Types and Applications of rigid flex pcb
Rigid-flex PCBs are an innovative engineering solution that offers both the flexibility and functionality of rigid PCBs and the flexibility and adaptability of flexible PCBs. As the name suggests, rigid-flex PCBs are a combination of both rigid and flexible circuit boards that are interconnected using mechanical fasteners and flexible connectors to form a complete unit.
There are two primary types of rigid-flex PCBs: single-sided rigid-flex PCBs and double-sided rigid-flex PCBs. Single-sided rigid-flex PCBs consist of a single rigid layer and a single flexible layer. On the other hand, double-sided rigid-flex PCBs have two rigid layers and two flexible layers.
The primary applications of rigid-flex PCBs include medical equipment, military and aerospace, automotive and transportation, and consumer electronics. These PCBs are widely used in medical devices as they can provide flexibility and durability in applications such as implant devices, diagnostic equipment, and medical sensors. In military and aerospace applications, rigid-flex PCBs offer robust and highly reliable solutions that can withstand extreme environmental conditions such as high temperatures, shocks, and vibration.
Automotive and transportation industries also utilize rigid-flex PCBs for their highly reliable nature, particularly in control and monitoring systems. Rigid-flex PCBs can also be used in various consumer electronics such as smartphones, tablets, and wearable devices. With their compact size, light weight, and flexibility, rigid-flex PCBs enable the creation of products that are not possible using traditional rigid PCBs.
In summary, rigid-flex PCBs are an innovative and versatile technology that offers a highly reliable and flexible solution for various industries. The two primary types of rigid-flex PCBs, single and double-sided, cater to specific design requirements. With their diverse applications from medical equipment to consumer electronics, rigid-flex PCBs offer endless design options and functionalities.
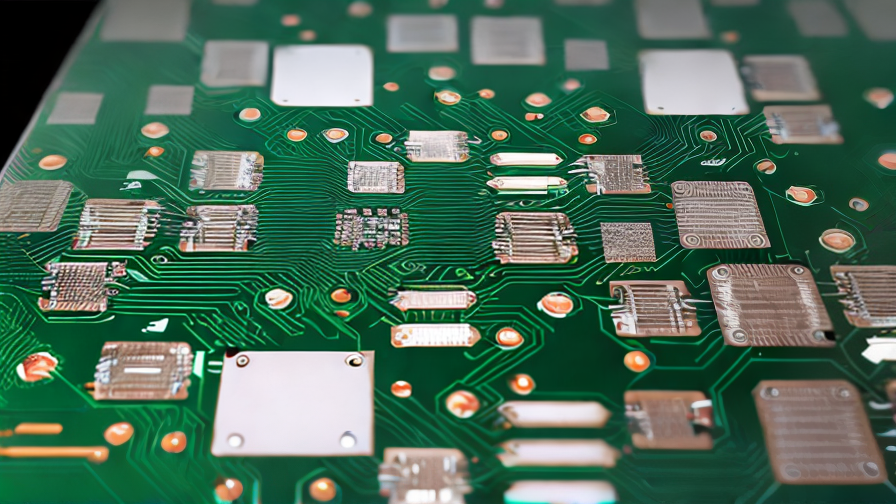
Benefits and Feature of Utilizing rigid flex pcb
Rigid flex PCBs, as their name suggests, combine the strengths of rigid and flexible PCBs. They consist of a rigid circuit board that is supplemented with flexible PCBs. The use of rigid flex PCBs allows for more compact and complex designs that would be difficult to achieve with rigid or flexible PCBs alone. In this article, we will explore the benefits and features of utilizing rigid flex PCBs.
Benefits:
1. Weight and Space Reduction: Rigid flex PCBs reduce the need for additional wiring and connectors, which can significantly reduce the weight and overall size of the device.
2. Reliability and Durability: Rigid flex PCBs are less prone to failure due to their increased durability as there are fewer connections in the design, which means less chance of failure.
3. High Flexibility: Rigid flex PCBs are designed to bend and twist without breaking. This makes them an ideal choice for devices requiring a high level of flexibility.
4. Cost Reduction: Rigid flex PCBs can reduce the cost of a device by eliminating the need for multiple rigid PCBs and connectors.
Features:
1. Increased Density: Rigid flex PCBs have a higher density of components and connections since they can be located on both the rigid and flexible parts of the PCB.
2. Increased Design Flexibility: Rigid flex PCBs allow for the designer to create more intricate and customized designs, combining the advantages of both rigid and flexible PCBs.
3. Multiple Layers: Rigid flex PCBs typically have more layers than traditional rigid or flexible ones, which facilitates routing and increases design complexity.
4. Enhanced Thermal Management: Rigid flex PCBs have a greater capacity for thermal management since they can incorporate a variety of thermal management solutions.
In conclusion, integrating rigid flex PCBs into the design of an electronic device can offer numerous benefits, such as reduced weight and space, higher reliability and durability, and increased flexibility. Moreover, rigid flex PCBs offer enhanced density, design flexibility, multiple layers, and thermal management capabilities. With all of these features combined, rigid flex PCBs are an excellent choice for many applications.
The Process of rigid flex pcb
Rigid flex PCB, as the name suggests, is a combination of a rigid board and a flexible board that are connected together. This design allows for increased functionality while reducing the overall size and weight of the product. The process of creating a rigid flex PCB involves several steps, which are as follows:
1. Design: The first step in creating a rigid flex PCB is to design the board. This involves creating a schematic diagram that outlines the components and their placement on the board.
2. Material selection: Once the design is complete, the materials for the rigid and flexible boards are selected. The rigid board is typically made of FR4 or other rigid materials, while the flexible board is made of polyimide or other flexible materials.
3. Layering: The rigid and flexible layers are then combined into a single stackup. Multiple layers can be added to increase the functionality of the board.
4. Stackup bonding: The layers are then bonded together using an adhesive or a heat-activated bonding process.
5. Drilling and routing: Holes for the components and connectors are drilled into the board, and the board is then routed to create the required shapes.
6. Plating: The holes and traces are then plated to create the required connections between the layers.
7. Assembly: The components are then mounted onto the board, and the board is tested to ensure that it is functioning correctly.
8. Final inspection: The finished board is inspected to ensure that it meets the required specifications.
In conclusion, the process of creating a rigid flex PCB involves designing the board, selecting materials, layering, bonding, drilling and routing, plating, assembly, and final inspection. Each step in the process is crucial to ensure that the board is functioning correctly and meets the required specifications.

How to use rigid flex pcb
Rigid flex PCB or printed circuit board is a combination of rigid and flexible circuits that are interconnected. It offers a way to reduce the use of connectors, which in turn reduces the weight, size, and cost of an electronic product. The rigid flex PCB consists of multiple layers of conductive materials and insulating polymers that are stacked together.
The first step in using rigid flex PCB is to create a design that specifies the various layers, the size and location of the rigid and flexible sections, and the location of the components that will be placed on the board. Once the design is finalized, the board is manufactured using a combination of chemical etching, drilling, and layer lamination.
One of the benefits of using rigid flex PCB is that it offers greater design flexibility, allowing for unique board shapes, and new opportunities to improve product performance. Additionally, the conductive layers of the rigid flex PCB offer improved signal reliability, which means less disruption to radio waves.
The key applications for using rigid flex PCB include medical devices, aerospace and military equipment, telecommunications products, and consumer electronics. In these industries, the combination of rigid and flexible circuits is essential to reduce the size, weight, and cost of the electronic devices while improving their reliability and performance.
Overall, the use of rigid flex PCB offers many advantages over traditional rigid PCB. By taking advantage of its design flexibility, the use of components, and reduced connector requirements, it can help reduce the manufacturing and assembly costs of various electronic products.
rigid flex pcb Manufacturer,Supplier and Wholesale
Rigid-flex PCBs offer significant advantages over traditional PCBs in terms of space management, flexibility, and durability. As a leading manufacturer and supplier of rigid-flex PCBs, we have the expertise to deliver quality products that meet the highest industry standards.
Our rigid-flex PCBs are made using advanced manufacturing techniques that ensure quality and consistency. We offer a range of services including design, prototyping, production, and assembly, all of which are tailored to meet the specific requirements of our customers.
With over a decade of experience in the industry, we have built a reputation for delivering reliable and cost-effective solutions to our customers. Our team of experts work closely with our customers to understand their requirements and provide them with customized solutions that meet their unique needs.
We use high-quality materials, state-of-the-art equipment, and rigorous quality control processes to ensure a finished product that meets or exceeds industry standards. Our products are widely used in a range of industries including aerospace, medical, automotive, and defense, among others.
As a wholesale supplier, we offer competitive pricing and fast turnaround times on all our products. We are committed to providing our customers with exceptional customer service and support, ensuring a hassle-free experience from start to finish.
In conclusion, if you are looking for a reliable and experienced manufacturer, supplier, and wholesale of rigid-flex PCBs, you can count on us to deliver quality products that meet your specific needs. Contact us today to learn more about our products and services.

rigid flex pcb Price
Rigid-flex PCBs, also known as hybrid PCBs, serve as an ideal solution for electronic products that require high level integration, reliability and solid structures. They combine the benefits of rigid PCBs’ mechanical strength and the flexibility of flex circuits. The pricing of this technology varies in line with aspect ratio, hole size, material type, order volume, layer count, number of bends and overall complexity.
The prices for rigid-flex PCBs (RFPs) vary depending on the aforementioned factors. Compared to traditional PCBs, RFPs are not cheap and their manufacturing process requires expertise and specialized equipment. The average cost generally ranges from a few hundred dollars to several thousand dollars, depending on the specifications.
Usually, customers can get an online quote or request a quote directly from the manufacturer before placing an order for RFPs. However, price transparency has improved significantly as customers can usually find an online calculator which provides an estimated cost for their custom RFP when they input their specifications.
In conclusion, the price for RFPs can vary extensively, often resulting in confusion about how much customers should expect to pay for them. Still, it’s important to ensure that you get what you pay for, such as high-quality materials, exceptional functionality, and reliable performance. As the technology continues to grow and develop, RFP prices are expected to reduce while maintaining their high quality and functionality.
FAQ sourcing rigid flex pcb manufacturer from China with multiple answers
Q: What should I consider when choosing a rigid flex PCB manufacturer from China?
A: When choosing a rigid flex PCB manufacturer from China, consider the following factors:
1. Manufacturing capabilities and experience in producing rigid flex PCBs
2. Quality control measures and certifications
3. Communication and language skills
4. Pricing and lead time
5. Customer service and support
Q: How can I ensure the quality of the rigid flex PCB?
A: To ensure the quality of the rigid flex PCB, you can request for a sample or prototype before placing a bulk order. You can also ask for information about the manufacturer’s quality control measures and certifications, such as ISO 9001 and UL. Additionally, you can perform in-house or third-party testing to verify the quality of the PCB.
Q: What is the lead time for a rigid flex PCB order?
A: The lead time for a rigid flex PCB order can vary depending on the manufacturer and the quantity ordered. Generally, the lead time can range from a few days for a small quantity to several weeks for a larger order. It is important to discuss the lead time with the manufacturer before placing the order to ensure it aligns with your project timeline.
Q: Can I customize my rigid flex PCB design?
A: Yes, most rigid flex PCB manufacturers from China offer custom design services. You can discuss your specific requirements and specifications with the manufacturer to ensure the PCB is tailored to your needs. Be sure to communicate your design requirements clearly and provide any necessary design files or documentation to the manufacturer.
Q: What is the cost of a rigid flex PCB?
A: The cost of a rigid flex PCB can vary depending on factors such as the size, quantity, and complexity of the design. You should request a quote from the manufacturer to obtain an accurate cost estimate. It is important to consider the quality and reliability of the PCB when comparing prices from different manufacturers.