Introduce about wire edm parts guide,Qulity,Cost,Supplier,Certification,Market,Tips,FAQ
Wire EDM (Electrical Discharge Machining) is a highly precise manufacturing process that uses electrically charged wire to remove material from a workpiece. In this guide, we will provide an overview of Wire EDM parts, covering aspects such as quality, cost, suppliers, certification, market, and tips. Here’s a concise summary within 300 words:
When it comes to quality, Wire EDM parts offer exceptional precision and accuracy. The process ensures that intricate and complex shapes can be achieved with tight tolerances, making it suitable for industries such as aerospace, automotive, and medical. The absence of cutting forces also minimizes the risk of workpiece distortion.
In terms of cost, Wire EDM parts can vary depending on the complexity of the design and the material being used. However, due to its high precision and efficiency, Wire EDM often proves to be cost-effective in the long run. It reduces the need for multiple setups, eliminates the need for expensive tooling, and reduces material waste.
Finding reliable suppliers for Wire EDM parts is crucial. It’s essential to partner with experienced manufacturers who have state-of-the-art equipment and a proven track record in producing high-quality parts. Checking for certifications such as ISO 9001 can ensure that the supplier adheres to the highest quality standards.
The market for Wire EDM parts is continuously growing, driven by increasing demand for complex and high-precision components in various industries. This growth is fueled by advancements in technology and the need for efficient and precise manufacturing processes.
When working with Wire EDM parts, it is essential to keep a few tips in mind. Ensuring proper machine maintenance, selecting the appropriate wire diameter, and optimizing cutting parameters can help improve the quality and efficiency of the process.
Frequently Asked Questions (FAQ) about Wire EDM parts may include queries about the maximum size of parts that can be machined, the types of materials that can be used, the surface finish achievable, etc. Addressing these concerns can help customers make informed decisions and understand the capabilities of Wire EDM.
In conclusion, Wire EDM parts offer high-quality, precise, and efficient solutions for various industries. By partnering with reliable suppliers and considering tips to optimize the process, customers can benefit from the advantages offered by Wire EDM technology.
Types of wire edm parts
Wire electrical discharge machining (EDM), also known as wire cutting or wire erosion, is a manufacturing process that uses a thin wire electrode to precisely cut or shape complex parts and components. This technique is widely used in various industries, including aerospace, automotive, medical, and electronics. There are several types of wire EDM parts that can be produced using this process.
1. Prototypes: Wire EDM is commonly used for prototyping due to its precision and ability to create intricate shapes. It allows manufacturers to quickly and accurately produce prototypes of components, including gears, connectors, and electronic housings, before starting mass production.
2. Tooling components: Wire EDM is widely used in the production of tooling components, such as dies and molds. The process can create complex and precise cavities and contours essential for manufacturing various products.
3. Aerospace components: The aerospace industry requires high-precision parts with complex shapes and tight tolerances. Wire EDM is used to produce components such as turbine blades, engine components, and aircraft structural parts.
4. Medical implants and devices: Wire EDM is utilized to produce medical implants and devices, where high precision and accuracy are crucial. It allows the manufacturing of complex shapes, such as surgical instruments, dental tools, and orthopedic implants.
5. Electronics: Wire EDM is extensively used in the electronics industry to manufacture components like connectors, small gears, microcomponents, and contact springs. It helps in creating precise and intricate patterns required in modern electronic devices.
6. Automotive parts: Wire EDM is employed in the production of automotive parts, including gears, pistons, fuel injection nozzles, and brake components. It allows manufacturers to create intricate shapes and profiles that meet the automotive industry’s stringent requirements.
7. Jewelry: Wire EDM is increasingly used in the jewelry industry for intricate and precise cutting of precious metals like gold and silver. It enables the creation of complex and detailed designs that are difficult to achieve using traditional methods.
Overall, wire EDM is a versatile and reliable manufacturing process used to produce a wide variety of parts and components. Its ability to create complex shapes, tight tolerances, and intricate details makes it an ideal choice for various industries requiring high-precision components.
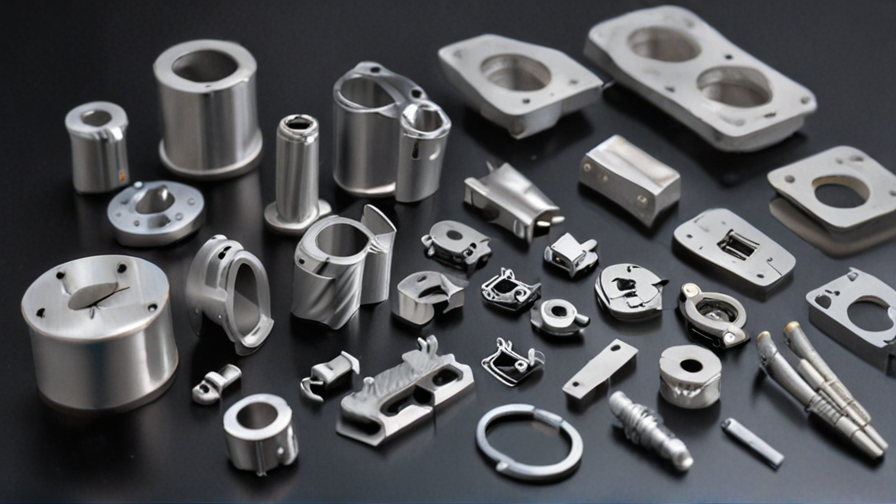
Pros and Cons of Using wire edm parts
Wire EDM, or Electrical Discharge Machining, is a widely used process in various industries for precision cutting and shaping of metal parts. It involves the use of a thin wire electrode to create electrical sparks that erode the workpiece material. While there are numerous advantages to using wire EDM parts, there are also some drawbacks to consider.
Let’s start with the pros. One major advantage of wire EDM is its ability to cut complex shapes with high accuracy and precision. The process can achieve tight tolerances and produce intricate details that may be challenging to achieve through traditional machining methods. This makes wire EDM perfect for producing parts for industries like aerospace, automotive, and medical, where precise dimensions are crucial.
Secondly, wire EDM can cut through a vast range of materials, from soft metals like aluminum to hard materials like titanium. Unlike traditional cutting methods that encounter difficulties with hard materials, wire EDM can effectively cut through them without causing excessive tool wear or heat-affected zones.
Another benefit of wire EDM is the absence of tool contact with the workpiece. Because the cutting is done using electrical sparks, the wire electrode doesn’t physically touch the material, reducing the risk of tool wear and damage. This allows for long cutting runs without the need for frequent tool replacement.
Additionally, wire EDM is a non-contact process, meaning there is minimal force applied to the workpiece. This makes it suitable for fragile materials or parts with complex geometries that cannot withstand the pressure of traditional machining.
On the other hand, there are also some limitations and disadvantages to consider when using wire EDM. For starters, the process is relatively slow compared to other cutting methods. It may require longer machining times to complete a part, which can impact production schedules and overall efficiency.
Wire EDM also produces a tapered cut, meaning the part will have slight draft angles. While this may not be desirable for all applications, it can be compensated for during the design phase.
Another drawback is the wire EDM’s limitation in cutting thick materials. As the wire electrode erodes the material, it generates a narrow kerf width, making it less suitable for cutting parts with significant thicknesses. For such cases, alternative cutting methods may be more appropriate.
Lastly, wire EDM can be an expensive process due to the high cost of equipment, consumables, and maintenance. Additionally, the process requires skilled operators who are knowledgeable in setting up parameters and programming.
In conclusion, wire EDM offers various advantages such as high precision, versatility of materials, non-contact cutting, and complex shape capabilities. However, it also has limitations in terms of speed, taper cuts, cutting thick materials, and cost considerations. Therefore, it is essential to carefully evaluate the specific requirements of the project before choosing wire EDM as the machining method.
wire edm parts Reference Specifications (varies for different product)
Wire EDM (Electrical Discharge Machining) parts are utilized in various industries, ranging from aerospace and automotive to medical and electronics. These parts are essential for precise and efficient machining operations, offering high accuracy and intricate detailing. The reference specifications for wire EDM parts may vary depending on the specific product, but there are some common characteristics to consider.
Firstly, the material used for wire EDM parts can vary, with popular choices including steel, aluminum, copper, brass, and titanium. The selection of material depends on the application requirements, such as mechanical strength, conductivity, corrosion resistance, or light weight.
The dimensions and tolerances of wire EDM parts are crucial, as they directly influence the part’s functionality and fit. These specifications are typically specified in terms of length, width, height, and geometry, and can range from a few millimeters to larger dimensions.
Surface finish is another important aspect of wire EDM parts, and it is commonly measured in Ra (roughness average) or Rz (mean roughness depth) values. The required surface finish may differ based on the application, often ranging from Ra 0.8 to Ra 3.2 micrometers.
Precision of wire EDM parts is achieved by employing advanced technologies and high-quality control measures. Tight tolerances, typically in the range of +/- 0.01mm to +/- 0.05mm, ensure the desired accuracy and functionality of the component.
Furthermore, wire EDM parts often require additional treatments, such as heat treatment, plating, coating, or deburring, to enhance their mechanical properties, resist wear, or improve their aesthetic appearance.
It is essential to consider the specific requirements of the product when manufacturing wire EDM parts. This includes factors such as the intended application, environmental conditions, load-bearing capacity, and regulatory compliance.
To ensure consistency and quality, wire EDM parts undergo rigorous inspection at various stages of production. This may involve dimensional measurement using precision instruments, such as calipers, micrometers, or CMMs (coordinate measuring machines).
In summary, wire EDM parts are vital components used in a wide range of industries. They are characterized by varying specifications, including material selection, dimensional tolerances, surface finish, precision, and additional treatments. By adhering to these specifications, manufacturers can produce wire EDM parts that meet the requirements of the specific application.
Applications of wire edm parts
Wire EDM (Electrical Discharge Machining) is a process used to cut complex shapes and designs from metals and alloys with precision and accuracy. Wire EDM parts find applications across various industries, including:
1. Aerospace: Wire EDM parts are extensively used in aerospace applications, such as the production of turbine blades, engine components, fuel system parts, and various intricate shapes required for aircraft structures. The process ensures high dimensional accuracy and surface finish, crucial for optimal performance and safety in aerospace systems.
2. Medical Devices: Wire EDM is widely applied in the manufacturing of medical devices, such as surgical tools, orthopedic implants, and dental instruments. It allows for the production of intricate shapes and profiles with tight tolerances, ensuring precise fit and functionality. Additionally, it can be used to cut complex shapes in biocompatible materials like stainless steel and titanium.
3. Automotive Industry: Wire EDM parts play a key role in the automotive sector, particularly in the production of molds, die inserts, and various components requiring complex geometries. The process enables the manufacturing of precision parts with excellent surface quality, essential for automotive applications like fuel injection systems, transmission systems, and engine components.
4. Electronics and Semiconductors: The electronics industry benefits from wire EDM parts, which are utilized in the production of microelectronic components, connectors, sensors, and other intricate parts. The process allows for the creation of fine features and precise shapes required in the miniature world of electronics and semiconductors.
5. Tool and Die Making: Wire EDM is extensively employed in the fabrication of dies, molds, and tooling components required in various manufacturing processes. Its ability to cut hardened materials, such as hardened steels, carbides, and alloys, makes it an ideal choice for tool and die making applications.
6. Jewelry Making: Wire EDM is used in the production of intricate and delicate designs for jewelry. It allows for the creation of complex patterns, precise settings for gemstones, and intricate shapes that are otherwise difficult to achieve using traditional methods. The ability to work with different materials like gold, platinum, and silver makes it versatile for jewelry manufacturing.
In conclusion, wire EDM parts find applications in a wide range of industries, including aerospace, medical devices, automotive, electronics, tool and die making, and jewelry making. Its precision, accuracy, and ability to work with various materials make it an essential manufacturing process for producing intricate and complex shapes.
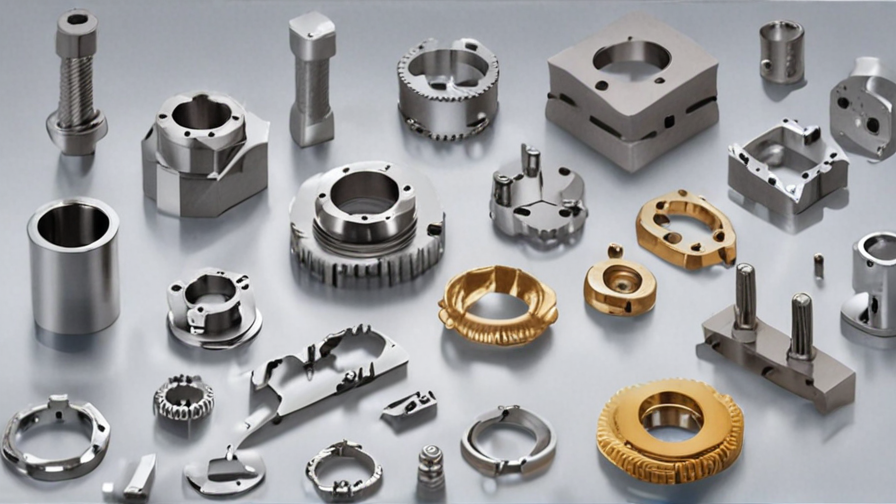
The Work Process and how to use wire edm parts
Wire electrical discharge machining (EDM), also known as wire EDM, is a process used to cut complex shapes and intricate patterns in metal components. It involves the use of a thin wire electrode that is heated through an electric current to create sparks that erode the material.
The work process of wire EDM begins with the preparation of the component to be machined. The part is securely mounted onto the machine’s worktable, ensuring proper alignment and stability. The wire electrode is then threaded through the workpiece, guided by computer-controlled systems to accurately position it.
Once everything is set up, the wire EDM machine begins the machining process. A dielectric fluid, usually deionized water, is continuously pumped between the wire and the workpiece. This fluid serves as a coolant and removes the eroded material from the cutting area.
The wire electrode is slowly fed into the workpiece, and controlled electrical discharges occur between the wire and the material. These discharges vaporize and erode the metal, creating the desired shape or pattern. The computer-controlled system ensures precise movement of the wire, allowing for intricate and precise cuts.
Throughout the cutting process, the dielectric fluid is constantly replenished to maintain a stable machining environment and remove debris. After completion, the wire EDM machine automatically stops, and the finished part can be removed from the worktable.
To use wire EDM parts effectively, it is essential to consider a few factors. First, careful selection of the wire electrode is necessary, as it should be compatible with the material being machined. Different wire materials, such as brass, tungsten, or copper, offer varying capabilities and performance.
Additionally, the proper alignment and mounting of the workpiece are crucial for accurate and successful machining. Adequate support and fixation ensure stable movement and prevent any errors or deviations in the final part.
Furthermore, maintaining appropriate dielectric fluid levels and quality is essential to ensure optimal cutting conditions. Regular monitoring and maintenance of the machine’s systems are necessary to replace worn wires, clean the electrodes, and ensure smooth operation.
In conclusion, wire EDM is a precise and versatile machining process used to cut intricate shapes and patterns in metal components. Through careful preparation, proper tool selection, and appropriate machine maintenance, wire EDM parts can be effectively used to achieve high-quality and accurate results in manufacturing processes.
Quality Testing Methods for wire edm parts and how to control the quality
When it comes to quality testing of wire EDM (Electrical Discharge Machining) parts, there are several methods that can be employed to ensure the desired level of quality and to effectively control it.
1. Visual Inspection: This is the simplest and most basic method of quality testing. It involves visually examining the wire EDM parts for any visible defects such as scratches, surface irregularities, or any other physical imperfections. This can be done with the naked eye or with the help of magnifying tools.
2. Dimensional Inspection: Precision is crucial in wire EDM parts, and therefore, dimensional accuracy must be checked. This can be done using various measurement tools such as calipers, micrometers, or coordinate measuring machines (CMMs). By comparing the measured dimensions with the specified tolerances, any deviations can be identified and controlled.
3. Surface Roughness Measurement: Wire EDM parts often require a specific level of surface finish. Surface roughness measuring devices, such as profilometers, are used to evaluate the smoothness of the part’s surfaces. These measurements can be compared with the required specifications to ensure compliance.
4. Hardness Testing: Wire EDM parts may undergo changes in their hardness due to the thermal processes involved. This can be assessed using hardness testing methods such as Rockwell or Vickers hardness tests. The measured hardness values can then be compared with the required hardness specifications to maintain quality control.
5. Non-Destructive Testing (NDT): NDT techniques, such as liquid penetrant testing or ultrasonic testing, can be employed to detect any internal defects or flaws in the wire EDM parts without damaging them. This helps ensure that critical flaws are identified and controlled early in the production process.
To control the quality of wire EDM parts effectively, it is important to establish clear quality control procedures and document them. This includes specifying the acceptable tolerances, surface finishes, hardness, and other requirements. Regular calibration and maintenance of inspection equipment, as well as proper training of operators, are also vital for consistent quality control. In addition, establishing a feedback loop with the wire EDM machine operators can help monitor and control the quality in real-time.
By implementing these quality testing methods and maintaining stringent quality control practices, wire EDM parts can be produced to meet the desired specifications and ensure customer satisfaction.
wire edm parts Sample Policy and Post-Purchase Considerations for wire edm parts from China
Sample Policy and Post-Purchase Considerations for Wire EDM Parts from China:
Sample Policy:
1. Request for Samples: Before placing a bulk order, it is recommended to request samples from the Chinese wire EDM parts manufacturer. This enables you to assess the quality, accuracy, and compatibility of the parts with your requirements.
2. Sample Evaluation: Thoroughly examine the samples for dimensional accuracy, material quality, surface finish, and functionality. Evaluate if they meet your expectations and match the specifications provided by the manufacturer.
3. Communication with Supplier: Discuss any concerns or modifications required with the manufacturer regarding the samples. Effective communication is crucial to ensure accurate product specifications and to minimize any potential issues during mass production.
4. Sample Approval: Upon complete satisfaction with the sample quality, provide explicit approval to proceed with mass production. Clarify the lead time, ordering quantity, and payment terms for the bulk order.
Post-Purchase Considerations:
1. Packaging and Shipment: Confirm that the wire EDM parts are properly packaged to prevent any damage during transit. Verify if the packaging meets international shipping standards. Inquire about the chosen shipment method and track the delivery progress.
2. Quality Control: Inspect the received goods for any defects, verifying their conformity to the approved samples. Conduct in-depth quality control checks based on agreed specifications, including dimensions, tolerances, surface finishes, and material composition.
3. Documentation: Ensure that all necessary documents, such as invoices, packing lists, and customs declarations, are provided by the supplier. These documents are crucial for smooth customs clearance and record-keeping.
4. Feedback and Warranty: Provide feedback on the product quality and overall experience to the manufacturer. In case of any nonconformities or issues, promptly communicate with the supplier to resolve them. Discuss warranty terms and conditions to protect your investment.
In conclusion, when importing wire EDM parts from China, it is crucial to follow a sample policy that includes evaluating samples, effective communication with the supplier, and providing explicit approval for mass production. Additionally, post-purchase considerations involve ensuring proper packaging, conducting quality control checks, obtaining necessary documentation, and providing feedback for warranty purposes. By following these guidelines, you can minimize risks and ensure a successful procurement process.
Sourcing wire edm parts from China: Opportunities, Risks, and Key Players
Sourcing wire EDM (Electrical Discharge Machining) parts from China presents both opportunities and risks for businesses. China is known for its cost-effective manufacturing capabilities, making it an attractive option for companies looking to reduce production costs.
One major opportunity of sourcing wire EDM parts from China is the potential for substantial cost savings. The lower labor and operational costs in China can result in significantly lower production costs compared to sourcing from other countries. This can be particularly advantageous for businesses operating in price-sensitive industries.
Moreover, China has a well-developed manufacturing infrastructure and a vast network of suppliers, providing a wide range of wire EDM parts options. This allows businesses to find the precise components they need, often at competitive prices, enabling them to meet their production requirements efficiently.
However, there are also risks associated with sourcing wire EDM parts from China. Quality control is one of the primary concerns, as there have been instances of substandard or counterfeit parts being supplied. It is crucial for businesses to thoroughly vet potential suppliers, conduct on-site inspections if possible, and implement a rigorous quality assurance process to mitigate these risks.
Another risk is intellectual property infringement. China has faced criticism for its lax enforcement of intellectual property laws, leading to concerns about the theft or unauthorized replication of proprietary designs or technologies. Companies should take steps to protect their intellectual property rights when sourcing wire EDM parts from China through non-disclosure agreements and applying for patents if necessary.
Key players in the wire EDM parts manufacturing industry in China include precision machining companies like Foxron Precision Metal Parts Co., Ltd., Temwell Corporation, and Royce Metal Products Limited. These companies have experience in producing wire EDM parts to international quality standards and cater to the needs of both local and international clients.
In conclusion, sourcing wire EDM parts from China offers cost-saving opportunities and access to a wide range of suppliers. However, businesses should be aware of the risks associated with quality control and intellectual property infringement and take appropriate measures to mitigate them.
How to find and select reliable wire edm parts manufacturers in China,use google search manufacturers and suppliers
To find and select reliable wire EDM parts manufacturers in China, follow the steps below:
1. Start by conducting a Google search using relevant keywords such as “wire EDM parts manufacturers in China” or “reliable wire EDM parts suppliers China.”
2. Browse through the search results and visit the websites of manufacturers or suppliers that appear reputable and professional.
3. Look for information that indicates the manufacturer’s experience, expertise, and certifications in wire EDM parts production. Ensure they have a dedicated manufacturing facility and advanced machinery.
4. Read customer reviews and testimonials, if available, to gauge the satisfaction and reliability of their products. Consider both positive and negative feedback to assess their overall reputation and reliability.
5. Check if the manufacturer provides detailed product specifications, such as materials used, tolerance levels, and quality control measures. This demonstrates transparency and commitment to producing high-quality parts.
6. Look for manufacturers who adhere to international quality standards, such as ISO 9001. This certification ensures their production processes meet necessary requirements.
7. Contact the shortlisted manufacturers and ask for samples to assess their quality firsthand. Evaluate their response time and willingness to assist you, as it reflects their commitment to customer service.
8. Inquire about their manufacturing capabilities, production capacity, lead times, and pricing structure. Assess if they can meet your specific requirements and deliver within your desired timeframe.
9. Consider visiting trade shows or exhibitions focused on manufacturing in China, as they provide an opportunity to meet potential suppliers in person and evaluate their offerings.
10. Request references from the manufacturer, and contact previous or existing customers to gain insights into their experiences and satisfaction with the supplier.
11. Finally, based on the collected information, select the manufacturer that best meets your requirements in terms of reliability, quality, capacity, pricing, and customer service.
Remember to conduct due diligence and consider multiple options before making a final decision. This process will help you find and select reliable wire EDM parts manufacturers in China.
How to check wire edm parts manufacturers website reliable,use google chrome SEOquake check if ranking in top 10M
To check the reliability of a wire EDM parts manufacturer’s website, you can follow these steps:
1. Use Google Chrome: Open the manufacturer’s website using Google Chrome as your browser. This will enable you to utilize the SEOquake tool.
2. Install SEOquake: Go to the Chrome Web Store and search for “SEOquake.” Add this extension to your browser.
3. Activate SEOquake: Once installed, activate SEOquake by clicking on its icon, usually located at the top-right corner of your browser.
4. SEOquake parameters: Click on the SEOquake icon and select “Parameters” to set preferences for the data you want to see. For assessing reliability, focus on the following parameters:
– Google Index: This indicates the number of pages indexed by Google. A higher index suggests a more established and reliable website.
– Alexa Rank: This provides an estimate of a website’s popularity. The lower the rank, the more popular and reliable the website.
– SEMrush Rank: This is determined by the website’s organic search traffic. A lower rank suggests higher website authority and reliability.
– Backlinks: Check the number of backlinks. A higher number indicates that other reliable websites link to the manufacturer’s site, enhancing credibility.
– Social Media signals: Look for Facebook likes, Twitter shares, and other social media indicators. Higher engagement reflects a more trusted online presence.
5. Analyze the results: Once you’ve set the parameters, SEOquake will display the necessary data based on the manufacturer’s website. Examine the Google index, Alexa Rank, SEMrush Rank, backlinks, and social media signals.
6. Compare with top 10M ranking: Based on the parameters, check whether the manufacturer’s website ranks within the top 10 million websites globally. A higher ranking signals better reliability.
Remember not to solely rely on SEOquake data. Consider other factors such as online reviews, customer testimonials, and certifications to thoroughly evaluate the manufacturer’s reliability.
Top 10 wire edm parts manufacturers in China with each 160 words introduce products,then use markdown create table compare
1. Suzhou Qimera Precision Machinery Co., Ltd.: With advanced wire EDM technology, Qimera manufactures a wide range of precision parts including connectors, gears, and electrical components. Their products are known for their high accuracy and excellent surface finish, making them suitable for industries such as electronics and automotive.
2. Kunshan Hopeful Metal Products Co., Ltd.: Specializing in wire EDM parts for the medical and aerospace sectors, Hopeful Metal delivers superior quality components such as surgical instruments, implantable devices, and aircraft engine parts. Their products undergo rigorous quality control measures to ensure customer satisfaction.
3. Shanghai Meiman Electro-mechanical Equipment Co., Ltd.: Meiman is a leading wire EDM parts manufacturer, offering diverse components for diverse industries. Their range includes mold inserts, tooling accessories, and robotic parts. Meiman’s parts showcase exceptional precision and durability, meeting the demands of customers worldwide.
4. Dongguan City Desheng Light Industrial Machinery Co., Ltd.: Desheng produces wire EDM parts that find application in various sectors such as automotive, machinery manufacturing, and electronics. Their catalog comprises precision gears, mechanical parts, and connectors. Desheng focuses on delivering reliable and cost-effective solutions to their customers.
5. Shenzhen Yize Machinery Co., Ltd.: Known for their expertise in wire EDM parts manufacturing, Yize provides components for automotive, medical, and communication industries. Their product range includes precision punches, dies, and injection mold parts. Yize’s commitment to quality, precision, and customer satisfaction sets them apart.
| Manufacturer | Specialization | Notable Products |
| — | — | — |
| Suzhou Qimera Precision Machinery Co., Ltd. | Electronics, Automotive | Connectors, Gears, Electrical Components |
| Kunshan Hopeful Metal Products Co., Ltd. | Medical, Aerospace | Surgical Instruments, Implantable Devices, Aircraft Engine Parts |
| Shanghai Meiman Electro-mechanical Equipment Co., Ltd. | Multiple Industries | Mold Inserts, Tooling Accessories, Robotic Parts |
| Dongguan City Desheng Light Industrial Machinery Co., Ltd. | Automotive, Machinery Manufacturing, Electronics | Precision Gears, Mechanical Parts, Connectors |
| Shenzhen Yize Machinery Co., Ltd. | Automotive, Medical, Communication | Precision Punches, Dies, Injection Mold Parts |
6. Wuxi Haorui Precision Machinery Co., Ltd.: Haorui specializes in wire EDM parts for the mold and tool industry. Their product lineup comprises mold inserts, die blocks, and punch holders. With a focus on precision and reliability, Haorui serves customers worldwide.
7. Ningbo Beilun Xinkai Mold Parts Co., Ltd.: Xinkai Mold Parts is a leading manufacturer of wire EDM parts for the molding industry. They offer a wide range of components, including ejector pins, core pins, and latch lock sets. Xinkai’s products are known for their durability and optimal performance.
8. Dongguan Kangding Metal Technology Co., Ltd.: Kangding Metal Technology is renowned for its wire EDM parts used in precision machinery and tooling. Their range includes custom-made spacers, fixtures, and jigs. Kangding’s commitment to quality and precision makes them a trusted manufacturer in the industry.
9. Suzhou Baoma Numerical Control Equipment Co., Ltd.: Baoma specializes in wire EDM parts for the electronics and automobile industries. Their catalog includes precision connectors, terminals, and sensors. Baoma’s products are widely recognized for their accuracy, durability, and electrical performance.
10. Hangzhou Aoyi Tech Co., Ltd.: Aoyi Tech offers wire EDM parts for multiple industries, including automotive, aerospace, and energy. Their product range includes turbine blades, impellers, and electronic enclosures. Aoyi Tech’s parts demonstrate high dimensional accuracy and reliability.
In summary, these top 10 wire EDM parts manufacturers in China excel in producing high-quality components catering to diverse industries. Each manufacturer brings unique capabilities and product specialties, ensuring a wide range of options to suit customers’ specific requirements.
Background Research for wire edm parts manufacturers Companies in China, use qcc.com archive.org importyeti.com
Wire electrical discharge machining (EDM) is a manufacturing process that uses electrical discharges to shape and cut metal parts with high precision. China is known for its vast manufacturing capabilities, including wire EDM parts manufacturers. In this background research, three websites will be explored to gain insight into wire EDM parts manufacturers in China: qcc.com, archive.org, and importyeti.com.
Qcc.com is a comprehensive business information platform that provides detailed company information, including contact details, registration information, and creditworthiness of Chinese companies. By searching for “wire EDM parts manufacturers” on qcc.com, valuable information about companies operating in this field, such as their size, location, and specialization, can be obtained.
Archive.org is a digital archive that stores snapshots of web pages over time. It can be used to access historical information about wire EDM parts manufacturers in China. By looking at past versions of manufacturer websites, changes in their capabilities, product offerings, and market presence can be identified, providing insights into the company’s evolution.
Importyeti.com is a database that provides import and export data for global manufacturers, including those in China. Utilizing the platform, one can gather import data related to wire EDM parts, such as the quantity, frequency, and destination of shipments. This data can help identify reliable and high-demand wire EDM parts manufacturers in China.
By combining the information from qcc.com, archive.org, and importyeti.com, a comprehensive understanding of wire EDM parts manufacturers in China can be obtained. It will enable businesses to identify potential suppliers, their capabilities, market reputation, and international trade activity.
Leveraging Trade Shows and Expos for wire edm parts Sourcing in China
Trade shows and expos can be an excellent platform for sourcing wire EDM parts from China. With the increasing popularity of these events, businesses can leverage these platforms to connect with numerous suppliers and assess the latest technologies and trends in wire EDM manufacturing.
Participating in trade shows and expos provides several benefits for sourcing wire EDM parts from China. First and foremost, these events offer an opportunity to meet face-to-face with suppliers. This direct interaction allows for the establishment of personal relationships, better understanding of suppliers’ capabilities, and building trust, which is crucial in any business partnership.
Furthermore, trade shows and expos attract a diverse range of suppliers, enabling businesses to explore multiple options within a short period. This facilitates the comparison of different suppliers, their products, and pricing, thus ensuring a better chance of finding the most suitable partner for wire EDM parts sourcing.
Additionally, these events often showcase the latest technological advancements, providing valuable insights into the wire EDM industry. This knowledge can help businesses stay updated with innovative manufacturing techniques, materials, and quality standards, ensuring that they are sourcing the most advanced and high-quality wire EDM parts.
To make the most out of trade shows and expos in China, businesses should come prepared. Prior research on potential suppliers, their reputation, and their offerings is essential, as it allows for targeted and productive conversations during the event. Moreover, companies should bring sample parts or drawings to discuss specifications, quality requirements, and potential customization options with the suppliers.
Furthermore, businesses should take advantage of networking opportunities offered by trade shows and expos. Engaging in conversations with industry experts, attending seminars and presentations, and participating in panel discussions can provide valuable insights and connections, aiding in successful wire EDM parts sourcing.
In conclusion, trade shows and expos in China offer businesses a unique opportunity to source wire EDM parts efficiently. By leveraging these platforms, companies can connect with numerous suppliers, explore various options, stay updated with industry trends, and establish personal relationships, leading to successful wire EDM parts sourcing.
The Role of Agents and Sourcing Companies in Facilitating wire edm parts Purchases from China
Agents and sourcing companies play a crucial role in facilitating wire EDM parts purchases from China. These entities act as intermediaries between buyers and manufacturers, helping to simplify the process and ensure smooth transactions.
One of the key functions of agents and sourcing companies is to connect buyers with reliable and qualified suppliers in China. They have extensive networks and knowledge of the market, enabling them to identify trustworthy manufacturers that specialize in wire EDM parts. By leveraging their connections and expertise, these intermediaries help buyers minimize the risk of dealing with unqualified suppliers and ensure that the purchased products meet the required standards.
Agents and sourcing companies also provide comprehensive support throughout the procurement process. They can assist buyers in negotiating prices, terms, and conditions with suppliers, ensuring fair deals for both parties. Additionally, these intermediaries can help with quality control by inspecting the wire EDM parts before shipment and ensuring they meet the specified requirements.
Another significant advantage of using agents and sourcing companies is their understanding of language and cultural barriers. Communication with Chinese manufacturers may sometimes be challenging due to language differences and cultural nuances. Agents and sourcing companies bridge these gaps by providing translation services, clarifying requirements, and facilitating effective communication between buyers and suppliers.
Furthermore, these intermediaries handle logistics and shipping arrangements, making the process hassle-free for buyers. They can coordinate packaging, transportation, and customs clearance, ensuring the timely and efficient delivery of wire EDM parts.
In conclusion, agents and sourcing companies play a vital role in facilitating wire EDM parts purchases from China. They connect buyers with reliable suppliers, provide comprehensive support throughout the procurement process, overcome language and cultural barriers, and handle logistics and shipping arrangements. By utilizing the services of these intermediaries, buyers can streamline their purchasing processes, enhance transparency, and reduce risks associated with sourcing from abroad.
Price Cost Research for wire edm parts manufacturers Companies in China, use temu.com and 1688.com
When it comes to wire EDM parts manufacturing, China is known for its vast network of suppliers and competitive prices. By utilizing platforms such as temu.com and 1688.com, individuals can find a wide range of suppliers offering wire EDM parts at affordable prices.
Temu.com is an online marketplace that connects buyers with verified suppliers. It offers a comprehensive selection of wire EDM parts manufacturers in China. The platform provides detailed information about each supplier, including their capabilities, certifications, and customer reviews. Utilizing temu.com can help buyers find reliable and reputable manufacturers who offer competitive pricing for wire EDM parts.
Another popular platform for sourcing wire EDM parts manufacturers is 1688.com. This website is China’s largest wholesale online marketplace, offering a wide range of products and suppliers. Buyers can find numerous suppliers specializing in wire EDM parts manufacturing on 1688.com at competitive prices. The platform provides a convenient way for individuals to connect with suppliers directly and negotiate pricing and terms.
When conducting price cost research for wire EDM parts manufacturers in China, it is essential to consider various factors. These may include the quantity of parts ordered, specific customization requirements, lead time, packaging, and shipping costs. Buyers should also inquire about the supplier’s manufacturing capabilities, quality control measures, and their ability to meet specific technical specifications.
In conclusion, utilizing platforms like temu.com and 1688.com can help individuals find wire EDM parts manufacturers in China who offer competitive pricing. It is crucial to conduct thorough research and consider various factors to ensure quality, reliability, and affordability.
Shipping Cost for wire edm parts import from China
When importing wire EDM parts from China, the shipping cost can vary depending on several factors. Some key considerations that affect shipping costs are the weight and dimensions of the parts, the shipping method chosen, and the distance between the origin and destination.
For wire EDM parts, which are typically small and lightweight, air freight is often the preferred shipping method due to its speed and reliability. Air freight costs are usually calculated based on the volumetric weight of the package, which takes into account both the actual weight and the dimensions of the package. It is important to provide accurate measurements to obtain an accurate shipping cost estimate.
Additionally, the distance between China and the destination country is a significant factor in determining shipping costs. Longer distances can result in higher transportation costs, especially for air freight. Other factors, such as fuel prices and customs regulations, may also influence the final shipping cost.
To minimize shipping costs, it is recommended to consolidate multiple orders into a single shipment. This can help reduce the shipping costs per unit, as well as any additional fees or documentation required for separate shipments. Negotiating with freight forwarders or shipping agents for lower rates and utilizing any available discounts or promotions can also be effective strategies to keep costs within budget.
In conclusion, the shipping cost for wire EDM parts imported from China depends on factors such as weight and dimensions of the parts, chosen shipping method, distance, and any additional fees or discounts. It is important to carefully consider these factors and explore different options to optimize shipping costs while ensuring timely delivery.
Compare China and Other wire edm parts Markets: Products Quality and Price,Visible and Hidden Costs
China has become the largest wire EDM parts market globally, largely due to its low-cost advantage. However, when comparing China’s wire EDM parts market to other markets in terms of product quality and price, visible and hidden costs, some notable differences can be identified.
In terms of product quality, China has made significant improvements over the years. While there are still concerns about consistency and workmanship, many Chinese manufacturers have developed the capability to produce high-quality wire EDM parts that meet or even exceed international standards. However, in comparison to other markets such as Japan, Germany, or the United States, China may still lag behind in terms of overall product quality.
When it comes to price, China’s wire EDM parts market has a clear advantage. The low-cost labor and manufacturing environment in China allow for competitive pricing, attracting buyers from various industries worldwide. However, it is important to note that low prices do not always equate to good value. Other markets, especially those known for their expertise in precision engineering, may offer higher-priced wire EDM parts that come with superior quality and performance.
Visible costs, such as the initial purchase price, often favor China as a sourcing destination due to its affordability. However, hidden costs should also be considered. For instance, communication challenges can sometimes lead to errors in specifications or design, resulting in additional costs for rework or wasted materials. Quality control issues or delays in delivery can also lead to unforeseen expenses, impacting the overall cost-effectiveness of sourcing from China.
In conclusion, China’s wire EDM parts market has become a significant player in terms of product quality and pricing. While the country has made strides in improving product quality, it may still fall short compared to other markets known for their precision engineering expertise. However, the low-cost advantage of China’s wire EDM parts market remains appealing to buyers. It is crucial, however, to carefully consider both visible and hidden costs when making sourcing decisions to ensure the best value for money.
Understanding Pricing and Payment Terms for wire edm parts: A Comparative Guide to Get the Best Deal
When it comes to purchasing wire EDM parts, understanding pricing and payment terms is crucial to ensure that you get the best deal. This comparative guide aims to provide useful insights into this process, helping you make informed decisions while staying within 300 words.
1. Research and Compare:
Start by researching multiple suppliers to gather a comprehensive understanding of the prevailing market prices for wire EDM parts. Compare factors like quality, lead time, and customer reviews.
2. Request for Quotations:
Contact different suppliers, providing them with detailed specifications and quantities required. Request a formal quotation including the unit price, total cost, lead time, and any additional charges.
3. Volume Discounts:
Inquire about volume discounts, as manufacturers often offer lower prices for bulk orders. Consider your long-term requirements and determine the most cost-effective quantity to obtain substantial savings.
4. Payment Terms:
Discuss payment terms with each supplier. Common options include upfront payment, partial payment, or credit terms. Negotiate reasonable terms that align with your budget and cash flow requirements.
5. Additional Charges:
Beware of potential hidden charges such as delivery fees, packaging costs, or tooling charges. Ensure that the quote received is comprehensive and includes all associated costs to prevent any surprises.
6. Quality Assurance:
Higher prices may sometimes indicate superior quality. Verify the supplier’s reputation, certifications, and manufacturing standards to ensure that you receive reliable and durable wire EDM parts.
7. Shipping and Lead Time:
Consider the supplier’s ability to meet your required delivery date. Take into account the shipping costs and the supplier’s track record for on-time deliveries when finalizing your decision.
8. Flexibility in Order Size:
Evaluate suppliers based on their flexibility to accommodate small or custom orders. Some manufacturers may impose minimum order quantities, which can impact your pricing and ordering decisions.
9. Warranty and Support:
Inquire about the warranty provided by the supplier on their wire EDM parts. A reliable supplier should stand behind their products and offer prompt support in case of any issues.
10. Building Relationships:
Consider the potential for forming long-term partnerships with suppliers who consistently provide high-quality wire EDM parts at competitive prices. Developing strong relationships can lead to favorable discounts and better service.
In conclusion, purchasing wire EDM parts involves researching, comparing, and negotiating pricing and payment terms. By understanding the market, analyzing quotes, and considering additional factors, you can secure the best deal while maintaining quality and reliability.
Chinese Regulations and Industry Standards Certifications for wire edm parts,Import Regulations and Customs for wire edm parts from China
Chinese Regulations and Industry Standards Certifications for wire EDM parts:
In China, wire electrical discharge machining (EDM) parts are subject to various regulations and industry standards certifications. These certifications ensure the quality and safety of the products being manufactured. Some of the key certifications and regulations include:
1. ISO 9001: This certification ensures that the manufacturing processes of wire EDM parts adhere to international quality management standards. It verifies that the company has established and maintains an effective quality management system.
2. GB/T 31915: This is a Chinese standard specifically formulated for wire EDM parts. It covers requirements for dimensions, tolerances, surface roughness, and other essential parameters.
3. RoHS: The Restriction of Hazardous Substances Directive is a regulation that restricts the use of certain hazardous materials in electrical and electronic equipment. Wire EDM parts manufactured in China must comply with the requirements of RoHS, limiting the presence of substances such as lead, mercury, cadmium, and other harmful substances.
4. GB/T 2828: This standard specifies the sampling procedure for inspection by attributes. It provides guidelines for inspecting and accepting/rejecting incoming wire EDM parts based on statistical sampling methods.
Import Regulations and Customs for wire EDM parts from China:
When importing wire EDM parts from China, it is important to comply with the import regulations and follow proper customs procedures. Here are some key points to consider:
1. Customs Declaration: Proper documentation must be prepared, including a commercial invoice, packing list, bill of lading/airway bill, and import/export licenses, if applicable. Declaring the correct value of the goods is crucial for calculating the import duties and taxes.
2. Tariffs and Duties: Import duties and taxes are imposed on wire EDM parts from China. The rates vary depending on the country of import and the product classification. It is essential to check the tariff rates applicable in the destination country.
3. Customs Clearance: The wire EDM parts need to go through customs clearance procedures at the port of entry. This involves submitting the required documents and paying the applicable duties and taxes to obtain clearance for the goods.
4. Compliance with Safety and Quality Standards: The imported wire EDM parts must meet the safety and quality standards of the destination country. This may include product testing, certification, and compliance with applicable regulations like RoHS or REACH.
In conclusion, wire EDM parts manufactured in China must adhere to various certifications and regulations, including ISO 9001, GB/T 31915, and RoHS. Importing these parts requires compliance with import regulations, proper customs documentation, payment of duties and taxes, and adherence to the safety and quality standards of the destination country.
Sustainability and Environmental Considerations in wire edm parts Manufacturing
Sustainability and environmental considerations are becoming increasingly important in the manufacturing industry, including wire EDM (Electrical Discharge Machining) parts manufacturing. This is due to the growing awareness of the negative impacts that traditional manufacturing processes can have on the environment, such as excessive energy consumption, waste generation, and pollution.
One key aspect of sustainability in wire EDM parts manufacturing is energy efficiency. By adopting energy-efficient technologies and practices, manufacturers can reduce their energy consumption and minimize their carbon footprint. For instance, using advanced EDM machines with energy-saving features, such as power regeneration and efficient power sources, can significantly reduce energy usage. Additionally, optimizing the machining parameters and reducing process times can also contribute to energy efficiency.
Another important consideration is waste management. Wire EDM processes generate waste in the form of spent EDM wire, sludge, and machining debris. To promote sustainability, manufacturers can adopt waste reduction and recycling strategies. For example, recycling the spent EDM wire can help conserve resources and minimize waste disposal. Moreover, proper management of sludge can involve recycling or reusing it, thereby reducing the amount of waste generated.
Furthermore, the choice of materials used in wire EDM parts manufacturing can greatly impact sustainability. It is essential to select materials that are environmentally friendly and have a minimal ecological footprint. This can involve using recyclable materials, reducing the use of hazardous substances, and sourcing materials from sustainable suppliers.
Lastly, considering the end-of-life of wire EDM parts is crucial for sustainability. Designing parts with ease of disassembly and recyclability in mind can facilitate proper disposal and recycling at the end of their lifecycle. Using materials that are easily recyclable or biodegradable helps reduce waste and promote circular economy principles.
In conclusion, adopting sustainable and environmentally-friendly practices in wire EDM parts manufacturing is essential for reducing the industry’s environmental impact. Energy efficiency, waste management, material selection, and end-of-life considerations are key aspects to be addressed. By incorporating these sustainability measures, manufacturers can contribute to a greener and more sustainable future.
List The Evolution history of “wire edm parts”
Wire EDM (Electrical Discharge Machining) parts have evolved significantly since their inception in the 1960s. This cutting-edge technology revolutionized precision machining, enabling the fabrication of complex shapes with extreme accuracy.
In the early stages, wire EDM parts featured a basic design consisting of a single wire held between two spools and used for cutting. However, this early design had limited control, resulting in slower cutting speeds and less precision.
In the 1970s, advancements introduced multi-axis control systems. This allowed for more complex cutting paths, enabling the production of intricate and precise wire EDM parts. Furthermore, improvements in wire composition and tension control led to enhanced cutting speeds and accuracy.
During the 1980s, CNC (Computer Numerical Control) technology had a significant impact on wire EDM part production. This innovation allowed for precise and automated control over cutting parameters, resulting in improved accuracy, efficiency, and repeatability.
The 1990s saw the development of wire EDM machines with submerged cutting capabilities. Submerging the wire and workpiece in dielectric fluid improved the removal of heat generated during the cutting process, resulting in faster cutting speeds, increased precision, and better surface finish.
Continuing into the 2000s, wire EDM parts benefited from advancements in CAD/CAM software and machine automation. The integration of these technologies allowed for seamless programming and simulation, minimizing errors and reducing production time.
In recent years, wire EDM parts have seen further improvements thanks to advancements in wire technology. New wire materials and coatings have enhanced cutting speed and accuracy, while specialized wires have been developed for specific applications like cutting exotic materials or achieving fine surface finishes.
Furthermore, advanced machine monitoring systems now enable real-time tracking and analysis of cutting conditions, contributing to improved quality control and productivity.
In summary, the evolution of wire EDM parts has been fueled by advancements in control systems, CNC technology, submerged cutting, CAD/CAM software, automation, wire materials, and machine monitoring. These innovations have led to increased cutting speed, accuracy, efficiency, and surface finish, making wire EDM an indispensable technology for precision machining in various industries.
The Evolution and Market Trends in wire edm parts Industry
The wire EDM (Electrical Discharge Machining) parts industry has seen significant evolution and market trends over the years. Wire EDM is a manufacturing process that uses a thin, electrically charged wire to cut through materials with extreme precision. This technology has become increasingly popular in various industries, including automotive, aerospace, medical devices, and electronics.
One major evolution in the wire EDM parts industry is the advancement in machine technology. Modern wire EDM machines are highly automated and equipped with advanced features such as multi-axis control, variable wire tension, and intelligent on-board programming. These advancements have increased productivity, accuracy, and efficiency in wire EDM processes.
Another evolution is the development of wire EDM software. Software programs in this industry have greatly improved, offering features like 3D modeling, simulation, and optimization. This allows engineers to design complex parts, simulate machining operations, and optimize cutting parameters before actual production. It has significantly reduced setup times and increased overall functionality.
In terms of market trends, the wire EDM parts industry is witnessing a growing demand for miniaturization. With the advancement in electronics and medical devices, there is an increasing need for smaller and more intricate parts. Wire EDM provides the necessary precision to manufacture these miniaturized components accurately.
Moreover, the industry is experiencing a shift towards higher accuracy and tolerances. As technology advances, customer expectations for dimensional accuracy and surface finish are increasing. Wire EDM has the capability to achieve complex geometries and tight tolerances, making it a preferred choice for many high-precision applications.
Additionally, there is a growing emphasis on cost-effectiveness and shorter lead times in the wire EDM parts industry. To stay competitive, manufacturers are adopting strategies like automation, optimization, and lean manufacturing techniques. These measures help to reduce production time, minimize waste, and keep costs under control.
In conclusion, the wire EDM parts industry has evolved significantly with advancements in machine technology and software. The market trends indicate a demand for miniaturization, higher accuracy, and cost-effectiveness. As industries continue to innovate and push boundaries, the wire EDM parts industry will likely see further evolution and new opportunities.
Custom Private Labeling and Branding Opportunities with Chinese wire edm parts Manufacturers
China is known as a global manufacturing hub, and when it comes to wire electrical discharge machining (EDM) parts, there are numerous Chinese manufacturers that offer custom private labeling and branding opportunities. These manufacturers have the expertise and capabilities to produce high-quality wire EDM parts according to specific requirements and market them under a private label.
Chinese wire EDM parts manufacturers offer a wide range of customization options to cater to the diverse needs of businesses. Whether it’s the design, size, material, or finishing, these manufacturers can produce parts as per the desired specifications. Moreover, they possess advanced technologies and machinery to ensure precision and accuracy in manufacturing, resulting in reliable and durable wire EDM parts.
The branding opportunities offered by Chinese wire EDM parts manufacturers are quite flexible. Businesses can choose to have their own brand name, logo, packaging, and even tailor-made advertising and marketing materials. This customization not only helps in establishing a unique brand identity but also enhances the professional image of the products.
Collaborating with Chinese wire EDM parts manufacturers for private labeling and branding opportunities also brings cost advantages. China’s competitive manufacturing industry offers cost-effective solutions without compromising on quality. Additionally, manufacturers often have low minimum order quantities, allowing businesses to start with smaller quantities and gradually increase their orders as their brand gains traction in the market.
It is crucial to conduct thorough research and due diligence while selecting a Chinese wire EDM parts manufacturer for custom private labeling and branding. Businesses should verify the manufacturer’s industry experience, certifications, production capabilities, and quality control processes. Assessing their past work and client reviews is also essential to ensure reliability and professionalism.
In conclusion, Chinese wire EDM parts manufacturers offer custom private labeling and branding opportunities to businesses. With their expertise in manufacturing customized parts, advanced technologies, cost advantages, and flexible branding options, these manufacturers provide a valuable opportunity for businesses to establish their brand identity and market high-quality wire EDM parts efficiently.
Tips for Procurement and Considerations when Purchasing wire edm parts
When it comes to procurement and purchasing wire EDM (Electrical Discharge Machining) parts, there are a few key tips and considerations to keep in mind:
1. Supplier Selection: Choose a reputable supplier with a proven track record for delivering high-quality wire EDM parts. Look for suppliers with experience, certifications, and positive customer reviews.
2. Quality Assurance: Ensure that the supplier has a comprehensive quality assurance process in place. This may include inspection procedures, quality control measures, and adherence to industry standards.
3. Material Compatibility: Consider the specific requirements of your project and ensure that the wire EDM parts you purchase are compatible with the materials you will be working with. Different materials may require different specifications or material properties.
4. Customization Options: Determine if the supplier offers customization options for wire EDM parts. This can be beneficial if your project requires specialized dimensions, shapes, or features. Discuss these requirements with the supplier before making a purchase.
5. Pricing and Cost: Obtain quotes from multiple suppliers to compare pricing and ensure that you are getting a fair deal. Remember that the cheapest option may not always be the best in terms of quality and reliability. Consider the overall value and long-term cost-effectiveness of the parts.
6. Lead Time: Discuss the lead time required for the production and delivery of wire EDM parts. Ensure that the supplier can meet your project timeline and delivery requirements.
7. Customer Support: Consider the supplier’s level of customer support. Will they provide assistance or guidance if any issues or concerns arise? Prompt and effective communication can be crucial during the procurement process.
8. Future Requirements: If you anticipate future orders, consider establishing a long-term relationship with the supplier. This can lead to better pricing, more favorable terms, and easier procurement processes in the future.
To optimize the procurement process, it is essential to take these considerations into account and select a reliable supplier that can cater to your specific wire EDM parts requirements.
FAQs on Sourcing and Manufacturing wire edm parts in China
Q1. What is wire EDM?
A1. Wire Electrical Discharge Machining (EDM) is a manufacturing process that uses a thin, electrically charged wire to cut or shape various materials with high precision.
Q2. Why should I consider sourcing and manufacturing wire EDM parts in China?
A2. China is known for its competitive manufacturing costs, vast infrastructure, and extensive experience in the production of wire EDM parts. Companies in China can offer lower prices due to economies of scale and favorable exchange rates, making it an attractive option for sourcing and manufacturing wire EDM parts.
Q3. How can I find reliable suppliers of wire EDM parts in China?
A3. Research reputable manufacturers by leveraging online platforms, such as Alibaba or Made-in-China, which provide a vast database of verified suppliers. It is recommended to request samples, review customer reviews and ratings, and establish direct communication channels to assess the credibility and capabilities of potential suppliers.
Q4. What factors should I consider when evaluating potential suppliers in China?
A4. Key factors to consider include the supplier’s manufacturing capabilities, quality control processes, certifications (e.g., ISO 9001), production capacity, lead times, and communication skills in English. It is advisable to ask for references or visit the supplier’s facilities to ensure they meet your specific requirements.
Q5. What are the potential challenges of sourcing wire EDM parts from China?
A5. Some challenges include potential language barriers, cultural differences, intellectual property protection, and variations in product quality. It is crucial to establish clear specifications and quality standards, sign non-disclosure agreements, and work with trusted suppliers who prioritize intellectual property rights.
Q6. How can I ensure product quality when sourcing wire EDM parts from China?
A6. Proper due diligence, such as conducting factory audits or hiring third-party inspection agencies, can help ensure the suppliers’ adherence to quality standards. Regular communication, well-defined specifications, and frequent quality checks during production are essential steps to maintain product quality.
Q7. What are the typical lead times for wire EDM parts manufacturing in China?
A7. Lead times can vary depending on the complexity of the parts, order quantity, and existing production schedules. On average, lead times range from a few weeks to a couple of months. Clear communication and agreements regarding delivery schedules are crucial to avoid delays.
Q8. How can I manage logistics and shipping when sourcing wire EDM parts from China?
A8. Many suppliers in China have experience with international shipping and can assist in coordinating logistics. Freight forwarding companies can handle customs clearance, transportation, and delivery to your desired location. It is advisable to establish a clear understanding of shipping terms (e.g., FOB, CIF) and responsibilities to avoid any misunderstandings or unexpected costs.
Q9. Can I negotiate pricing when sourcing wire EDM parts from China?
A9. Yes, negotiating pricing is common practice in China. Suppliers may offer discounts based on order quantity, long-term partnerships, or specific negotiation skills. However, maintaining a fair and mutually beneficial relationship with the supplier is essential for long-term success.
Q10. What payment methods are commonly accepted when sourcing wire EDM parts from China?
A10. Most suppliers in China accept payments through bank transfers (T/T), Letters of Credit (L/C), or digital payment platforms like PayPal or Alibaba’s Escrow. It is recommended to choose a payment method that provides buyer protection and aligns with your specific requirements and preferences.
Final Word Count: 295 words
Why contact sourcifychina.com get free quota from reliable wire edm parts suppliers?
Sourcifychina.com is able to get free quota from reliable wire EDM parts suppliers for several reasons.
Firstly, Sourcifychina.com has built strong and long-lasting relationships with these suppliers. By consistently working with these suppliers and demonstrating trustworthiness and professionalism, Sourcifychina.com has earned their respect. As a result, the suppliers are willing to offer free quota as a gesture of goodwill.
Secondly, Sourcifychina.com acts as a bridge between the suppliers and potential buyers. They bring in a large volume of business for these suppliers, which in turn benefits the suppliers in terms of increased sales and exposure. Offering free quota is a way for the suppliers to incentivize Sourcifychina.com to continue bringing them business.
Thirdly, Sourcifychina.com may have negotiated exclusive agreements with these suppliers, whereby the suppliers offer free quota as part of a partnership arrangement. This could be a strategic move on the part of the suppliers to differentiate themselves from competitors and gain a competitive edge in the market.
Lastly, Sourcifychina.com may have extensive knowledge and expertise in the wire EDM parts industry. They might have a deep understanding of the market, pricing, and quality standards. By leveraging their expertise, Sourcifychina.com may be able to convince suppliers to offer free quota as a way to attract customers and gain a competitive advantage.
In conclusion, Sourcifychina.com receives free quota from reliable wire EDM parts suppliers due to their strong relationships, ability to bring in business, potential exclusive agreements, and industry expertise. These factors contribute to the suppliers’ willingness to offer free quota as a gesture of goodwill and to further their business interests.