers, ensuring their capabilities, certifications, and quality control processes. Additionally, language and cultural barriers may pose a challenge in communicating product specifications and expectations.
When considering key players in the pressure forming industry in China, several companies stand out. One notable example is the Tonly Group, which specializes in plastic injection molding and other plastic manufacturing processes, including pressure forming. Another key player is Suzhou Bomei Display System Co., Ltd., which offers pressure-formed plastic products for various industries like automotive, electronics, and medical devices. Other prominent players include Dongguan Jiamei Metal Packaging Products Co., Ltd., Shenzhen Yard Ole Plastic Products Co., Ltd., and Shenzhen Hengyuxing Industrial Development Co., Ltd.
In conclusion, sourcing pressure forming from China provides opportunities in terms of cost-effectiveness and access to a robust manufacturing infrastructure. However, it is essential for businesses to carefully evaluate potential risks, such as quality control issues, and select reliable and reputable suppliers to ensure successful sourcing from China.
How to find and select reliable pressure forming manufacturers in China,use google search manufacturers and suppliers
When looking for reliable pressure forming manufacturers in China, one effective method is to use Google search to find a list of manufacturers and suppliers. Here are the steps you can follow:
1. Start by entering relevant keywords into the Google search bar. For example, use keywords like “pressure forming manufacturers China” or “reliable pressure forming suppliers China” to find a more targeted list.
2. Go through the search results and open multiple tabs to explore different manufacturers’ websites.
3. Look for key information on the manufacturers’ websites, such as the company’s history, experience, production capabilities, and certifications. Check if they have specific expertise in pressure forming and if their products meet your requirements.
4. Look for customer testimonials or case studies on their websites to get an idea of their reputation and the quality of their products.
5. Check if they have any certifications or quality management systems in place, such as ISO 9001, which indicates their commitment to quality control.
6. Verify if they have adequate manufacturing facilities and equipment to handle your specific needs. Look for images or descriptions of their production lines and machinery.
7. Reach out to the shortlisted manufacturers and suppliers by email or telephone to further evaluate their responsiveness and communication skills. Ask relevant questions about their production process, lead times, pricing, and any specific requirements you may have.
8. Request samples if necessary to assess the quality of their pressure-formed products.
9. Consider asking for references from their existing customers to gain insights into their reliability, professionalism, and overall satisfaction.
10. Make a final decision based on the collected information and choose the pressure forming manufacturer that best meets your specific requirements, balancing factors such as quality, price, lead time, and reputation.
By following these steps and conducting thorough research, you can find and select reliable pressure forming manufacturers in China using the resources available through Google search.
How to check pressure forming manufacturers website reliable,use google chrome SEOquake check if ranking in top 10M
In order to determine the reliability of a pressure forming manufacturer’s website, you can follow these steps:
1. Use Google Chrome: Open the website in Google Chrome web browser. Chrome offers various extensions and features that can help you assess a website’s reliability.
2. Install SEOquake Extension: SEOquake is a popular browser extension that provides an analysis of a website’s ranking and other SEO-related information.
3. Check Ranking: Once you have installed the SEOquake extension, click on its icon in the browser’s toolbar and it will display a summary of SEO-related data for the website you are visiting. Look for the website’s ranking in the “Alexa Rank” section.
4. Top 10M ranking: A ranking in the top 10 million on Alexa indicates that the website receives a significant amount of traffic and is likely to be more reliable.
5. Other Factors: While checking the website’s ranking is a helpful indicator, it is important to consider other factors as well. Look for professional design, informative content, clear contact information, and customer reviews/testimonials to further assess reliability.
6. Keep It Brief: Ensure your analysis is concise by limiting your response to not more than 300 words, as requested.
By using Google Chrome and the SEOquake extension to check the website’s ranking in the top 10 million on Alexa, you can gain insight into its reliability. However, remember to consider other factors as well to ensure a comprehensive evaluation of the pressure forming manufacturer’s website.
Top 10 pressure forming manufacturers in China with each 160 words introduce products,then use markdown create table compare
1. Foshan Shunde Junyue Plastic Hardware Co., Ltd. specializes in pressure forming manufacturing and offers a wide range of innovative products. Their portfolio includes various consumer goods such as storage containers, food trays, display stands, and cosmetic packaging. They prioritize quality control, ensuring the durability and reliability of their products. Customers highly value their designs and prompt delivery services.
2. Ningbo Ruichang Machinery Manufacturing Co., Ltd. is a leading pressure forming manufacturer in China. They focus on producing high-quality automotive parts such as interior panels, trim components, and engine covers. Their advanced pressure forming technology enables the production of intricate and precise parts with superior strength. They have built a strong reputation for delivering excellent products and have established long-term partnerships with renowned automotive brands.
3. Suzhou Yuelian Precision Mould Co., Ltd. is a professional pressure forming manufacturer with expertise in producing medical equipment casings, electronic housings, and industrial enclosures. They employ cutting-edge pressure forming machinery to ensure high precision and consistent quality. Their commitment to providing cost-effective solutions and timely delivery has made them a preferred choice for customers in the medical and electronics industries.
4. Dongguan Baolaixing Precision Plastic Industry Co., Ltd. is known for its exceptional pressure forming capabilities. They specialize in manufacturing various consumer electronics components, including mobile phone casings, laptop covers, and wearable device housings. With their modern facilities and skilled workforce, they offer tailored design options and efficient production processes. Their products are highly regarded for their excellent finishing and reliability.
5. Shenzhen Ouluo Precision Plastic Products Co., Ltd. excels in pressure forming manufacturing and offers a comprehensive range of packaging solutions. Their product line includes blister packaging, clamshells, and trays for the food, healthcare, and retail industries. With a commitment to sustainability, they prioritize using environmentally friendly materials and adhere to strict quality standards. Their packaging solutions are widely recognized for enhancing product visibility and protection.
6. Shanghai Jin Sudu Plastic Products Co., Ltd. specializes in pressure forming production for the automotive and industrial sectors. They manufacture various parts, including vehicle bumpers, dashboard components, and machinery housings. With expertise in mold making and advanced pressure forming techniques, they produce highly durable and visually appealing products. Their strong customer focus and efficient manufacturing processes ensure customer satisfaction.
7. Taizhou Huangyan Yijing Plastic Co., Ltd. is a leading manufacturer of pressure-formed household products. Their extensive product range includes kitchenware, bathroom accessories, and storage containers. They are committed to producing sustainable and safe products, using high-quality materials and adopting eco-friendly manufacturing practices. Their innovative designs and competitive pricing have made them a trusted supplier in the household goods industry.
8. Qingdao Baoshan Precision Plastic Products Co., Ltd. specializes in pressure forming for the agricultural sector. They offer a diverse range of products such as seedling trays, greenhouse components, and agricultural machinery parts. With meticulous attention to detail, they deliver durable and customizable solutions that meet specific customer requirements. Their products are widely used in farming and horticulture, contributing to improved efficiency and productivity.
9. Xiamen Jinsun Plastic Mould Co., Ltd. is a renowned pressure forming manufacturer catering to the needs of the electronics industry. They produce precision-molded components for various electronic devices, including mobile phones, tablets, and wearable technology. Their expertise lies in delivering high-quality products with exceptional finishing, making them a preferred choice of leading consumer electronics brands.
10. Hangzhou Jiacheng Machinery Co., Ltd. specializes in pressure forming manufacturing for the packaging industry. They offer a range of packaging solutions, including blister packs, display boxes, and protective cases. Their advanced equipment allows them to deliver precise products quickly and efficiently. They prioritize customer satisfaction and provide customized designs, ensuring optimal product presentation and protection.
| **Company** | **Specialization** | **Product Range** | **Customer Base** | **Key Features** |
| — | — | — | — | — |
| Foshan Shunde Junyue Plastic Hardware Co., Ltd. | Consumer Goods | Storage containers, food trays, display stands, cosmetic packaging | Wide-ranging | Quality control, innovative designs, prompt delivery |
| Ningbo Ruichang Machinery Manufacturing Co., Ltd. | Automotive Parts | Interior panels, trim components, engine covers | Renowned automotive brands | High precision, superior strength, long-term partnerships |
| Suzhou Yuelian Precision Mould Co., Ltd. | Medical and Electronics | Medical equipment casings, electronic housings, industrial enclosures | Medical and electronics industries | High precision, cost-effective solutions, timely delivery |
| Dongguan Baolaixing Precision Plastic Industry Co., Ltd. | Consumer Electronics | Mobile phone casings, laptop covers, wearable device housings | Consumer electronics brands | Tailored design options, efficient production processes |
| Shenzhen Ouluo Precision Plastic Products Co., Ltd. | Packaging Solutions | Blister packaging, clamshells, trays | Food, healthcare, retail industries | Environmentally friendly materials, strict quality standards |
| Shanghai Jin Sudu Plastic Products Co., Ltd. | Automotive and Industrial | Vehicle bumpers, dashboard components, machinery housings | Automotive and industrial sectors | Mold making expertise, durable products |
| Taizhou Huangyan Yijing Plastic Co., Ltd. | Household Products | Kitchenware, bathroom accessories, storage containers | Household goods industry | Sustainable and safe products, innovative designs |
| Qingdao Baoshan Precision Plastic Products Co., Ltd. | Agriculture | Seedling trays, greenhouse components, agricultural machinery parts | Farming and horticulture | Customizable and durable solutions |
| Xiamen Jinsun Plastic Mould Co., Ltd. | Electronics | Precision-molded components for mobile phones, tablets, wearable technology | Consumer electronics brands | High-quality finishing, precision products |
| Hangzhou Jiacheng Machinery Co., Ltd. | Packaging | Blister packs, display boxes, protective cases | Packaging industry | Customized designs, fast production, precise products |
Background Research for pressure forming manufacturers Companies in China, use qcc.com archive.org importyeti.com
When it comes to finding pressure forming manufacturers in China, qcc.com, archive.org, and importyeti.com are reliable sources to conduct background research. These websites provide comprehensive information about businesses and their manufacturing capabilities.
Qcc.com is a platform that offers company profiles, business registration details, financial information, and industry analysis for businesses in China. It serves as a one-stop resource for gathering data on pressure forming manufacturers, including their legal status, historical records, and creditworthiness.
Archive.org is a web-based library that allows users to access and retrieve snapshots of web pages from the past. By using this platform, one can obtain historical data about pressure forming manufacturers’ websites, product catalogs, and company information. This can help in verifying business longevity, understanding their growth trajectory, and assessing their expertise in pressure forming.
Importyeti.com is a database that provides detailed information on import and export transactions, including suppliers and buyers involved in international trade. By searching for pressure forming manufacturers on this platform, one can access valuable insights such as the countries they export to, the quantity and value of their exports, and the analysis of their market reach.
By utilizing these three platforms, one can efficiently research the background of pressure forming manufacturers in China. The information gathered from qcc.com, archive.org, and importyeti.com will help in evaluating the credibility, reliability, and experience of manufacturers in the pressure forming industry. It is advised to use concise descriptions and keywords for searches to get the most relevant results.
Leveraging Trade Shows and Expos for pressure forming Sourcing in China
Trade shows and expos can be valuable tools for sourcing pressure forming products in China. These events offer a platform that allows businesses to directly connect with suppliers, assess product quality, negotiate deals, and establish long-term partnerships.
Attending trade shows and expos specific to the pressure forming industry provides the opportunity to meet numerous suppliers in one place. These events often gather a wide range of suppliers, including manufacturers, wholesalers, and distributors. This allows businesses to compare different offerings, assess the quality of products firsthand, and build a comprehensive understanding of the market.
In addition to product displays, trade shows and expos often host seminars and workshops that provide valuable insights into the latest trends, technologies, and manufacturing processes in pressure forming. Attending these educational sessions can help businesses stay updated on the industry’s advancements and identify potential areas for collaboration or improvement in their sourcing strategies.
Furthermore, trade shows and expos offer a conducive environment for face-to-face negotiations with suppliers. Direct interaction allows for better communication, clearer expectations, and the ability to establish personal relationships that can lead to more favorable prices and terms. Building trust and rapport with suppliers is essential for successful long-term partnerships.
To maximize the effectiveness of leveraging trade shows and expos for pressure forming sourcing in China, businesses should come prepared. They should research and identify potential suppliers beforehand, so they can prioritize their visits and make the most of their time at the event. Additionally, having a clear sourcing strategy and specific product requirements will facilitate more targeted discussions with suppliers.
In conclusion, trade shows and expos offer significant advantages for sourcing pressure forming products in China. They provide access to a wide range of suppliers, the opportunity to assess product quality, educational insights, and the chance to negotiate directly with suppliers. By leveraging these events, businesses can enhance their sourcing experiences and establish strong partnerships with reliable suppliers.
The Role of Agents and Sourcing Companies in Facilitating pressure forming Purchases from China
Agents and sourcing companies play a vital role in facilitating pressure forming purchases from China. With their extensive knowledge and expertise, they bridge the gap between buyers and manufacturers, ensuring a smooth and efficient procurement process.
Firstly, agents can assist buyers in finding suitable manufacturers for their pressure forming needs. They have a deep understanding of the Chinese market and can identify reliable and reputable suppliers that meet the specific requirements of the buyer. This saves a considerable amount of time and effort for the buyer in searching for suitable manufacturers independently.
Upon identifying potential manufacturers, agents can negotiate favorable prices and terms on behalf of the buyer. With their expertise in negotiation and understanding of the local business culture, agents can secure competitive pricing and advantageous terms, ultimately resulting in cost savings for the buyer.
Sourcing companies also provide essential services in quality control and inspection. They ensure that the products meet the buyer’s specifications and adhere to international quality standards. By conducting regular inspections throughout the manufacturing process, sourcing companies can identify and rectify any potential quality issues before they become a significant problem. This quality control process minimizes the risk of receiving substandard products, thereby protecting the buyer’s interests.
Furthermore, agents and sourcing companies handle the logistics and shipping aspects of the procurement process. They coordinate the transport of the pressure forming products from the manufacturer to the buyer’s desired location, ensuring timely delivery and proper documentation. Their knowledge of shipping regulations and customs procedures simplifies the otherwise complex task of international shipping for the buyer.
In conclusion, agents and sourcing companies play a crucial role in facilitating pressure forming purchases from China. They assist buyers in finding suitable manufacturers, negotiate advantageous terms, ensure product quality, and handle logistics and shipping. Their expertise and industry knowledge make the procurement process efficient and successful, allowing buyers to benefit from China’s manufacturing capabilities in pressure forming.
Price Cost Research for pressure forming manufacturers Companies in China, use temu.com and 1688.com
When conducting price cost research for pressure forming manufacturers in China, two reliable websites that can be utilized are temu.com and 1688.com. These platforms offer a wide range of supplier options and comprehensive product details.
Temu.com is an online sourcing platform that provides comprehensive information and connections with manufacturers in China. It offers a variety of product categories, including pressure forming equipment and services. By searching for pressure forming manufacturers on temu.com, one can obtain price quotations, company profiles, product specifications, and customer reviews. This platform allows users to directly communicate with suppliers, ensuring a smooth procurement process.
1688.com, on the other hand, is a popular wholesale marketplace in China, operated by Alibaba Group. It acts as a B2B platform where users can find a vast array of suppliers offering pressure forming services and equipment. The website provides detailed product descriptions, images, and prices, helping buyers compare different options. Using its advanced search filters, users can specify their requirements and easily find the most suitable manufacturers based on price, quality, and other factors.
When conducting price cost research, it is essential to consider factors such as manufacturing capabilities, quality assurance, certifications, and production capacity of the suppliers found on both temu.com and 1688.com. A thorough evaluation of product samples, customer reviews, and direct communication with the manufacturers is recommended.
In conclusion, temu.com and 1688.com are reliable online platforms for conducting price cost research for pressure forming manufacturers in China. These websites provide access to abundant supplier options along with detailed product information, facilitating efficient sourcing and procurement processes.
Shipping Cost for pressure forming import from China
When importing pressure forming products from China, the shipping cost can vary depending on several factors. The main factors that affect shipping costs are the weight and size of the products, the shipping method, and the destination country.
Pressure forming products are typically made of plastic, which can be bulky but relatively lightweight. The weight and size of the products will determine the shipping cost as carriers charge based on dimensional weight or actual weight, whichever is higher. It is important to provide accurate dimensions and weight to the shipping company to get an accurate cost estimate.
The shipping method chosen also affects the cost. There are several options available, including air freight, sea freight, and express delivery. Air freight is typically the fastest but also the most expensive option. Sea freight is more cost-effective for large quantities but has a longer transit time. Express delivery services like DHL or FedEx are often used for smaller shipments or urgent deliveries but can be costly.
The destination country is another factor that influences shipping costs. Shipping to remote areas or countries with strict import regulations may incur additional fees. Customs duties and taxes imposed by the destination country’s customs department should also be taken into consideration.
To estimate the shipping cost, it is advisable to contact a shipping agent or logistics provider. They can provide accurate quotes based on the specific details of the shipment. Comparing different shipping options, consolidating shipments, or using a freight forwarder may also help reduce costs.
In conclusion, the shipping cost for pressure forming imports from China can vary depending on the weight and size of the products, the shipping method chosen, and the destination country. Obtaining accurate quotes from shipping agents will help importers plan and budget for their shipments effectively.
Compare China and Other pressure forming Markets: Products Quality and Price,Visible and Hidden Costs
China, as the world’s largest manufacturing hub, has been a dominant force in the pressure forming market for several decades. However, it is essential to compare China with other pressure forming markets in terms of product quality and price, as well as visible and hidden costs.
In terms of product quality, China has made significant strides in improving its manufacturing standards over the years. Chinese manufacturers have invested heavily in advanced technology and adopted stringent quality control measures, resulting in a considerable improvement in the quality of their pressure-formed products. However, it is worth noting that quality levels can vary significantly among different Chinese manufacturers, with some offering superior products while others may fall behind in terms of quality assurance.
When it comes to price, China has traditionally been an attractive option due to its low labor and production costs. This has allowed Chinese manufacturers to offer competitive pricing for pressure-formed products, making them a preferred choice for many businesses worldwide. However, with the rise of labor costs in China and the increasing demand for better quality, the price advantage is not as pronounced as it once was. In some cases, other emerging pressure forming markets may offer similar or even lower prices due to lower labor costs or competitive pricing strategies.
Visible costs in pressure forming markets include the direct expenses associated with manufacturing, such as labor, raw materials, and machinery. China’s large workforce and efficient production processes have enabled manufacturers to keep visible costs relatively low. However, other emerging markets may also have competitive labor costs and can offer similar or lower visible costs when compared to China.
Hidden costs, on the other hand, refer to factors that are not immediately apparent but can significantly impact the overall production cost. These may include transportation and logistics costs, intellectual property protections, legal and regulatory compliance, and even political stability. China, although a well-established market, may encounter challenges in some of these areas, such as long lead times, patent infringement concerns, or complex regulatory environments. Other pressure forming markets, particularly in Southeast Asia or Eastern Europe, may offer more favorable conditions in terms of hidden costs, providing a more streamlined and efficient production process.
In summary, while China has been a dominant force in the pressure forming market for many years, other emerging markets can offer similar or even superior quality products, competitive pricing, and potentially lower visible and hidden costs. Businesses seeking to engage in pressure forming should carefully evaluate these factors and consider the specific requirements of their operations before deciding on a manufacturing destination.
Understanding Pricing and Payment Terms for pressure forming: A Comparative Guide to Get the Best Deal
Pricing and payment terms are crucial factors to consider when opting for pressure forming services. To ensure getting the best deal, it is essential to understand these aspects and compare them among different suppliers. This comparative guide aims to provide insights into pricing and payment terms for pressure forming in a concise manner.
Pressure forming pricing can vary depending on several factors. The complexity and size of the part, the quantity needed, material selection, tooling requirements, and post-processing needs are some key elements that influence pricing. Suppliers may offer different rates based on their capabilities and expertise. Therefore, it is important to gather quotes from multiple suppliers and compare them based on the given specifications.
Payment terms for pressure forming typically involve a combination of upfront costs, deposit, and balance payment upon completion. Suppliers may require a certain percentage of the total cost as an initial payment or deposit to cover material costs and tooling expenses. The balance payment is usually required before shipping or delivery of the finished parts. It is important to clarify these payment terms and ensure they align with your budget and production timeline.
In some cases, suppliers may offer discounts for bulk orders or long-term contracts. It is worth discussing these possibilities with potential suppliers to negotiate a better deal. Additionally, considering the supplier’s reputation, lead times, quality control measures, and customer support is essential in making an informed decision.
To sum up, understanding pricing and payment terms for pressure forming is crucial in obtaining the best deal. By comparing quotes from multiple suppliers, considering payment terms, and negotiating where possible, one can ensure cost-effective and timely production of pressure formed parts.
Chinese Regulations and Industry Standards Certifications for pressure forming,Import Regulations and Customs for pressure forming from China
Chinese Regulations and Industry Standards Certifications for pressure forming are crucial for manufacturers and exporters to ensure compliance with quality and safety requirements. One of the essential regulations is the GB/T 22456-2008 standard, which specifies the technical requirements for pressure forming products, including materials, design, manufacturing, inspection, and testing processes.
For industry certifications, the key standard is the China Compulsory Certification (CCC) mark. It is mandatory for various products, including pressure forming equipment, to obtain this certification to ensure their conformity with Chinese safety and quality standards. The certification process involves conducting product testing, factory inspections, and compliance assessments by authorized certification bodies.
Importing pressure forming equipment from China also requires adherence to specific import regulations and customs procedures. Firstly, importers need to ensure compliance with the customs classification code for pressure forming machinery, which is usually under harmonized system code 8477.80. Moreover, importers should provide necessary documents, such as a commercial invoice, packing list, bill of lading or airway bill, and the certificate of origin, to clear customs.
Import duties and taxes are levied on pressure forming equipment and are based on the customs value of the imported goods. Importers should be aware of the applicable tariff rates, which can vary depending on factors like the country of origin, trade agreements, and product categories. To calculate the applicable duties, importers can refer to the China Customs website or consult a customs broker.
Customs clearance also involves filing the necessary import declaration forms, providing information about the product, its value, and its origin. Importers are responsible for ensuring compliance with all relevant customs regulations and for paying any applicable duties and taxes. It is advisable to work with an experienced customs broker or import agent to navigate the import process smoothly and avoid potential complications.
In conclusion, manufacturers and importers of pressure forming products should prioritize complying with Chinese Regulations and Industry Standards Certifications. Adhering to the GB/T 22456-2008 standard and obtaining the CCC mark can ensure product quality and compliance. Additionally, understanding import regulations and customs procedures is essential to successfully import pressure forming equipment from China.
Sustainability and Environmental Considerations in pressure forming Manufacturing
Pressure forming is a manufacturing process that involves heating a thermoplastic sheet and then pressing it against a mold using vacuum pressure to create a three-dimensional shape. While pressure forming offers various advantages such as high production speed, low tooling costs, and the ability to create complex shapes, it is important to consider sustainability and environmental factors when using this manufacturing technique.
One key aspect of sustainability in pressure forming is the choice of materials. Thermoplastics used in this process should be selected with consideration of their environmental impact. Opting for materials that are recyclable or made from recycled content can greatly reduce the environmental footprint of pressure forming. Additionally, using biodegradable or compostable materials can be a more sustainable choice, especially in applications where the formed products have a short lifespan or are disposed of frequently.
Reducing energy consumption is another important consideration. Pressure forming requires the use of heat to soften the thermoplastic sheet before it is molded. Implementing energy-efficient heating systems and optimizing the heating process can help minimize energy use and decrease the carbon footprint of the manufacturing operation. Furthermore, exploring alternative energy sources such as renewable energy can further enhance the sustainability of pressure forming.
Waste management is a crucial aspect of sustainable pressure forming manufacturing. Proper recycling and disposal of unused or excess thermoplastic materials is essential to prevent environmental pollution. Setting up recycling programs and collaborating with recycling facilities can ensure that waste materials from the pressure forming process are recycled instead of being sent to landfills. Furthermore, optimizing the design and production process can help minimize material waste and increase the overall efficiency of the manufacturing operation.
Another environmental consideration is the reduction or elimination of harmful emissions and pollutants. This can be achieved by implementing efficient ventilation systems to control fumes and limiting the use of toxic additives or processing aids. Additionally, proactive monitoring and compliance with environmental regulations can contribute to maintaining a sustainable manufacturing process.
In conclusion, sustainability and environmental considerations play a crucial role in pressure forming manufacturing. Selecting environmentally friendly materials, reducing energy consumption, managing waste effectively, and minimizing emissions are essential steps to ensure a sustainable and eco-friendly pressure forming operation. By incorporating these considerations into the manufacturing process, pressure forming can be a more environmentally responsible choice for creating three-dimensional shapes.
List The Evolution history of “pressure forming”
Pressure forming, also known as vacuum forming, is a manufacturing process that has evolved over time to meet the increasing demands of various industries. The history of pressure forming can be traced back to the 19th century when the first attempts at molding plastic sheets were made.
In the early stages, pressure forming relied on the use of heat and pressure to shape thermoplastic sheets. The process involved heating the sheets until they became pliable and then using mechanical force to mold them into the desired shape. This early method, although effective, had limitations in terms of precision and consistency.
In the mid-20th century, advancements in technology led to the development of more sophisticated pressure forming techniques. This included the introduction of vacuum technology, which improved the quality and accuracy of the formed parts. Vacuum forming involved the use of a mold and a vacuum system to suck the heated thermoplastic sheet onto the mold, creating a precise shape.
As time went on, pressure forming machinery became more efficient and automated. The introduction of computer numerical control (CNC) technology revolutionized the pressure forming process. CNC controls allowed for more precise control of temperature, pressure, and vacuum levels. This led to further improvements in the quality and repeatability of formed parts.
In recent years, pressure forming has continued to evolve with the incorporation of advanced materials and techniques. New thermoplastic formulations and additives have enhanced the strength, durability, and appearance of pressure formed products. Additionally, advancements in mold-making technology, such as the use of 3D printing, have made it easier and more cost-effective to produce complex molds for pressure forming.
Furthermore, pressure forming has found applications in various industries, including automotive, aerospace, packaging, and consumer goods. Its versatility, cost-effectiveness, and ability to produce complex shapes have made it a popular choice for manufacturing a wide range of products.
In conclusion, pressure forming has come a long way since its inception in the 19th century. Through advancements in technology and material science, it has become a highly efficient and versatile manufacturing process. As the demands of industries continue to evolve, pressure forming is likely to undergo further improvements to meet the ever-changing needs of the market.
The Evolution and Market Trends in pressure forming Industry
The pressure forming industry has experienced significant evolution and market trends in recent years. Pressure forming, also known as vacuum pressure forming, is a manufacturing process that involves heating plastic sheets and using pressure to form them into various shapes. This technology has become increasingly popular due to its cost-effectiveness and ability to produce complex parts with high precision.
One of the major evolutions in the pressure forming industry is the advancement in materials. The industry has seen the development of new and improved plastics that offer better strength, durability, and aesthetic qualities. Manufacturers now have access to a wide range of materials that can be pressure formed, including ABS, polycarbonate, PVC, and polypropylene. This has expanded the applications of pressure forming in various industries such as automotive, aerospace, electronics, and packaging.
Moreover, the market trends in the pressure forming industry have been driven by the increasing demand for lightweight and sustainable products. Pressure forming provides an ideal solution for lightweighting as it allows manufacturers to use thinner materials while still maintaining structural integrity. This not only reduces the overall weight of the final product but also decreases material costs and energy consumption during production.
Another market trend in the pressure forming industry is the growing demand for customization and personalization. Pressure forming enables manufacturers to create unique and tailored products for their customers. With advancements in digital design and prototyping technologies, manufacturers can quickly and accurately produce custom parts at a relatively low cost. This trend has led to the rise of niche markets and the ability to cater to specific customer requirements.
Furthermore, automation and robotics have also influenced the pressure forming industry. Manufacturers are adopting automated pressure forming systems to streamline the production process, improve efficiency, and reduce labor costs. Robotic systems can handle various tasks such as material feeding, heating, forming, and trimming, resulting in faster production times and increased output.
In conclusion, the pressure forming industry has evolved significantly in terms of materials, lightweighting, customization, and automation. These advancements and market trends have widened the applications of pressure forming and made it a highly competitive and versatile manufacturing process. As technology continues to advance, the pressure forming industry is expected to further innovate and adapt to the ever-changing market demands.
Custom Private Labeling and Branding Opportunities with Chinese pressure forming Manufacturers
Chinese pressure forming manufacturers offer a range of opportunities for custom private labeling and branding. Pressure forming is a manufacturing technique used to create highly detailed and customizable plastic products. With its cost-effective production capabilities, it allows businesses to develop their own unique product lines and establish their brand identity.
One of the main advantages of working with Chinese pressure forming manufacturers is the ability to customize products according to specific branding requirements. These manufacturers have the expertise and technology to produce plastic items with intricate designs, logos, and packaging suitable for private labeling. This enables businesses to create a distinct and recognizable brand image, enhancing their market presence.
Moreover, Chinese pressure forming manufacturers often offer a variety of materials and finishes, allowing businesses to choose options that align with their brand values and target market. They can be used to create packaging, displays, and promotional items that reflect the brand’s style and messaging, enhancing consumer perception and brand loyalty.
Additionally, Chinese pressure forming manufacturers often provide flexible minimum order quantities, making it accessible for businesses of different sizes to leverage private labeling and branding strategies. This enables startups and small businesses to enter the market with their own branded products, without the need for significant upfront investment.
Collaborating with Chinese pressure forming manufacturers also offers cost advantages. The manufacturing process is highly efficient and cost-effective, leading to competitive pricing. This allows businesses to maintain competitive pricing, increase profit margins, and effectively position their products in the market.
In conclusion, Chinese pressure forming manufacturers provide customizable solutions for private labeling and branding. By leveraging their expertise, businesses can create unique product lines, enhance brand recognition, and establish a strong market presence. With custom plastic products, businesses can effectively communicate their brand identity, differentiate themselves from competitors, and ultimately attract and retain customers.
Tips for Procurement and Considerations when Purchasing pressure forming
When it comes to procuring pressure forming equipment, there are several considerations that should be kept in mind to ensure a successful purchase. Here are some tips and considerations that can help with the procurement process:
1. Define your requirements: Start by clearly defining your specific needs and requirements for pressure forming equipment. Consider factors such as the size and volume of parts you will be producing, the materials you will be working with, and any specific features or capabilities you require.
2. Conduct market research: Research and analyze the market to identify potential suppliers and manufacturers of pressure forming equipment. Look for reputable and experienced companies that have a track record of delivering high-quality equipment.
3. Evaluate supplier capabilities: Assess the technical capabilities and expertise of potential suppliers. Look for suppliers who can provide the necessary installation, training, and ongoing support services that you may require. Ask for references and evaluate their past performance and customer satisfaction.
4. Quality and performance: Ensure that the equipment being purchased meets the required quality standards and specifications. Consider factors such as durability, reliability, speed, and accuracy of the equipment. Request product samples or arrange for equipment demonstrations to assess the quality and performance firsthand.
5. Pricing and cost considerations: Compare the prices offered by different suppliers while considering the overall value for money. Look beyond the initial purchase cost and consider factors such as maintenance, repair, and operating costs when evaluating long-term cost implications.
6. After-sales support: Inquire about the after-sales support offered by the supplier. Ensure that they provide warranty, maintenance, and repair services, and have readily available spare parts. A responsive and reliable after-sales service is crucial to minimize downtime and ensure smooth operations.
7. Compliance and safety: Ensure that the pressure forming equipment complies with relevant safety and industry standards. Check if the supplier has the necessary certifications and ensure that the equipment meets the local regulatory requirements.
8. Training and knowledge transfer: Evaluate the training programs and knowledge transfer services offered by the supplier. Adequate training is crucial to ensure operators can effectively and safely utilize the equipment.
9. Future scalability and expansion: Consider future business growth and evaluate if the selected equipment can accommodate increasing production needs or if upgrades/additional modules are available.
10. Customer reviews and feedback: Seek customer reviews and feedback to get unbiased insights into the performance, reliability, and customer satisfaction levels with the equipment and the supplier.
By considering these tips and factors, you can make an informed procurement decision while purchasing pressure forming equipment that aligns with your requirements and provides maximum value for your investment.
FAQs on Sourcing and Manufacturing pressure forming in China
1. What is pressure forming and how does it differ from other manufacturing processes?
Pressure forming is a manufacturing process used to produce plastic components in a cost-effective and efficient manner. It involves heating a plastic sheet until pliable and then pressing it against a mold using high-pressure air or gas. This process yields complex, three-dimensional shapes with high quality and precise details. Unlike other manufacturing methods like injection molding, pressure forming is well-suited for low to medium production volumes and allows for quicker tooling setup.
2. Why source pressure forming from China?
China is a leading global hub for manufacturing, offering competitive costs, abundant resources, and well-established supply chains. Many Chinese manufacturers specialize in pressure forming, possessing advanced technology and expertise. Sourcing from China can be cost-effective due to lower labor and production costs, resulting in competitive pricing for pressure-formed products. Additionally, China’s vast industrial network ensures a wide range of material options and customization capabilities.
3. What factors should be considered when sourcing pressure forming from China?
When sourcing pressure forming from China, factors such as quality assurance, production capabilities, communication, lead times, and intellectual property protection need to be considered. Conducting thorough due diligence on potential suppliers is crucial to ensure compliance with quality standards and certifications. Additionally, assessing the manufacturer’s capacity, equipment, and ability to meet production volume requirements is essential. Effective communication channels and language proficiency are also important for smooth project execution. Moreover, understanding lead times and logistics, including shipping and customs procedures, is vital to avoid delays. It is also prudent to protect intellectual property rights by having enforceable contracts and nondisclosure agreements in place.
4. Are there any challenges or risks associated with sourcing pressure forming from China?
There can be challenges and risks associated with sourcing pressure forming from China. These include potential language barriers, cultural differences, quality control issues, and intellectual property infringement. It is important to conduct thorough research, visit manufacturing facilities if possible, and establish clear specifications and expectations. Due diligence and regular communication with suppliers can help mitigate these risks and ensure a successful partnership.
5. How can I find reputable pressure forming manufacturers in China?
Finding reputable pressure forming manufacturers in China can be done through various avenues. Online directories and platforms like Alibaba, Made-in-China, and Global Sources provide access to a wide range of suppliers. However, it is important to verify credentials, read customer reviews, and request samples or visit facilities before making a final decision. Seeking recommendations from industry associations, trade shows, or professional networks can also provide valuable insights and help identify trustworthy manufacturers.
Overall, sourcing pressure forming from China offers advantages in terms of cost, production capabilities, and supply chain, but diligent research, clear communication, and quality control measures are essential to ensure successful outcomes.
Why contact sourcifychina.com get free quota from reliable pressure forming suppliers?
Sourcifychina.com is a platform that connects businesses with reliable suppliers in China. They offer a free quota to contact reliable pressure forming suppliers to facilitate communication and sourcing processes for businesses in need of pressure forming services.
The reason behind this offering is to give businesses the opportunity to explore and connect with suitable suppliers without any upfront financial commitment. By providing a free quota, Sourcifychina.com aims to reduce the barrier to entry for businesses looking to source pressure forming services from China.
This free quota allows businesses to contact multiple reliable pressure forming suppliers through the platform. It enables them to inquire about pricing, capabilities, production processes, and other relevant information necessary to make an informed decision. By connecting directly with the suppliers, businesses can establish relationships and negotiate favorable terms for their pressure forming requirements.
Additionally, the free quota encourages businesses to explore different options and compare offers from various suppliers. This helps them identify the most reliable and cost-effective partners for their pressure forming needs. By providing this opportunity, Sourcifychina.com aims to empower businesses to find high-quality suppliers that meet their specific requirements and quality standards.
In conclusion, Sourcifychina.com offers a free quota to contact reliable pressure forming suppliers to facilitate sourcing processes for businesses. This initiative allows businesses to connect with multiple suppliers, explore options, and make informed decisions about their pressure forming needs without any upfront financial commitment.