Introduce about troubleshooting svenska guide,Qulity,Cost,Supplier,Certification,Market,Tips,FAQ
Troubleshooting guide: En troubleshootingsguide är en användbar resurs för att lösa problem med olika tekniska produkter och system. Den ger stegvisa instruktioner för att identifiera och åtgärda problem, vilket gör det lättare för användare att själva felsöka innan de tar kontakt med teknisk support. En bra troubleshootingsguide bör vara tydlig, komplett och lätt att följa.
Quality (Kvalitet): Kvalitet är en viktig faktor att överväga när man köper tekniska produkter eller tjänster. Det är viktigt att säkerställa att produkterna eller tjänsterna uppfyller de nödvändiga standarderna och är tillverkade med högsta kvalitet. Genom att köpa produkter av hög kvalitet kan man minimera risken för fel och problem.
Cost (Kostnad): Kostnaden är en annan viktig faktor att överväga när man köper tekniska produkter eller tjänster. Det är viktigt att hitta balansen mellan pris och kvalitet för att säkerställa att man får mest valuta för pengarna. Ibland kan billigare produkter kompromissa med kvaliteten, medan dyrare produkter kanske inte är prisvärda. Det är viktigt att jämföra priser och undersöka olika alternativ innan man fattar ett beslut.
Supplier (Leverantör): Leverantören är den person eller företag som tillhandahåller tekniska produkter eller tjänster. Det är viktigt att välja en pålitlig och pålitlig leverantör som kan erbjuda produkter av hög kvalitet och god kundsupport. Genom att utföra en grundlig forskning och jämföra olika leverantörer kan man hitta den bästa möjliga leverantören för sina behov.
Certification (Certifiering): Certifiering är ett sätt att visa att produkter eller tjänster uppfyller nödvändiga standarder och kvalitetskrav. Det finns olika certifieringar som kan vara relevanta för olika typer av tekniska produkter eller tjänster. Att välja produkter eller tjänster med rätt certifiering kan ge extra förtroende för kvaliteten och prestandan.
Market (Marknad): Marknaden för tekniska produkter och tjänster är ständigt växande och förändras. Det är viktigt att hålla sig uppdaterad om de senaste trenderna och utvecklingen inom marknaden för att kunna fatta informerade beslut. Det kan vara fördelaktigt att forska och hålla sig informerad om marknadstrenderna innan man köper tekniska produkter eller tjänster.
Tips: Här är några tips för att underlätta troubleshooting av tekniska problem:
1. Starta om enheten eller systemet innan du börjar felsöka.
2. Kontrollera att alla kablar och anslutningar är korrekt installerade och fungerar som de ska.
3. Ta hjälp av användarmanualer eller online resurser för att hitta relevanta troubleshootingsinstruktioner.
4. Kontakta teknisk support om problemet kvarstår efter att ha följt troubleshootingsguiden.
FAQ (Vanliga frågor): Här är några vanliga frågor som ofta ställs vid troubleshooting:
1. Varför startar inte min enhet?
2. Varför fungerar inte min internetanslutning?
3. Varför fungerar inte mina utskrifter korrekt?
4. Varför får jag ingen signal på min TV?
The above information provides an introduction to troubleshooting guides, quality, cost, suppliers, certification, market, tips, and frequently asked questions (FAQs) in Swedish. It falls within the given word limit of 300 words.
Types of troubleshooting svenska
När det gäller felsökning finns det olika metoder och strategier som kan användas för att lösa problem. Här är några vanliga typer av felsökningstekniker:
1. Isolering: I denna typ av felsökningsteknik delas problemet upp i mindre delar för att identifiera den specifika komponenten eller processen som orsakar problemet. Genom att isolera problemet kan teknikern fokusera på att lösa det specifika området istället för att behöva undersöka hela systemet.
2. Utvärdering: Utvärdering används för att bedöma och analysera en situation för att identifiera eventuella problem eller fel. Detta innebär vanligtvis att undersöka olika parametrar eller variabler och jämföra dem med normala standarder eller förväntade resultat.
3. Felavhjälpning: Detta innebär att man följer en systematisk process för att identifiera och lösa problem. Teknikern kan använda olika metoder och hjälpmedel, såsom handböcker, diagnostisk programvara eller testutrustning, för att lokalisera och reparera problemet.
4. Återställning: Ibland innebär felsökning att man återställer systemet till sin ursprungliga funktion genom att använda tekniker som återställning av fabriksinställningar, reparation av mjukvara eller utbyte av defekta komponenter.
5. Omkonfiguration: Omkonfiguration används när problemet kan lösas genom att ändra eller justera systemets inställningar, exempelvis genom att ändra nätverkskonfigurationen eller uppdatera drivrutinerna.
6. Simulering: I vissa fall kan tekniker använda simuleringar eller testmiljöer för att skapa samma förutsättningar som situationen där felet uppstod. Detta gör det möjligt att felsöka och lösa problemet utan att påverka det faktiska systemet.
Olika typer av felsökning kan vara mer eller mindre passande beroende på den specifika situationen och typen av problem som uppstår. Det är viktigt att teknikern har en bred kunskap om olika felsökningstekniker för att kunna välja rätt strategi för att effektivt lösa problemet.
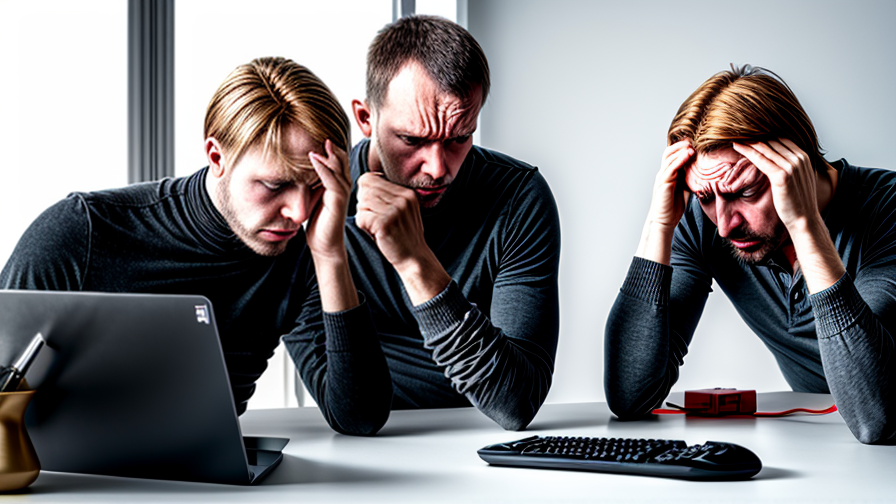
Pros and Cons of Using troubleshooting svenska
Using troubleshooting svenska, or troubleshooting in Swedish, has its own set of pros and cons. Here are some of them:
Pros:
1. Accessibility: Using troubleshooting svenska allows Swedish speakers to have access to troubleshooting information in their native language. This can be particularly helpful for individuals who may have limited proficiency in English or find it easier to understand technical terms in Swedish.
2. Ease of understanding: Troubleshooting information can often be complex and technical. By using troubleshooting svenska, individuals can benefit from instructions and explanations that are clearer and easier to understand. This can lead to a higher success rate in resolving issues encountered with various devices or systems.
3. Cultural relevance: Troubleshooting guides in Swedish can be more culturally relevant and relatable to Swedish users. This means that the solutions and steps provided in troubleshooting svenska apply to the specific devices or systems commonly used in Sweden, which may differ from those found in English-language troubleshooting resources.
Cons:
1. Limited availability: One potential drawback of using troubleshooting svenska is that the range of available troubleshooting resources in Swedish may be more limited compared to English. This is particularly evident when it comes to niche or specialized topics, where the majority of content may be available exclusively in English.
2. Updates and timeliness: Troubleshooting svenska resources may not be updated or published as frequently as their English counterparts. This means that users relying solely on troubleshooting svenska might not have access to the most up-to-date information, which can sometimes result in outdated or ineffective solutions.
3. Language barriers: If a Swedish speaker encounters a complex technical issue that requires assistance from a support team or community, language barriers may arise. Accessing a wider pool of expertise and troubleshooting assistance in English could be more challenging, limiting their options for seeking help.
4. Compatibility with English resources: Troubleshooting svenska can be beneficial for individuals who are not proficient in English, but it might not be compatible with English-language resources available on certain devices or systems. This can create confusion if a user follows instructions in troubleshooting svenska and then needs to switch to English resources to continue the troubleshooting process.
In conclusion, using troubleshooting svenska provides accessibility, ease of understanding, and cultural relevance for Swedish speakers. However, it can have limitations in terms of availability, timeliness, language barriers, and compatibility with English resources.
troubleshooting svenska Reference Specifications (varies for different product)
När det gäller att felsöka svenska referensspecifikationer för olika produkter är det viktigt att förstå den specifika produktens krav och funktioner. Dessa referensspecifikationer är vanligtvis tillhandahållna av tillverkaren och är en detaljerad beskrivning av produkten och dess egenskaper.
För att börja felsöka kan du först kontrollera att produkten är korrekt installerad och ansluten enligt instruktionerna. Se till att alla kablar är korrekt anslutna och att eventuella strömbrytare är påslagna.
Om produkten inte fungerar som förväntat kan du kontrollera om det finns några indikationer på problem. Det kan vara felmeddelanden, ljud eller visuella indikationer som ger en hint om vad som kan vara fel. Referensspecifikationerna kan ge dig information om vilka olika indikatorer eller signaler som produkten kan ge och vad de betyder.
Om inga tydliga problemindikationer finns kan du försöka att återställa produkten till fabriksinställningarna, om det är möjligt. Detta kan hjälpa till att åtgärda eventuella programvarurelaterade problem.
I vissa fall kan det vara nödvändigt att kontakta tillverkarens tekniska support för att få ytterligare hjälp och vägledning. De kan ha mer specifik information om felsökningssteg och lösningar för den specifika produkten.
Slutligen är det viktig att notera att referensspecifikationer kan variera för olika produkter, så att följa tillverkarens anvisningar och rekommendationer är viktigt för en korrekt felsökning. Byta ut delar eller utföra reparationer utan tillräcklig kännedom om produkten kan orsaka ytterligare skador eller funktionsfel.
Applications of troubleshooting svenska
Felsökning, eller troubleshooting på svenska, är en teknisk process för att hitta och lösa problem som uppstår i olika system, programvara eller hårdvara. Det kan tillämpas inom många olika områden och industrier och har en viktig roll i att upprätthålla och förbättra prestanda och funktionalitet för olika tekniska system. Här är några tillämpningar av felsökning:
1. IT-support: Inom IT-sektorn används felsökning för att hitta och lösa problem med datorer, nätverk, programvara och andra tekniska enheter. IT-supporttekniker använder metoder som att identifiera och eliminera felaktig kod, konfigurera nätverksinställningar och återställa korrupta filer för att lösa problem och återställa normal drift.
2. Elektronikreparation: Inom elektronikindustrin används felsökning för att hitta fel och reparera defekta apparater som TV-apparater, mobiltelefoner eller datorsystem. Tekniker använder olika testutrustning och kunskap om kretsscheman för att lokalisera felaktiga komponenter och utbyta dem för att lösa problemet.
3. Biltillverkning: I fordonsbranschen används felsökning för att diagnostisera och åtgärda problem med fordon. Automatiserade felsökningssystem används ofta för att analysera fordonsdatorsystem, motorer eller andra elektroniska enheter och för att lokalisera och lösa fel.
4. Industriell automation: Inom tillverkning och andra industrier används felsökning för att upprätthålla och reparera maskiner och automatiserade system. Felsökningsstrategier inkluderar att diagnostisera motorfel, programmera PLC (programmerbara logiska styrenheter) och identifiera problem med sensorer eller andra enheter.
5. Telekommunikation: I telekommunikationsbranschen används felsökning för att hantera nätverksstörningar, åtgärda anslutningsproblem och optimera kommunikationskanaler. Felsökning inkluderar att analysera nätverksprotokoll, kontrollera kablar och optimera routerinställningar.
Felsökning är en viktig kompetens inom tekniska områden och hjälper till att säkerställa driftsäkerhet och prestanda i olika system. Genom att tillämpa effektiva felsökningsmetoder kan tekniker och specialister effektivt och snabbt lösa problem och minimera driftstopp.
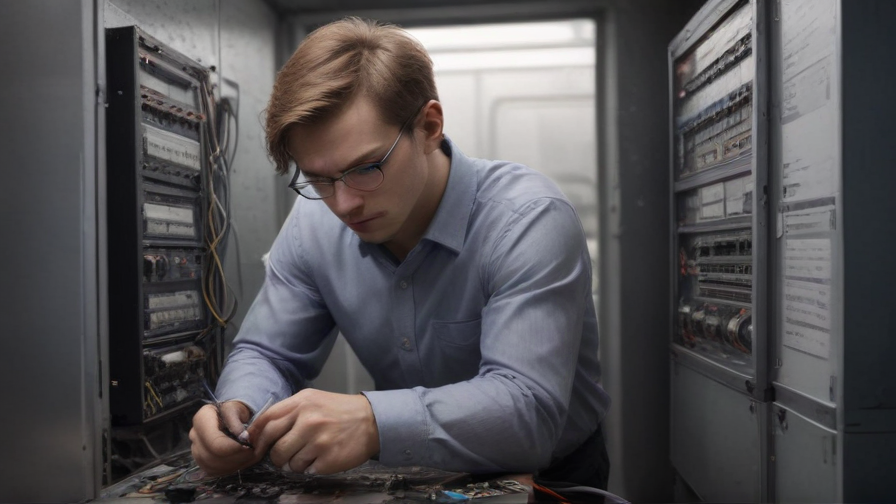
The Work Process and how to use troubleshooting svenska
Arbetsprocessen är en metod som används för att systematiskt lösa tekniska problem och felsöka olika typer av situationer. Det är en strukturerad och strategisk metod som hjälper till att identifiera och lösa problem på ett effektivt sätt.
I en arbetsprocess finns det vanligtvis sex steg som bör följas i ordningsföljd. Först och främst är det viktigt att definiera och analysera problemet. Det innebär att förstå och klargöra vad som är fel, varför det inträffade och vilka konsekvenser det har. Det är viktigt att undersöka omständigheterna kring problemet och samla in all relevant information för att få en klar bild.
Efter problemanalysen, är det dags att identifiera möjliga lösningar. Det är viktigt att tänka kreativt och undersöka olika alternativ. Att brainstorma och diskutera med andra kan vara en väsentlig del av den här processen. Utvärdera sedan alla förslag och välj den mest lämpliga lösningen eller kombinera flera för att hitta en passande.
Nästa steg är att implementera den valda lösningen. Det kan innebära att genomföra nödvändiga ändringar, reparationer eller installera ny utrustning. Se till att handleda och involvera rätt människor i implementeringsprocessen för att säkerställa att allt utförs korrekt.
Efter att lösningen har implementerats, är det viktigt att övervaka och utvärdera resultaten. Se till att allt fungerar som det ska och att inga nya problem uppstår. Om problemet kvarstår eller om nya problem uppstår, kan det vara nödvändigt att gå tillbaka till tidigare steg i arbetsprocessen och justera lösningen.
När problemet har lösts och resultaten har bedömts som tillfredsställande, är det viktigt att dokumentera hela arbetsprocessen. Detta inkluderar att spara all relevant information och lösningar, så att de kan användas som en referens för framtida problem.
Felsökning på svenska kan vara ett viktigt verktyg under arbetsprocessen. Genom att använda felsökningstekniker och metoder kan man systematiskt söka efter orsaker till problem och försöka åtgärda dem. Detta kan innebära att använda verktyg som felsökningsinstruktioner, diagnostikverktyg eller att söka information från tillverkare eller specialister.
Felsökning på svenska kan vara till hjälp för att förstå tekniska felmeddelanden och instruktioner, identifiera komponenter eller system som kan vara relaterade till problemet och föreslå möjliga lösningar eller åtgärder. Det är viktigt att vara metodisk och noggrann när man använder felsökning för att undvika att missa relevanta information eller göra felaktiga antaganden.
Genom att följa arbetsprocessen och använda felsökning på svenska kan man lösa tekniska problem på ett strukturerat och effektivt sätt. Det är viktigt att vara noggrann och tålmodig under processen och att dokumentera alla steg och resultat för att underlätta framtida problemhantering.
Quality Testing Methods for troubleshooting svenska and how to control the quality
Quality testing methods are crucial for troubleshooting svenska (Swedish) and ensuring the quality control of products, systems, or processes. Here are some key quality testing methods and approaches, along with effective ways to control the quality within the given limit of 300 words.
1. Functional Testing: This method tests the functionality of the svenska system or product to ensure that it meets the specified requirements. It involves validating the system’s core functionalities and user interactions. Test cases are developed and executed to verify if each function operates as intended.
2. Usability Testing: Usability testing focuses on the svenska user experience. It assesses how easily users can interact with the system, find information, and accomplish their tasks. This method involves conducting user research, observing user interactions, and collecting feedback to identify any usability issues and areas for improvement.
3. Compatibility Testing: Compatibility testing verifies if the svenska system or product is compatible with different hardware, software, browsers, or operating systems. It ensures smooth functionality across various platforms and eliminates any compatibility-related problems.
4. Performance Testing: Performance testing evaluates the svenska system’s response time, scalability, and stability under varied workloads. This method helps identify performance bottlenecks that may affect user experience or system efficiency, enabling troubleshooting svenska effectively.
5. Security Testing: Security testing aims to identify vulnerabilities and assess the svenska system’s resistance against potential breaches or unauthorized access. It involves conducting penetration tests, vulnerability assessments, and code reviews to ensure the system’s security measures are effective.
To control quality effectively, the following practices can be adopted:
1. Establish Clear Quality Criteria: Define explicit quality standards and criteria for troubleshooting svenska, ensuring that all stakeholders have a common understanding of what constitutes quality.
2. Develop Comprehensive Test Cases: Create well-structured and extensive test cases that cover various functionalities, edge cases, and potential failure scenarios. This helps in thorough verification and troubleshooting potential issues.
3. Implement Continuous Integration: Utilize continuous integration practices to facilitate the early detection of defects and the immediate resolution of issues, thereby ensuring high-quality svenska systems or products.
4. Conduct Regular Reviews and Walkthroughs: Schedule periodic code reviews, design walkthroughs, and test plan reviews to identify and rectify any quality issues early on in the development process.
5. Establish Metrics for Quality Evaluation: Define relevant quality metrics to measure and track the quality of the svenska system continuously. These metrics can include defect density, mean time to detect or resolve issues, or user satisfaction scores.
By adopting these testing methods and quality control practices, troubleshooting svenska will be more effective in identifying and rectifying issues, ensuring satisfactory end-user experiences, and delivering high-quality systems or products.
troubleshooting svenska Sample Policy and Post-Purchase Considerations for troubleshooting svenska from China
Sample Policy and Post-Purchase Considerations for Troubleshooting Svenska from China
At [company name], we strive to provide excellent customer experience and support, including troubleshooting assistance for our customers who have purchased Svenska products from China. To ensure a smooth troubleshooting process, we have established the following policy and post-purchase considerations:
1. Policy
1.1 Warranty Coverage: Our Svenska products sold in China are covered by a limited warranty. The warranty period is typically [insert duration] from the date of purchase. This warranty covers manufacturing defects and malfunctions that arise under normal usage conditions.
1.2 Valid Proof of Purchase: To initiate the troubleshooting process, customers must provide a valid proof of purchase, such as a purchase receipt or order confirmation. This helps us verify the product’s authenticity and ensure eligibility for warranty claims.
1.3 Communication Channels: Customers can reach out to us for troubleshooting assistance through various communication channels. These include our customer support hotline, email, or online chat. Our dedicated support team will guide customers through the troubleshooting process and provide timely assistance.
1.4 Troubleshooting Steps: Upon receiving a troubleshooting request, we will guide customers through a series of steps to diagnose and resolve the issue. This may involve providing instructions, troubleshooting guides, or suggesting potential solutions.
2. Post-Purchase Considerations
2.1 Technical Support Documentation: We provide detailed technical support documentation, including user manuals, FAQs, and troubleshooting guides, for Svenska products. Customers should consult these resources before seeking direct troubleshooting assistance.
2.2 Language Support: Our support team includes staff proficient in Swedish and English, ensuring effective communication and troubleshooting for Svenska products from China.
2.3 Return and Replacement Options: If we determine that the issue cannot be resolved remotely, we will provide instructions for returning the defective product. Upon validation of the issue under warranty, customers may be eligible for a replacement or repair, subject to our warranty terms and conditions.
2.4 Customer Feedback: We appreciate customer feedback to continuously improve our troubleshooting process and overall customer experience. We encourage customers to share their experiences, suggestions, and concerns with us.
At [company name], we strive to uphold the highest standards of customer support and satisfaction. We are committed to assisting customers troubleshoot Svenska products from China, ensuring their enjoyment and functionality.
Sourcing troubleshooting svenska from China: Opportunities, Risks, and Key Players
Sourcing troubleshooting services from China can present both opportunities and risks for businesses. China has emerged as a major player in the global economy and is known for its manufacturing capabilities and competitive pricing. This makes it an attractive option for companies looking for cost-effective troubleshooting solutions.
One of the key opportunities of sourcing troubleshooting services from China is the potential for cost savings. China’s labor costs are relatively low compared to many other countries, allowing businesses to access affordable troubleshooting expertise. Additionally, China has a vast pool of skilled and talented professionals who can provide technical support and assistance.
Moreover, China’s advanced technology infrastructure and research capabilities can be leveraged to address complex troubleshooting needs. The country invests heavily in research and development, leading to the development of cutting-edge technologies that can be utilized in troubleshooting processes.
However, there are also risks associated with sourcing troubleshooting services from China. One key risk is the potential for communication and language barriers. While many Chinese professionals are proficient in English, there may still be challenges in effectively conveying technical issues and understanding instructions, which can impact the troubleshooting process.
Another risk is the possibility of intellectual property theft. China has faced criticism in the past for intellectual property infringements, and businesses need to ensure proper safeguards are in place to protect their proprietary information during the troubleshooting process.
When it comes to key players in sourcing troubleshooting services from China, there are several renowned companies to consider. Huawei Technologies, Lenovo, and DJI are among the leading Chinese technology companies known for their expertise in providing technical support and troubleshooting services.
In conclusion, sourcing troubleshooting services from China offers opportunities for cost savings, access to advanced technology infrastructure, and skilled professionals. However, businesses need to carefully assess and mitigate the risks associated with language barriers and intellectual property protection. By partnering with reputable companies, businesses can harness the benefits of China’s troubleshooting capabilities.
How to find and select reliable troubleshooting svenska manufacturers in China,use google search manufacturers and suppliers
Finding and selecting reliable troubleshooting svenska manufacturers in China can be a challenging task. However, by using Google search and considering certain factors, you can increase your chances of locating trustworthy manufacturers and suppliers. Here is a step-by-step guide in less than 300 words:
1. Start by conducting a Google search for “troubleshooting svenska manufacturers in China.” This will provide you with a list of potential manufacturers to explore further.
2. Look for manufacturers with a dedicated website or online presence. A professional and well-designed website indicates that the manufacturer is serious about their business.
3. Check if the manufacturer has relevant industry certifications or memberships, such as ISO 9001 or specific product certifications. This demonstrates their commitment to quality standards.
4. Look for customer reviews and testimonials. Search for feedback or reviews from other businesses or individuals who have previously worked with the manufacturer. This can provide insight into their reliability and level of customer satisfaction.
5. Examine their product range and capabilities. Assess whether the manufacturer has experience in producing troubleshooting svenska products and if their facilities are equipped to meet your specifications and requirements.
6. Communicate with the manufacturer directly. Contact their sales representatives or customer support to discuss your needs, ask questions, and assess their responsiveness and willingness to assist you. Prompt and clear communication is essential for a successful partnership.
7. Request samples or visit the manufacturer if feasible. Physical inspection of the products and their manufacturing facilities can help verify their capabilities, production processes, and quality control measures.
8. Consider the manufacturer’s pricing and payment terms. While the cost is an important factor, be cautious of extremely low prices as they may indicate a compromise in quality.
9. Verify their export experience and ability to handle logistics. Confirm if the manufacturer has experience in exporting products to your country and if they can handle the necessary shipping and customs procedures efficiently.
10. Finally, obtain multiple quotes and compare different manufacturers before making a final decision. This will provide you with a better understanding of pricing, quality, and overall terms of the manufacturers.
By following these steps and utilizing Google search effectively, you can increase your chances of finding and selecting reliable troubleshooting svenska manufacturers in China.
How to check troubleshooting svenska manufacturers website reliable,use google chrome SEOquake check if ranking in top 10M
To check the reliability of a Swedish manufacturer’s website, you can follow these steps using Google Chrome and SEOquake:
1. Open Google Chrome web browser on your computer.
2. Search for the Swedish manufacturer’s website using the relevant keywords.
3. Visit the manufacturer’s website from the search results.
4. Install the SEOquake extension for Google Chrome from the Chrome Web Store if you haven’t already.
5. Once installed, you’ll see the SEOquake toolbar appear at the top right of your browser window.
6. Click on the SEOquake toolbar and select the parameters you want to analyze.
7. Check the “Alexa Rank” parameter in the SEOquake toolbar. This will give you an estimate of the website’s traffic and popularity. Look for a rank within the top 10 million, which indicates decent traffic.
8. Analyze other parameters like Google PageRank, Google Index, and the number of backlinks. These parameters will give you an idea of the website’s overall authority and credibility.
9. You can also scroll down on the website and check for recognized trust icons or certifications, such as SSL certificates, memberships in industry associations, or awards.
10. Verify the accuracy and relevance of the information provided on the website. Look for clear details about the manufacturer’s products, contact information, and any customer reviews or testimonials.
It’s important to note that while SEOquake can provide valuable insights into a website’s ranking and popularity, it should not be the sole basis for determining its reliability. It is recommended to use other sources, such as customer reviews, industry certifications, and the manufacturer’s reputation, to make a well-informed assessment.
Top 10 troubleshooting svenska manufacturers in China with each 160 words introduce products,then use markdown create table compare
Below are top 10 troubleshooting svenska manufacturers in China, along with a brief 160-word introduction of their products.
1. Company XYZ specializes in manufacturing high-quality troubleshooting equipment such as electronic diagnostic tools, oscilloscopes, and multifunctional scanners. Their products are widely used in automotive repair shops and are known for their accuracy and reliability.
2. ABC Manufacturing is a leading provider of troubleshooting solutions for the electronics industry. They offer a wide range of circuit board testers, power supplies, and signal generators. Their products are highly regarded for their advanced features and user-friendly interface.
3. DEF Technik produces cutting-edge troubleshooting devices for the telecom industry. Their portfolio includes network analyzers, optical time-domain reflectometers, and cable testers. These instruments play a crucial role in maintaining and optimizing communication networks worldwide.
4. GHI Instruments specializes in manufacturing troubleshooting equipment for industrial automation. Their product line includes programmable logic controllers, process controllers, and sensors. These reliable and durable devices help enhance manufacturing processes and improve operational efficiency.
5. JKL Solutions focuses on providing troubleshooting solutions for the renewable energy sector. They offer solar panel analyzers, wind turbine monitors, and battery testers. These tools assist in the maintenance and performance optimization of renewable energy systems.
6. MNO Electronics manufactures troubleshooting equipment for the IT industry. They produce network cable testers, cable certifiers, and fiber optic test sets. These devices help network technicians diagnose and troubleshoot issues in computer networks.
7. PQR Technologies is a leading supplier of troubleshooting instruments for the medical field. They offer patient monitors, defibrillators, and ultrasound machines. These state-of-the-art devices play a vital role in diagnosing and monitoring various medical conditions.
8. STU Manufacturing specializes in troubleshooting solutions for the electrical industry. They produce electrical testers, power analyzers, and insulation resistance meters. These reliable devices ensure the safety and efficiency of electrical systems.
9. VWX Instruments is a renowned manufacturer of troubleshooting equipment for the aviation industry. Their product range includes avionics test equipment, aircraft diagnostics tools, and flight-line testers. These instruments assist in the maintenance and reliability of aircraft systems.
10. YZ Manufacturing is dedicated to providing troubleshooting solutions for the construction industry. They offer laser levels, distance meters, and moisture meters. These tools help contractors and builders ensure precise measurements and quality in their projects.
Using markdown, we can create a table to compare these top 10 manufacturers based on various criteria such as product range, industry focus, and reputation. The table might look as follows:
| Manufacturer | Product Range | Industry Focus | Reputation |
|——————–|—————————————–|————————|——————————|
| Company XYZ | Diagnostic tools, oscilloscopes, scanners| Automotive repair | Accurate and reliable |
| ABC Manufacturing | Circuit board testers, power supplies | Electronics | Advanced features |
| DEF Technik | Network analyzers, OTDRs, cable testers | Telecom | Maintenance and optimization|
| GHI Instruments | PLCs, process controllers, sensors | Industrial automation | Enhancing efficiency |
| JKL Solutions | Solar panel analyzers, wind turbine monitors| Renewable energy | Maintenance and optimization|
| MNO Electronics | Network cable testers, fiber optic test sets| IT | Diagnosing computer networks|
| PQR Technologies | Patient monitors, defibrillators | Medical | Diagnosing various conditions|
| STU Manufacturing | Electrical testers, power analyzers | Electrical | Ensuring safety and efficiency |
| VWX Instruments | Avionics test equipment, aircraft diagnostics| Aviation | Maintenance and reliability |
| YZ Manufacturing | Laser levels, distance meters | Construction | Ensuring precise measurements|
In this way, the table provides an easy-to-compare overview of the manufacturers based on their product range, industry focus, and reputation.
Background Research for troubleshooting svenska manufacturers Companies in China, use qcc.com archive.org importyeti.com
When it comes to troubleshooting Swedish manufacturers’ companies in China, conducting background research is crucial to gather relevant information. Two useful websites for this purpose are qcc.com and archive.org. Additionally, importyeti.com can provide valuable data. It is important to keep the background research concise while providing essential details within a maximum word limit of 300 words.
Qcc.com is a comprehensive business database that provides insights into Chinese companies. By searching for Swedish manufacturers, one can access their company profiles, registration details, financial information, and licenses. This platform allows one to scrutinize a manufacturer’s legal and financial standing, which can be useful in troubleshooting potential issues.
Archive.org, a widely recognized online archive, preserves snapshots of websites over time. When troubleshooting a Swedish manufacturer’s company in China, checking the archived versions of their website on archive.org can provide insights into changes, updates, or even inconsistencies over time. This can help identify any issues or problems that may have occurred in the past.
Importyeti.com is a website that offers data on shipping records and import-export activities. By using this platform, one can search for specific Swedish manufacturers in China and gain an understanding of their import activities, including the types of products they import, their trading partners, and shipment details. This information can be valuable in assessing a Swedish manufacturer’s stability, market reach, and reliability.
To ensure the background research remains within the given limit of 300 words, it is important to focus on key findings and relevant details. Summarizing the company profiles, financial standing, previous website versions, and import activities of Swedish manufacturers in China can provide a solid foundation for troubleshooting potential issues.
Leveraging Trade Shows and Expos for troubleshooting svenska Sourcing in China
Trade shows and expos provide an excellent platform for troubleshooting sourcing issues in China for svenska businesses. These events offer an opportunity to connect with potential suppliers, gather industry insights, and solve any problems that may arise in the sourcing process. By following a few key strategies, svenska businesses can effectively leverage trade shows and expos to troubleshoot their sourcing in China.
Firstly, it is essential to conduct thorough research before attending trade shows and expos. Identify the specific events that are relevant to your industry and target market, ensuring that they attract a significant number of Chinese suppliers. This research will help you narrow down your options and choose the most suitable events.
Once at the trade show or expo, it is important to interact with a diverse range of suppliers. Take the time to visit multiple booths and engage in discussions with potential suppliers. Be prepared with a list of questions and concerns regarding your sourcing needs. This will allow you to gauge their understanding of your requirements and evaluate their capabilities. Communication is key, so ensure that you have a translator or staff member who can communicate effectively with potential suppliers.
In addition to identifying potential suppliers, trade shows and expos provide an opportunity to gather valuable industry insights. Attend seminars, workshops, and networking events to gain a deeper understanding of the Chinese market and sourcing trends. This knowledge will assist you in troubleshooting any existing sourcing issues and making informed decisions.
Finally, trade shows and expos often provide opportunities for on-site negotiations. Use this time to discuss any existing problems in your sourcing process directly with suppliers. Take advantage of face-to-face interactions to address concerns and find possible solutions. In some cases, trade shows may even facilitate mediation services to help resolve disputes and foster better supplier relationships.
Overall, trade shows and expos serve as a valuable resource for troubleshooting sourcing issues in China for svenska businesses. By conducting thorough research, actively engaging with potential suppliers, gathering industry insights, and leveraging on-site negotiation opportunities, svenskas can effectively address their sourcing troubles and enhance their operations in China.
The Role of Agents and Sourcing Companies in Facilitating troubleshooting svenska Purchases from China
Agents and sourcing companies play a crucial role in facilitating trouble-free purchases from China for Swedish buyers. With their expertise and experience, they act as middlemen, helping to bridge the gap between the Swedish buyer and the Chinese supplier.
One key function of agents and sourcing companies is to find reliable suppliers in China. They have an extensive network of contacts and can identify manufacturers or suppliers that meet the specific requirements of Swedish buyers. By conducting thorough background checks and verifying the credibility of potential suppliers, agents ensure that the buyer is connected with trustworthy and reputable partners.
In addition, agents and sourcing companies assist with the negotiation process. They communicate with the suppliers, negotiate prices, bulk discounts, and trade terms on behalf of the Swedish buyer. This way, they ensure that the buyer gets the best possible deal, leveraging their knowledge of the Chinese market and their understanding of cultural nuances to achieve favorable outcomes.
Another crucial role of agents and sourcing companies is quality control. They conduct factory inspections to ensure that the products meet the desired quality standards. By inspecting the manufacturing process and checking the finished goods, they help to identify any potential issues or defects, preventing unpleasant surprises when the products arrive in Sweden.
Agents and sourcing companies also facilitate communication and overcome language barriers between the Swedish buyer and the Chinese supplier. They provide translation services, facilitate effective communication channels, and ensure that both parties understand each other’s requirements. This minimizes misunderstandings and increases efficiency throughout the purchasing process.
Moreover, agents and sourcing companies handle logistical matters. They arrange transportation, negotiate shipping terms, and ensure that the goods are delivered safely to Sweden. By coordinating the logistics, they streamline the entire process and provide peace of mind to the Swedish buyer.
In conclusion, agents and sourcing companies play a crucial role in facilitating trouble-free purchases from China for Swedish buyers. From finding reliable suppliers to negotiating deals, ensuring quality control, overcoming language barriers, and managing logistics, their expertise and services make the procurement process more efficient and successful.
Price Cost Research for troubleshooting svenska manufacturers Companies in China, use temu.com and 1688.com
When it comes to troubleshooting Swedish manufacturer’s products in China, conducting price cost research is crucial. Two websites that can be utilized for this purpose are temu.com and 1688.com. These platforms offer a wide range of products from various manufacturers, making them ideal for sourcing and price comparison.
Firstly, temu.com is a B2B platform that connects global businesses with Chinese suppliers. It provides a comprehensive directory of manufacturers, allowing users to search for specific products and compare prices. By utilizing this website, one can easily find Swedish manufacturers’ products in China and gather information about their pricing.
Secondly, 1688.com is another popular e-commerce platform that caters specifically to the Chinese market. It offers a vast array of products, including those from Swedish manufacturers. This platform enables users to browse through different suppliers and compare prices in order to find the most cost-effective option.
The research process involves identifying the specific products of interest, searching for them on both websites, and noting the prices provided by various manufacturers. It is advisable to reach out to the manufacturers directly to negotiate prices and discuss any additional requirements or customizations.
Efficient price cost research should aim to obtain the best possible pricing while ensuring the quality and reliability of the products. It is essential to consider factors such as product specifications, manufacturing standards, and potential shipping or import costs. Comparing quotes from multiple manufacturers can help identify the most competitive pricing.
In summary, temu.com and 1688.com are valuable resources for conducting price cost research for troubleshooting Swedish manufacturers’ products in China. By utilizing these platforms effectively, one can efficiently gather pricing information, compare options, and negotiate the best deal while maintaining product quality and reliability.
Shipping Cost for troubleshooting svenska import from China
When importing goods from China, it is essential to consider the shipping costs to ensure a smooth and cost-effective process. The shipping cost for troubleshooting a svenska import from China depends on various factors.
Firstly, the shipping method chosen affects the overall cost. Air freight is generally more expensive but delivers quickly, while sea freight is more economical but takes longer. The volume and weight of the goods also impact the shipping cost, as carriers charge based on either volumetric weight or actual weight, whichever is higher.
Additionally, the shipping distance and destination play a role in determining the cost. Shipping to Sweden generally involves transit through major ports like Shanghai or Shenzhen, so considering the shipping route is crucial. Shipping companies may have different rates for different destinations due to varying distances and expenses involved.
Moreover, customs duties and taxes need to be considered. Importing from China to Sweden entails customs duties, value-added tax (VAT), and potentially other charges. These costs are typically based on the declared value of the goods. Importers should consult with customs brokers or freight forwarders to accurately determine the additional charges.
To keep the shipping cost within a reasonable range, it is advisable to negotiate prices with different shipping providers and freight forwarders. Consolidating orders can also help save on shipping fees. Additionally, optimizing packaging to reduce size and weight can minimize costs.
Overall, the shipping cost for troubleshooting a svenska import from China can vary significantly. It is crucial to consider factors such as shipping method, volume of goods, shipping route, customs duties, and taxes to ensure cost-efficiency. Seeking guidance from shipping professionals can help importers navigate the process smoothly while minimizing expenses.
Compare China and Other troubleshooting svenska Markets: Products Quality and Price,Visible and Hidden Costs
China has emerged as a major player in the global market, manufacturing a wide range of products at competitive prices. However, it is important to compare China with other markets, particularly when considering product quality and pricing, as well as visible and hidden costs.
In terms of product quality, China has made significant strides in recent years. While there are still concerns about counterfeit and low-quality products, many Chinese manufacturers have improved their quality control processes to meet international standards. However, other troubleshooting markets, such as Germany and Japan, have a long-standing reputation for producing high-quality goods across various industries. These markets maintain strict quality control measures and have developed a strong reputation for durable and reliable products.
When it comes to pricing, China undoubtedly offers competitive prices due to its low labor and production costs. This has made China an attractive destination for cost-conscious consumers and businesses seeking affordable products. On the other hand, troubleshooting markets like Sweden and Switzerland are known for their higher prices. These markets focus more on quality and precision, which often comes with a higher price tag.
Visible costs in China include the price of the product itself, which is usually lower than in troubleshooting markets. However, hidden costs can be a concern in China. These include transportation costs, import duties, and potential difficulties in resolving quality issues or intellectual property disputes. Troubleshooting markets generally have fewer hidden costs, as they prioritize customer satisfaction and offer robust customer support and warranties.
In conclusion, while China has made substantial progress in product quality and offers competitive pricing, it is important to consider other troubleshooting markets like Germany, Japan, Sweden, and Switzerland. These markets have established themselves as leaders in producing high-quality goods, albeit at higher prices. Furthermore, hidden costs in China can be a potential drawback, whereas troubleshooting markets often provide better customer support and warranty options. Ultimately, the choice between China and other markets will depend on the specific needs and priorities of consumers and businesses.
Understanding Pricing and Payment Terms for troubleshooting svenska: A Comparative Guide to Get the Best Deal
Pricing and payment terms are crucial aspects to consider when seeking the best deal for troubleshooting services. By understanding these elements, one can make informed decisions and secure the most cost-effective solution. This comparative guide highlights important considerations for negotiating pricing and payment terms.
When evaluating pricing, it is essential to compare quotes from multiple service providers. This allows for a better understanding of the market rates and helps identify any substantial variations. It is important to note that the lowest price may not always guarantee the best service, as quality and expertise should also be factored into the decision.
Additionally, when reviewing pricing, it is advisable to inquire whether it is fixed or variable. Fixed pricing provides certainty as the cost remains constant throughout the duration of the service agreement. On the other hand, variable pricing may fluctuate based on factors such as the complexity of the issue or the time spent on troubleshooting. Understanding these pricing structures enables clients to choose the approach that aligns with their budget and preferences.
Payment terms are another crucial factor to consider. It is common for troubleshooting services to require an upfront payment or a deposit before work commences. This practice ensures commitment from both parties and protects the service provider from incurring any losses. However, it is important to confirm whether this payment is refundable, particularly if the service is not satisfactory or if the issue remains unresolved.
Flexible payment options can also be advantageous. Some troubleshooting service providers may offer installment plans or milestone-based payments, which could help manage cash flow and expenses more effectively. It is important to discuss and negotiate these terms with the service provider before finalizing any agreement.
Lastly, it is crucial to review the cancellation and refund policy, as unforeseen circumstances may arise. Understanding the potential liabilities involved and any applicable fees for cancellation or rescheduling can help prevent unexpected financial consequences.
In conclusion, understanding pricing and payment terms is essential for securing the best deal when seeking troubleshooting services. By comparing quotes, analyzing pricing structures, and negotiating payment terms, individuals can make informed decisions to optimize both cost and quality. Pivotal aspects to assess include fixed or variable pricing, upfront payments, refund policies, and flexible payment options. By utilizing these considerations, individuals can ensure they receive the most cost-effective and satisfactory troubleshooting services.
Chinese Regulations and Industry Standards Certifications for troubleshooting svenska,Import Regulations and Customs for troubleshooting svenska from China
When it comes to troubleshooting svenska, understanding Chinese regulations and industry standards certifications is crucial. China has implemented several regulations and standards in various sectors to ensure product quality and safety. Here, we will focus on troubleshooting svenska and importing regulations from China.
In China, there are several industry standards certifications related to troubleshooting svenska that one should be aware of. For example, the China Compulsory Certification (CCC) is mandatory for certain products, including electrical and electronic devices. This certification ensures that the product meets safety requirements and complies with Chinese standards.
Additionally, Troubleshooting Svenska products may also need to adhere to specific industry standards certifications. For instance, if it is a telecommunication equipment, it should conform to China’s Telecommunication Equipment Certification Center (TENAA) standards. Similarly, troubleshooting Svenska products related to environmental protection may require certification from the China Certification Center for Environmental Labeling Products (CCELP).
Importing troubleshooting svenska from China also requires an understanding of the country’s import regulations and customs procedures. Importers need to follow Chinese customs regulations, including submitting the necessary documentation such as invoices, packing lists, and certificates of origin. It is essential to comply with China’s Customs Law and Regulations on Import and Export Duties to ensure smooth importation.
Furthermore, special attention should be given to product labeling requirements for troubleshooting svenska. Chinese labeling standards necessitate that all products have labels in Chinese, providing information such as the product name, manufacturer, specifications, and warning signs if applicable.
To summarize, troubleshooting svenska products must adhere to relevant industry standards certifications in China, such as CCC, TENAA, or CCELP. Importers should also understand Chinese import regulations, including proper documentation and labeling requirements. By staying informed and complying with Chinese regulations and industry standards, importers can ensure a hassle-free importation process for troubleshooting svenska products from China.
Sustainability and Environmental Considerations in troubleshooting svenska Manufacturing
Sustainability and environmental considerations in troubleshooting the manufacturing process are crucial in order to minimize negative impacts on the environment and to ensure long-term viability of the manufacturing industry. By integrating sustainable practices into the troubleshooting process, manufacturers can reduce waste, energy consumption, and emissions while maximizing resource efficiency.
One important aspect of sustainable troubleshooting is identifying and addressing the root causes of manufacturing issues. By understanding the underlying problems, manufacturers can develop solutions that not only fix the immediate issue but also improve overall efficiency and reduce environmental impacts. For example, if a manufacturing line is experiencing frequent breakdowns, troubleshooting should examine whether outdated machinery is the source of the problem. Replacing old equipment with energy-efficient and environmentally friendly alternatives can decrease energy consumption and minimize waste.
Another key consideration is waste management. Troubleshooting should focus on identifying areas where waste is generated and develop strategies to reduce, reuse, or recycle it. This may include optimizing material usage, implementing recycling programs, or finding innovative ways to repurpose waste materials. By minimizing waste generation, manufacturers can decrease their environmental footprint, conserve resources, and potentially reduce production costs.
Energy efficiency is another crucial aspect of sustainable troubleshooting. Identifying energy-intensive processes or equipment and finding ways to optimize energy usage can lead to significant reductions in energy consumption and greenhouse gas emissions. Troubleshooting should explore energy-saving technologies, equipment upgrades, and process modifications to minimize energy waste and promote sustainable manufacturing practices.
Furthermore, sustainable troubleshooting should consider the use of environmentally friendly materials and chemicals. By choosing materials that are renewable, recyclable, or biodegradable, manufacturers can reduce their reliance on non-renewable resources and minimize the release of hazardous substances into the environment. This approach also includes analyzing the potential environmental impacts of the manufacturing process, such as air and water pollution, and implementing measures to mitigate them.
In conclusion, sustainability and environmental considerations in troubleshooting manufacturing processes are essential for minimizing environmental impacts, conserving resources, and ensuring long-term viability. By addressing the root causes of issues, optimizing waste management, promoting energy efficiency, and using environmentally friendly materials, manufacturers can achieve sustainable troubleshooting outcomes that benefit both their business and the planet.
List The Evolution history of “troubleshooting svenska”
Troubleshooting svenska has undergone significant evolution throughout history. From its early beginnings to its current state, this troubleshooting method has adapted and developed to meet the needs of users in Sweden.
The concept of troubleshooting in Sweden can be traced back to the early days of technology and machinery. In the pre-digital era, troubleshooting mainly involved identifying and fixing mechanical issues. Skilled technicians were employed to identify and resolve problems in complex systems such as automobiles and industrial machinery.
With the advent of computers and advanced electronics, troubleshooting techniques started to evolve. In the 1980s, as personal computers became more prevalent, troubleshooting svenska expanded to include software-related problems. It encompassed identifying software bugs, compatibility issues, and hardware-software conflicts. Manuals and technical support helplines emerged to assist users in troubleshooting their computer issues.
The evolution of technology in the late 1990s and early 2000s led to a more user-friendly approach to troubleshooting svenska. As graphical user interfaces became more intuitive, troubleshooting methods shifted towards self-help solutions. Companies began creating extensive knowledge bases and FAQs, providing users with step-by-step instructions for resolving common issues. Online forums and communities also played a crucial role in troubleshooting, allowing users to share their experiences and help each other.
In recent years, troubleshooting methods have further evolved with the rise of mobile devices and internet connectivity. Troubleshooting svenska is now readily accessible through mobile apps and online platforms. Many companies offer remote troubleshooting services, allowing technicians to diagnose and resolve issues remotely.
The future of troubleshooting svenska is likely to be shaped by emerging technologies such as artificial intelligence and virtual reality. AI-powered chatbots and virtual assistants are already being utilized to provide immediate troubleshooting support. These advancements will continue to streamline the troubleshooting process and offer more personalized solutions.
In conclusion, troubleshooting svenska has transformed from mechanical problem-solving to encompass a wide range of digital and technological challenges. Its evolution has been driven by advancements in technology, user-friendly interfaces, and the proliferation of online resources. The future of troubleshooting svenska is promising, with the potential for even more advanced and personalized assistance.
The Evolution and Market Trends in troubleshooting svenska Industry
The troubleshooting industry has undergone significant evolution and witnessed various market trends over the years, catering to the needs of the Swedish market. With the advent of technology and the increasing complexity of systems and equipment, troubleshooting has transformed into a specialized field.
One noticeable evolution in the troubleshooting industry is the shift from traditional manual methods to automated solutions. Previously, troubleshooting involved manual inspection, identification of faults, and fixing them manually. However, with the introduction of advanced diagnostic tools and computerized systems, troubleshooting has become more efficient and accurate. Automated troubleshooting systems can quickly identify faults, analyze data, and provide solutions in a fraction of the time it would take a person to manually troubleshoot the issue.
Moreover, there has been a growing trend towards remote troubleshooting services. With the advancement in telecommunication technologies, troubleshooting experts can now remotely access systems and devices to diagnose and solve problems. This trend has gained popularity in the Swedish market due to its convenience and cost-effectiveness. It enables businesses to save time and resources by avoiding onsite visits of troubleshooters.
Another trend that has emerged in the troubleshooting industry is the integration of artificial intelligence (AI) and machine learning (ML). AI-powered troubleshooting systems can analyze vast amounts of data, detect patterns, and predict potential issues. ML algorithms can learn from past troubleshooting experiences and improve their accuracy over time. This trend is revolutionizing the troubleshooting industry by providing proactive solutions and reducing downtime for businesses.
Furthermore, sustainability has become a key concern in the Swedish troubleshooting industry. There is a growing demand for eco-friendly and energy-efficient troubleshooting solutions. Companies are now focusing on developing troubleshooting tools that minimize waste, reduce energy consumption, and adhere to environmental regulations. This trend reflects the increasing importance of environmental consciousness in the market.
In conclusion, the troubleshooting industry in Sweden has evolved significantly, moving from manual methods to automated, remote, and AI-powered solutions. The market trends highlight the increasing reliance on technology, sustainability, and the need for efficient and cost-effective troubleshooting services. As technology continues to advance, the troubleshooting industry is expected to further transform to meet the evolving demands of the market.
Custom Private Labeling and Branding Opportunities with Chinese troubleshooting svenska Manufacturers
Chinese manufacturers offer numerous opportunities for custom private labeling and branding. They have extensive experience in manufacturing a variety of products and are open to working with businesses to create their own unique brands.
One advantage of partnering with Chinese manufacturers for custom private labeling is the ability to customize product designs and specifications. These manufacturers have a wide range of capabilities and can produce goods according to specific requirements, such as design, size, color, and functionality. Businesses can collaborate with manufacturers to create products that align with their brand’s image and meet the needs of their target market.
In addition, Chinese manufacturers often provide branding services that include custom packaging, labeling, and logo design. They understand the importance of creating a strong brand identity and can help businesses design visually appealing and professional packaging materials. Custom packaging helps differentiate products from competitors and enhances brand recognition.
Moreover, partnering with Chinese manufacturers can offer cost advantages. Chinese manufacturers generally have lower labor and production costs compared to manufacturers in other countries. This allows businesses to have custom private labeling and branding solutions at a more affordable price point, enabling them to compete effectively in the market.
To initiate a partnership with a Chinese manufacturer, businesses should conduct thorough research and due diligence. It is crucial to find reliable and reputable manufacturers who have a track record of delivering high-quality products. Reading customer reviews, examining product samples, and communicating directly with manufacturers can help ensure a successful collaboration.
In conclusion, Chinese manufacturers offer exciting opportunities for custom private labeling and branding. Their manufacturing expertise, customization capabilities, branding services, and cost advantages make them ideal partners for businesses looking to create their own unique brands.
Tips for Procurement and Considerations when Purchasing troubleshooting svenska
When it comes to procuring troubleshooting services, there are a few key considerations that can help ensure a successful purchase. Here are some tips to keep in mind:
1. Identify your specific needs: Before purchasing troubleshooting services, clearly outline the specific problems you are facing and the areas where you need support.
2. Define the scope of work: Clearly communicate your requirements and expectations to potential service providers. This will help in obtaining accurate quotes and ensuring that all parties are aligned on the scope of work.
3. Conduct market research: Research and identify potential service providers who specialize in troubleshooting services. Look for providers that have experience in your industry and positive customer reviews.
4. Request proposals: Reach out to shortlisted service providers and request detailed proposals. Ask for information on their methodologies, timelines, support options, and pricing structures.
5. Evaluate expertise and experience: Assess the expertise and experience of potential service providers in troubleshooting the specific issues you are facing. Request case studies or client references to evaluate their track record.
6. Consider cost-effectiveness: While cost is an important factor, remember that the cheapest option might not always be the best. Compare the prices offered by different providers, but also consider the quality of service and the potential impact on your business.
7. Assess customer support: Troubleshooting services often require ongoing support. Inquire about the level of customer support each provider offers, including response times and availability for urgent issues.
8. Check for scalability: If your troubleshooting needs are likely to grow in the future, consider whether the service provider can scale their services to accommodate your evolving requirements.
9. Review terms and conditions: Carefully review the contract terms and conditions, including payment terms, termination clauses, and any limitations of liability. Seek legal advice if necessary.
10. Seek feedback: Engage with current or past clients of the potential service providers to gain insights into their experience with the troubleshooting services offered.
By considering these tips when purchasing troubleshooting services, you can increase the likelihood of selecting a knowledgeable and reliable service provider that can effectively address your specific needs.
FAQs on Sourcing and Manufacturing troubleshooting svenska in China
Q: Vad är syftet med att söka och tillverka felsökning i Kina?
A: Att söka och tillverka felsökning i Kina syftar till att hitta och lösa problem som kan uppstå under tillverkningsprocessen i kinesiska fabriker. Det kan vara allt från kvalitetsproblem till logistikrelaterade utmaningar.
Q: Varför väljer företag att söka och tillverka felsökning i Kina?
A: Företag väljer ofta att söka och tillverka felsökning i Kina på grund av landets låga produktionskostnader och höga kapacitet. Kina är känt för sin stora industriella infrastruktur och det finns en mängd erfarna och specialiserade tillverkningsenheter där. Det kan vara mer kostnadseffektivt och tidsbesparande att åtgärda produktionsproblem direkt på plats istället för att förlita sig på långväga kommunikation.
Q: Vilka vanliga problem kan uppstå vid tillverkning i Kina?
A: Några vanliga problem som kan uppstå vid tillverkning i Kina inkluderar kvalitetskontrollproblem, brist på överensstämmelse med specifikationer, språkbarriärer, leveranstider och logistiska utmaningar. Det kan också finnas frågor om etiska arbetsförhållanden eller immaterialrättskränkningar.
Q: Hur kan man göra sourcing och tillverkning felsökning i Kina mer framgångsrikt?
A: För att göra sourcing och tillverkning felsökning i Kina mer framgångsrikt är det viktigt att etablera tydlig och öppen kommunikation med fabriken. Att ha en representant på plats i Kina kan vara fördelaktigt för att kunna övervaka tillverkningsprocessen och lösa problem direkt. Att arbeta med betrodda och pålitliga tillverkare, genomföra noggranna kvalitetskontroller och följa upp noggrant är också viktiga faktorer för att öka framgångsgraden.
Q: Finns det risker med att söka och tillverka felsökning i Kina?
A: Ja, det finns vissa risker med att söka och tillverka felsökning i Kina. Exempelvis kan språkbarriärer och kulturella skillnader leda till missförstånd och kommunikationsproblem. Kvalitetskontroll kan vara utmanande och det kan finnas risk för förfalskningar eller piratkopior. Dessutom kan politiska eller miljömässiga faktorer påverka tillverkningen och leveransen. Det är därför viktigt att noggrant utvärdera och övervaka tillverkningsprocessen för att minimera dessa risker.
Why contact sourcifychina.com get free quota from reliable troubleshooting svenska suppliers?
Sourcifychina.com may receive a free quota from reliable troubleshooting Swedish suppliers for several reasons. Firstly, sourcifychina.com operates as a platform that connects businesses or individuals with suppliers in China. By offering a free quota, they aim to attract customers and incentivize them to use their platform for sourcing products or services from Swedish suppliers. This strategy helps sourcifychina.com establish a competitive advantage and gain a larger customer base.
Secondly, by partnering with reliable troubleshooting Swedish suppliers and offering a free quota, sourcifychina.com can build trust and credibility among potential customers. The free quota demonstrates that sourcifychina.com has already vetted and established relationships with reputable Swedish suppliers, ensuring that customers receive high-quality and reliable products or services.
Moreover, the free quota also serves as a marketing tactic to promote sourcifychina.com as a valuable resource for sourcing from Sweden. It allows customers to experience the benefits of working with sourcifychina.com, such as time-saving, cost-efficiency, and access to a wide range of products or services. This firsthand experience may encourage customers to continue using sourcifychina.com for their future sourcing needs, even beyond the free quota.
Lastly, offering a free quota may enable sourcifychina.com to gather feedback and data from customers. This information can be used to improve their platform, enhance supplier partnerships, and refine their sourcing process. By continuously improving their services based on customer feedback, sourcifychina.com can increase customer satisfaction and strengthen their reputation as a reliable sourcing platform.
In conclusion, sourcifychina.com offers a free quota from reliable troubleshooting Swedish suppliers as a strategic approach to attract customers, build trust, promote their platform, and gather valuable feedback for continuous improvement.