Analysis of Manufacturing Expenses for pump cost
Manufacturing expenses for pump cost can be broken down into several categories. The first and most obvious is the direct material cost, which includes all of the raw materials required to produce a pump. This may include metal, plastic, rubber, and other specialized materials, depending on the design and specifications of the pump. The cost of these materials can vary greatly depending on the quality, quantity, and location of the supplier.
The second category is the direct labor cost, which includes the wages and benefits paid to the workers involved in the manufacturing process, such as assembly, machining, and testing. Labor costs can vary greatly depending on the skill level and experience of the workers, as well as the location and availability of the workforce.
The third category is the indirect cost, which includes all of the expenses associated with the manufacturing process that are not directly related to the production of the pump. This may include facility rental, utilities, insurance, maintenance and repair, taxes and fees, and other overhead costs. These expenses can be difficult to accurately calculate and may vary greatly depending on the size and location of the production facility.
Finally, there are the distribution costs, which include the expenses involved in getting the pump from the manufacturer to the end user. This may include shipping, packaging, and marketing expenses, as well as any commissions or fees paid to distributors or sales agents.
Overall, the manufacturing expenses for pump cost can vary greatly depending on a wide range of factors, including the size and complexity of the pump, the location of the manufacturer, and the distribution channels used to get the product to market. By carefully analyzing each of these factors and finding ways to optimize costs and improve efficiency, manufacturers can help to reduce the overall cost of producing a pump, making it more affordable and accessible to a wider range of customers.
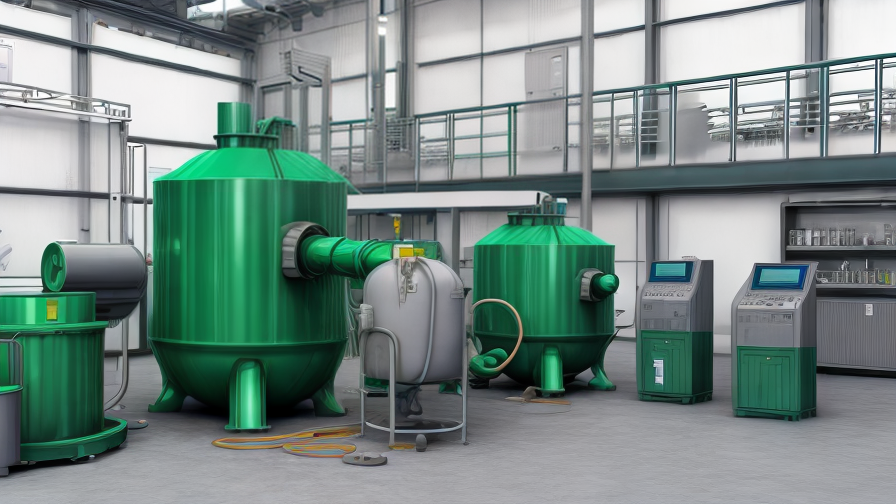
Understanding the Components that Contribute to the Price of pump cost
There are several components that contribute to the price of pump cost. These include the cost of materials used to manufacture the pump, labor costs associated with assembling the pump, distribution costs, taxes and tariffs, and profit margin for the manufacturer and/or retailer.
The cost of materials used to manufacture the pump can vary greatly depending on the type of pump and the materials used. For example, a simple hand pump may be made primarily of plastic, while a high-end industrial pump may be made of stainless steel, aluminum, and other high-quality materials.
Labor costs associated with assembling the pump can also vary depending on the type of pump. Assembly of a simple hand pump may require minimal labor, while assembly of a complex industrial pump may require skilled labor and specialized tools.
Distribution costs include transportation and storage costs associated with getting the pump from the manufacturer to the retailer or end-user. These costs can be significant depending on the size and weight of the pump, as well as the distance between the manufacturer and the retailer or end-user.
Taxes and tariffs can also impact the price of a pump. Import/export taxes, sales tax, and other fees may be applied to the pump, depending on where it is manufactured and sold.
Profit margin is a key component of pump cost. Manufacturers and retailers must make a profit to stay in business, so they will typically add a markup to the cost of the pump to cover their expenses and generate a profit.
In conclusion, the components that contribute to the price of pump cost are the cost of materials, labor costs, distribution costs, taxes and tariffs, and profit margin. Understanding these components can help consumers make informed decisions when purchasing a pump and can also help manufacturers and retailers determine appropriate pricing strategies.
Comparing the Wholesale and Retail Prices of pump cost in China
In China, the wholesale and retail prices of pump cost vary significantly. The wholesale price is the price a manufacturer or supplier charges a retailer for the product, while the retail price is the price at which the retailer sells the product to consumers.
In China, the wholesale price of pump cost is lower than the retail price. This is because manufacturers and suppliers offer discounts to retailers when they purchase large quantities of pumps. In return, retailers charge a higher price to consumers to make a profit.
The difference between the wholesale and retail price can range anywhere from 30% to 50%. This means that consumers could be paying a significantly higher amount for the same product that retailers purchase for a much lower price.
However, it’s important to note that some retailers, particularly in online marketplaces such as Alibaba and Taobao, may sell the pumps at a price closer to the wholesale price. This is because they may be purchasing directly from manufacturers or suppliers, eliminating the need for intermediaries and allowing them to offer a more competitive price to consumers.
In summary, the wholesale and retail prices of pump cost in China differ significantly, with the wholesale price being much lower than the retail price. Consumers can save money by purchasing from retailers that offer prices closer to the wholesale price, such as those found in online marketplaces.

Understanding Shipping and Logistics for pump cost from China
Shipping and logistics play a vital role in the overall cost of importing pumps from China. The cost of the pump itself is just one aspect of the total cost of importing. Other costs include shipping fees, taxes, customs duties, and various logistics costs, such as warehousing, handling, and clearance.
The most common shipping methods for pumps from China are air freight, sea freight, and express delivery. The choice of shipping method depends on various factors, such as the size and weight of the pump, urgency of delivery, and budget.
Air freight is the fastest shipping method but is also the most expensive, especially for large and heavy pumps. Sea freight, on the other hand, is the most affordable option but takes longer to arrive and involves more complex logistics. Express delivery is ideal for small and urgent shipments but can be costly for larger quantities.
Customs duties and taxes are also important considerations when importing pumps from China. It is essential to determine the correct HS code for the product to avoid incorrect classification, which can lead to increased customs duties. Import taxes also vary by country and can significantly impact the overall pricing of the goods.
Finally, logistics costs such as warehousing, handling, and clearance should also be factored in when calculating the cost of importing pumps from China. These costs can vary depending on the port of entry and destination, and it is essential to work with reputable logistics providers who can assist in navigating these costs effectively.
In conclusion, the total cost of importing pumps from China includes various factors such as shipping fees, taxes, customs duties, and logistics costs. By understanding these factors and working with trusted partners, importers can effectively manage their costs and ensure a successful and profitable importation of their pumps.
Potential Tariffs or Import Taxes on pump cost Purchased from China
The U.S. government has recently proposed imposing tariffs on goods purchased from China, including pumps. If these tariffs are implemented, it could increase the cost of pumps purchased from China and ultimately affect the price at which they are sold in the U.S.
Import taxes or tariffs would be levied on the cost price of pumps imported from China. The higher the tariff, the more expensive the imported pump will be. If the import tax increases by 10%, for instance, the cost of a pump originally valued at $20 would go up to $22. This would increase the retail price of pumps in the United States, making it less attractive to consumers.
Higher tariffs or import taxes would significantly impact American manufacturers and distributors who rely heavily on pumps imported from China. This may result in product scarcity, lower profit margins, and a decrease in sales. Moreover, it would lead to the loss of jobs in the manufacturing and distribution sectors.
In conclusion, implementing tariffs on imported pumps from China could increase pump costs, and in turn, affect the profitability of companies in the pump industry. It could also lead to a reduction of available pumps in the United States, hurting consumers’ options as well.

Impact of Market Demand and Competitive Environment on pump cost
The cost of pumps is influenced by market demand and competitive environment. A higher demand for pumps would cause an increase in production, which may result in an increase in price due to price elasticity of supply. However, competition within the market may force producers to lower prices in order to attract buyers and gain market share. The competitive environment of the market can also lead to innovation and cost-saving measures implemented by manufacturers to remain competitive, leading to lower costs for consumers. Additionally, changes in input costs such as raw materials or energy may affect pump cost and profitability. All these factors are interdependent, and any change in one may have cascading effects on the others. In conclusion, market demand and competition are key factors in determining pump cost, which ultimately affects consumer’s purchasing decisions.
FAQ about pump cost with multiple answers
Q: How much does a pump cost?
A: The cost of a pump can vary depending on the type, size, and brand. For example, a small submersible pump for home use can cost around $50, while a larger commercial-grade pump can cost up to $5,000 or more.
Q: How much does it cost to install a pump?
A: The cost of pump installation can also vary depending on the type and size of the pump, as well as any additional equipment or labor required. For a basic installation of a small submersible pump, the cost can range from $100-$500, while a more complex installation of a larger commercial pump can cost upwards of $10,000.
Q: How often do I need to replace my pump?
A: The lifespan of a pump can vary depending on how frequently it is used and how well it is maintained. However, most pumps have an average lifespan of 10-15 years. It is important to regularly inspect and maintain your pump to ensure it is functioning properly and catch any potential issues before they escalate.
Q: Can I save money on pump costs?
A: Yes, there are several ways to save on pump costs. One way is to invest in a high-quality pump that is energy efficient, as this can help reduce energy costs over time. Additionally, proper maintenance and upkeep of your pump can help prolong its lifespan and prevent costly repairs or replacement.
Q: Is it worth it to buy a more expensive pump?
A: It may be worth it to invest in a more expensive pump if it is higher quality and more energy efficient. A higher quality pump may also have a longer lifespan and require less maintenance, ultimately saving money in the long run. However, it is important to consider the specific needs and usage of the pump before making a purchasing decision.
In summary, the cost of a pump and installation can vary widely depending on several factors, and regular maintenance and proper usage can help prolong the lifespan and save money in the long run. It may also be worth it to invest in a higher quality and more energy efficient pump, but this should be considered based on individual needs and usage.